What is Solder Mask?
Solder mask, also known as solder resist or solder stop, is a thin lacquer-like layer of polymer applied to the copper traces of a printed circuit board (PCB). Its primary purpose is to prevent solder from bridging between conductors, providing protection against oxidation and contamination during the soldering process and in the finished assembly.
The solder mask is usually applied by screen printing or photo imaging and covers the entire PCB except for the pads and areas that need to be soldered. It is typically green in color but can also come in other colors such as red, blue, black, yellow, or white.
Key Functions of Solder Mask
-
Insulation: Solder mask acts as an insulating layer, preventing short circuits caused by accidental solder bridges between closely spaced solder pads.
-
Protection: It protects the copper traces from oxidation, corrosion, and other environmental factors that could degrade the performance of the PCB over time.
-
Aesthetics: Solder mask gives the PCB a finished and professional appearance, improving the overall aesthetics of the final product.
-
Identification: Different colored solder masks can be used to help identify different types of PCBs or to improve the contrast for better optical recognition of components during assembly.
Solder Mask Application Process
The application of solder mask involves several steps to ensure proper coverage and adhesion to the PCB surface. The following table outlines the general process:
Step | Description |
---|---|
1. Cleaning | The PCB is thoroughly cleaned to remove any contaminants or residues from the copper surface. |
2. Solder Mask Application | The liquid solder mask is applied to the PCB using screen printing or curtain coating techniques. |
3. Curing | The solder mask is cured using UV light or heat to harden and adhere to the PCB surface. |
4. Inspection | The PCB is inspected for any defects or imperfections in the solder mask coverage. |
5. Final Finish Application | The exposed pads are plated with the desired final finish (e.g., ENIG, HASL, or OSP) to protect the copper and enhance solderability. |
Solder Mask Application Methods
There are two primary methods for applying solder mask to a PCB:
-
Screen Printing: In this method, a stencil with the desired solder mask pattern is placed over the PCB. The liquid solder mask is then applied using a squeegee, forcing it through the openings in the stencil onto the PCB surface. This method is suitable for high-volume production and provides a consistent layer thickness.
-
Photo Imaging: This method involves applying a photosensitive solder mask to the entire PCB surface. The solder mask is then exposed to UV light through a photographic film with the desired pattern. The exposed areas harden while the unexposed areas remain soluble and can be washed away. This method offers high precision and is suitable for fine-pitch designs.
Solder Mask Types and Properties
Several types of solder mask are available, each with specific properties and advantages. The following table compares the most common solder mask types:
Solder Mask Type | Description | Advantages |
---|---|---|
Liquid Photoimageable (LPI) | A photosensitive liquid solder mask that is applied and patterned using UV light exposure. | High resolution, excellent adhesion, and durability. Suitable for fine-pitch designs. |
Dry Film Photoimageable | A solid photosensitive film laminated onto the PCB surface and patterned using UV light exposure. | Easy to apply, consistent thickness, and good resolution. Suitable for high-volume production. |
Epoxy Liquid | A two-part epoxy-based solder mask that is screen printed onto the PCB surface. | Excellent chemical and heat resistance, high durability, and good insulation properties. |
Acrylate Liquid | A UV-curable acrylate-based solder mask that is screen printed onto the PCB surface. | Fast curing, good adhesion, and flexibility. Lower cost compared to other types. |
Solder Mask Properties
When selecting a solder mask for a specific application, several key properties should be considered:
-
Dielectric Strength: The ability of the solder mask to withstand high voltages without breaking down, preventing electrical shorts between conductors.
-
Insulation Resistance: The resistance of the solder mask to electrical current flow, ensuring proper insulation between conductors.
-
Thermal Resistance: The ability of the solder mask to withstand high temperatures during soldering and operation without degrading or delaminating.
-
Chemical Resistance: The resistance of the solder mask to various chemicals, solvents, and fluxes used during the PCB manufacturing and assembly processes.
-
Adhesion: The ability of the solder mask to adhere to the PCB surface and copper traces, preventing delamination or peeling during handling and use.
-
Resolution: The capability of the solder mask to achieve fine features and openings, particularly important for high-density and fine-pitch designs.
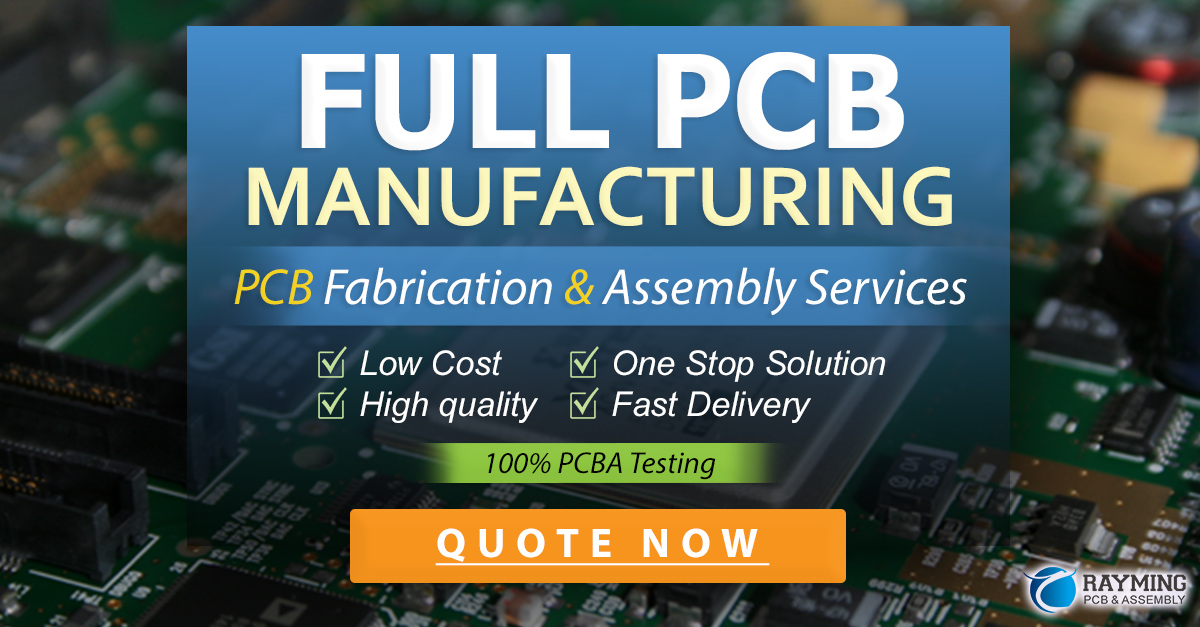
Solder Mask Design Considerations
When designing a PCB with solder mask, several factors should be taken into account to ensure optimal performance and manufacturability:
Solder Mask Clearance
Solder mask clearance refers to the distance between the edge of a pad or trace and the solder mask opening. Adequate clearance is necessary to accommodate tolerances in the solder mask application process and ensure proper solder wetting during assembly. The following table provides general guidelines for solder mask clearance based on the pad size:
Pad Size (mm) | Solder Mask Clearance (mm) |
---|---|
≤ 0.5 | 0.05 – 0.075 |
0.5 – 1.0 | 0.075 – 0.1 |
1.0 – 2.0 | 0.1 – 0.15 |
> 2.0 | 0.15 – 0.2 |
Solder Mask Sliver
A solder mask sliver is a thin strip of exposed copper between two solder mask openings. Slivers can cause short circuits or solder bridges during assembly and should be avoided in the PCB design. To prevent slivers, ensure that the spacing between pads or traces is sufficient to accommodate the minimum solder mask web width, typically 0.1 – 0.15 mm.
Solder Mask Color
The choice of solder mask color is primarily driven by aesthetic considerations and the specific requirements of the end application. Green is the most common color, but other colors such as black, red, blue, or white can be used to improve contrast, aid in component placement, or enhance the visual appeal of the final product.
Solder Mask Inspection and Quality Control
To ensure the quality and reliability of the solder mask application, several inspection and testing methods are employed during the PCB manufacturing process:
Visual Inspection
Visual inspection is the first step in assessing the quality of the solder mask. The PCB is examined under magnification to check for any defects, such as pinholes, bubbles, scratches, or incomplete coverage. Automated optical inspection (AOI) systems can be used to detect and classify defects quickly and consistently.
Thickness Measurement
Solder mask thickness is critical to ensuring proper insulation and protection of the PCB. The thickness can be measured using non-destructive methods such as eddy current testing or ultrasonic gauging. The typical solder mask thickness ranges from 0.01 mm to 0.03 mm, depending on the application and the solder mask type.
Adhesion Testing
Adhesion testing is performed to evaluate the bond strength between the solder mask and the PCB surface. Common methods include the cross-hatch test, where a pattern of cuts is made in the solder mask and the adhesion is assessed based on the amount of material removed when a tape is applied and peeled off. Another method is the peel strength test, where a strip of solder mask is peeled off the PCB surface, and the force required is measured.
Insulation Resistance Testing
Insulation resistance (IR) testing measures the resistance of the solder mask to electrical current flow. A high voltage is applied between the conductors, and the resistance is measured to ensure that it meets the specified requirements. This test helps to verify the insulating properties of the solder mask and detect any defects that could lead to shorts or leakage currents.
FAQ
1. What is the purpose of solder mask on a PCB?
Solder mask serves several purposes on a PCB, including:
– Insulating the copper traces to prevent short circuits
– Protecting the copper from oxidation and contamination
– Providing a surface for applying component identification markings
– Improving the aesthetic appearance of the PCB
2. Can solder mask be applied to both sides of a PCB?
Yes, solder mask can be applied to both sides of a PCB. In fact, most PCBs have solder mask on both the top and bottom surfaces to provide insulation and protection for the copper traces on both sides.
3. What is the difference between liquid photoimageable (LPI) and dry film solder mask?
LPI solder mask is a liquid that is applied to the PCB surface and then exposed to UV light through a photomask to create the desired pattern. Dry film solder mask, on the other hand, is a solid film that is laminated onto the PCB surface and then exposed to UV light to create the pattern. LPI solder mask offers higher resolution and finer features, while dry film solder mask is easier to apply and provides a more consistent thickness.
4. How does solder mask affect the solderability of pads?
Solder mask can affect the solderability of pads in several ways. If the solder mask openings are too small, it can be difficult for the solder to wet the pads properly, leading to poor solder joints. If the solder mask is not properly cured or has poor adhesion, it can peel away from the pads during soldering, exposing the copper to oxidation and contamination. To ensure good solderability, it is important to design the solder mask with appropriate clearances and to use a high-quality solder mask material that is properly applied and cured.
5. Can solder mask be removed from a PCB?
Yes, solder mask can be removed from a PCB using various methods, such as chemical stripping, abrasive blasting, or laser ablation. However, removing the solder mask can expose the copper traces to oxidation and contamination, and it may also damage the PCB surface or the components. In most cases, it is not recommended to remove the solder mask unless absolutely necessary for repair or rework purposes.
No responses yet