Introduction to PCB Pooling
PCB pooling, also known as panel sharing or order combining, is a cost-effective method for manufacturing printed circuit boards (PCBs) in small quantities. In PCB pooling, multiple designs from different customers are combined onto a single large panel for fabrication. This allows the fixed costs of production to be shared among all the participating customers, resulting in lower prices per PCB compared to ordering them individually.
PCB pooling has become increasingly popular among hobbyists, students, and small businesses who require prototype or low-volume production of PCBs. Many PCB manufacturers now offer pooling services with various options for board specifications, lead times, and pricing.
How PCB Pooling Works
The process of PCB pooling typically involves the following steps:
-
Customers submit their PCB designs to the manufacturer, specifying the required board specifications such as size, layer count, material, thickness, copper weight, surface finish, and solder mask color.
-
The manufacturer checks the designs for manufacturability and groups together designs with similar specifications onto a single large panel, usually in a grid pattern with space between each design.
-
The panel is fabricated using standard PCB manufacturing processes such as etching, drilling, plating, solder mask application, and silkscreen printing.
-
After fabrication, the individual PCBs are cut out from the panel using a process called depaneling or routing. The boards are then packaged and shipped to their respective customers.
The size of the panel and the number of designs that can fit on it depend on the capabilities of the manufacturer and the specifications of the boards. A typical panel size is 18″ x 24″ (457 mm x 610 mm), which can accommodate dozens of small PCBs or a few large ones. The minimum and maximum board sizes, as well as the allowed spacing between boards, are usually specified by the manufacturer.
Advantages of PCB Pooling
Cost Savings
The main advantage of PCB pooling is the significant cost savings compared to ordering PCBs individually. By combining multiple designs onto a single panel, the fixed costs of production such as tooling, setup, and materials are shared among all the participating customers. This results in a lower cost per PCB, especially for small quantities.
For example, ordering a single prototype PCB might cost $100 or more, but ordering the same PCB through a pooling service might cost only $20-$30. The cost savings can be even greater for larger quantities, as the fixed costs are spread out over more boards.
Faster Turnaround Times
Another advantage of PCB pooling is the faster turnaround times compared to ordering PCBs individually. Since the manufacturer can process multiple designs at once, they can often offer shorter lead times for pooled orders. This is especially useful for prototyping and testing, where quick iterations are necessary.
Many PCB pooling services offer standard lead times of 5-15 business days, depending on the complexity of the designs and the chosen service options. Some manufacturers also offer expedited services with lead times as short as 24-48 hours, although these come at a higher cost.
Access to Advanced Features
PCB pooling also allows customers to access advanced features and capabilities that might be too expensive or impractical for individual orders. For example, some manufacturers offer pooling services with options for high-density interconnect (HDI) designs, blind and buried vias, impedance control, and advanced surface finishes such as ENIG (Electroless Nickel Immersion Gold) or hard gold plating.
These advanced features can enable more complex and high-performance designs, but they often require specialized equipment and processes that are not cost-effective for small-scale production. By pooling orders, customers can take advantage of these capabilities without incurring the full cost of production.
Disadvantages of PCB Pooling
Limited Design Flexibility
One of the main disadvantages of PCB pooling is the limited design flexibility compared to ordering PCBs individually. Since multiple designs are combined onto a single panel, there are constraints on the size, shape, and layout of the boards that can be accommodated.
Most PCB pooling services have standard board sizes and specifications that customers must adhere to. These typically include rectangular or square boards with standard dimensions (e.g. 100mm x 100mm), a limited number of layers (e.g. 2-4 layers), and a fixed thickness (e.g. 1.6mm). Customers may also be limited in their choice of materials, surface finishes, and other options.
For designs that require non-standard sizes, shapes, or specifications, PCB pooling may not be a viable option. In these cases, customers may need to order their PCBs individually or find a manufacturer that offers more flexible pooling services.
Minimum Order Quantities
Another disadvantage of PCB pooling is the minimum order quantities required by some manufacturers. While pooling allows customers to order smaller quantities than individual orders, there may still be minimum order requirements that can be cost-prohibitive for very small projects.
For example, a manufacturer may require a minimum order of 10 or 20 PCBs per design, even if the customer only needs one or two. This can significantly increase the overall cost of the project, especially if multiple designs are needed.
Some manufacturers offer lower minimum order quantities for pooled orders, such as 5 or even 1 PCB per design. However, these may come with higher prices or longer lead times compared to larger orders.
Intellectual Property Concerns
PCB pooling also raises concerns about intellectual property (IP) protection, as multiple designs from different customers are combined onto a single panel. There is a risk that sensitive or proprietary information could be exposed or leaked during the manufacturing process.
To mitigate this risk, many PCB manufacturers have strict policies and procedures in place to protect customer IP. This may include non-disclosure agreements (NDAs), secure data transfer and storage, and physical and electronic access controls.
Customers should also take steps to protect their own IP, such as removing sensitive information from their design files before submitting them for manufacturing. This may include removing component labels, test points, or other identifying markings that could reveal the purpose or function of the board.
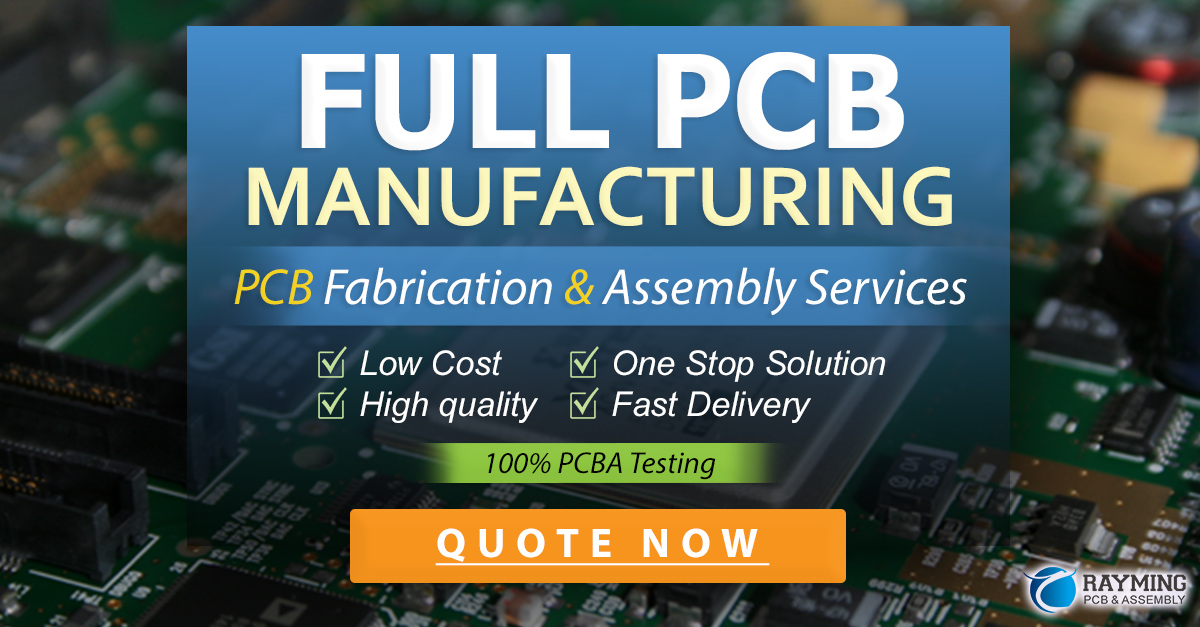
PCB Pooling vs. Individual Ordering
When deciding whether to use PCB pooling or order PCBs individually, customers should consider several factors such as cost, lead time, design flexibility, and IP protection. The following table summarizes some of the key differences between these two options:
Factor | PCB Pooling | Individual Ordering |
---|---|---|
Cost per PCB | Lower for small quantities | Higher for small quantities |
Lead Time | Faster for standard options | Slower for custom options |
Design Flexibility | Limited by standard sizes and specs | Unlimited customization |
Minimum Order Quantity | Lower (5-20 PCBs) | Higher (50-100 PCBs) |
IP Protection | Moderate risk | Low risk |
For most small-scale projects and prototypes, PCB pooling is a cost-effective and time-saving option that can deliver high-quality boards at a fraction of the cost of individual ordering. However, for larger-scale production or highly customized designs, individual ordering may be necessary to achieve the desired specifications and quantities.
Choosing a PCB Pooling Service
When choosing a PCB pooling service, customers should consider several factors to ensure they get the best value and quality for their project. Some key considerations include:
Board Specifications
Different PCB pooling services offer different options for board specifications such as size, layer count, material, thickness, and surface finish. Customers should choose a service that can accommodate their design requirements and preferences.
Pricing and Lead Times
PCB pooling services vary in their pricing and lead times depending on the complexity of the designs, the chosen specifications, and the order quantity. Customers should compare prices and lead times from multiple services to find the best value for their project.
Design Guidelines and Restrictions
Each PCB pooling service has its own design guidelines and restrictions that customers must follow to ensure manufacturability and quality. These may include minimum feature sizes, clearances, drill sizes, and panelization requirements. Customers should carefully review and adhere to these guidelines to avoid delays or additional costs.
Customer Support and Communication
Good customer support and communication are essential for a smooth and successful PCB pooling experience. Customers should choose a service with responsive and knowledgeable support staff who can answer questions, provide guidance, and resolve issues in a timely manner.
Quality and Reliability
The quality and reliability of the PCBs are critical for the success of any project. Customers should choose a PCB pooling service with a proven track record of delivering high-quality boards that meet or exceed industry standards. This may include certifications such as ISO 9001, UL, or IPC, as well as customer reviews and testimonials.
FAQ
What is the minimum order quantity for PCB pooling?
The minimum order quantity for PCB pooling varies by manufacturer and service. Some services offer a minimum of 5-10 PCBs per design, while others may require 20 or more. Customers should check the specific requirements of each service before placing an order.
How long does PCB pooling take?
The lead time for PCB pooling depends on the complexity of the designs, the chosen specifications, and the order quantity. Most services offer standard lead times of 5-15 business days, although expedited options may be available for an additional cost.
Can I use PCB pooling for complex or high-density designs?
Yes, many PCB pooling services offer options for complex and high-density designs, including HDI, blind and buried vias, and impedance control. However, these options may come with additional costs and longer lead times compared to standard designs.
Is my intellectual property protected when using PCB pooling?
PCB manufacturers have policies and procedures in place to protect customer IP, including NDAs, secure data handling, and access controls. However, there is always some risk of exposure when multiple designs are combined onto a single panel. Customers should take steps to protect their own IP, such as removing sensitive information from their design files.
Can I get a refund if I’m not satisfied with my PCB pooling order?
Most PCB pooling services have limited refund policies due to the custom nature of the products. However, many services offer warranties or guarantees for defective or non-conforming boards. Customers should review the specific terms and conditions of each service before placing an order.
No responses yet