Types of PCB laminates
PCB laminates come in various types, each with its own unique set of properties and applications. The most common types of PCB laminates include:
FR-4 Laminate
FR-4 (Flame Retardant 4) is the most widely used PCB laminate material. It is composed of a woven fiberglass cloth impregnated with an epoxy resin. The fiberglass provides mechanical strength and dimensional stability, while the epoxy resin offers excellent insulation properties and resistance to moisture and chemicals.
Properties of FR-4 Laminate
Property | Value |
---|---|
Dielectric Constant | 4.2 – 4.8 (at 1 MHz) |
Dissipation Factor | 0.02 – 0.03 (at 1 MHz) |
Thermal Expansion (X-Y) | 12 – 16 ppm/°C |
Thermal Expansion (Z) | 50 – 70 ppm/°C |
Glass Transition Temperature | 125 – 135 °C |
FR-4 laminates are suitable for a wide range of applications, including consumer electronics, telecommunications, and industrial control systems.
High Tg FR-4 Laminate
High Tg (Glass Transition Temperature) FR-4 laminates are a variant of the standard FR-4 material. They are designed to withstand higher operating temperatures and offer improved thermal stability. The higher glass transition temperature is achieved by using a modified epoxy resin formulation.
Properties of High Tg FR-4 Laminate
Property | Value |
---|---|
Dielectric Constant | 4.2 – 4.8 (at 1 MHz) |
Dissipation Factor | 0.02 – 0.03 (at 1 MHz) |
Thermal Expansion (X-Y) | 12 – 16 ppm/°C |
Thermal Expansion (Z) | 50 – 70 ppm/°C |
Glass Transition Temperature | 170 – 180 °C |
High Tg FR-4 laminates are commonly used in automotive electronics, aerospace applications, and high-power LED lighting systems.
Polyimide Laminate
Polyimide laminates are known for their exceptional thermal stability, chemical resistance, and mechanical strength. They are composed of a polyimide film bonded to a copper foil using an adhesive layer. Polyimide laminates can withstand extreme temperatures, making them suitable for high-reliability applications.
Properties of Polyimide Laminate
Property | Value |
---|---|
Dielectric Constant | 3.2 – 3.6 (at 1 MHz) |
Dissipation Factor | 0.002 – 0.006 (at 1 MHz) |
Thermal Expansion (X-Y) | 20 – 40 ppm/°C |
Thermal Expansion (Z) | 60 – 100 ppm/°C |
Glass Transition Temperature | 220 – 260 °C |
Polyimide laminates are commonly used in aerospace, military, and high-temperature applications.
Composition of PCB Laminates
PCB laminates are composed of several layers that are bonded together under high pressure and temperature. The typical layers found in a PCB laminate include:
Substrate Material
The substrate material forms the core of the PCB laminate. It provides the necessary insulation and mechanical support for the conductive layers. The most common substrate materials used in PCB laminates are:
- Fiberglass cloth (e.g., FR-4)
- Polyimide film
- Ceramic
The choice of substrate material depends on the specific requirements of the application, such as the desired electrical properties, thermal stability, and mechanical strength.
Conductive Layers
Conductive layers, typically made of copper foil, are bonded to the substrate material. These layers serve as the pathways for electrical signals and power distribution. The thickness of the copper foil can vary depending on the current-carrying requirements of the circuit.
Common Copper Foil Thicknesses
Thickness (oz/ft²) | Thickness (μm) |
---|---|
0.5 oz | 17.5 μm |
1 oz | 35 μm |
2 oz | 70 μm |
3 oz | 105 μm |
The copper foil is etched to create the desired circuit pattern using photolithography and chemical etching processes.
Adhesive Layers
Adhesive layers are used to bond the conductive layers to the substrate material. The most common adhesives used in PCB laminates are:
- Epoxy resin
- Acrylic adhesive
- Phenolic resin
The choice of adhesive depends on the required bond strength, thermal stability, and compatibility with the substrate and conductive materials.
Manufacturing Process of PCB Laminates
The manufacturing process of PCB laminates involves several steps to ensure the desired properties and quality. The main steps in the manufacturing process include:
-
Impregnation: The substrate material (e.g., fiberglass cloth) is impregnated with the resin (e.g., epoxy) to form a prepreg (pre-impregnated) sheet.
-
Layup: The prepreg sheets, along with the copper foil, are stacked in the desired order to form the PCB laminate structure.
-
Pressing: The stacked layers are placed in a press and subjected to high pressure and temperature. This process allows the resin to flow and bond the layers together, forming a solid laminate.
-
Cooling: The laminate is cooled to room temperature, allowing the resin to fully cure and solidify.
-
Cutting: The laminate sheet is cut to the desired size and shape using precision cutting tools.
-
Surface Treatment: The copper surface of the laminate may undergo additional treatments, such as brushing, polishing, or chemical cleaning, to improve its surface finish and adhesion properties.
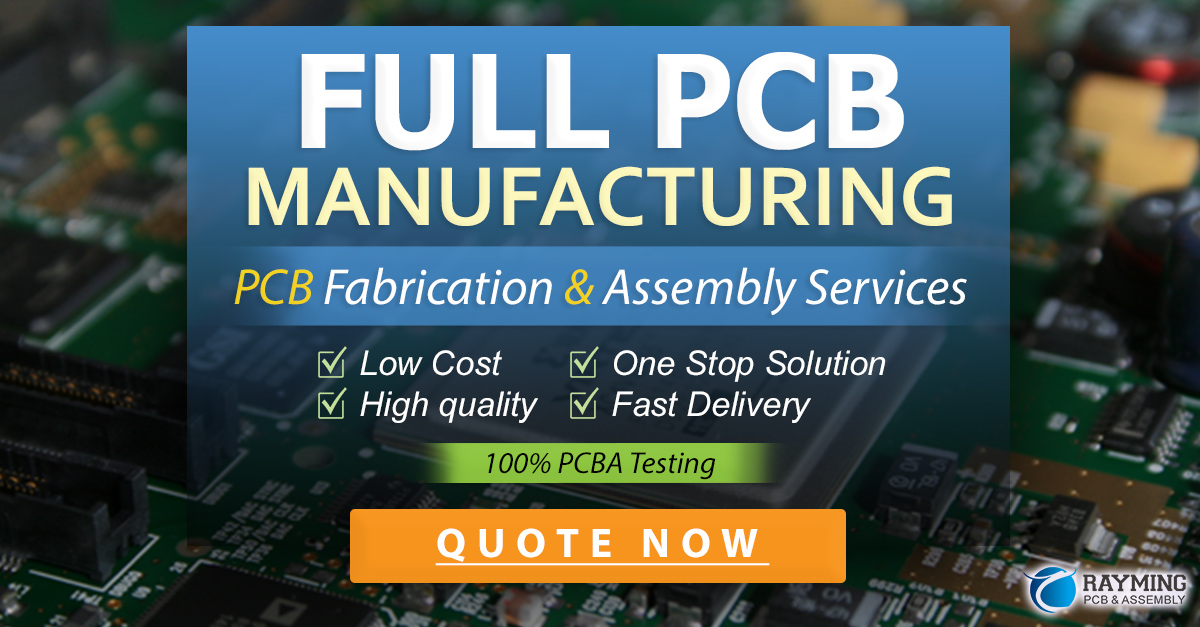
Factors Affecting PCB Laminate Performance
Several factors can affect the performance of PCB laminates in electronic devices. These factors include:
Environmental Conditions
PCB laminates are exposed to various environmental conditions during their operation, such as temperature fluctuations, humidity, and chemical exposure. The choice of laminate material should consider the expected environmental conditions to ensure reliable performance.
Manufacturing Process
The quality of the manufacturing process can impact the performance of PCB laminates. Proper control of parameters such as pressure, temperature, and curing time is essential to achieve the desired properties and minimize defects.
Thermal Management
The thermal management of PCB laminates is crucial to prevent overheating and ensure reliable operation. Factors such as the thermal conductivity of the substrate material, the layout of the conductive layers, and the use of thermal vias can influence the thermal performance of the PCB.
Frequently Asked Questions (FAQ)
-
What is the difference between FR-4 and High Tg FR-4 laminates?
FR-4 and High Tg FR-4 laminates differ in their glass transition temperature (Tg). High Tg FR-4 laminates have a higher Tg, typically around 170-180 °C, compared to standard FR-4, which has a Tg of 125-135 °C. The higher Tg of High Tg FR-4 laminates makes them more suitable for applications that require higher operating temperatures and improved thermal stability. -
Can PCB laminates be recycled?
Yes, PCB laminates can be recycled. The recycling process typically involves separating the metal components (e.g., copper) from the substrate material. The recovered metals can be reused in the production of new PCBs or other applications. However, the recycling process can be complex and may require specialized facilities and techniques. -
What are the advantages of using polyimide laminates?
Polyimide laminates offer several advantages, including excellent thermal stability, chemical resistance, and mechanical strength. They can withstand extreme temperatures, making them suitable for high-reliability applications in aerospace, military, and high-temperature environments. Polyimide laminates also have a low dielectric constant and dissipation factor, which is beneficial for high-frequency applications. -
How does the thickness of the copper foil affect PCB performance?
The thickness of the copper foil in PCB laminates influences the current-carrying capacity and signal integrity of the circuit. Thicker copper foils can handle higher currents and provide better heat dissipation. However, thicker foils also increase the overall thickness of the PCB and may require wider trace widths and spacing. The choice of copper foil thickness depends on the specific requirements of the application, such as power handling, signal speed, and manufacturing constraints. -
What are the challenges in manufacturing PCB laminates?
Manufacturing PCB laminates presents several challenges, including ensuring uniform resin distribution, maintaining precise layer alignment, and controlling the curing process. Uneven resin distribution can lead to voids or delamination, while misaligned layers can cause signal integrity issues. Proper control of the curing process is essential to achieve the desired mechanical and electrical properties of the laminate. Additionally, the handling and storage of the raw materials, such as prepregs and copper foils, require careful attention to prevent contamination and maintain their quality.
Conclusion
PCB laminates are the backbone of electronic devices, providing the necessary insulation, mechanical support, and conductive pathways for electrical signals. The composition of PCB laminates, including the substrate material, conductive layers, and adhesive layers, plays a crucial role in determining their performance and reliability.
Understanding the properties and characteristics of different PCB laminate materials, such as FR-4, High Tg FR-4, and polyimide, is essential for selecting the appropriate laminate for a given application. Factors such as environmental conditions, thermal management, and manufacturing process control also influence the performance of PCB laminates.
As electronic devices continue to advance and push the boundaries of performance, the development of new PCB laminate materials and manufacturing techniques will be crucial to meet the evolving demands of the industry. By carefully considering the composition, properties, and manufacturing process of PCB laminates, designers and manufacturers can ensure the reliability and functionality of electronic devices in a wide range of applications.
No responses yet