Introduction to High-TG-PCB
High-TG-PCB refers to printed circuit boards (PCBs) that are made using high glass transition temperature (Tg) materials. The glass transition temperature is the point at which a polymer substrate changes from a rigid, glassy material to a more compliant, rubbery state. In PCBs, a high Tg value is desirable for applications that require greater thermal stability and reliability.
What Makes High-TG-PCB Different?
Compared to standard FR-4 PCBs, which have a Tg around 130-140°C, high-TG-PCB materials boast glass transition temperatures ranging from 170°C to over 200°C. This increased thermal resistance offers several advantages:
- Improved dimensional stability at elevated temperatures
- Reduced thermal expansion and warping
- Better resistance to thermal stress and cycling
- Enhanced durability in harsh environments
These properties make high-TG-PCB an ideal choice for applications that involve high operating temperatures, such as automotive electronics, aerospace systems, and power electronics.
Materials Used in High-TG-PCB
Several materials are commonly used in the manufacture of high-TG-PCB, each with its own unique set of properties and advantages.
High-Tg FR-4
High-Tg FR-4 is an enhanced version of the standard FR-4 material, with glass transition temperatures ranging from 170°C to 180°C. This material offers improved thermal stability and mechanical properties while maintaining the familiarity and ease of processing associated with traditional FR-4.
Polyimide
Polyimide (PI) is a high-performance polymer known for its excellent thermal stability, with glass transition temperatures exceeding 250°C. PI-based PCBs offer superior resistance to heat, chemicals, and mechanical stress, making them suitable for the most demanding applications. However, PI is more expensive and challenging to process compared to FR-4 materials.
High-Tg Epoxy
High-Tg epoxy materials, such as FR-5 and FR-6, offer glass transition temperatures between 170°C and 200°C. These materials provide a balance of thermal performance, mechanical strength, and processability, making them a popular choice for high-reliability applications.
Comparison of High-TG-PCB Materials
The following table compares the key properties of the most common high-TG-PCB materials:
Material | Glass Transition Temperature (Tg) | Thermal Expansion Coefficient (CTE) | Dielectric constant (Dk) | Dissipation Factor (Df) |
---|---|---|---|---|
High-Tg FR-4 | 170-180°C | 12-15 ppm/°C | 4.2-4.6 | 0.02-0.03 |
Polyimide | >250°C | 12-20 ppm/°C | 3.4-3.6 | 0.002-0.003 |
FR-5 | 170-180°C | 12-15 ppm/°C | 4.0-4.4 | 0.02-0.03 |
FR-6 | 190-200°C | 10-14 ppm/°C | 4.4-4.8 | 0.02-0.03 |
Manufacturing Process of High-TG-PCB
The manufacturing process for high-TG-PCB is similar to that of standard PCBs, with a few key differences to accommodate the unique properties of the high-performance materials.
Substrate Preparation
The high-Tg substrate material is cut to size and cleaned to remove any contaminants. Copper foil is then laminated onto the substrate using heat and pressure. The lamination process for high-TG-PCB may require higher temperatures and pressures compared to standard FR-4 to ensure proper bonding.
Drilling and Plating
Holes are drilled into the laminated substrate to accommodate through-hole components and vias. The holes are then plated with copper to create electrical connections between layers. High-TG-PCB materials may require specialized drill bits and plating solutions to maintain the integrity of the holes.
Patterning and Etching
The desired circuit pattern is transferred onto the copper-clad substrate using photoresist and exposure to UV light. The exposed copper is then etched away, leaving behind the designed circuit traces. High-TG-PCB materials may require adjustments to the etching process parameters to ensure accurate and reliable patterning.
Solder Mask and Silkscreen
A solder mask is applied to the PCB to protect the copper traces from oxidation and short-circuits. Silkscreen printing is then used to add component labels, logos, and other markings to the board. High-TG-PCB materials may require specialized solder mask and silkscreen inks that can withstand elevated temperatures.
Assembly and Testing
The completed high-TG-PCB is populated with components using either through-hole or Surface-mount technology. The assembled board undergoes a series of tests to ensure proper functionality and reliability, including visual inspection, electrical testing, and thermal cycling.
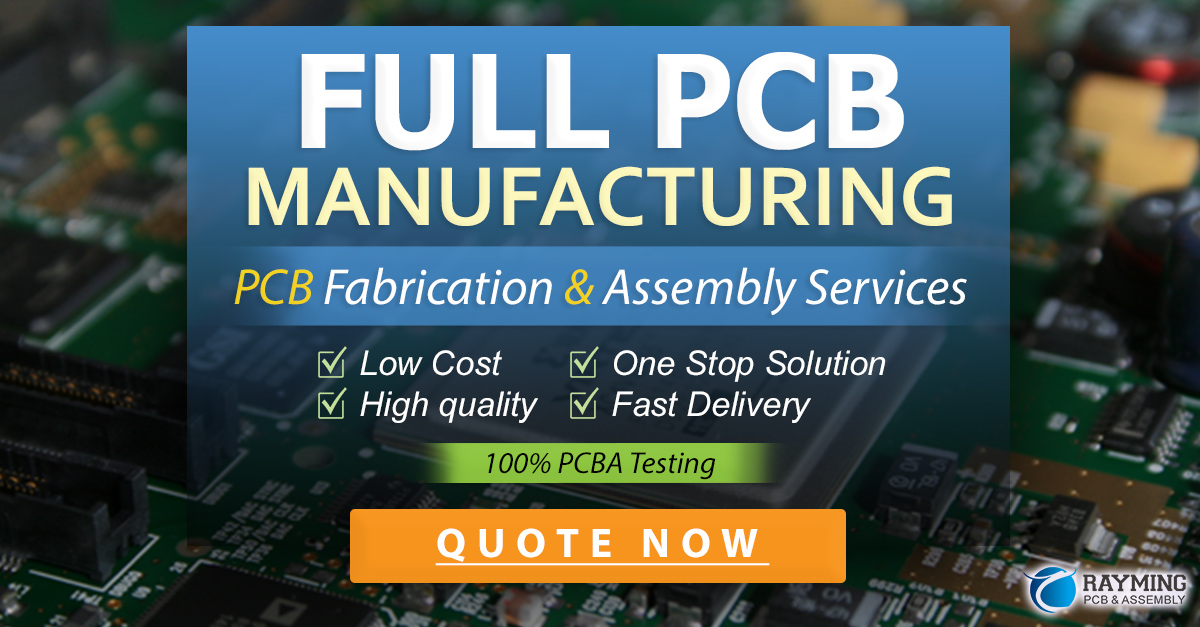
Applications of High-TG-PCB
High-TG-PCB finds use in a wide range of industries and applications where thermal stability, reliability, and durability are critical.
Automotive Electronics
The automotive industry has increasingly adopted high-TG-PCB for electronic systems that are exposed to high operating temperatures, such as engine control units, power inverters, and battery management systems. High-TG-PCB materials ensure reliable performance in the harsh environment under the hood, where temperatures can exceed 150°C.
Aerospace and Defense
Aerospace and defense applications demand the utmost reliability and performance from electronic components. High-TG-PCB is used in avionics, radar systems, and satellite communications equipment to withstand extreme temperature fluctuations, vibrations, and other environmental stresses.
Power Electronics
Power electronic devices, such as high-power LED lights, motor drives, and solar inverters, generate significant heat during operation. High-TG-PCB materials provide the necessary thermal stability to prevent deformation and ensure reliable performance in these demanding applications.
Industrial Automation
Industrial automation systems, including robotics, machine vision, and process control equipment, often operate in harsh environments with elevated temperatures and exposure to chemicals. High-TG-PCB offers the durability and resistance needed to maintain reliable operation in these challenging conditions.
Advantages of Using High-TG-PCB
Choosing high-TG-PCB for your application offers several key advantages over traditional PCB materials:
-
Enhanced thermal stability: High-TG-PCB materials maintain their dimensional stability and mechanical properties at elevated temperatures, reducing the risk of warping, delamination, and other thermal-induced failures.
-
Improved reliability: The increased thermal resistance of high-TG-PCB translates to better long-term reliability, particularly in applications that involve frequent thermal cycling or exposure to high operating temperatures.
-
Reduced thermal expansion: High-TG-PCB materials have lower coefficients of thermal expansion (CTE) compared to standard FR-4, minimizing the risk of thermal stress and strain on components and solder joints.
-
Compatibility with lead-free soldering: The higher glass transition temperatures of high-TG-PCB materials make them well-suited for lead-free soldering processes, which require higher reflow temperatures compared to traditional tin-lead soldering.
-
Durability in harsh environments: High-TG-PCB offers superior resistance to chemicals, moisture, and other environmental factors, ensuring reliable performance in demanding industrial and automotive applications.
Challenges and Considerations
While high-TG-PCB offers numerous benefits, there are also some challenges and considerations to keep in mind when designing and manufacturing these boards:
-
Higher material costs: High-TG-PCB materials, particularly polyimide, are more expensive than standard FR-4, which can increase the overall cost of the PCB.
-
Specialized processing requirements: The unique properties of high-TG-PCB materials may require adjustments to manufacturing processes, such as lamination, drilling, and etching, to ensure optimal results.
-
Limited availability: Some high-TG-PCB materials may have longer lead times or limited availability compared to standard FR-4, which can impact project timelines and costs.
-
Design considerations: The different thermal and mechanical properties of high-TG-PCB materials may require adjustments to the PCB Design, such as modified trace widths, via sizes, and component placement, to ensure optimal performance and reliability.
Frequently Asked Questions
1. What is the difference between standard FR-4 and high-TG-PCB?
Standard FR-4 PCBs have a glass transition temperature (Tg) around 130-140°C, while high-TG-PCB materials offer Tg values ranging from 170°C to over 250°C. This higher Tg provides improved thermal stability, reduced thermal expansion, and better durability in harsh environments.
2. Can high-TG-PCB be used for all applications?
While high-TG-PCB offers superior thermal and mechanical properties, it may not be necessary or cost-effective for all applications. Standard FR-4 PCBs are still suitable for many consumer electronics and general-purpose applications where thermal requirements are less demanding.
3. How much more expensive is high-TG-PCB compared to standard PCBs?
The cost difference between high-TG-PCB and standard PCBs can vary depending on the specific material, volume, and manufacturing requirements. In general, high-TG-PCB materials can be 20-50% more expensive than standard FR-4, with polyimide being the most costly option.
4. Are there any special design considerations when using high-TG-PCB?
Yes, the unique properties of high-TG-PCB materials may require adjustments to the PCB design to ensure optimal performance and reliability. This can include modifying trace widths, via sizes, and component placement to account for the different thermal and mechanical characteristics of the high-Tg materials.
5. How do I choose the right high-TG-PCB material for my application?
Choosing the right high-TG-PCB material depends on the specific requirements of your application, such as the operating temperature range, environmental factors, and budget constraints. Consult with a PCB manufacturer or material supplier to discuss your needs and determine the most suitable high-TG-PCB material for your project.
Conclusion
High-TG-PCB is an essential technology for applications that demand superior thermal stability, reliability, and durability. By utilizing materials with glass transition temperatures ranging from 170°C to over 250°C, high-TG-PCB offers improved dimensional stability, reduced thermal expansion, and enhanced resistance to harsh environments compared to standard FR-4 PCBs.
While high-TG-PCB materials may come with higher costs and specialized processing requirements, the benefits they provide in terms of long-term reliability and performance make them a critical choice for industries such as automotive, aerospace, power electronics, and industrial automation.
As technology continues to advance and the demand for high-performance electronics grows, the importance of high-TG-PCB will only continue to increase. By understanding the materials, manufacturing processes, and design considerations involved in high-TG-PCB, engineers and manufacturers can unlock the full potential of this technology to create more robust, reliable, and efficient electronic systems for a wide range of applications.
No responses yet