Characteristics of High-Frequency PCBs
High-frequency PCBs have several unique characteristics that distinguish them from standard PCBs:
-
Material Properties: HF PCBs use substrate materials with low dielectric constant (Dk) and dissipation factor (Df) to minimize signal loss and distortion at high frequencies. Common materials include PTFE, Rogers, and Isola.
-
Controlled Impedance: The PCB traces are designed to have specific impedance values (typically 50Ω or 75Ω) to match the impedance of connected components and prevent signal reflections.
-
Thin Dielectric Layers: The dielectric layers between copper layers are made as thin as possible to reduce signal propagation delay and losses.
-
Tight Tolerances: HF PCBs require tighter manufacturing tolerances for trace width, spacing, and hole sizes to maintain signal integrity and avoid impedance mismatches.
Structure of High-Frequency PCBs
A typical high-frequency PCB consists of the following layers:
-
Copper Layers: HF PCBs usually have multiple copper layers for signal routing, power distribution, and grounding. The number of layers depends on the complexity of the design and the required performance.
-
Dielectric Layers: The dielectric layers provide insulation between the copper layers and determine the board’s electrical properties. The dielectric material is chosen based on its Dk and Df values at the operating frequency.
-
Solder Mask: The solder mask is a protective coating applied over the outer copper layers to prevent short circuits and improve solderability.
-
Silkscreen: The silkscreen layer contains text and symbols for component placement and identification.
Types of High-Frequency PCBs
There are several types of high-frequency PCBs, each designed for specific applications and frequency ranges:
1. Microwave PCBs
Microwave PCBs operate at frequencies from 1 GHz to 30 GHz and are used in radar systems, satellite communication, and wireless infrastructure. They use specialized materials like PTFE and Rogers laminates with very low Dk and Df values. Microwave PCBs often incorporate features like:
- Grounded coplanar waveguides (GCPW)
- Microstrip transmission lines
- Stripline transmission lines
- Cavity backed antennas
2. Millimeter-Wave PCBs
Millimeter-wave PCBs operate at frequencies from 30 GHz to 300 GHz and are used in 5G wireless networks, automotive radar, and imaging systems. They require extremely low-loss materials and precise manufacturing techniques to maintain signal integrity at these high frequencies. Millimeter-wave PCBs often use:
- Substrate integrated waveguides (SIW)
- Microstrip transmission lines with thin substrates
- Flip-chip interconnects
- Wafer-level packaging
3. RF PCBs
RF PCBs operate at frequencies from 500 MHz to 2.5 GHz and are used in wireless communication devices, GPS, and Bluetooth modules. They use materials with moderate Dk and Df values like FR-4 and Rogers 4000 series. RF PCBs typically include:
- Controlled impedance transmission lines
- Impedance matching networks
- Shielding and grounding techniques
- Surface mount components
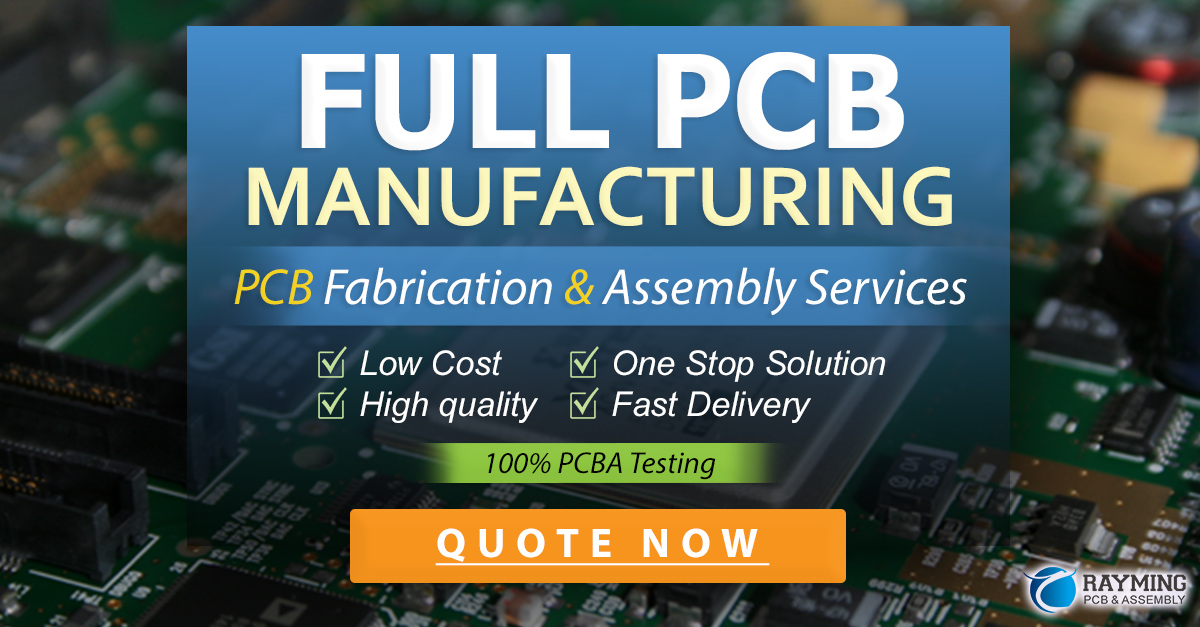
High-Frequency PCB Materials
The choice of substrate material is crucial for high-frequency PCBs to ensure optimal signal propagation and minimal losses. Some common materials used in HF PCBs are:
Material | Dielectric Constant (Dk) | Dissipation Factor (Df) | Applications |
---|---|---|---|
FR-4 | 4.3 – 4.7 | 0.02 – 0.03 | General purpose, low-cost RF PCBs |
Rogers 4003C | 3.38 @ 10 GHz | 0.0027 @ 10 GHz | Microwave, millimeter-wave, high-speed digital |
Rogers RT/duroid 5880 | 2.20 @ 10 GHz | 0.0009 @ 10 GHz | Microwave, millimeter-wave, radar |
Isola I-Tera MT40 | 3.45 @ 10 GHz | 0.0030 @ 10 GHz | High-speed digital, automotive radar |
PTFE (Teflon) | 2.1 – 2.4 | 0.0002 – 0.0008 | Microwave, millimeter-wave, high-power RF |
High-Frequency PCB Design Considerations
Designing high-frequency PCBs requires careful consideration of several factors to ensure optimal performance and signal integrity:
-
Impedance Matching: Ensure proper impedance matching between the PCB traces, components, and connectors to minimize reflections and signal distortion.
-
Transmission Line Design: Use appropriate transmission line structures (e.g., microstrip, stripline, GCPW) based on the frequency, substrate material, and layout constraints.
-
Grounding and Shielding: Implement proper grounding and shielding techniques to reduce electromagnetic interference (EMI) and crosstalk between signals.
-
Component Placement: Optimize component placement to minimize signal path lengths, avoid coupling, and ensure proper heat dissipation.
-
Via Design: Use minimum via sizes and avoid unnecessary vias to reduce signal discontinuities and reflections.
-
Simulation and Verification: Perform electromagnetic simulations and measurements to verify the PCB design’s performance and make necessary adjustments.
Manufacturing High-Frequency PCBs
Manufacturing high-frequency PCBs requires specialized equipment and processes to achieve the required precision and quality:
-
Material Handling: The low-loss materials used in HF PCBs are often sensitive to moisture and temperature, requiring controlled storage and processing conditions.
-
Laser Drilling: High-speed laser drilling is used to create small, precise vias and holes in the PCB.
-
Photolithography: High-resolution photolithography is employed to create fine-pitch traces and features on the PCB.
-
Plating: Advanced plating techniques, such as semi-additive process (SAP) or modified semi-additive process (mSAP), are used to achieve thin, uniform copper traces.
-
Lamination: The PCB layers are laminated together under high pressure and temperature to ensure proper bonding and dimensional stability.
-
Testing and Inspection: Rigorous testing and inspection procedures are performed to verify the PCB’s electrical performance, signal integrity, and mechanical quality.
Applications of High-Frequency PCBs
High-frequency PCBs find applications in various industries and products, including:
- 5G wireless communication systems
- Radar systems for automotive, aviation, and defense
- Satellite communication equipment
- High-speed data networks and servers
- Millimeter-wave imaging and sensing devices
- IoT devices and smart sensors
- Medical imaging and diagnostic equipment
- Aerospace and avionics systems
As technology advances and the demand for higher data rates and frequencies continues to grow, the importance of high-frequency PCBs will only increase in the future.
FAQ
1. What is the difference between high-frequency PCBs and standard PCBs?
High-frequency PCBs are designed to handle signals with frequencies above 500 MHz, while standard PCBs are used for lower-frequency applications. HF PCBs use specialized low-loss materials, controlled impedance traces, and require tighter manufacturing tolerances compared to standard PCBs.
2. What are the most common materials used in high-frequency PCBs?
The most common materials used in high-frequency PCBs are PTFE (Teflon), Rogers laminates (e.g., RO4003C, RT/duroid 5880), and low-loss variants of FR-4. These materials have low dielectric constant (Dk) and dissipation factor (Df) values, which minimize signal loss and distortion at high frequencies.
3. What are the key design considerations for high-frequency PCBs?
The key design considerations for high-frequency PCBs include impedance matching, transmission line design, grounding and shielding, component placement, via design, and simulation and verification. Careful attention to these factors ensures optimal signal integrity and performance.
4. What are the challenges in manufacturing high-frequency PCBs?
Manufacturing high-frequency PCBs presents challenges due to the sensitive low-loss materials, tight tolerances, and advanced processing techniques required. These include laser drilling, high-resolution photolithography, advanced plating methods, and strict testing and inspection procedures.
5. What are the main applications of high-frequency PCBs?
High-frequency PCBs are used in various applications, such as 5G wireless communication, radar systems, satellite communication, high-speed data networks, millimeter-wave imaging, IoT devices, medical imaging equipment, and aerospace and avionics systems. As technology advances, the demand for HF PCBs is expected to grow in the future.
No responses yet