Introduction to Functional Testing
Functional testing is a crucial step in the printed circuit board (PCB) assembly process that ensures the proper functioning of the assembled board. It is a type of testing that verifies whether the PCB performs as intended, according to the design specifications and requirements. Functional testing is usually performed after the PCB has undergone other types of testing, such as in-circuit testing (ICT) and flying probe testing.
The Importance of Functional Testing
Functional testing is essential for several reasons:
- Quality Assurance: It ensures that the PCB functions as expected and meets the required quality standards.
- Defect Detection: Functional testing helps identify any defects or issues that may have been missed during previous testing stages.
- Reliability: By verifying the proper functioning of the PCB, functional testing contributes to the overall reliability of the final product.
- Customer Satisfaction: Delivering a fully functional product that meets the customer’s requirements is essential for maintaining customer satisfaction and trust.
Types of Functional Testing
There are several types of functional testing that can be performed on a PCB, depending on the specific requirements and complexity of the board. Some common types include:
Power-On Testing
Power-on testing is the first step in functional testing. It involves applying power to the PCB and verifying that it powers up correctly without any issues, such as short circuits or excessive current draw.
Boundary Scan Testing
Boundary scan testing, also known as JTAG (Joint Test Action Group) testing, is a method that uses a special test access port (TAP) to test the interconnections between integrated circuits (ICs) on the PCB. This type of testing is particularly useful for detecting issues related to solder joints, short circuits, and open circuits.
Functional Test Fixtures
Functional test fixtures are custom-designed jigs that allow for the testing of specific functions of the PCB. These fixtures typically include connectors, switches, and other components that simulate the actual operating conditions of the board. Functional test fixtures are used to verify the proper functioning of various subsystems on the PCB, such as input/output ports, communication interfaces, and power management.
Automated Functional Testing
Automated functional testing involves the use of specialized software and hardware to perform functional tests on the PCB. This type of testing is particularly useful for high-volume production, as it allows for faster and more efficient testing compared to manual methods. Automated functional testing systems can be programmed to perform a wide range of tests, including power-on testing, boundary scan testing, and functional test fixturing.
The Functional Testing Process
The functional testing process typically involves the following steps:
-
Test Planning: The first step is to develop a comprehensive test plan that outlines the specific tests to be performed, the test criteria, and the expected results. This plan should be based on the design specifications and requirements of the PCB.
-
Test Setup: The next step is to set up the test environment, which may include functional test fixtures, automated testing systems, and other necessary equipment. The PCB is then connected to the test setup, and the necessary software and firmware are loaded.
-
Test Execution: Once the test setup is complete, the functional tests are executed according to the test plan. This may involve manually triggering certain functions or running automated test sequences.
-
Results Analysis: After the tests are complete, the results are analyzed to determine whether the PCB has passed or failed. Any issues or defects that are identified during testing are documented and investigated further.
-
Reporting and Documentation: Finally, a detailed report is generated that summarizes the test results, including any issues or defects that were found and the corrective actions taken. This report serves as a record of the functional testing process and is used for quality assurance and traceability purposes.
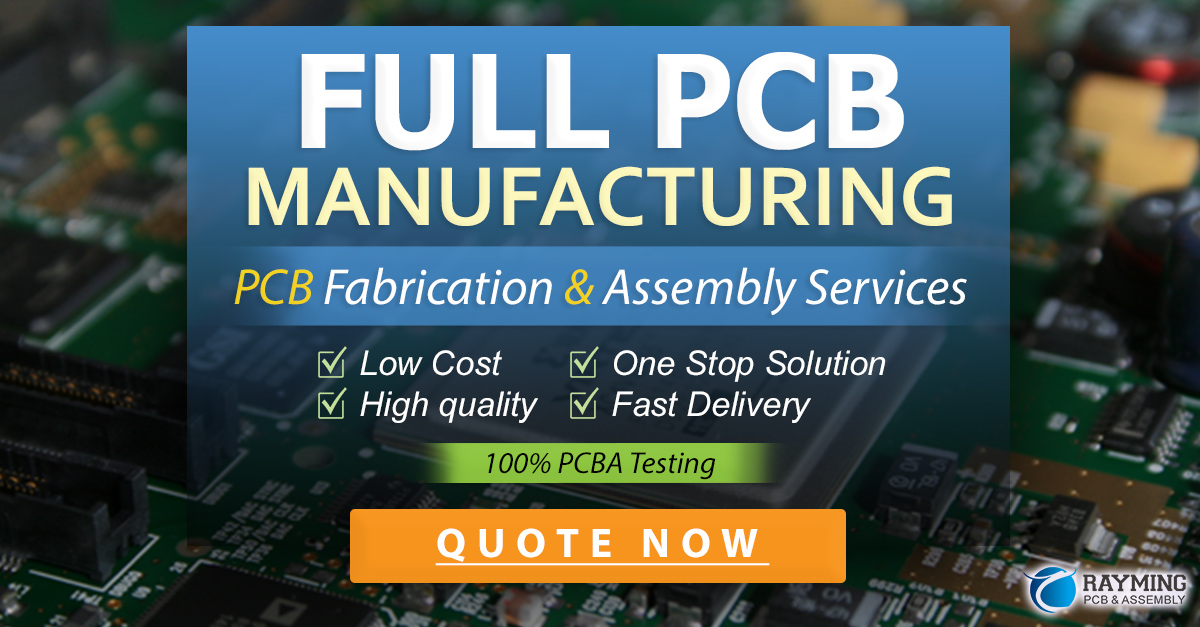
Benefits of Functional Testing
Functional testing offers several benefits in the PCB Assembly process:
-
Early Defect Detection: By performing functional testing early in the assembly process, defects and issues can be identified and corrected before the PCB is integrated into the final product. This can save time and money by avoiding costly rework and delays later in the production process.
-
Improved Quality: Functional testing helps ensure that the PCB meets the required quality standards and functions as intended. This reduces the risk of defective products reaching the customer and improves overall product quality.
-
Increased Reliability: By verifying the proper functioning of the PCB under various conditions, functional testing contributes to the overall reliability of the final product. This can help reduce warranty claims and improve customer satisfaction.
-
Compliance with Standards: Functional testing can help ensure that the PCB complies with relevant industry standards and regulations, such as those related to safety, electromagnetic compatibility (EMC), and environmental requirements.
Challenges in Functional Testing
Despite its many benefits, functional testing also presents some challenges:
-
Test Coverage: Ensuring adequate test coverage can be challenging, especially for complex PCBs with many functions and subsystems. It is important to develop a comprehensive test plan that covers all critical functions and scenarios.
-
Test Fixture Design: Designing and building functional test fixtures can be time-consuming and costly, especially for custom PCBs. It is important to strike a balance between test coverage and fixture complexity to optimize the testing process.
-
Test Automation: Implementing automated functional testing can be challenging, as it requires specialized software and hardware. It is important to choose the right automation tools and develop robust test scripts to ensure reliable and efficient testing.
-
Debugging and Troubleshooting: When issues or defects are identified during functional testing, debugging and troubleshooting can be complex and time-consuming. It is important to have a systematic approach to problem-solving and to involve the appropriate experts and resources.
Best Practices for Functional Testing
To ensure the effectiveness and efficiency of functional testing, consider the following best practices:
-
Develop a Comprehensive Test Plan: A well-defined test plan is essential for ensuring adequate test coverage and avoiding gaps in testing. The plan should outline the specific tests to be performed, the test criteria, and the expected results.
-
Use Appropriate Test Equipment: Choose test equipment that is appropriate for the specific requirements of the PCB, such as functional test fixtures, automated testing systems, and boundary scan tools. Ensure that the equipment is properly calibrated and maintained.
-
Implement Test Automation: Where possible, implement automated functional testing to improve efficiency and reduce the risk of human error. Choose automation tools that are compatible with your PCB design and test requirements.
-
Collaborate with Design and Manufacturing Teams: Functional testing should be a collaborative effort involving the design, manufacturing, and quality assurance teams. Regular communication and feedback can help identify and resolve issues early in the process.
-
Document and Analyze Test Results: Maintain detailed records of test results, including any issues or defects that were identified and the corrective actions taken. Use this data to continuously improve the testing process and identify opportunities for optimization.
Functional Testing vs. Other Types of PCB Testing
Functional testing is just one of several types of testing that may be performed on a PCB during the assembly process. Other common types of testing include:
Testing Type | Description |
---|---|
In-Circuit Testing (ICT) | Verifies the presence, orientation, and value of individual components on the PCB using a bed-of-nails fixture. |
Flying Probe Testing | Uses moving probes to test the electrical continuity and component values on the PCB without the need for a custom fixture. |
Boundary Scan Testing | Tests the interconnections between ICs on the PCB using a special test access port (TAP). |
X-Ray Inspection | Uses X-ray imaging to inspect solder joints and other internal structures of the PCB for defects. |
Burn-In Testing | Subjects the PCB to elevated temperatures and voltages to identify early failures and improve reliability. |
Each type of testing has its own advantages and limitations, and the appropriate combination of tests will depend on the specific requirements and complexity of the PCB.
FAQ
-
What is the purpose of functional testing in PCB assembly?
Functional testing verifies that the assembLED PCB performs as intended, according to the design specifications and requirements. It ensures that the board functions properly and meets the required quality standards. -
When is functional testing typically performed in the PCB assembly process?
Functional testing is usually performed after the PCB has undergone other types of testing, such as in-circuit testing (ICT) and flying probe testing. It is one of the final steps in the assembly process before the board is integrated into the final product. -
What are some common types of functional testing for PCBs?
Common types of functional testing for PCBs include power-on testing, boundary scan testing, functional test fixturing, and automated functional testing. The specific types of tests performed will depend on the requirements and complexity of the board. -
How does functional testing differ from other types of PCB testing, such as in-circuit testing (ICT)?
Functional testing focuses on verifying the overall functionality of the assembled PCB, while in-circuit testing (ICT) verifies the presence, orientation, and value of individual components on the board. Functional testing is typically performed after ICT and other types of testing have been completed. -
What are some best practices for implementing functional testing in PCB assembly?
Some best practices for functional testing include developing a comprehensive test plan, using appropriate test equipment, implementing test automation where possible, collaborating with design and manufacturing teams, and documenting and analyzing test results. By following these practices, you can ensure the effectiveness and efficiency of the functional testing process.
Conclusion
Functional testing is a critical step in the PCB assembly process that ensures the proper functioning of the assembled board according to the design specifications and requirements. It involves various types of testing, such as power-on testing, boundary scan testing, functional test fixturing, and automated functional testing.
Functional testing offers several benefits, including early defect detection, improved quality, increased reliability, and compliance with industry standards. However, it also presents challenges, such as ensuring adequate test coverage, designing test fixtures, implementing test automation, and debugging and troubleshooting issues.
To overcome these challenges and ensure the effectiveness of functional testing, it is important to follow best practices such as developing a comprehensive test plan, using appropriate test equipment, implementing test automation, collaborating with design and manufacturing teams, and documenting and analyzing test results.
By incorporating functional testing into the PCB assembly process and following best practices, you can ensure that your PCBs meet the required quality standards and function as intended, ultimately leading to improved product quality, reliability, and customer satisfaction.
No responses yet