Physical Properties of FR4
FR4 has excellent mechanical, electrical, and thermal properties that make it suitable for many different uses:
Property | Value |
---|---|
Density | 1.850 g/cm³ |
Thermal Conductivity | 0.29 W/m·K |
Dielectric Constant @ 1MHz | 4.8 |
Dissipation Factor @ 1MHz | 0.017 |
Dielectric Strength | 20 kV/mm |
Flexural Strength | 415 MPa |
Tensile Strength | 320 MPa |
Water Absorption | 0.15% |
The fiberglass cloth provides mechanical strength and electrical insulation while the epoxy resin is both a binder and a flame retardant. FR4 has good strength to weight ratio, is stiff, and retains its properties over a wide temperature range from cryogenic temperatures up to 130°C. It maintains its high mechanical values and electrical insulating qualities in both dry and humid conditions.
Main Applications of FR4
Printed Circuit Boards (PCBs)
The primary application of FR4 is for making rigid printed circuit boards. The majority of rigid PCBs produced worldwide are made from FR4. It strikes an excellent balance of properties and cost for typical PCB applications:
- Mechanically strong to protect components
- Good electrical insulator
- Retains properties in various conditions
- Flame resistant for safety
- Can be drilled and machined
- Relatively affordable
Copper clad FR4 sheets form the substrate that electronic circuits are printed onto. Circuits are etched from the copper and then components are attached by soldering or other means. FR4 provides a rigid backing that supports and protects the circuitry. Multi-layer FR4 PCBs can be laminated together with heat and adhesives.
Electrical Insulation
FR4’s electrical insulating properties, mechanical strength, and flame resistance make it well suited for many electrical applications beyond circuit boards:
- Terminal boards
- Transformers
- Insulators
- Switch gear components
- Arc shields
- Electrical housings
Structural Components
FR4 can be a lightweight and strong material for certain structural applications:
- Aerospace components
- Automotive components
- Radomes
- Hard drive actuator arms
- Industrial equipment
It offers a high strength to weight ratio and maintains its properties over a wide temperature range. FR4 shapes can be machined, stamped, or molded as needed.
Other Applications
Some other niche uses for FR4 include:
- Medical instruments
- Orthodontic appliances
- Prosthetics
- Acoustic equipment
- Sports equipment
FR4’s unique combination of properties allows it to be used for many specialized applications beyond its primary use in electronics.
Advantages of Using FR4
FR4 offers many benefits as a material:
- Excellent electrical insulator
- High mechanical strength and stiffness
- Lightweight
- Flame resistant for safety
- Retains properties in harsh conditions
- Good thermal stability
- Resistant to chemicals and solvents
- Relatively low cost
These advantages make FR4 the go-to material for rigid PCBs as well as many other applications that require its combination of mechanical, thermal, and electrical properties. It is widely available in sheets, rods, tubes and other shapes.
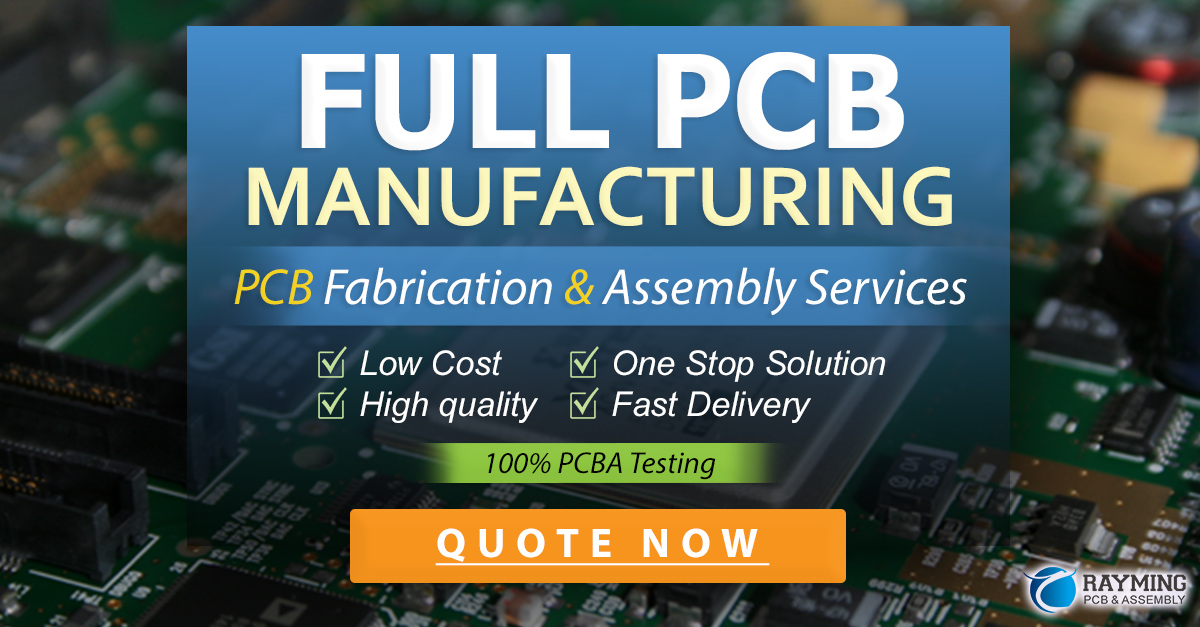
Disadvantages of FR4
While FR4 is a very useful material, it does have some limitations:
- Not suitable for very high frequencies
- Can be brittle if machined incorrectly
- Limited maximum operating temperature around 130-140°C
- Requires special treatment for outdoor UV exposure
- Can absorb small amounts of moisture over time
For most applications these limitations of FR4 are acceptable. However, for very high frequency circuits, outdoor exposure, or high temperature environments, other materials may need to be considered.
Manufacturing Processes Used with FR4
FR4 starts as glass fibers woven into a cloth which is then impregnated with epoxy resin. Heat and pressure are applied to cure the resin, creating a solid laminated sheet. Additional processes are then used to convert the raw FR4 into finished products.
Common conversion processes include:
- Drilling
- Milling
- Routing
- Stamping
- Laser cutting
- Molding
Copper foils can be laminated to one or both sides of FR4 sheets to create copper clad laminates ready for PCB fabrication. Multiple FR4 layers can be laminated together under heat and pressure to create multi-layer circuit boards.
Comparison to Other Materials
FR4 is one of the most popular materials for making rigid PCBs, but it is not the only option. Some common alternatives include:
Material | Advantages | Disadvantages |
---|---|---|
Aluminum | Excellent thermal conductivity | Expensive, needs insulating layer |
Polyimide | High temp tolerance, flexible | Expensive, moisture sensitive |
Ceramics | High strength, thermal conductivity | Brittle, expensive |
PTFE | Low dielectric loss, chemically inert | Expensive, difficult to process |
The choice of material depends on the specific requirements of the application and the trade-offs between performance and cost. FR4 offers a good balance of properties and affordability for a broad range of uses.
Environmental Impact and Recyclability of FR4
The production of FR4 does involve the use of some hazardous chemicals and resins which must be properly managed. However, the finished FR4 material is inert and does not pose a health risk in normal use.
FR4 waste from manufacturing processes can be recycled by grinding it into a fine powder and using it as a filler in new molding compounds. PCBs and other FR4 products can also be recycled at the end of their life to recover the precious metals and glasses used in them.
Proper recycling helps reduce the environmental impact of FR4 by keeping waste out of landfills and reducing the need for virgin raw materials. Many electronics recyclers now specialize in recovering valuable materials from PCBs and other FR4 products.
Future Developments in FR4 Technology
While FR4 is already a well-established material, there is ongoing research to enhance its properties and develop new variants for specific applications. Some areas of development include:
- High speed/low loss materials for higher frequencies
- Improved thermal conductivity
- Higher temperature stability
- Reduced moisture absorption
- Enhanced mechanical properties
- More environmentally friendly resins
These advancements will help expand the range of applications for FR4 and keep it a preferred material well into the future. Its combination of properties and affordability remain hard to beat for many uses.
Frequently Asked Questions
What does FR4 stand for?
FR4 stands for “Flame Retardant 4”, indicating a woven glass epoxy laminate with self-extinguishing flame retardant properties.
Is FR4 toxic?
No, cured FR4 material is inert and non-toxic under normal use. However, dust from machining processes should be avoided.
What temperature can FR4 withstand?
FR4 retains its properties up to about 130-140°C. Above these temperatures the material may start to degrade or deform.
Can FR4 be used outdoors?
Standard FR4 can degrade with prolonged UV and moisture exposure outdoors. Special variants with enhanced UV and moisture resistance are available for outdoor applications.
How can I recycle FR4?
FR4 waste can be sent to recycling facilities that specialize in recovering valuable metals and glasses from PCBs and other electronic waste. Many electronics recyclers now offer this service.
No responses yet