Composition and Structure of FR4 PCB
FR4 is a designation for “Flame Retardant 4,” indicating the material’s flame-retardant properties. The main components of FR4 PCB are:
- Fiberglass cloth: This provides mechanical strength and dimensional stability to the board.
- Epoxy resin: The fiberglass cloth is impregnated with this thermosetting polymer, which offers excellent insulation and heat resistance properties.
- Copper foil: Thin layers of copper foil are laminated onto one or both sides of the FR4 substrate to create conductive paths for electrical signals.
The structure of an FR4 PCB typically consists of multiple layers:
- Core layer: The central layer made of the FR4 material.
- Prepreg layers: Additional layers of pre-impregnated fiberglass and epoxy resin used to bond the core and copper layers together.
- Copper layers: Conductive copper foil laminated onto the core and prepreg layers to form the circuit patterns.
- Solder mask: A protective coating applied over the copper traces to prevent short circuits and oxidation.
- Silkscreen: A printed layer used for labeling components and providing visual references on the PCB.
Properties and Advantages of FR4 PCB
FR4 PCB has several desirable properties that make it an ideal choice for a wide range of electronic applications:
-
Mechanical strength: The fiberglass reinforcement provides excellent mechanical strength and rigidity, making FR4 PCBs suitable for use in harsh environments and applications subject to vibration or impact.
-
Electrical insulation: The epoxy resin offers high electrical insulation, preventing current leakage and ensuring signal integrity.
-
Flame retardancy: FR4 material is designed to be flame-retardant, minimizing the risk of fire in electronic devices.
-
Thermal stability: FR4 PCBs have a glass transition temperature (Tg) of around 130°C to 140°C, allowing them to maintain their mechanical and electrical properties over a wide temperature range.
-
Moisture resistance: The material has low moisture absorption, which helps maintain its dimensional stability and prevents delamination.
-
Cost-effectiveness: FR4 is relatively inexpensive compared to other PCB materials, making it a cost-effective choice for many applications.
Applications of FR4 PCB
FR4 PCBs are used in a wide variety of electronic applications due to their versatility and reliability. Some common applications include:
- Consumer electronics: Smartphones, tablets, laptops, televisions, and home appliances.
- Industrial electronics: Process control systems, automation equipment, and power electronics.
- Automotive electronics: Engine control units, infotainment systems, and sensors.
- Medical devices: Diagnostic equipment, patient monitoring systems, and implantable devices.
- Aerospace and defense: Avionics, communication systems, and military equipment.
- Telecommunications: Routers, switches, and network equipment.
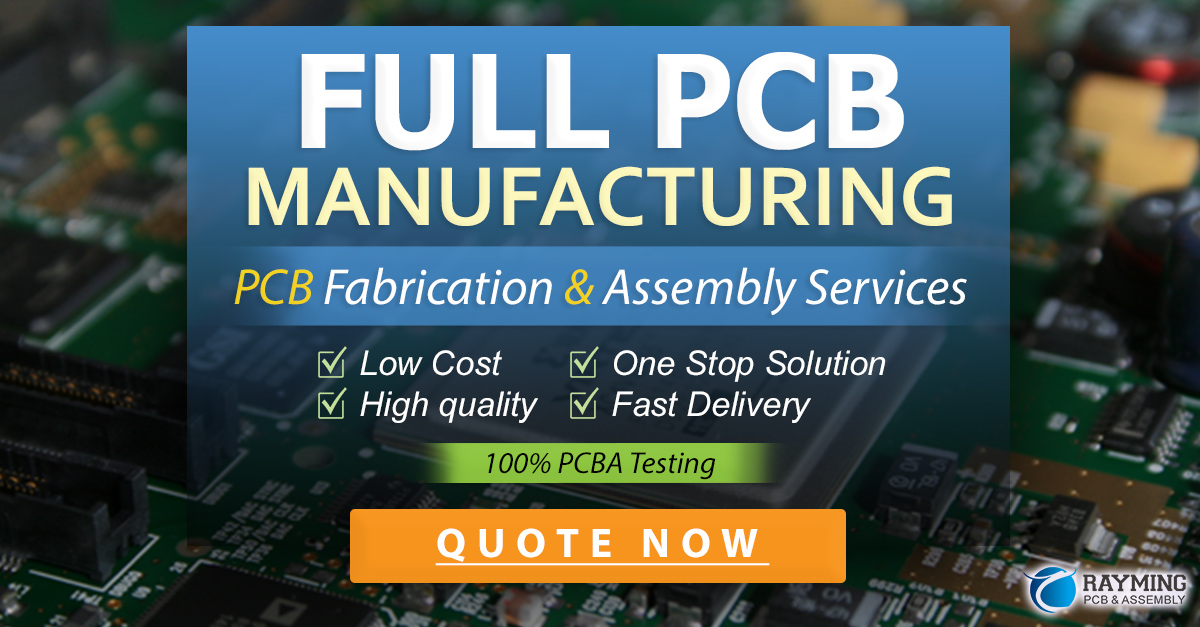
FR4 PCB Fabrication Process
The fabrication of FR4 PCBs involves several steps:
-
Design: The PCB layout is designed using electronic design automation (EDA) software, which generates the necessary files for manufacturing.
-
Material preparation: The FR4 substrate, copper foil, and prepreg layers are cut to the required sizes.
-
Lamination: The layers are stacked and laminated together under high pressure and temperature to form a solid board.
-
Drilling: Holes are drilled through the board for component leads and vias.
-
Copper patterning: The desired circuit pattern is transferred onto the copper layers using photolithography and etching processes.
-
Solder mask application: A protective solder mask is applied over the copper traces, leaving exposed areas for component soldering.
-
Surface finish: A surface finish, such as HASL (Hot Air Solder Leveling) or ENIG (Electroless Nickel Immersion Gold), is applied to the exposed copper to prevent oxidation and improve solderability.
-
Silkscreen printing: Labels and visual references are printed onto the board using silkscreen printing.
-
Electrical testing: The completed PCB undergoes electrical testing to ensure proper functionality and adherence to design specifications.
-
Singulation: The panel containing multiple PCBs is cut into individual boards.
FR4 PCB Specifications and Standards
FR4 PCBs are manufactured according to various industry standards to ensure consistent quality and performance. Some important specifications and standards include:
- IPC-4101: Specification for base materials for rigid and multilayer printed boards.
- IPC-6012: Qualification and performance specification for rigid printed boards.
- IPC-A-600: Acceptability of printed boards.
- UL 94: Standard for safety of flammability of plastic materials for parts in devices and appliances.
- NEMA LI 1: Industrial laminated thermosetting products.
These standards cover aspects such as material properties, dimensional tolerances, electrical characteristics, and quality requirements for FR4 PCBs.
Comparison with Other PCB Materials
While FR4 is the most common PCB material, there are other materials used for specific applications or requirements:
Material | Advantages | Disadvantages | Typical Applications |
---|---|---|---|
CEM-1 | Lower cost | Lower mechanical and thermal performance | Low-end consumer electronics |
CEM-3 | Better mechanical properties than CEM-1 | Higher cost than CEM-1 | Mid-range consumer electronics |
Polyimide | High-temperature resistance, flexibility | Higher cost, lower mechanical strength | Aerospace, military, and high-temperature applications |
PTFE (Teflon) | Low Dielectric constant, low loss at high frequencies | Higher cost, lower mechanical strength | High-frequency and microwave applications |
Aluminum | Excellent thermal conductivity | Higher cost, requires insulation | High-power and LED applications |
The choice of PCB material depends on factors such as the application requirements, operating environment, budget, and desired performance characteristics.
Frequently Asked Questions (FAQ)
- What does FR4 stand for in FR4 PCB?
-
FR4 stands for “Flame Retardant 4,” indicating the material’s flame-retardant properties.
-
What is the difference between FR4 and other PCB materials?
-
FR4 offers a balanced combination of mechanical strength, electrical insulation, flame retardancy, and cost-effectiveness. Other materials, such as polyimide or PTFE, may offer specific advantages like high-temperature resistance or low dielectric constant but at a higher cost.
-
Can FR4 PCBs be used for high-frequency applications?
-
While FR4 is suitable for many general-purpose applications, it may not be the best choice for high-frequency applications due to its higher dielectric loss. Materials like PTFE or Rogers laminates are better suited for high-frequency and microwave applications.
-
What is the typical thickness of an FR4 PCB?
-
FR4 PCBs are available in various thicknesses, typically ranging from 0.4 mm to 3.2 mm. The most common thicknesses are 0.8 mm, 1.6 mm, and 2.4 mm.
-
How do I choose the right FR4 PCB thickness for my application?
- The choice of PCB thickness depends on factors such as the number of layers required, component sizes, mechanical strength needed, and the application’s space constraints. Thicker boards offer better mechanical stability but may be more challenging to route and assemble. Consulting with a PCB manufacturer or an experienced design engineer can help determine the optimal thickness for your specific application.
Conclusion
FR4 PCB is the most widely used material for printed circuit board fabrication due to its excellent mechanical, electrical, and thermal properties. Its combination of fiberglass reinforcement and epoxy resin offers a cost-effective solution for a wide range of electronic applications, from consumer devices to industrial and aerospace systems.
Understanding the composition, properties, and fabrication process of FR4 PCBs is essential for designers and engineers to create reliable and high-performance electronic products. By adhering to industry standards and carefully selecting the appropriate specifications, manufacturers can ensure the quality and consistency of their FR4 PCBs.
As technology continues to advance, FR4 PCBs will likely remain a crucial component in the electronics industry, providing a foundation for innovative and dependable electronic devices.
No responses yet