Key Components of FR4
FR4 is a composite material that consists of two main components:
- Epoxy resin
- Glass fiber reinforcement
The combination of these materials creates a laminate that offers superior strength, durability, and electrical insulation properties.
Epoxy Resin
Epoxy resin is a thermosetting polymer that forms the matrix of the FR4 material. It is made by reacting epichlorohydrin with bisphenol A (BPA) or other similar compounds. The resulting polymer has excellent adhesive properties, chemical resistance, and dimensional stability.
The epoxy resin used in FR4 is typically a brominated or phosphorus-containing flame retardant version, which enhances the material’s ability to withstand high temperatures and prevent the spread of flames in case of a fire.
Advantages of Epoxy Resin in FR4
- High mechanical strength
- Excellent electrical insulation
- Good chemical resistance
- Low moisture absorption
- Dimensional stability
Glass Fiber Reinforcement
Glass fiber reinforcement is the second key component of FR4. It is made from fine strands of glass that are woven into a fabric or mat. The glass fibers provide the necessary strength and stiffness to the composite material, while the epoxy resin binds them together and transfers the loads between the fibers.
The most common type of glass fiber used in FR4 is E-glass, which is an alumino-borosilicate glass with low electrical conductivity and high mechanical strength. Other types of glass fibers, such as S-glass or NE-glass, may also be used for specialized applications that require higher strength or better electrical properties.
Advantages of Glass Fiber Reinforcement in FR4
- High tensile strength
- Low coefficient of thermal expansion
- Good dimensional stability
- Excellent electrical insulation
- Lightweight
Manufacturing Process of FR4
The manufacturing process of FR4 involves several steps that ensure the proper mixing and bonding of the epoxy resin and glass fiber reinforcement. The basic steps are as follows:
-
Glass fabric impregnation: The glass fiber fabric is impregnated with the epoxy resin solution, ensuring that the resin thoroughly penetrates the fibers.
-
Drying: The impregnated fabric is then dried to remove any excess solvent and partially cure the resin.
-
Cutting and layup: The dried fabric is cut to the desired size and shape, and multiple layers are stacked together to achieve the required thickness.
-
Pressing: The stacked layers are placed in a heated press, where high pressure and temperature are applied to fully cure the resin and bond the layers together.
-
Cooling: The laminated FR4 board is then cooled to room temperature.
-
Finishing: The cooled board undergoes final finishing processes, such as cutting, drilling, and copper cladding, depending on the specific requirements of the application.
Properties of FR4
FR4 exhibits a combination of properties that make it suitable for a wide range of electronic applications. Some of the key properties of FR4 include:
Mechanical Properties
Property | Value |
---|---|
Density | 1.85 g/cm³ |
Tensile Strength | 310 MPa |
Flexural Strength | 415 MPa |
Compressive Strength | 415 MPa |
Izod Impact Strength | 53 J/m |
Rockwell Hardness (M Scale) | 110 |
FR4 has high mechanical strength, which allows it to withstand the stresses and strains encountered during the manufacturing process and in the final application. Its good impact resistance and hardness protect the PCB from damage due to handling or environmental factors.
Electrical Properties
Property | Value |
---|---|
Dielectric Constant (at 1 MHz) | 4.7 |
Dielectric Loss Tangent (at 1 MHz) | 0.02 |
Dielectric Strength | 20 kV/mm |
Volume Resistivity | 10¹⁴ Ω·cm |
Surface Resistivity | 10¹³ Ω |
FR4 has excellent electrical insulation properties, with a high dielectric strength and low dielectric loss. This ensures that the electrical signals in the PCB are not distorted or attenuated, and there is minimal cross-talk between adjacent circuits. The high volume and surface resistivity prevent leakage currents and ensure reliable performance.
Thermal Properties
Property | Value |
---|---|
Glass Transition Temperature (Tg) | 130-140°C |
Thermal Conductivity | 0.3 W/m·K |
Coefficient of Thermal Expansion (CTE) | 14-16 ppm/°C |
Flammability Rating (UL 94) | V-0 |
FR4 has a relatively high glass transition temperature, which allows it to maintain its mechanical and electrical properties at elevated temperatures. Its low thermal conductivity helps to insulate the electronic components from heat generated during operation. The low CTE ensures that the material does not expand or contract excessively with changes in temperature, minimizing stress on the components and solder joints.
The flame-retardant properties of FR4 are crucial for the safety of electronic devices. The UL 94 V-0 rating indicates that the material self-extinguishes within 10 seconds of removing the flame source, and does not drip flaming particles that could ignite other materials.
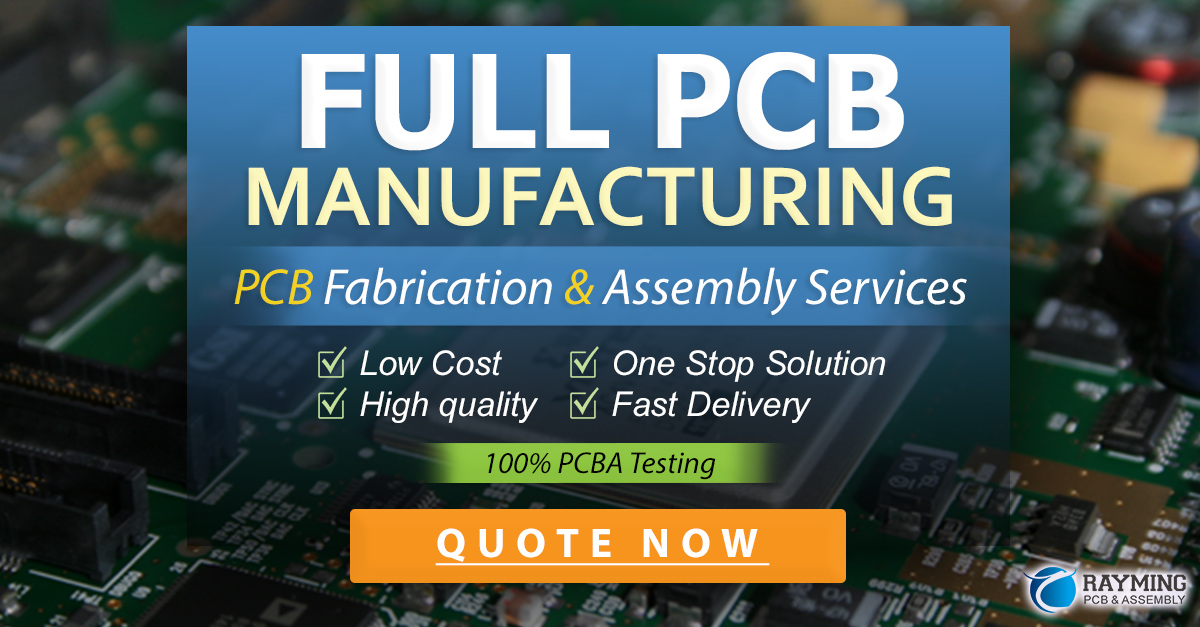
Applications of FR4
FR4 is widely used in various electronic applications, including:
- Consumer electronics (smartphones, laptops, televisions)
- Automotive electronics (engine control units, infotainment systems)
- Industrial electronics (process control systems, power supplies)
- Medical devices (diagnostic equipment, monitoring systems)
- Aerospace and defense electronics (avionics, radar systems)
- Telecommunications (routers, switches, base stations)
The versatility of FR4 and its ability to meet the demanding requirements of these applications make it an indispensable material in the electronics industry.
Variations of FR4
While the basic composition of FR4 remains the same, there are several variations that cater to specific requirements:
High Tg FR4
High Tg FR4 is a variation that uses a modified epoxy resin with a higher glass transition temperature (170-180°C). This makes the material more suitable for applications that require higher operating temperatures or enhanced thermal stability, such as automotive and aerospace electronics.
Halogen-Free FR4
Halogen-free FR4 is a more environmentally friendly version that uses non-halogenated flame retardants instead of the traditional brominated compounds. This helps to reduce the environmental impact of electronic waste and complies with regulations such as RoHS (Restriction of Hazardous Substances).
High-Speed FR4
High-speed FR4 is optimized for high-frequency applications, such as 5G telecommunications and high-speed digital circuits. It has a lower dielectric constant and loss tangent, which minimizes signal distortion and attenuation at higher frequencies.
Low-Loss FR4
Low-loss FR4 is designed for applications that require low signal attenuation, such as high-performance RF and microwave circuits. It achieves this by using a special glass fabric with lower dielectric loss and a modified epoxy resin that reduces the dissipation factor.
Frequently Asked Questions (FAQ)
-
Q: What is the difference between FR4 and G10?
A: FR4 and G10 are similar materials, but FR4 has better flame-retardant properties due to the addition of bromine or phosphorus compounds in the epoxy resin. G10 is a more general-purpose material that may not meet the same flammability ratings as FR4. -
Q: Can FR4 be used for high-temperature applications?
A: Standard FR4 has a glass transition temperature of 130-140°C, which limits its use in high-temperature environments. For applications that require higher thermal stability, high Tg FR4 with a glass transition temperature of 170-180°C can be used. -
Q: Is FR4 suitable for high-frequency applications?
A: Standard FR4 can be used for frequencies up to a few gigahertz, but its performance may degrade at higher frequencies due to its relatively high dielectric constant and loss tangent. For high-frequency applications, high-speed or low-loss FR4 variants with optimized dielectric properties are recommended. -
Q: How does FR4 compare to other PCB materials, such as polyimide or PTFE?
A: FR4 is a cost-effective and versatile material that offers a good balance of mechanical, electrical, and thermal properties. Polyimide and PTFE have better thermal stability and lower dielectric loss, making them suitable for high-temperature and high-frequency applications, but they are also more expensive and harder to process. -
Q: Can FR4 be recycled?
A: FR4 is a thermoset material, which means that it cannot be easily recycled by melting and reshaping like thermoplastics. However, there are some emerging technologies that can reclaim the glass fibers and epoxy resin from waste FR4, allowing them to be repurposed in other applications. Proper disposal and recycling of FR4 waste are important for reducing the environmental impact of electronic manufacturing.
In conclusion, FR4 is a versatile and reliable material that has become the backbone of the electronics industry. Its unique combination of mechanical strength, electrical insulation, thermal stability, and flame retardance makes it an ideal choice for a wide range of applications. As electronic devices continue to evolve and push the boundaries of performance, FR4 and its variants will undoubtedly play a crucial role in enabling the next generation of technology.
No responses yet