Introduction to FR4 composition
FR4 is a widely used material in the electronics industry, particularly in the manufacturing of printed circuit boards (PCBs). It is a composite material that consists of a flame-resistant epoxy resin reinforced with woven fiberglass cloth. The combination of these materials provides FR4 with excellent mechanical, thermal, and electrical properties, making it an ideal substrate for electronic circuits.
In this article, we will delve into the composition of FR4, exploring its key components and their roles in creating a robust and reliable material for electronic applications.
Key Components of FR4
Epoxy Resin
The primary component of FR4 is an epoxy resin system. Epoxy resins are thermosetting polymers known for their strong adhesive properties, chemical resistance, and excellent insulation capabilities. In FR4, the epoxy resin acts as a binder, holding the reinforcing fiberglass cloth together and providing a stable matrix for the composite material.
The most common epoxy resin used in FR4 is a bifunctional epoxy based on diglycidyl ether of bisphenol A (DGEBA). This resin is derived from the reaction between bisphenol A and epichlorohydrin. The resulting epoxy resin exhibits high strength, low shrinkage, and good resistance to heat and chemicals.
Fiberglass Reinforcement
The second key component of FR4 is the reinforcing fiberglass cloth. Fiberglass is a type of composite material made from fine glass fibers woven into a fabric. In FR4, the fiberglass cloth is typically a plain weave, meaning the warp and weft fibers are interlaced in a simple over-under pattern.
The fiberglass reinforcement provides several important properties to the FR4 composite:
-
Mechanical Strength: The fiberglass cloth enhances the tensile strength, flexural strength, and impact resistance of the FR4 laminate. It helps to distribute stress evenly throughout the material, reducing the likelihood of fractures or delamination.
-
Dimensional Stability: The woven structure of the fiberglass cloth minimizes the expansion and contraction of the FR4 laminate when subjected to temperature changes. This dimensional stability is crucial for maintaining the integrity of the copper traces on the PCB.
-
Electrical Insulation: Fiberglass is an excellent electrical insulator, contributing to the overall insulation properties of the FR4 composite. It helps to prevent short circuits and reduces the risk of electrical leakage between conductive layers.
Flame Retardants
To meet the stringent fire safety requirements of the electronics industry, FR4 incorporates flame retardants into its composition. These additives help to inhibit the ignition and spread of flames, reducing the risk of fire hazards in electronic devices.
The most common flame retardants used in FR4 are halogenated compounds, such as brominated or chlorinated substances. These compounds release halogen radicals when exposed to high temperatures, which interfere with the combustion process and help to extinguish the flames.
However, due to environmental and health concerns associated with halogenated flame retardants, there is a growing trend towards the use of halogen-free alternatives. These alternatives include phosphorus-based compounds, metal hydroxides, and nitrogen-based additives, which provide effective flame retardancy without the potential harmful effects of halogens.
Manufacturing Process of FR4
The manufacturing process of FR4 involves the following key steps:
-
Impregnation: The fiberglass cloth is impregnated with the epoxy resin system, ensuring thorough penetration and even distribution of the resin throughout the fabric.
-
Layup: Multiple layers of the impregnated fiberglass cloth are stacked together to achieve the desired thickness of the FR4 laminate. The number of layers and their orientation can be adjusted to optimize the mechanical and electrical properties of the final product.
-
Pressing: The stacked layers are placed in a heated press, where high pressure and temperature are applied. This process allows the epoxy resin to flow and cure, bonding the fiberglass layers together into a solid laminate.
-
Curing: The pressed laminate undergoes a controlled curing cycle, typically involving a gradual increase in temperature followed by a cooling phase. During this process, the epoxy resin undergoes cross-linking, forming a strong and stable polymer network.
-
Finishing: After curing, the FR4 laminate is trimmed to the desired size and shape. The surface may be sanded or polished to achieve a smooth finish, and copper foil can be laminated onto one or both sides of the laminate for the subsequent fabrication of PCBs.
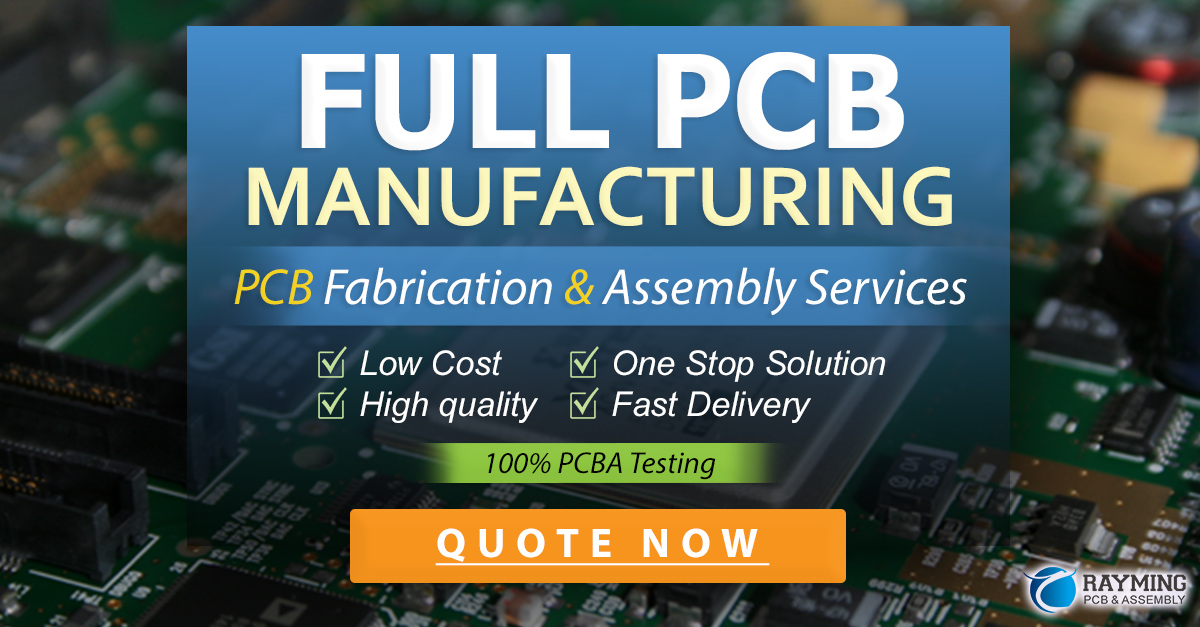
Properties of FR4
The unique composition of FR4 gives rise to a range of desirable properties that make it suitable for electronic applications:
Mechanical Properties
- High tensile strength
- Excellent flexural strength
- Good impact resistance
- Dimensional stability over a wide temperature range
Thermal Properties
- Glass transition temperature (Tg) around 130-180°C
- Thermal expansion coefficient (CTE) closely matched to copper
- Good thermal conductivity for heat dissipation
Electrical Properties
- High dielectric strength
- Low dielectric constant and dissipation factor
- Excellent insulation resistance
- Good high-frequency performance
Chemical Properties
- Resistance to a wide range of chemicals and solvents
- Low moisture absorption
- Compatibility with various PCB fabrication processes
Applications of FR4
FR4 finds extensive use in the electronics industry, particularly in the manufacturing of PCBs. Some common applications include:
- Consumer electronics (smartphones, laptops, televisions)
- Automotive electronics (engine control units, infotainment systems)
- Industrial control systems
- Telecommunications equipment
- Medical devices
- Aerospace and defense electronics
The versatility and reliability of FR4 have made it a go-to material for a wide range of electronic products, from small-scale consumer gadgets to large-scale industrial systems.
FR4 Variants and Alternatives
While standard FR4 is the most widely used laminate in the electronics industry, there are several variants and alternatives available to meet specific requirements:
- High Tg FR4: Features a higher glass transition temperature (Tg) for improved thermal performance and stability.
- Halogen-Free FR4: Utilizes non-halogenated flame retardants to address environmental and health concerns.
- FR4 with Modified Resin Systems: Incorporates modified epoxy resins to enhance specific properties, such as improved thermal conductivity or lower dielectric constant.
- High-Frequency Laminates: Designed for high-frequency applications, these laminates often use alternative reinforcement materials (e.g., ceramic fibers) and specialized resin systems to optimize electrical performance.
- Flexible Laminates: Made from flexible substrates like polyimide or polyester, these laminates are used for flexible PCBs and wearable electronics.
The choice of laminate depends on the specific requirements of the application, such as operating temperature, electrical performance, environmental conditions, and cost considerations.
Future Trends in FR4 Composition
As the electronics industry continues to evolve, there is a constant drive for improved materials and technologies. Some future trends in FR4 composition include:
- Eco-Friendly Flame Retardants: With increasing environmental awareness, there is a push towards the development and adoption of more sustainable and non-toxic flame retardants.
- Nanomaterial Reinforcements: The incorporation of nanomaterials, such as carbon nanotubes or graphene, into the FR4 composite could potentially enhance its mechanical, thermal, and electrical properties.
- Bio-Based Resins: Research is being conducted on the use of bio-based epoxy resins derived from renewable resources, aiming to reduce the environmental impact of FR4 production.
- Multifunctional Additives: The development of multifunctional additives that can simultaneously improve multiple properties, such as flame retardancy, thermal conductivity, and dielectric performance, is an area of active research.
As these advancements in FR4 composition materialize, we can expect to see even better-performing and more sustainable materials for electronic applications in the future.
Frequently Asked Questions (FAQ)
-
What does FR4 stand for?
FR4 stands for “Flame Retardant 4,” indicating that it is a flame-resistant material suitable for use in electronic applications. -
Is FR4 a type of fiberglass?
FR4 is a composite material that consists of fiberglass reinforcement impregnated with an epoxy resin system. While fiberglass is a key component of FR4, the term “FR4” refers to the complete composite material, not just the fiberglass. -
Can FR4 withstand high temperatures?
Standard FR4 has a glass transition temperature (Tg) around 130-180°C, which is the temperature range where the material starts to soften and lose its mechanical properties. For higher temperature applications, high Tg FR4 variants are available. -
Is FR4 environmentally friendly?
Traditional FR4 laminates contain halogenated flame retardants, which have raised environmental and health concerns. However, there is a growing trend towards the use of halogen-free and eco-friendly alternatives in FR4 composition. -
Can FR4 be used for flexible PCBs?
Standard FR4 is a rigid material and is not suitable for flexible PCBs. For flexible applications, specialized flexible laminates, such as those based on polyimide or polyester, are used instead.
Conclusion
FR4 is a versatile and reliable composite material that has become an essential component in the electronics industry. Its composition, which includes an epoxy resin system reinforced with fiberglass cloth and flame retardants, provides a unique combination of mechanical, thermal, and electrical properties that make it ideal for PCB manufacturing.
As the demand for high-performance electronic devices continues to grow, the development of advanced FR4 compositions and alternatives remains an active area of research. By understanding the key components and properties of FR4, engineers and designers can make informed decisions when selecting materials for their electronic products.
With ongoing advancements in eco-friendly flame retardants, nanomaterial reinforcements, and bio-based resins, we can expect to see even more innovative and sustainable FR4 compositions in the future, contributing to the ever-evolving landscape of the electronics industry.
Component | Role in FR4 Composition |
---|---|
Epoxy Resin | Binder, provides strength and insulation |
Fiberglass Cloth | Reinforcement, enhances mechanical and thermal properties |
Flame Retardants | Imparts flame resistance, ensures fire safety |
Table: Key components of FR4 and their roles in the composite material.
No responses yet