Fiberglass Cloth Substrate
The foundation of FR4 is a fiberglass cloth substrate. Fiberglass is made from fine strands of glass that are woven together to form a fabric. The most commonly used type of fiberglass in FR4 is E-glass, which is known for its excellent electrical insulation properties and mechanical strength.
The fiberglass cloth used in FR4 typically has a plain weave pattern, meaning that the warp and weft fibers are interlaced in a simple crisscross pattern. This weave pattern provides a balance between mechanical strength and ease of impregnation with the epoxy resin.
The thickness of the fiberglass cloth can vary depending on the specific application and the desired properties of the final FR4 laminate. Common thicknesses range from 0.002 inches to 0.007 inches (0.05mm to 0.18mm).
Advantages of Fiberglass Cloth in FR4
- High mechanical strength
- Excellent electrical insulation properties
- Good dimensional stability
- Resistance to heat and moisture
Epoxy Resin Binder
The fiberglass cloth substrate is impregnated with an epoxy resin binder to create the FR4 laminate. Epoxy resin is a thermosetting polymer that undergoes a curing process when exposed to heat, forming a solid and durable material.
The epoxy resin used in FR4 is typically a bifunctional epoxy, meaning that it has two reactive sites per molecule. This allows for cross-linking between the epoxy molecules during the curing process, resulting in a strong and rigid material.
In addition to the base epoxy resin, various additives and modifiers are incorporated into the resin system to enhance its properties. These additives can include:
- Flame retardants: Added to improve the fire resistance of FR4
- Fillers: Used to modify the mechanical and thermal properties of the laminate
- Curing agents: Facilitate the cross-linking of the epoxy molecules during the curing process
- Accelerators: Speed up the curing reaction
- Colorants: Provide color to the FR4 laminate
Advantages of Epoxy Resin in FR4
- High mechanical strength and stiffness
- Excellent adhesion to the fiberglass substrate
- Good chemical resistance
- Low moisture absorption
- Flame retardant properties
Manufacturing Process
The manufacturing process of FR4 involves several steps to create the final laminate:
-
Impregnation: The fiberglass cloth is impregnated with the epoxy resin system using a process called dip-coating or roller-coating. This ensures that the resin is evenly distributed throughout the fiberglass substrate.
-
Drying: The impregnated fiberglass cloth is then dried to remove any excess solvent and to partially cure the epoxy resin. This step is known as B-staging.
-
Layup: Multiple sheets of B-staged fiberglass cloth are stacked together to achieve the desired thickness of the final laminate.
-
Pressing: The stacked layers are placed in a heated press, where they are subjected to high temperature and pressure. This causes the epoxy resin to fully cure and bond the fiberglass layers together.
-
Cooling: After pressing, the laminate is cooled to room temperature.
-
Cutting and Finishing: The cooled laminate is then cut to the desired size and shape, and any necessary finishing operations, such as drilling or milling, are performed.
Laminate Thickness and Copper Cladding
FR4 laminates are available in various thicknesses to accommodate different PCB design requirements. The thickness is typically expressed in terms of the number of fiberglass layers and the thickness of each layer. For example, a 1.6mm thick FR4 laminate may consist of eight layers of 7628 fiberglass cloth, each with a thickness of 0.2mm.
In most applications, FR4 laminates are clad with copper foil on one or both sides to create the conductive layers of the PCB. The copper foil is bonded to the FR4 substrate during the pressing stage of the manufacturing process. The thickness of the copper foil can vary depending on the intended use of the PCB, with common thicknesses ranging from 0.5 oz/ft² to 2 oz/ft² (17µm to 68µm).
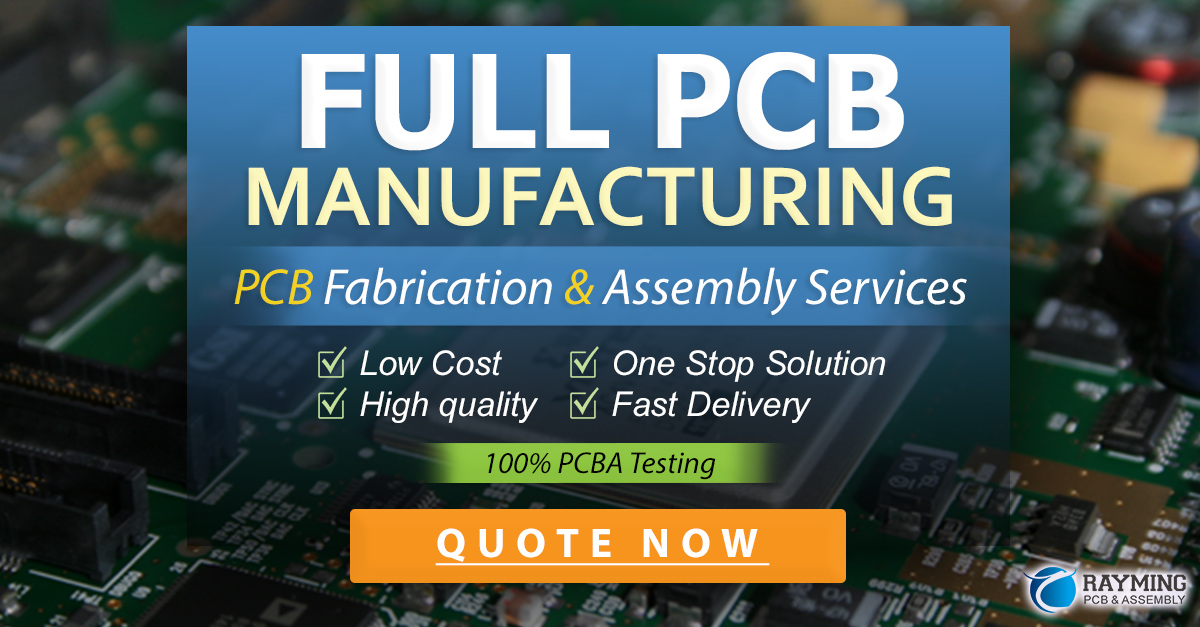
Properties of FR4
The composition of FR4 gives it a unique combination of properties that make it suitable for a wide range of electronic applications. Some of the key properties of FR4 include:
- Electrical Properties:
- High dielectric strength
- Low dielectric constant
- Low dissipation factor
-
Good insulation resistance
-
Mechanical Properties:
- High flexural strength
- Good impact resistance
- Excellent dimensional stability
-
Low water absorption
-
Thermal Properties:
- Glass transition temperature (Tg) around 130°C to 140°C
- Thermal expansion coefficient (CTE) closely matched to that of copper
-
Good thermal conductivity
-
Flame Retardant Properties:
- Meets UL 94 V-0 flammability rating
- Self-extinguishing
- Low smoke generation
These properties make FR4 an excellent choice for PCBs used in various industries, including:
- Consumer electronics
- Telecommunications
- Automotive electronics
- Industrial control systems
- Medical devices
- Aerospace and defense applications
Comparison with Other PCB Materials
While FR4 is the most widely used PCB material, there are other materials available that offer different properties and advantages. Some common alternatives to FR4 include:
-
High Tg FR4: A variant of FR4 with a higher glass transition temperature (Tg) around 170°C to 180°C, offering better thermal stability and performance in high-temperature applications.
-
Polyimide: A high-performance polymer with excellent thermal stability, chemical resistance, and mechanical strength. Polyimide is often used in applications that require operation at elevated temperatures or exposure to harsh environments.
-
PTFE (Teflon): A fluoropolymer known for its low dielectric constant, low dissipation factor, and excellent high-frequency performance. PTFE is commonly used in high-speed, high-frequency applications such as radar and microwave systems.
-
Ceramic: Ceramic substrates, such as alumina (Al₂O₃) and aluminum nitride (AlN), offer excellent thermal conductivity, high dielectric strength, and low dielectric loss. They are often used in high-power and high-frequency applications.
Each material has its own advantages and disadvantages, and the choice of PCB material depends on the specific requirements of the application, such as operating temperature, frequency, mechanical stress, and environmental conditions.
FAQ
- What does FR4 stand for?
-
FR4 stands for Flame Retardant 4, indicating that it is a flame-resistant material that meets the UL 94 V-0 flammability rating.
-
Is FR4 a good insulator?
-
Yes, FR4 is an excellent electrical insulator. Its high dielectric strength and low dielectric constant make it suitable for use in PCBs and other electronic applications.
-
What is the difference between FR4 and G10?
-
FR4 and G10 are similar materials, but FR4 is specifically designed for electronic applications and has better flame-retardant properties. G10 is a more general-purpose grade of fiberglass-epoxy laminate.
-
Can FR4 be used in high-temperature applications?
-
Standard FR4 has a glass transition temperature (Tg) around 130°C to 140°C, which limits its use in high-temperature applications. However, high Tg FR4 variants with a Tg around 170°C to 180°C are available for use in more demanding thermal environments.
-
Is FR4 environmentally friendly?
- FR4 is not biodegradable and contains flame retardants, which can be harmful to the environment if not disposed of properly. However, efforts are being made to develop more eco-friendly PCB materials and to improve the recycling processes for electronic waste containing FR4.
Conclusion
FR4 is a composite material consisting of a fiberglass cloth substrate impregnated with an epoxy resin binder. The combination of these two components gives FR4 its unique properties, making it an ideal choice for a wide range of electronic applications, particularly in the manufacturing of PCBs.
The fiberglass cloth provides mechanical strength, dimensional stability, and electrical insulation, while the epoxy resin offers high adhesion, chemical resistance, and flame retardant properties. The manufacturing process of FR4 involves impregnating the fiberglass cloth with the epoxy resin, followed by drying, layup, pressing, and finishing operations.
FR4 offers a balance of electrical, mechanical, thermal, and flame-retardant properties, making it suitable for use in various industries, including consumer electronics, telecommunications, automotive, industrial control, medical devices, and aerospace applications.
While FR4 is the most widely used PCB material, other materials such as high Tg FR4, polyimide, PTFE, and ceramic substrates are available for applications with specific requirements, such as high-temperature operation, high-frequency performance, or exposure to harsh environments.
Understanding the composition and properties of FR4 is crucial for designers and manufacturers in the electronics industry to make informed decisions when selecting materials for their products. As technology advances and new applications emerge, the development of new PCB materials and the optimization of existing ones, like FR4, will continue to play a vital role in the evolution of electronic devices.
No responses yet