What is FR2?
FR2, also known as phenolic paper or phenolic cotton paper, is a composite material made from paper or cotton fabric that is impregnated with a phenolic resin. The resin provides the material with its flame-retardant properties and enhances its mechanical strength and electrical insulation capabilities.
Composition of FR2
The main components of FR2 are:
- Paper or cotton fabric: This serves as the base material and provides the laminate with its structure and flexibility.
- Phenolic resin: The resin is a synthetic polymer that is derived from the reaction between phenol and formaldehyde. It is used to impregnate the paper or cotton fabric, giving the laminate its flame-retardant properties and mechanical strength.
Properties of FR2
FR2 has several key properties that make it suitable for use in PCB manufacturing:
- Flame retardancy: The phenolic resin used in FR2 provides excellent flame-retardant properties, making it resistant to ignition and the spread of flames.
- Electrical insulation: FR2 has good electrical insulation properties, which helps to prevent short circuits and other electrical issues in PCBs.
- Mechanical strength: The phenolic resin imparts mechanical strength to the laminate, making it resistant to bending, twisting, and other forms of mechanical stress.
- Moisture resistance: FR2 has moderate moisture resistance, which helps to protect the PCB from damage caused by humidity and other environmental factors.
- Low cost: Compared to other PCB substrate materials, such as FR4, FR2 is relatively inexpensive, making it a cost-effective choice for certain applications.
Applications of FR2 in PCB Manufacturing
FR2 is commonly used in the production of low-cost, single-sided PCBs for various applications, including:
- Consumer electronics: FR2 is often used in the production of PCBs for consumer electronic devices, such as calculators, toys, and small appliances.
- Automotive electronics: Some automotive electronic components, such as simple control modules and sensors, may use FR2-based PCBs.
- Telecommunications: FR2 can be used in the production of PCBs for certain telecommunications equipment, such as telephone systems and low-end routers.
- Industrial electronics: Simple industrial electronic devices, such as control panels and sensors, may utilize FR2-based PCBs.
Advantages of using FR2 in PCB manufacturing
Using FR2 as a substrate material in PCB manufacturing offers several advantages:
- Cost-effectiveness: FR2 is less expensive than other PCB substrate materials, such as FR4, making it a cost-effective choice for low-cost, single-sided PCBs.
- Ease of fabrication: FR2 is relatively easy to work with during the PCB manufacturing process, as it can be easily drilled, cut, and machined.
- Adequate performance: For simple, low-density PCB designs, FR2 provides adequate electrical and mechanical performance, making it suitable for a wide range of applications.
- Flame retardancy: The inherent flame-retardant properties of FR2 help to ensure the safety of the end product and comply with various safety standards.
Limitations of FR2 in PCB manufacturing
Despite its advantages, FR2 also has some limitations that should be considered when selecting a substrate material for PCB manufacturing:
- Limited layer count: FR2 is primarily used for single-sided PCBs and is not suitable for multi-layer designs due to its lower mechanical strength and thermal stability compared to other materials like FR4.
- Lower thermal stability: FR2 has a lower glass transition temperature (Tg) than FR4, which means it is more susceptible to deformation and damage at higher temperatures.
- Higher moisture absorption: Compared to FR4, FR2 has a higher moisture absorption rate, which can lead to reduced electrical insulation properties and increased warpage in humid environments.
- Lower dimensional stability: FR2 is more prone to dimensional changes due to temperature fluctuations and moisture absorption, which can affect the accuracy and reliability of the PCB.
Manufacturing Process of FR2 PCBs
The manufacturing process for FR2 PCBs is similar to that of other types of PCBs, with a few key differences:
- Laminate preparation: The FR2 laminate is cut to the desired size and shape, and any necessary holes are drilled.
- Copper foil application: A thin layer of copper foil is laminated to one side of the FR2 substrate using heat and pressure.
- Circuit pattern creation: The desired circuit pattern is transferred to the copper foil using a photoresist and etching process.
- Solder mask application: A solder mask is applied to the PCB to protect the copper traces and prevent short circuits.
- Silkscreen printing: Any necessary text, logos, or component designators are printed onto the PCB using a silkscreen process.
- Surface finish application: A surface finish, such as HASL (Hot Air Solder Leveling) or ENIG (Electroless Nickel Immersion Gold), is applied to the exposed copper to improve solderability and protect against oxidation.
- Cutting and finishing: The PCB is cut to its final shape and size, and any necessary finishing processes, such as beveling or routing, are performed.
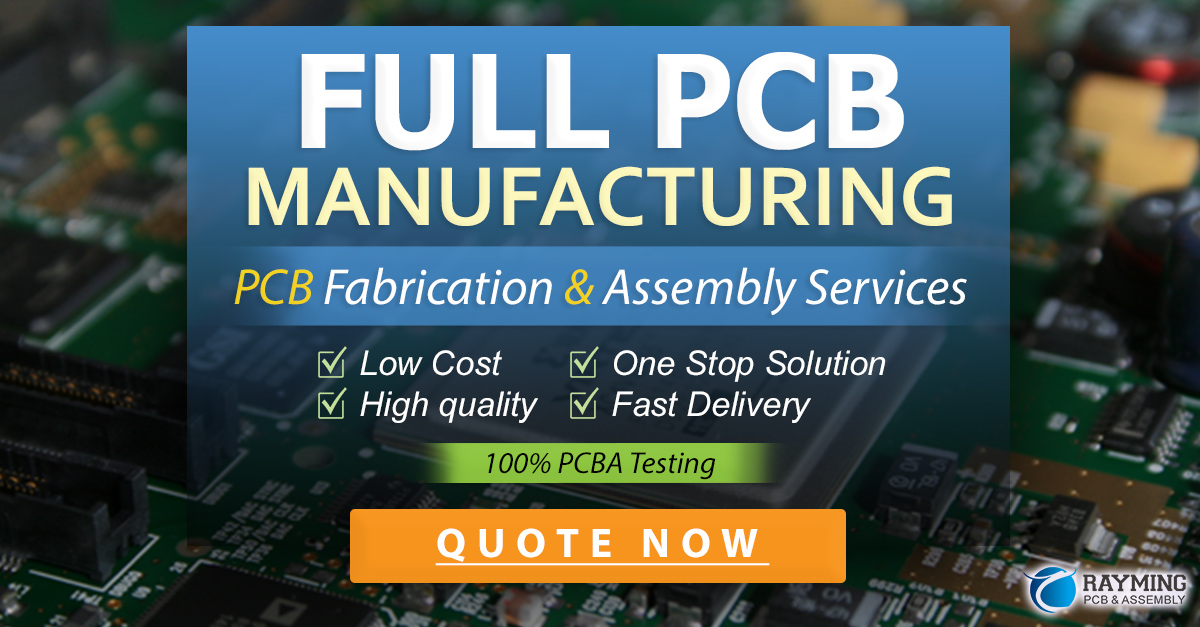
Comparison of FR2 with Other PCB Substrate Materials
There are several other substrate materials used in PCB manufacturing, each with its own unique properties and advantages. Here, we will compare FR2 with two common alternatives: FR4 and CEM-1.
FR2 vs. FR4
FR4 is a glass-reinforced epoxy laminate that is widely used in the production of high-quality, multi-layer PCBs. Compared to FR2, FR4 offers several advantages:
- Higher mechanical strength and stability
- Better thermal stability and higher glass transition temperature (Tg)
- Lower moisture absorption and higher dimensional stability
- Suitable for multi-layer PCB designs
However, FR4 is more expensive than FR2 and may not be necessary for simple, low-cost, single-sided PCB applications.
FR2 vs. CEM-1
CEM-1 (Composite Epoxy Material) is another paper-based PCB substrate material that is similar to FR2. The main difference between the two is that CEM-1 uses an epoxy resin instead of a phenolic resin. Compared to FR2, CEM-1 offers:
- Slightly better mechanical and thermal properties
- Improved moisture resistance
- Better dimensional stability
However, CEM-1 is typically more expensive than FR2 and may not provide significant advantages for low-cost, single-sided PCB applications.
Property | FR2 | FR4 | CEM-1 |
---|---|---|---|
Base material | Paper | Glass | Paper |
Resin type | Phenolic | Epoxy | Epoxy |
Flame retardancy | Good | Excellent | Good |
Mechanical strength | Low | High | Medium |
Thermal stability | Low | High | Medium |
Moisture resistance | Medium | High | High |
Dimensional stability | Low | High | Medium |
Cost | Low | High | Medium |
FAQ
-
Q: What does FR stand for in FR2?
A: FR stands for “Flame Retardant,” indicating that the material has been treated to resist ignition and the spread of flames. -
Q: Can FR2 be used for multi-layer PCBs?
A: No, FR2 is primarily used for single-sided PCBs due to its lower mechanical strength and thermal stability compared to materials like FR4. -
Q: Is FR2 suitable for high-temperature applications?
A: No, FR2 has a lower glass transition temperature (Tg) than other materials like FR4, making it more susceptible to deformation and damage at higher temperatures. -
Q: What are the main advantages of using FR2 in PCB manufacturing?
A: The main advantages of using FR2 are its low cost, ease of fabrication, adequate performance for simple PCB designs, and inherent flame-retardant properties. -
Q: How does FR2 compare to other paper-based PCB substrate materials, such as CEM-1?
A: FR2 and CEM-1 are similar, but CEM-1 uses an epoxy resin instead of a phenolic resin, resulting in slightly better mechanical, thermal, and moisture resistance properties. However, CEM-1 is typically more expensive than FR2.
Conclusion
FR2 is a cost-effective, flame-retardant, paper-based substrate material commonly used in the production of low-cost, single-sided PCBs. While it has limitations compared to other materials like FR4, FR2 offers adequate performance and ease of fabrication for simple PCB designs in various applications, such as consumer electronics, automotive electronics, telecommunications, and industrial electronics.
When selecting a substrate material for PCB manufacturing, it is essential to consider the specific requirements of the application, including the necessary mechanical, thermal, and electrical properties, as well as the cost and manufacturing constraints. By understanding the properties, advantages, and limitations of FR2 and other substrate materials, designers and manufacturers can make informed decisions to ensure the optimal performance and reliability of their PCBs.
No responses yet