Why are FR PCBs Important?
FR PCBs play a crucial role in various industries, including:
- Consumer electronics
- Automotive
- Aerospace
- Medical devices
- Industrial equipment
The use of flame retardant materials in PCBs is essential to prevent fire hazards and ensure the safety of users and the surrounding environment. FR PCBs help to minimize the risk of fire spreading in case of electrical faults or overheating, thereby protecting both the device and the user.
Types of FR PCBs
There are several types of FR PCBs available in the market, each with different flame retardant properties and suitable for specific applications. The most common types of FR PCBs include:
FR-1
- Paper-based phenolic resin
- Low cost and low performance
- Suitable for low-end consumer electronics
FR-2
- Paper-based phenolic resin with better mechanical properties than FR-1
- Low cost and moderate performance
- Suitable for consumer electronics and low-end industrial applications
FR-3
- Paper-based epoxy resin
- Better mechanical and electrical properties than FR-1 and FR-2
- Suitable for consumer electronics and general-purpose applications
FR-4
- Glass-reinforced epoxy laminate
- Excellent mechanical, electrical, and thermal properties
- Most widely used FR PCB material
- Suitable for a wide range of applications, including high-end consumer electronics, automotive, aerospace, and industrial equipment
FR-5
- Glass-reinforced epoxy laminate with higher glass transition temperature than FR-4
- Enhanced thermal resistance and dimensional stability
- Suitable for high-temperature applications and lead-free soldering processes
FR-6
- Matte glass-reinforced polyester laminate
- High resistance to moisture and chemicals
- Suitable for outdoor and harsh environment applications
FR-4 PCB: The Most Popular Choice
Among the various types of FR PCBs, FR-4 is the most widely used material due to its excellent properties and versatility. Let’s take a closer look at FR-4 PCBs and their characteristics.
Composition of FR-4 PCBs
FR-4 PCBs are made of a composite material consisting of woven fiberglass cloth impregnated with an epoxy resin binder. The fiberglass reinforcement provides mechanical strength and dimensional stability, while the epoxy resin offers excellent insulation and flame retardant properties.
Properties of FR-4 PCBs
FR-4 PCBs exhibit several desirable properties that make them suitable for a wide range of applications:
-
Mechanical strength: The fiberglass reinforcement in FR-4 PCBs provides high tensile and flexural strength, making them resistant to vibrations and mechanical stress.
-
Electrical insulation: The epoxy resin in FR-4 PCBs offers excellent electrical insulation, preventing short circuits and leakage currents.
-
Flame retardancy: FR-4 PCBs are designed to self-extinguish when exposed to fire, limiting the spread of flames and minimizing fire hazards.
-
Thermal stability: FR-4 PCBs have a glass transition temperature (Tg) of around 130°C to 140°C, providing good thermal stability and resistance to high-temperature environments.
-
Moisture resistance: FR-4 PCBs have low moisture absorption, making them suitable for use in humid environments.
-
Chemical resistance: FR-4 PCBs offer good resistance to various chemicals, including acids, alkalis, and solvents.
Applications of FR-4 PCBs
Due to their excellent properties, FR-4 PCBs find applications in a wide range of industries and products, such as:
- Consumer electronics (smartphones, laptops, televisions)
- Automotive electronics (engine control units, infotainment systems)
- Industrial equipment (power supplies, motor drives, automation systems)
- Medical devices (patient monitors, diagnostic equipment)
- Aerospace and defense (avionics, radar systems, communication equipment)
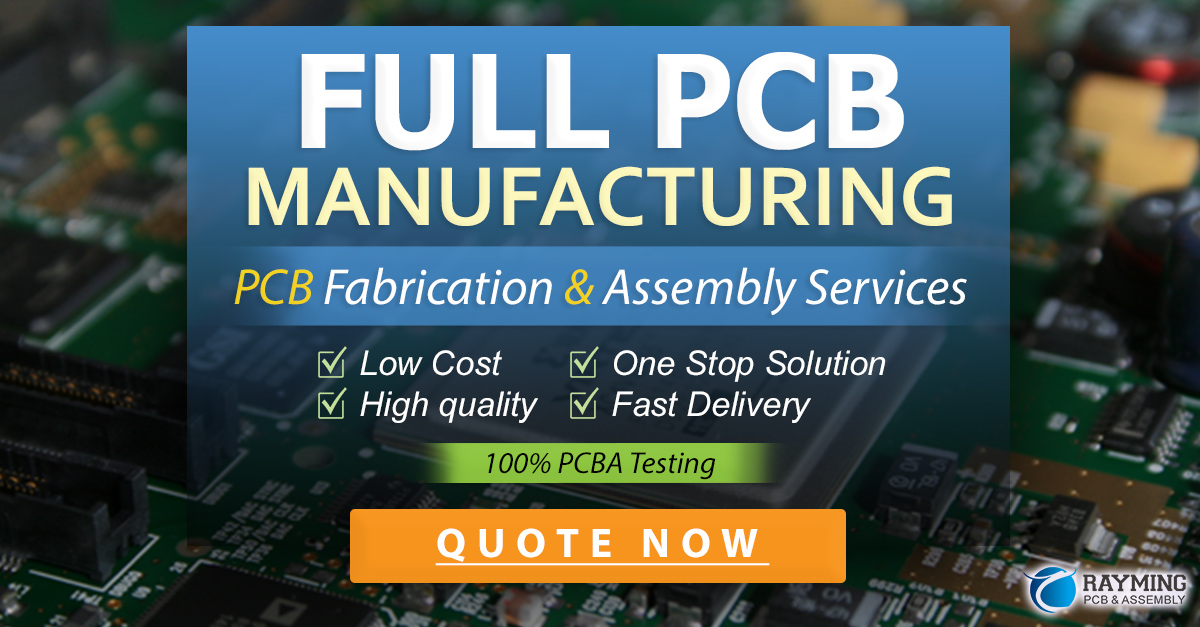
Manufacturing Process of FR PCBs
The manufacturing process of FR PCBs involves several steps to ensure the desired properties and performance. The general steps in the manufacturing process include:
-
Material selection: The appropriate FR material (e.g., FR-4) is selected based on the specific application requirements and desired properties.
-
Cutting and drilling: The FR laminate is cut to the required size, and holes are drilled for component mounting and vias.
-
Copper cladding: A thin layer of copper is laminated onto the FR substrate using heat and pressure.
-
Patterning: The desired circuit pattern is transferred onto the copper layer using photolithography and etching processes.
-
Solder mask application: A protective solder mask layer is applied to the PCB surface, leaving only the exposed pads for component soldering.
-
Surface finish: A surface finish (e.g., HASL, ENIG, or OSP) is applied to the exposed pads to enhance solderability and protect the copper from oxidation.
-
Silkscreen printing: Text, logos, and component identifiers are printed onto the PCB surface using silkscreen printing.
-
Electrical testing: The manufactured PCB undergoes electrical testing to ensure proper functionality and adherence to specifications.
Flame Retardant Additives in FR PCBs
To achieve the desired flame retardant properties, various additives are incorporated into the FR PCB materials during the manufacturing process. The most common flame retardant additives used in FR PCBs include:
Halogenated Flame Retardants
- Brominated flame retardants (BFRs)
- Chlorinated flame retardants (CFRs)
Halogenated flame retardants work by releasing halogen radicals during combustion, which inhibit the flame propagation. However, concerns over the environmental and health impacts of halogenated flame retardants have led to a shift towards halogen-free alternatives.
Halogen-Free Flame Retardants
- Phosphorus-based flame retardants
- Nitrogen-based flame retardants
- Inorganic flame retardants (e.g., aluminum hydroxide, magnesium hydroxide)
Halogen-free flame retardants work through various mechanisms, such as promoting char formation, releasing non-combustible gases, or absorbing heat to reduce the temperature of the material.
Flame Retardancy Standards for FR PCBs
To ensure the safety and reliability of FR PCBs, various flame retardancy standards have been established by international organizations. The most widely recognized standards for FR PCBs include:
UL 94
UL 94 is a flammability testing standard developed by Underwriters Laboratories (UL). It classifies materials into different flammability ratings based on their performance in vertical and horizontal burning tests. The most common UL 94 ratings for FR PCBs are:
UL 94 Rating | Description |
---|---|
V-0 | Self-extinguishing within 10 seconds, no flaming drips |
V-1 | Self-extinguishing within 30 seconds, no flaming drips |
V-2 | Self-extinguishing within 30 seconds, flaming drips allowed |
HB | Slow burning rate, no flame spread |
IEC 60695-11-10
IEC 60695-11-10 is a flame retardancy testing standard developed by the International Electrotechnical Commission (IEC). It assesses the fire hazard of electrotechnical products under end-use conditions. The standard includes tests such as the needle flame test and the vertical burning test.
IPC-4101
IPC-4101 is a specification for base materials for rigid and multilayer printed boards, developed by the Institute for Printed Circuits (IPC). It defines the requirements for FR PCB materials, including their flammability performance and other properties.
Designing with FR PCBs
When designing electronic products with FR PCBs, several factors should be considered to ensure optimal performance and safety:
-
Material selection: Choose the appropriate FR PCB material based on the specific application requirements, such as temperature range, mechanical stress, and environmental conditions.
-
Layout and routing: Design the PCB layout and routing to minimize the risk of overheating and electrical faults. Consider factors such as power dissipation, current density, and spacing between components.
-
Component selection: Select components that are compatible with the FR PCB material and meet the required flame retardancy standards.
-
Manufacturing process: Work closely with the PCB manufacturer to ensure that the desired flame retardant properties are achieved through the appropriate manufacturing processes and quality control measures.
-
Compliance with standards: Ensure that the designed FR PCB meets the relevant flame retardancy standards (e.g., UL 94, IEC 60695-11-10) and other applicable industry standards.
FAQ
1. What is the difference between FR-4 and regular PCBs?
FR-4 PCBs are made of a flame retardant material that self-extinguishes when exposed to fire, while regular PCBs do not have enhanced flame retardant properties. FR-4 PCBs offer better safety and reliability in applications where fire hazards are a concern.
2. Can FR PCBs be used for high-frequency applications?
Yes, FR-4 PCBs can be used for high-frequency applications up to a few gigahertz. However, for very high-frequency applications (e.g., above 10 GHz), specialized PCB materials with lower dielectric loss, such as Rogers or PTFE laminates, may be more suitable.
3. Are halogen-free FR PCBs as effective as halogenated ones?
Halogen-free FR PCBs can provide similar flame retardant properties as halogenated ones, while offering better environmental and health safety. Many halogen-free flame retardants, such as phosphorus and nitrogen-based additives, have been developed to meet the required flame retardancy standards.
4. How do I choose the right FR PCB material for my application?
When selecting an FR PCB material, consider factors such as the operating temperature range, mechanical requirements, electrical properties, and environmental conditions. Consult with PCB manufacturers or material suppliers to determine the most suitable FR PCB material for your specific application.
5. Can FR PCBs be recycled?
Yes, FR PCBs can be recycled through proper electronic waste management processes. However, the presence of flame retardant additives may require special handling and treatment during the recycling process to prevent environmental contamination and ensure safe disposal of the materials.
Conclusion
FR PCBs are essential components in ensuring the safety and reliability of electronic devices and equipment. By incorporating flame retardant materials and additives, FR PCBs minimize the risk of fire hazards and protect both the device and the user.
Among the various types of FR PCBs, FR-4 is the most widely used material due to its excellent mechanical, electrical, and thermal properties. FR-4 PCBs find applications in a wide range of industries, including consumer electronics, automotive, aerospace, and industrial equipment.
When designing with FR PCBs, it is crucial to consider factors such as material selection, layout and routing, component compatibility, manufacturing process, and compliance with relevant flame retardancy standards.
As the electronics industry continues to evolve, the development of new flame retardant materials and technologies will further enhance the safety and performance of FR PCBs, enabling the creation of more reliable and sustainable electronic products.
No responses yet