Overview of Flexible PCBs
Flexible printed circuit boards, also known as flex circuits or flexible PCBs, are a type of printed circuit board that uses flexible plastic substrates like polyimide films instead of rigid substrates like FR4 fiberglass. This allows the PCB to bend, twist, and conform to different shapes. Flexible PCBs enable the design of compact, lightweight electronic devices and wearable technology.
Flexible circuits were first developed in the 1950s for aerospace applications and have steadily grown in popularity for consumer electronics and other industries. The global flexible printed circuit board market size was valued at USD 15.2 billion in 2020 and is expected to expand at a compound annual growth rate (CAGR) of 11.9% from 2021 to 2028.
Advantages of Flexible PCBs
Flexible PCBs offer several advantages over traditional rigid PCBs:
-
Flexibility and durability: The flexible substrates can bend and twist without breaking, making them more durable than rigid boards. They can withstand vibration, shock, and extreme temperatures.
-
Lightweight and thin: Flex circuits are much thinner and lighter than rigid PCBs. This allows the design of more compact devices and reduces overall product weight.
-
Space savings: Flexible PCBs can be bent to fit into tight spaces and conform to the shape of product housings. This enables higher component density and more efficient use of space.
-
Simplified assembly: Flex circuits can integrate wiring, connectors, and components into a single unit, simplifying assembly and reducing the need for wires and connectors.
-
High-speed applications: The thin dielectric layers and fine trace geometries of flex circuits are well-suited for high-speed signaling. The shorter signal paths reduce noise and interference.
Applications of Flexible PCBs
Flexible PCBs are used across many industries and applications, including:
- Consumer electronics: Smartphones, tablets, laptops, wearables, digital cameras, etc.
- Medical devices: Hearing aids, pacemakers, defibrillators, drug delivery systems, patient monitoring, etc.
- Automotive: Dashboard displays, sensors, engine control units, lighting, etc.
- Aerospace and military: Avionics, satellite systems, missiles, radar, etc.
- Industrial equipment: Robotics, automation systems, inspection devices, etc.
Some well-known products that utilize flex circuits include:
- Apple iPhone and iPad
- Fitbit and Apple Watch
- Cochlear implants
- Missile guidance systems
- Mars Curiosity Rover
Types of Flexible PCBs
There are several different types of flexible PCBs with varying constructions and capabilities:
Single-sided Flex Circuits
Single-sided flex circuits have conductive copper traces on one side of a flexible dielectric substrate. They are the simplest and most economical type of flex circuit.
Double-sided Flex Circuits
Double-sided flex circuits have conductive copper traces on both sides of the dielectric substrate. Through-hole vias or microvias are used to interconnect the top and bottom layers. Double-sided flex offers higher wiring density than single-sided.
Multi-layer Flex Circuits
Multi-layer flex circuits are constructed using three or more flexible substrate layers interconnected using plated through-holes (PTHs). Multi-layer flex allows very high wiring density and are used for complex circuits in miniature devices.
Rigid-Flex PCBs
Rigid-flex PCBs combine flexible substrates with rigid PCB sections. The rigid sections mount components and connectors while the flexible sections act as interconnects between rigid sections. Rigid-flex constructions eliminate connectors and cables, simplify assembly, and improve reliability.
Flex-Rigid PCBs
Flex-rigid PCBs, in contrast to rigid-flex, have flexible exterior layers applied to the outer surfaces of a rigid PCB. This allows flexibility in regions of the board not occupied by rigid components. Flex-rigid is a lower-cost alternative to rigid-flex for some applications.
Flexible PCB Materials
The materials used in flexible PCB fabrication are selected for their mechanical, electrical, and environmental properties. Key material choices include:
Flexible Substrates
The substrate or base material provides mechanical support and electrical insulation for the conductors. The most common substrate material for flex circuits is polyimide (PI) film due to its excellent thermal, mechanical, and electrical properties. Other substrates used include polyester (PET), polyethylene naphthalate (PEN), and fluorinated ethylene propylene (FEP).
Conductive Materials
Copper foil is the most common conductor material used for flexible circuits. Copper thickness typically ranges from 9 μm to 70 μm (1/4 oz to 2 oz). The copper foil is bonded to the substrate using adhesive, heat, and pressure. Rolled annealed (RA) copper provides higher flexibility than electro-deposited (ED) copper.
Coverlay Materials
Coverlay is an insulating layer applied on top of the conductor layer to protect the circuits. Coverlays are typically made of polyimide or photo-imageable solder mask (PIM). PIM allows finer features and higher resolution than standard polyimide coverlays.
Stiffeners
Stiffeners are used to reinforce specific areas of the flex circuit, such as connector areas or component mounting locations. Stiffeners are commonly made of FR4, polyimide, or metal.
Adhesives
Adhesives bond the copper foil to the substrate and coverlays to the conductor layer. Typical adhesives include acrylic, epoxy, and pressure-sensitive adhesive (PSA). The choice of adhesive depends on the application requirements such as temperature resistance, flexibility, and chemical resistance.
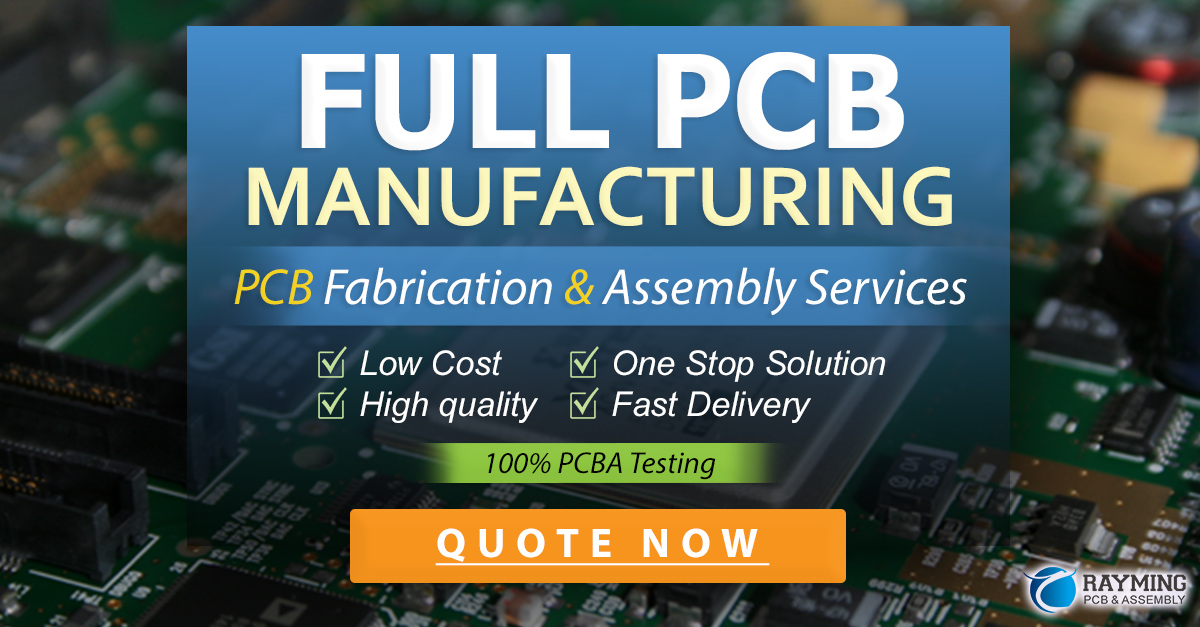
Flexible PCB Manufacturing Process
The manufacturing process for flexible PCBs shares many similarities with rigid PCB fabrication, but there are some unique challenges and considerations. The basic steps in flex circuit manufacturing include:
-
Circuit design and layout: The circuit schematic is created and a physical layout is designed using PCB CAD tools. The layout must account for mechanical stress, bend radii, and material stack-up.
-
Substrate preparation: The flexible substrate material is cut to size and cleaned.
-
Copper lamination: Copper foil is laminated to the substrate using adhesive, heat, and pressure.
-
Imaging and etching: The circuit pattern is transferred to the copper layer using photolithography and then etched using chemical or laser etching.
-
Coverlay lamination: The coverlay is laminated on top of the etched circuits using adhesive and heat.
-
Drilling and plating: Through-holes and microvias are drilled and then plated with copper to interconnect layers.
-
Surface finishing: The exposed copper is coated with a surface finish such as ENIG, OSP, or HASL to protect against corrosion and improve solderability.
-
Cutting and profiling: The panel is cut into individual circuit shapes using steel-rule dies, laser cutting, or routing.
-
Testing and inspection: The finished circuits are electrically tested and visually inspected for defects.
Flexible PCB Design Considerations
Designing flexible PCBs requires careful consideration of mechanical and electrical factors to ensure reliability and performance. Key design considerations include:
Bend Radius
The bend radius is the minimum radius that the flex circuit can be bent without damaging the conductors or substrate. The bend radius depends on the thickness and material properties of the substrate and copper. In general, the minimum bend radius is 6 times the total thickness of the circuit.
Conductor Width and Spacing
The width and spacing of copper traces impact the flexibility and current carrying capacity of the circuit. Wider traces are less flexible but can carry more current. Smaller spacing allows higher wiring density but may limit flexibility. Typical minimum trace width and spacing for flex circuits are 0.003 inches (3 mil).
Stiffener Placement
Stiffeners are used to reinforce areas of the flex circuit that experience high stress or require mechanical support, such as ZIF connector areas. The placement and shape of stiffeners must be carefully designed to avoid creating stress concentrations that can lead to cracking or delamination.
Thermal Management
Flexible circuits have limited ability to dissipate heat compared to rigid PCBs due to the thin substrates and lack of thermal vias. Designers must carefully consider component placement and power dissipation to avoid overheating. Thermal stiffeners or heat spreaders may be used in high-power applications.
Advantages and Disadvantages of Flexible PCBs
Advantages
- Flexibility and durability
- Lightweight and compact
- Space savings and high component density
- Simplified assembly and reduced wiring
- Suitable for high-speed and high-frequency applications
Disadvantages
- Higher cost than rigid PCBs
- Limited heat dissipation
- More complex design and manufacturing process
- Reduced current carrying capacity compared to rigid PCBs
- Limited component options due to size and weight constraints
Flexible PCB Applications by Industry
Consumer Electronics
Flexible PCBs are widely used in consumer electronics due to their lightweight, compact form factor, and ability to fit into tight spaces. Some common applications include:
- Smartphones and tablets
- Laptops and 2-in-1 devices
- Smartwatches and fitness trackers
- Digital cameras and camcorders
- Virtual reality and augmented reality headsets
Medical Devices
Flex circuits are used in a variety of medical devices due to their reliability, biocompatibility, and ability to conform to body contours. Applications include:
- Wearable health monitors
- Hearing aids and cochlear implants
- Pacemakers and defibrillators
- Endoscopes and catheters
- Surgical instruments
Automotive
Flexible PCBs are increasingly used in automotive applications to save weight, space, and simplify wiring harnesses. Common applications include:
- Dashboard displays and touchscreens
- Lighting systems
- Sensors and cameras
- Engine control units
- Electric vehicle battery management systems
Aerospace and Defense
Flex circuits were first developed for aerospace applications and continue to be used extensively in this industry. Applications include:
- Avionics systems
- Satellite communication systems
- Radar and guidance systems
- Wearable soldier systems
- Unmanned aerial vehicles (UAVs)
Industrial and Robotics
Flexible PCBs are used in industrial equipment and robotics applications that require compact, lightweight, and reliable electronics. Examples include:
- Industrial automation systems
- Robotics and motion control
- Inspection and testing equipment
- Portable instruments and gauges
- Wearable computing devices for workers
Flex Circuit Materials Comparison
Material | Dielectric Constant | Dissipation Factor | Moisture Absorption | Tensile Modulus | Tg (°C) | Tmax (°C) |
---|---|---|---|---|---|---|
Polyimide | 3.2-3.5 | 0.002-0.006 | 1.3-2.8% | 2.5 GPa | 360 | 200 |
Polyester (PET) | 3.0-3.2 | 0.002-0.005 | 0.4-0.6% | 2-4 GPa | 115 | 105 |
PEN | 3.1-3.3 | 0.002-0.005 | 0.3-0.4% | 5-6 GPa | 155 | 140 |
FEP | 2.0-2.1 | 0.0006-0.0009 | <0.01% | 0.4-0.8 GPa | 260 | 200 |
Adhesiveless PI | 3.2-3.5 | 0.002-0.006 | 1.3-2.8% | 2.5 GPa | 360 | 200 |
Flexible PCB Standards and Specifications
There are several industry standards and specifications that provide guidelines and requirements for flexible PCB design, fabrication, and testing. Some key standards include:
- IPC-2223: Sectional Design Standard for Flexible Printed Boards
- IPC-4202: Flexible Base Dielectrics for Use in Flexible Printed Circuitry
- IPC-4203: Cover Materials for Flexible Printed Circuitry
- IPC-4204: Adhesives for Flexible Printed Circuitry
- IPC-6013: Qualification and Performance Specification for Flexible Printed Boards
- ASTM-D-257: Standard Test Methods for DC Resistance or Conductance of Insulating Materials
- MIL-P-50884: General Specification for Flexible and Rigid-Flex Printed Wiring Boards
Frequently Asked Questions (FAQ)
1. What is the difference between flexible PCBs and rigid PCBs?
Flexible PCBs use flexible plastic substrates like polyimide instead of rigid substrates like FR4 used in rigid PCBs. This allows flex circuits to bend, twist, and conform to different shapes. Flex circuits are thinner, lighter, and more durable than rigid PCBs, but generally have higher cost and more complex manufacturing processes.
2. What are the typical materials used for flexible PCBs?
The most common substrate material for flex circuits is polyimide (PI) film. Other substrates include polyester (PET), polyethylene naphthalate (PEN), and fluorinated ethylene propylene (FEP). Copper foil is the most common conductor material, with adhesives used to bond the copper to the substrate.
3. What are the advantages of using flexible PCBs?
Advantages of flex circuits include flexibility and durability, lightweight and compact form factor, space savings and high component density, simplified assembly and reduced wiring, and suitability for high-speed and high-frequency applications.
4. What industries commonly use flexible PCBs?
Flex circuits are used across many industries including consumer electronics (smartphones, wearables), medical devices (hearing aids, pacemakers), automotive (displays, sensors), aerospace and defense (avionics, satellites), and industrial equipment (robotics, automation).
5. What are some key design considerations for flexible PCBs?
Key design considerations for flex circuits include bend radius (minimum radius without damaging the circuit), conductor width and spacing (affects flexibility and current carrying capacity), stiffener placement (reinforces high-stress areas), and thermal management (limited heat dissipation compared to rigid PCBs).
No responses yet