Introduction to Electronic Contract Manufacturing
Electronic Contract Manufacturing (ECM) is a business model where a company, known as the contract manufacturer, produces electronic components or products for another company, known as the Original Equipment Manufacturer (OEM). The OEM outsources the manufacturing process to the contract manufacturer, who is responsible for the production, assembly, and testing of the electronic products according to the OEM’s specifications and requirements.
ECM has become increasingly popular in recent years due to the growing complexity of electronic products, the need for specialized manufacturing equipment and expertise, and the desire for companies to reduce costs and focus on their core competencies.
Key Benefits of Electronic Contract Manufacturing
-
Cost reduction: By outsourcing manufacturing, OEMs can avoid the high costs associated with setting up and maintaining their own production facilities, purchasing expensive equipment, and hiring and training skilled labor.
-
Access to specialized expertise: ECM companies often have extensive experience and knowledge in manufacturing specific types of electronic products, ensuring high-quality output and adherence to industry standards.
-
Scalability and flexibility: OEMs can easily scale their production up or down based on market demand, without having to invest in additional resources or infrastructure.
-
Faster time-to-market: ECM companies can often produce products more quickly than OEMs, as they have streamlined processes and dedicated resources in place.
-
Focus on core competencies: By outsourcing manufacturing, OEMs can focus on their core competencies, such as product design, marketing, and sales.
The Electronic Contract Manufacturing Process
The ECM process typically involves the following steps:
-
Design and development: The OEM provides the contract manufacturer with the product design, specifications, and requirements.
-
Material sourcing: The contract manufacturer sources the necessary components and raw materials from approved suppliers.
-
Prototype and testing: The contract manufacturer creates a prototype of the product and conducts thorough testing to ensure it meets the OEM’s specifications and quality standards.
-
Production: Once the prototype is approved, the contract manufacturer begins mass production of the electronic product.
-
Quality control: Throughout the production process, the contract manufacturer conducts regular quality control checks to ensure the products meet the required standards.
-
Packaging and shipping: The finished products are packaged and shipped to the OEM or directly to their customers, depending on the agreed-upon arrangement.
Choosing the Right Electronic Contract Manufacturer
When selecting an ECM partner, OEMs should consider the following factors:
-
Technical capabilities: Ensure the contract manufacturer has the necessary equipment, expertise, and certifications to produce your specific electronic products.
-
Quality control processes: Look for a contract manufacturer with robust quality control processes and a proven track record of producing high-quality products.
-
Financial stability: Choose a financially stable contract manufacturer to ensure they can meet your long-term production needs and invest in new technologies as required.
-
Communication and collaboration: Select a contract manufacturer that values open communication, transparency, and collaboration to ensure a smooth and successful partnership.
-
Location and logistics: Consider the location of the contract manufacturer and their ability to efficiently manage the supply chain and logistics to meet your delivery requirements.
Types of Electronic Contract Manufacturing Services
ECM companies offer a wide range of services to meet the diverse needs of OEMs. Some of the most common types of ECM services include:
1. Printed Circuit Board (PCB) Assembly
PCB assembly is the process of soldering electronic components onto a printed circuit board. ECM companies often specialize in various types of PCB assembly, such as:
- Through-hole assembly: Components are inserted into drilled holes on the PCB and soldered onto the opposite side.
- Surface-mount assembly: Components are placed and soldered directly onto the surface of the PCB.
- Mixed-technology assembly: A combination of through-hole and surface-mount components are used on a single PCB.
2. Cable and Harness Assembly
Cable and harness assembly involves the production of custom electrical cables and wire harnesses for use in electronic products. This service may include:
- Cutting and stripping wires to specified lengths
- Crimping terminals and connectors onto wire ends
- Arranging and bundling wires into harnesses
- Testing the continuity and functionality of the assembled cables and harnesses
3. Box Build Assembly
Box build assembly is the process of integrating various electronic components, PCBs, and sub-assemblies into a complete, functional product. This service may include:
- Mechanical assembly of the enclosure or box
- Installation of PCBs, cables, and other components
- Wiring and interconnection of sub-assemblies
- Functional testing and quality control of the finished product
4. Electronic Design and Engineering Support
Some ECM companies offer electronic design and engineering support services to help OEMs develop and optimize their products. These services may include:
- Product concept development and feasibility studies
- Schematic design and PCB layout
- Bill of Materials (BOM) optimization and component selection
- Design for Manufacturability (DFM) and Design for Assembly (DFA) analysis
- Firmware and software development
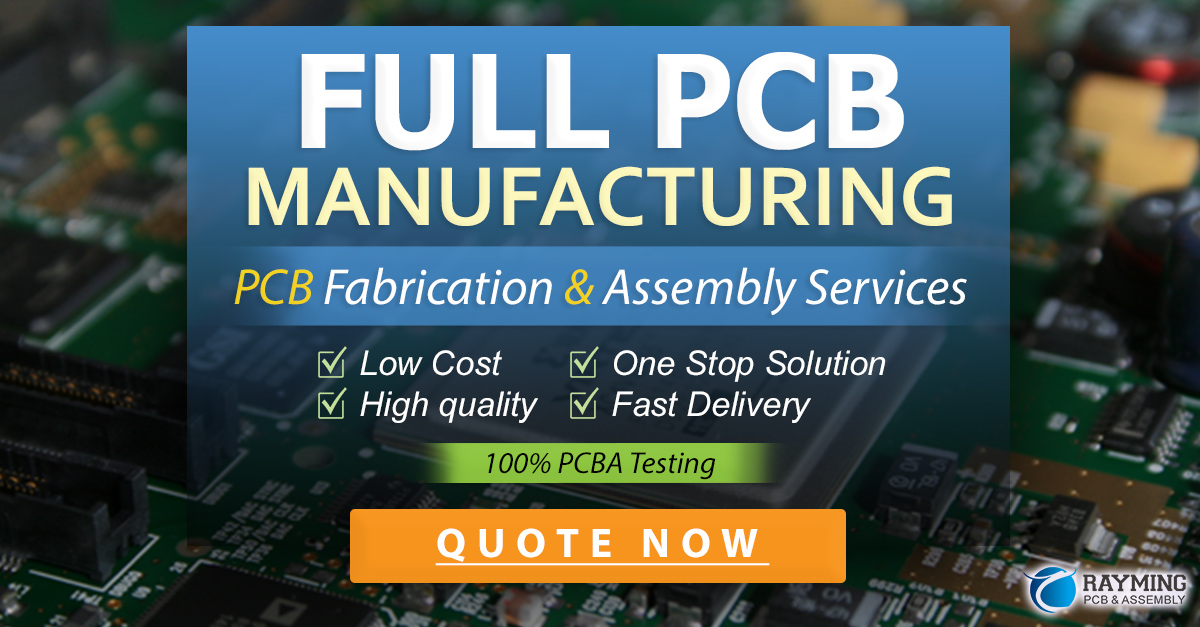
Advantages of Electronic Contract Manufacturing
ECM offers several key advantages for OEMs, including:
1. Cost Savings
Outsourcing electronic manufacturing to an ECM company can significantly reduce costs for OEMs. By leveraging the contract manufacturer’s economies of scale, purchasing power, and efficient processes, OEMs can minimize their capital expenditures and operating costs associated with in-house manufacturing.
2. Access to Specialized Expertise and Technology
ECM companies often have extensive experience and specialized knowledge in manufacturing specific types of electronic products. They invest in the latest manufacturing technologies, equipment, and processes to ensure high-quality output and adherence to industry standards. By partnering with an ECM company, OEMs can access this expertise and technology without having to invest in it themselves.
3. Increased Flexibility and Scalability
Outsourcing manufacturing to an ECM company allows OEMs to quickly adapt to changes in market demand. They can easily scale production up or down as needed, without having to worry about the capacity constraints or fixed costs associated with in-house manufacturing. This flexibility enables OEMs to respond more quickly to customer needs and maintain a competitive edge in the market.
4. Improved Time-to-Market
ECM companies typically have streamlined processes and dedicated resources in place to manufacture electronic products efficiently. By outsourcing manufacturing, OEMs can often bring their products to market faster than if they were to manufacture them in-house. This can be a significant advantage in fast-paced, competitive markets where being first to market can make all the difference.
5. Enhanced Focus on Core Competencies
By outsourcing manufacturing to an ECM company, OEMs can free up resources and focus on their core competencies, such as product design, marketing, and sales. This allows them to allocate their resources more strategically and invest in areas that drive growth and innovation for their business.
Challenges and Risks of Electronic Contract Manufacturing
While ECM offers many benefits, there are also some challenges and risks that OEMs should be aware of, including:
1. Loss of Control
When outsourcing manufacturing to an ECM company, OEMs may have less direct control over the production process. This can be a concern for OEMs who have strict quality control requirements or who want to maintain close oversight of the manufacturing process.
2. Intellectual Property (IP) Risks
Outsourcing manufacturing to an ECM company may involve sharing sensitive product designs, specifications, and other IP with the contract manufacturer. OEMs must take steps to protect their IP, such as signing non-disclosure agreements (NDAs) and implementing robust security measures to prevent unauthorized access or use of their IP.
3. Communication and Collaboration Challenges
Working with an ECM company requires effective communication and collaboration between the OEM and the contract manufacturer. Language barriers, cultural differences, and time zone differences can sometimes make this challenging. OEMs should select an ECM partner that values open communication and has processes in place to facilitate smooth collaboration.
4. Supply Chain Risks
Outsourcing manufacturing to an ECM company can introduce additional risks into the supply chain, such as the risk of disruptions due to natural disasters, geopolitical events, or supplier issues. OEMs should carefully evaluate the ECM company’s supply chain management processes and contingency plans to mitigate these risks.
5. Quality Control Issues
While ECM companies typically have robust quality control processes in place, there is always a risk that quality issues may arise. OEMs should work closely with their ECM partner to establish clear quality standards and expectations, and to implement regular quality audits and inspections to ensure that products meet the required specifications.
Best Practices for Successful Electronic Contract Manufacturing Partnerships
To ensure a successful partnership with an ECM company, OEMs should follow these best practices:
-
Clearly define product specifications and requirements upfront to avoid misunderstandings and ensure that the ECM company can meet your needs.
-
Establish open and regular communication channels with your ECM partner to facilitate collaboration and quickly resolve any issues that may arise.
-
Implement robust quality control processes and regularly audit the ECM company’s performance to ensure that products meet your quality standards.
-
Protect your intellectual property by signing NDAs and implementing security measures to prevent unauthorized access or use of your IP.
-
Continuously monitor and evaluate the performance of your ECM partner, and be prepared to make changes if necessary to ensure that your needs are being met.
The Future of Electronic Contract Manufacturing
As the electronics industry continues to evolve, so too will the role of ECM companies. Some of the key trends and developments that are likely to shape the future of ECM include:
1. Increased Automation and Digitalization
ECM companies will continue to invest in automation and digitalization technologies to improve efficiency, reduce costs, and enhance quality control. This may include the use of robotics, artificial intelligence (AI), and the Internet of Things (IoT) to streamline manufacturing processes and enable predictive maintenance.
2. Growing Demand for Customization and Flexibility
As product life cycles continue to shorten and consumer demands for customization increase, ECM companies will need to become more agile and flexible in their manufacturing processes. This may involve the use of modular manufacturing techniques, 3D printing, and other advanced technologies to enable faster, more customized production.
3. Expansion into New Markets and Industries
ECM companies will continue to expand into new markets and industries, such as automotive, medical devices, and renewable energy. This will require ECM companies to invest in new technologies and expertise to meet the specific requirements of these industries.
4. Increased Focus on Sustainability and Circular Economy
As concerns about climate change and environmental sustainability continue to grow, ECM companies will face increasing pressure to adopt sustainable manufacturing practices and support the transition to a circular economy. This may involve the use of eco-friendly materials, renewable energy sources, and closed-loop manufacturing processes that minimize waste and maximize resource efficiency.
Conclusion
Electronic Contract Manufacturing is a critical component of the modern electronics industry, enabling OEMs to outsource their manufacturing needs to specialized companies with the expertise, technology, and resources to produce high-quality products efficiently and cost-effectively. By partnering with an ECM company, OEMs can reduce costs, improve time-to-market, and focus on their core competencies, while benefiting from the contract manufacturer’s specialized knowledge and capabilities.
However, outsourcing manufacturing also introduces new challenges and risks, such as loss of control, IP risks, and supply chain disruptions. To mitigate these risks and ensure a successful partnership, OEMs should carefully evaluate potential ECM partners, establish clear communication channels and quality control processes, and continuously monitor and assess the performance of their chosen partner.
As the electronics industry continues to evolve, ECM companies will play an increasingly important role in enabling innovation, customization, and sustainability. By staying at the forefront of technological advancements and adapting to changing market demands, ECM companies can help OEMs stay competitive and succeed in the dynamic world of electronics manufacturing.
Frequently Asked Questions (FAQ)
-
What is the difference between Electronic Contract Manufacturing (ECM) and Original Equipment Manufacturing (OEM)?
-
ECM refers to a company that manufactures electronic products or components on behalf of another company (the OEM), based on the OEM’s designs and specifications. The OEM is the company that ultimately sells the products under its own brand name.
-
What types of services do Electronic Contract Manufacturing companies typically offer?
-
ECM companies offer a wide range of services, including PCB assembly, cable and harness assembly, box build assembly, and electronic design and engineering support. Some ECM companies may specialize in specific types of products or services, while others offer a more comprehensive range of capabilities.
-
How can outsourcing to an Electronic Contract Manufacturer help reduce costs for OEMs?
-
Outsourcing to an ECM company can help OEMs reduce costs in several ways, including:
- Avoiding the high capital expenditures associated with setting up and maintaining in-house manufacturing facilities and equipment
- Leveraging the ECM company’s economies of scale and purchasing power to obtain components and materials at lower costs
- Reducing labor costs by accessing the ECM company’s skilled workforce and efficient manufacturing processes
-
What should OEMs consider when selecting an Electronic Contract Manufacturing partner?
-
When selecting an ECM partner, OEMs should consider factors such as:
- Technical capabilities and expertise in manufacturing the specific type of product required
- Quality control processes and certifications
- Financial stability and ability to scale production as needed
- Communication and collaboration processes
- Location and logistics capabilities
-
How can OEMs protect their intellectual property when working with an Electronic Contract Manufacturer?
-
To protect their intellectual property, OEMs should:
- Sign non-disclosure agreements (NDAs) with the ECM company and any other relevant parties
- Implement secure data sharing and storage practices to prevent unauthorized access to sensitive information
- Establish clear guidelines and expectations around IP ownership and use in the contract with the ECM company
- Regularly monitor and audit the ECM company’s processes and practices to ensure compliance with IP protection requirements
No responses yet