Composition of Copper Clad Laminate
Copper-Clad Laminate is made up of two main components:
- Copper foil
- Non-conductive substrate
Copper Foil
The copper foil used in CCL is typically made of high-purity, electrolytic copper. The thickness of the copper foil can vary depending on the specific requirements of the PCB. Common copper foil thicknesses include:
Thickness (oz/ft²) | Thickness (μm) |
---|---|
0.5 | 17.5 |
1 | 35 |
2 | 70 |
3 | 105 |
The copper foil is treated to improve its adhesion to the substrate and to enhance its resistance to oxidation.
Non-Conductive Substrate
The non-conductive substrate in copper-clad laminate provides the mechanical support and insulation required for the PCB. The most common substrate materials include:
- FR-4: A glass-reinforced epoxy laminate, widely used for its excellent mechanical and electrical properties.
- CEM-1: A composite epoxy material with lower cost and performance compared to FR-4.
- Polyimide: A high-temperature substrate material used in applications requiring increased thermal stability.
- PTFE: A low-loss, high-frequency substrate material used in RF and microwave applications.
The choice of substrate material depends on factors such as the intended application, operating environment, and cost constraints.
Manufacturing Process of Copper Clad Laminate
The manufacturing process of copper-clad laminate involves several steps:
- Substrate preparation: The non-conductive substrate material is cut to the desired size and shape.
- Copper foil preparation: The copper foil is cleaned and treated to improve its adhesion properties.
- Lamination: The copper foil is bonded to the substrate using heat and pressure in a lamination press.
- Cooling: The laminated board is cooled to room temperature.
- Inspection: The resulting copper-clad laminate is inspected for defects and conformity to specifications.
Properties of Copper Clad Laminate
Copper-clad laminate exhibits several important properties that make it suitable for PCB manufacturing:
Electrical Properties
- Conductivity: The copper foil provides excellent electrical conductivity, allowing for the efficient transfer of electrical signals.
- Dielectric constant: The substrate material has a specific dielectric constant that affects the signal propagation speed and impedance of the PCB.
- Dissipation factor: The substrate’s dissipation factor influences the signal loss and heat generation in the PCB.
Mechanical Properties
- Strength: The substrate material provides mechanical strength and rigidity to the PCB.
- Dimensional stability: Copper-clad laminate maintains its dimensions under various environmental conditions, ensuring the integrity of the PCB.
- Thermal expansion: The coefficient of thermal expansion (CTE) of the substrate should be compatible with that of the copper foil to minimize stress and warpage.
Thermal Properties
- Glass transition temperature (Tg): The temperature at which the substrate material transitions from a rigid to a softer state, affecting the PCB’s performance at elevated temperatures.
- Thermal conductivity: The substrate’s ability to conduct heat influences the thermal management of the PCB.
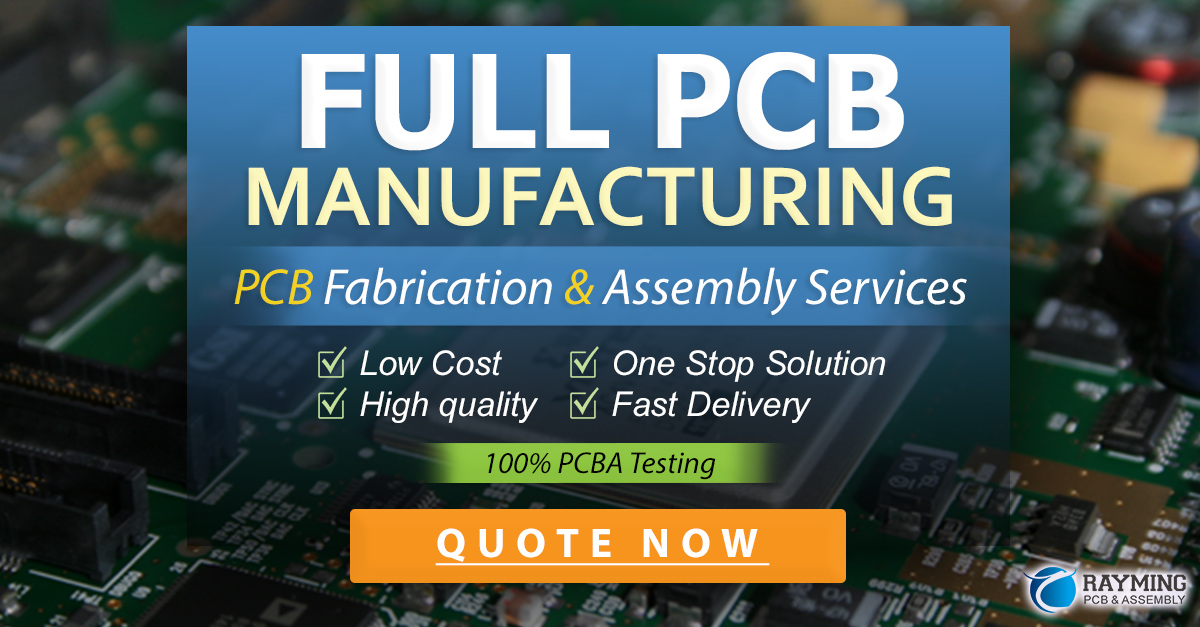
Applications of Copper Clad Laminate in PCB Manufacturing
Copper-clad laminate is used in various stages of PCB manufacturing:
Etching
The copper foil on the CCL is selectively etched away to create the desired conductive patterns on the PCB. The etching process involves:
- Applying a photoresist layer on the copper foil.
- Exposing the photoresist to UV light through a photomask with the desired circuit pattern.
- Developing the photoresist to remove the exposed areas.
- Etching away the exposed copper using a chemical etchant.
- Removing the remaining photoresist to reveal the final copper pattern.
Multilayer PCB Fabrication
Copper-clad laminate is used to create the individual layers of a multilayer PCB. The process involves:
- Etching the inner layers of the PCB using the same process as described above.
- Aligning and stacking the etched inner layers with prepreg (pre-impregnated) layers in between.
- Laminating the stack under heat and pressure to bond the layers together.
- Drilling through-holes and vias to interconnect the layers.
- Plating the through-holes and vias with copper to establish electrical connections.
Surface Finish
Copper-clad laminate also serves as the base for applying various surface finishes to the PCB, such as:
- HASL (Hot Air Solder Leveling): A tin-lead alloy is applied to the exposed copper surfaces to improve solderability and protect against oxidation.
- ENIG (Electroless Nickel Immersion Gold): A layer of nickel is deposited on the copper, followed by a thin layer of gold to provide excellent solderability and corrosion resistance.
- OSP (Organic Solderability Preservative): A thin, organic coating is applied to the copper surfaces to prevent oxidation and maintain solderability.
Choosing the Right Copper Clad Laminate
When selecting a copper-clad laminate for a specific PCB application, several factors should be considered:
Electrical Requirements
- Signal frequency: Higher frequencies require substrates with lower dielectric constants and dissipation factors to minimize signal loss and distortion.
- Impedance control: The substrate’s dielectric constant and thickness influence the characteristic impedance of the PCB traces.
Mechanical Requirements
- Thickness: The overall thickness of the CCL should be appropriate for the desired PCB thickness and the number of layers.
- Flexibility: Flexible PCBs require substrates with high flexibility and durability, such as polyimide.
Environmental Conditions
- Operating temperature: The substrate material should have a glass transition temperature (Tg) higher than the maximum operating temperature of the PCB.
- Humidity: The substrate should resist moisture absorption to maintain its dimensional stability and prevent delamination.
Cost Considerations
- Material cost: The choice of substrate material and copper foil thickness affects the overall cost of the CCL and the resulting PCB.
- Processing cost: Some substrate materials may require specialized processing techniques, impacting the manufacturing cost.
Quality Control and Testing
To ensure the quality and reliability of copper-clad laminate, various tests and inspections are performed:
Visual Inspection
- Surface defects: The CCL surface is inspected for scratches, pits, and other irregularities that may affect the PCB’s performance.
- Copper thickness: The uniformity and consistency of the copper foil thickness are visually checked.
Electrical Testing
- Dielectric strength: The substrate’s ability to withstand high voltages without breakdown is tested.
- Insulation resistance: The resistance between the copper foil and the substrate is measured to ensure adequate insulation.
Mechanical Testing
- Peel strength: The adhesion between the copper foil and the substrate is tested by measuring the force required to peel the foil from the substrate.
- Flexural strength: The substrate’s ability to withstand bending and flexing without cracking or delamination is evaluated.
Environmental Testing
- Thermal cycling: The CCL is subjected to repeated cycles of high and low temperatures to assess its resistance to thermal stress.
- Humidity exposure: The laminate is exposed to high humidity conditions to evaluate its resistance to moisture absorption and delamination.
Frequently Asked Questions (FAQ)
-
What is the difference between FR-4 and CEM-1 substrates?
FR-4 is a high-performance, glass-reinforced epoxy laminate, while CEM-1 is a lower-cost composite epoxy material. FR-4 offers better mechanical and electrical properties compared to CEM-1. -
Can copper-clad laminate be used for flexible PCBs?
Yes, copper-clad laminates with flexible substrates, such as polyimide, can be used to manufacture flexible PCBs. These laminates provide the necessary flexibility and durability required for flexible PCB applications. -
What is the purpose of surface finishes on copper-clad laminate?
Surface finishes, such as HASL, ENIG, and OSP, are applied to the exposed copper surfaces of the laminate to improve solderability, protect against oxidation, and enhance the PCB’s overall reliability. -
How does the thickness of the copper foil affect the PCB’s performance?
The thickness of the copper foil determines the current-carrying capacity and the trace width of the PCB. Thicker copper foils allow for higher current carrying capacity and wider traces, which can be beneficial for power electronics applications. However, thicker copper foils also increase the overall thickness and weight of the PCB. -
Can copper-clad laminate be recycled?
Yes, copper-clad laminate can be recycled. The recycling process involves separating the copper foil from the substrate material. The copper is then recycled and reused, while the substrate material can be ground down and repurposed for other applications or used as a filler material.
Conclusion
Copper-clad laminate is a fundamental component in the manufacturing of printed circuit boards. Its combination of a conductive copper layer and a non-conductive substrate material provides the necessary electrical, mechanical, and thermal properties required for reliable PCB performance. Understanding the composition, manufacturing process, and properties of copper-clad laminate is essential for designing and fabricating high-quality PCBs. By selecting the appropriate CCL for a specific application and following proper quality control and testing procedures, PCB manufacturers can ensure the reliability and functionality of their products.
As technology advances and the demand for more complex and high-performance PCBs grows, the development of new copper-clad laminate materials and manufacturing techniques will continue to evolve. Innovations in substrate materials, copper foil treatments, and lamination processes will enable the creation of PCBs with improved electrical, mechanical, and thermal properties, meeting the ever-increasing requirements of modern electronic devices and systems.
No responses yet