Advantages of Multilayer PCBs
Multilayer PCBs offer several advantages over single or double-layer PCBs:
-
Increased Density: Multilayer PCBs allow for a higher component density, as the additional layers provide more space for routing traces and placing components. This enables the design of more complex circuits in a smaller footprint.
-
Improved Signal Integrity: The use of multiple layers helps to reduce electromagnetic interference (EMI) and crosstalk between signals. By designing proper signal routing and ground planes, the signal integrity can be maintained, ensuring reliable performance of the circuit.
-
Enhanced Thermal Management: Multilayer PCBs can incorporate dedicated layers for power and ground, which act as heat sinks and help to dissipate heat generated by components. This improves the thermal management of the board and prevents overheating.
-
Reduced Size and Weight: With the ability to accommodate more components and routing in a smaller area, multilayer PCBs enable the design of compact and lightweight electronic devices. This is particularly important for portable and space-constrained applications.
-
Increased Reliability: Multilayer PCBs offer better mechanical strength and durability compared to single or double-layer boards. The additional layers provide support and reduce the risk of board warping or damage during assembly and operation.
Multilayer PCB Structure
A typical multilayer PCB consists of the following layers:
-
Signal Layers: These layers are used for routing the electrical signals between components. The number of signal layers depends on the complexity of the circuit and the routing requirements.
-
Power and Ground Layers: Dedicated layers for power and ground are used to distribute power to the components and provide a low-impedance return path for the signals. These layers also act as shields to reduce EMI and crosstalk.
-
Insulating Layers: Insulating layers, typically made of FR-4 material, are placed between the conductive layers to provide electrical isolation and mechanical support.
-
Solder Mask: A protective coating applied to the outer layers of the PCB to prevent short circuits and improve the solderability of the pads.
-
Silkscreen: A printed layer on top of the solder mask that provides labels, component outlines, and other visual information for assembly and identification purposes.
Here’s a visual representation of a 4-layer PCB structure:
Layer | Description |
---|---|
Top Layer | Signal layer, components, and silkscreen |
Ground | Ground plane |
Power | Power plane |
Bottom Layer | Signal layer and solder mask |
Designing Multilayer PCBs
Designing multilayer PCBs requires careful consideration of various factors to ensure proper functionality, signal integrity, and manufacturability. Some key aspects to consider include:
-
Layer Stack-up: Determine the number of layers required and the arrangement of signal, power, and ground layers. The stack-up should be designed to minimize EMI, crosstalk, and impedance mismatch.
-
Signal Routing: Route the signals on the appropriate layers, following good design practices such as avoiding sharp bends, maintaining proper trace width and spacing, and minimizing the length of high-speed signals.
-
Via Placement: Place vias strategically to connect traces between layers while minimizing the impact on signal integrity. Use appropriate via types (through-hole, blind, or buried) based on the design requirements.
-
Power and Ground Distribution: Design a robust power and ground distribution network to ensure stable power delivery to all components. Use proper plane shapes, copper weights, and decoupling capacitors to minimize impedance and noise.
-
Thermal Management: Consider the thermal requirements of the components and design appropriate thermal relief pads, copper pours, and heat sinks to dissipate heat effectively.
-
Manufacturing Constraints: Adhere to the manufacturing capabilities and guidelines provided by the PCB fabricator, such as minimum trace width and spacing, hole sizes, and clearances.
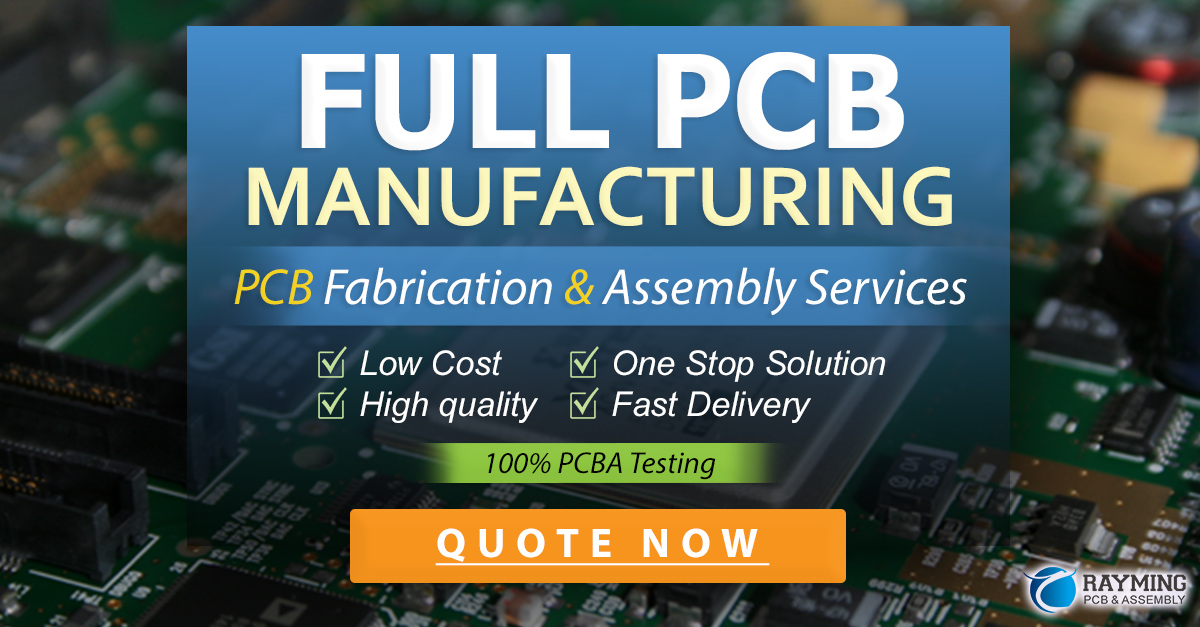
Manufacturing Multilayer PCBs
The manufacturing process of multilayer PCBs involves several steps:
-
Layer Fabrication: Each conductive layer is fabricated separately using a photolithography process. The desired pattern is transferred onto the copper-clad laminate using a photomask and then etched away, leaving only the desired traces and pads.
-
Lamination: The fabricated layers are aligned and laminated together under high pressure and temperature. The insulating material (prepreg) between the layers melts and bonds the layers together, forming a solid board.
-
Drilling: Holes are drilled through the board to accommodate through-hole components and vias. The type of drilling (mechanical or laser) depends on the hole size and accuracy requirements.
-
Plating: The drilled holes are plated with copper to establish electrical connections between layers. This is typically done using an electroless plating process followed by an electroplating process.
-
Solder Mask and Silkscreen: A solder mask is applied to the outer layers to protect the copper traces and prevent solder bridging. The silkscreen layer is then printed on top of the solder mask for component identification and assembly guidance.
-
Surface Finishing: A surface finish, such as HASL (Hot Air Solder Leveling), ENIG (Electroless Nickel Immersion Gold), or OSP (Organic Solderability Preservative), is applied to the exposed copper pads to enhance solderability and protect against oxidation.
-
Electrical Testing: The manufactured PCBs undergo electrical testing to ensure proper connectivity and functionality. Various tests, such as continuity, insulation resistance, and high-voltage testing, are performed to detect any manufacturing defects.
Applications of Multilayer PCBs
Multilayer PCBs find applications in a wide range of industries and products, including:
-
Consumer Electronics: Smartphones, tablets, laptops, and wearable devices often utilize multilayer PCBs to achieve compact and high-performance designs.
-
Telecommunications: Network equipment, routers, switches, and base stations rely on multilayer PCBs to handle high-speed data transmission and complex routing requirements.
-
Automotive: Modern vehicles incorporate multilayer PCBs in various systems, such as infotainment, engine control, and advanced driver assistance systems (ADAS).
-
Medical Devices: Medical equipment, such as patient monitors, diagnostic devices, and imaging systems, employ multilayer PCBs for reliable and precise operation.
-
Aerospace and Defense: Avionics systems, satellite communication equipment, and military electronics use multilayer PCBs to meet stringent reliability and performance requirements.
-
Industrial Automation: Control systems, sensors, and actuators in industrial automation applications often rely on multilayer PCBs for robust and reliable operation in harsh environments.
Frequently Asked Questions (FAQ)
-
Q: What is the difference between a multilayer PCB and a single-layer PCB?
A: A multilayer PCB consists of three or more conductive layers, while a single-layer PCB has only one conductive layer. Multilayer PCBs offer higher density, improved signal integrity, and better thermal management compared to single-layer PCBs. -
Q: How many layers can a multilayer PCB have?
A: Multilayer PCBs can have various numbers of layers, typically ranging from 4 to 12 layers. However, advanced designs can have even more layers, such as 16, 24, or 32 layers, depending on the complexity and requirements of the application. -
Q: What materials are used in multilayer PCBs?
A: The most common base material used in multilayer PCBs is FR-4, which is a glass-reinforced epoxy laminate. Other materials, such as high-frequency laminates (e.g., Rogers) or flexible substrates (e.g., polyimide), can also be used for specific applications. -
Q: Are multilayer PCBs more expensive than single or double-layer PCBs?
A: Yes, multilayer PCBs are generally more expensive than single or double-layer PCBs due to the additional materials, processing steps, and complexity involved in their manufacturing. However, the cost is often justified by the enhanced performance, reliability, and space savings they offer. -
Q: What are the challenges in designing multilayer PCBs?
A: Designing multilayer PCBs presents several challenges, such as ensuring proper layer stack-up, managing signal integrity, minimizing EMI and crosstalk, optimizing power distribution, and considering manufacturing constraints. Careful design practices and simulation tools are essential to overcome these challenges and achieve a successful multilayer PCB design.
Conclusion
Multilayer PCBs are a crucial component in modern electronic devices, offering numerous advantages over single or double-layer PCBs. With their ability to accommodate higher component density, improve signal integrity, and enhance thermal management, multilayer PCBs enable the design of compact, high-performance, and reliable electronic systems.
Designing and manufacturing multilayer PCBs requires expertise and attention to detail to ensure proper functionality and manufacturability. By considering factors such as layer stack-up, signal routing, power distribution, and thermal management, designers can create optimal multilayer PCB designs that meet the specific requirements of their applications.
As technology continues to advance and the demand for more complex and compact electronic devices grows, the importance of multilayer PCBs will only increase. Understanding the fundamentals, advantages, and design considerations of multilayer PCBs is essential for engineers and manufacturers to stay at the forefront of the ever-evolving electronics industry.
No responses yet