History of Polytetrafluoroethylene
Discovery and Development
Polytetrafluoroethylene was accidentally discovered by Roy J. Plunkett, a chemist working for DuPont, in 1938. While attempting to create a new refrigerant, Plunkett found that the tetrafluoroethylene gas had polymerized into a white, waxy solid inside its pressurized canister. This new material exhibited exceptional properties, such as low friction, high heat resistance, and chemical inertness.
DuPont recognized the potential of this new discovery and began researching and developing applications for PTFE. In 1945, the company patented the material and registered the Teflon trademark. The first commercial use of PTFE was as a coating for valves and seals in the Manhattan Project during World War II, due to its corrosion resistance and ability to withstand high temperatures.
Expansion and Commercialization
Following the war, DuPont continued to research and expand the applications of PTFE. In the 1950s, the company introduced Teflon-coated non-stick cookware, which quickly gained popularity among consumers. This marked the beginning of PTFE’s widespread use in various industries.
Over the years, new processing methods and formulations were developed, enabling the creation of PTFE products with enhanced properties and performance. These advancements led to the expansion of PTFE’s applications in fields such as aerospace, automotive, electronics, and medical devices.
Properties of Polytetrafluoroethylene
Chemical Structure and Composition
Polytetrafluoroethylene is a linear polymer composed of repeating tetrafluoroethylene (TFE) monomer units. The chemical formula for PTFE is (C2F4)n, where n represents the number of TFE units in the polymer chain. The carbon-fluorine bonds in PTFE are extremely strong, contributing to the material’s exceptional properties.
The molecular structure of PTFE is highly ordered and crystalline, with the fluorine atoms evenly distributed around the carbon backbone. This unique structure is responsible for PTFE’s low surface energy, high melting point, and resistance to chemical attack.
Physical Properties
PTFE exhibits a range of remarkable physical properties that make it suitable for various applications:
-
Low friction coefficient: PTFE has one of the lowest friction coefficients of any solid material, making it an excellent choice for applications requiring low friction and wear resistance.
-
High melting point: With a melting point of approximately 327°C (620°F), PTFE can withstand high temperatures without degrading or deforming.
-
Chemical inertness: PTFE is resistant to most chemicals, including strong acids, bases, and solvents. This property makes it suitable for use in corrosive environments.
-
Hydrophobicity: PTFE has a low surface energy, which results in its hydrophobic nature. This property contributes to its non-stick characteristics and resistance to wetting.
-
Electrical insulation: PTFE is an excellent electrical insulator, with a high dielectric strength and low Dielectric constant. This makes it suitable for use in electrical and electronic applications.
-
Low thermal conductivity: PTFE has a low thermal conductivity, which makes it an effective thermal insulator.
Mechanical Properties
PTFE’s mechanical properties are unique compared to other polymers:
-
Tensile strength: PTFE has a relatively low tensile strength compared to other engineering plastics. However, its tensile strength can be improved through the addition of fillers or by using modified PTFE formulations.
-
Elongation at break: PTFE has a high elongation at break, allowing it to deform significantly before fracturing. This property contributes to its toughness and ability to withstand stress.
-
Creep resistance: PTFE exhibits a high degree of creep, especially under high loads and temperatures. This can be mitigated by using PTFE formulations with improved creep resistance or by designing components to account for creep behavior.
-
Hardness: PTFE has a relatively low hardness compared to other engineering plastics. However, its hardness can be increased through the use of fillers or by using modified PTFE formulations.
Applications of Polytetrafluoroethylene
Industrial Applications
PTFE’s unique properties make it suitable for a wide range of industrial applications:
-
Seals and gaskets: PTFE’s chemical inertness, low friction, and high-temperature resistance make it an ideal material for seals and gaskets in chemical processing, automotive, and aerospace industries.
-
Bearings and bushings: The low friction and wear resistance of PTFE make it suitable for use in bearings and bushings, particularly in applications where lubrication is not feasible or desirable.
-
Cable and wire insulation: PTFE’s excellent electrical insulation properties and high-temperature resistance make it a popular choice for insulating cables and wires in high-performance electrical and electronic applications.
-
Filtration membranes: PTFE membranes are used in various filtration applications, including water treatment, air filtration, and chemical processing, due to their chemical inertness and ability to form microporous structures.
Consumer Applications
PTFE’s non-stick and low-friction properties have led to its widespread use in consumer products:
-
Non-stick cookware: PTFE coatings on cookware provide a non-stick surface that prevents food from adhering and makes cleaning easier.
-
Waterproof and breathable fabrics: PTFE membranes, such as Gore-Tex, are used in waterproof and breathable clothing and footwear, allowing moisture vapor to pass through while preventing liquid water from penetrating.
-
Dental floss: PTFE’s low friction and chemical inertness make it an ideal material for dental floss, as it can easily slide between teeth and resist bacterial growth.
-
Personal care products: PTFE is used in various personal care products, such as hair straighteners and curling irons, due to its heat resistance and non-stick properties.
Medical Applications
PTFE’s biocompatibility and chemical inertness make it suitable for use in medical devices:
-
Vascular grafts: PTFE is used to create artificial blood vessels for bypass surgery and other vascular procedures.
-
Sutures: PTFE sutures are used in surgery due to their low tissue reactivity and high strength.
-
Catheter coatings: PTFE coatings on catheters reduce friction and prevent the adhesion of bacteria and other contaminants.
-
Orthopedic implants: PTFE is used in various orthopedic implants, such as joint replacements and ligament replacements, due to its low friction and wear resistance.
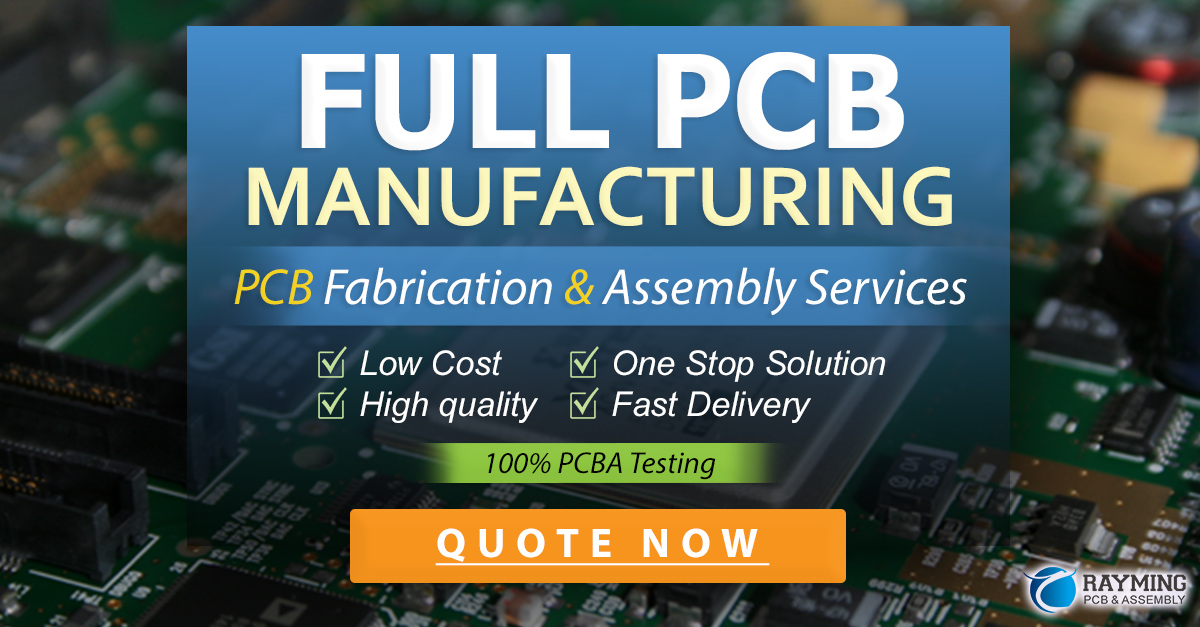
Environmental Considerations
PFOA and PFOS
Perfluorooctanoic acid (PFOA) and perfluorooctanesulfonic acid (PFOS) are two chemicals that were historically used in the production of PTFE and other fluoropolymers. These substances have been linked to potential health and environmental concerns, including bioaccumulation and persistence in the environment.
In response to these concerns, major manufacturers have phased out the use of PFOA and PFOS in PTFE production. Alternative processing methods and chemicals have been developed to produce PTFE without the use of these substances.
Recycling and Disposal
PTFE is not biodegradable and can persist in the environment for long periods. Proper disposal and recycling of PTFE products are essential to minimize their environmental impact.
PTFE can be recycled through various methods, including:
-
Mechanical recycling: PTFE scrap can be ground into powder and reprocessed into new products.
-
Chemical recycling: PTFE can be chemically decomposed into its constituent monomers, which can then be used to produce new PTFE or other fluoropolymers.
-
Thermal recycling: PTFE can be incinerated to recover the energy content, with proper emission control measures in place.
When disposing of PTFE products, it is important to follow local regulations and guidelines to ensure proper handling and minimize environmental impact.
Future Developments and Research
Researchers continue to explore new ways to enhance the properties and performance of PTFE, as well as develop new applications for this versatile material. Some areas of ongoing research include:
-
Modified PTFE formulations: The development of new PTFE formulations with improved mechanical properties, such as higher tensile strength and creep resistance, can expand the range of applications for PTFE.
-
Nanocomposites: The incorporation of nanoparticles, such as carbon nanotubes or graphene, into PTFE matrices can enhance the material’s mechanical, thermal, and electrical properties.
-
Additive manufacturing: The development of PTFE-based materials suitable for additive manufacturing processes, such as 3D printing, can enable the creation of complex structures and geometries not achievable through traditional manufacturing methods.
-
Sustainability: Research into more sustainable production methods, alternative processing chemicals, and improved recycling technologies can help reduce the environmental impact of PTFE throughout its life cycle.
Frequently Asked Questions
-
Q: Is PTFE safe for use in cookware?
A: When used as intended, PTFE-coated cookware is generally considered safe. However, overheating PTFE coatings above 500°F (260°C) can cause the release of fumes that may cause temporary flu-like symptoms in humans and may be harmful to birds. It is important to follow the manufacturer’s guidelines for safe use and to avoid overheating PTFE-coated cookware. -
Q: Can PTFE be used in high-temperature applications?
A: PTFE has a high melting point of approximately 327°C (620°F) and can maintain its properties at elevated temperatures. However, the maximum service temperature for PTFE is generally considered to be around 260°C (500°F), as prolonged exposure to higher temperatures can cause the material to degrade and release harmful fumes. -
Q: Is PTFE resistant to all chemicals?
A: While PTFE is resistant to most chemicals, it can be affected by certain highly reactive substances, such as molten alkali metals, elemental fluorine, and certain complex halogenated compounds at high temperatures. In most industrial and consumer applications, however, PTFE provides excellent chemical resistance. -
Q: Can PTFE be bonded to other materials?
A: Due to its low surface energy and non-stick properties, bonding PTFE to other materials can be challenging. However, special surface treatments, such as etching or plasma treatment, can be used to improve the adhesion of PTFE to other surfaces. Additionally, modified PTFE formulations with improved bonding properties are available for specific applications. -
Q: How does PTFE compare to other fluoropolymers?
A: PTFE is one of the most well-known fluoropolymers, but there are other fluoropolymers with similar properties, such as FEP (fluorinated ethylene propylene), PFA (perfluoroalkoxy alkane), and ETFE (ethylene tetrafluoroethylene). Each of these fluoropolymers has unique properties and applications, and the choice of material depends on the specific requirements of the application, such as temperature resistance, chemical compatibility, and mechanical properties.
Conclusion
Polytetrafluoroethylene, or PTFE, is a remarkable synthetic fluoropolymer known for its unique combination of properties, including low friction, high-temperature resistance, chemical inertness, and non-stick characteristics. These properties have made PTFE an essential material in a wide range of industries and applications, from industrial seals and bearings to consumer products like non-stick cookware and waterproof clothing.
Since its accidental discovery in 1938, PTFE has undergone continuous development and improvement, with new formulations and processing methods enhancing its performance and expanding its potential applications. Research into PTFE and other fluoropolymers continues to push the boundaries of what is possible with these materials, addressing challenges such as sustainability, mechanical properties, and advanced manufacturing techniques.
As industries and technologies evolve, PTFE will likely continue to play a crucial role in enabling innovation and improving the performance of products and processes across various sectors. By understanding the properties, applications, and environmental considerations of PTFE, engineers, designers, and consumers can make informed decisions about how to best utilize this extraordinary material while minimizing its environmental impact.
Property | Description |
---|---|
Chemical formula | (C2F4)n |
Density | 2.13-2.19 g/cm³ |
Melting point | 327°C (620°F) |
Maximum service temperature | 260°C (500°F) |
Tensile strength | 20-35 MPa |
Elongation at break | 200-400% |
Coefficient of friction | 0.05-0.10 |
Dielectric constant | 2.0-2.1 |
Dielectric strength | 60-173 kV/mm |
Water absorption | <0.01% |
Table 1: Key properties of PTFE
Application | Examples |
---|---|
Industrial | Seals, gaskets, bearings, bushings, cable insulation, filtration membranes |
Consumer | Non-stick cookware, waterproof and breathable fabrics, dental floss, personal care products |
Medical | Vascular grafts, sutures, catheter coatings, orthopedic implants |
Table 2: Examples of PTFE applications in various sectors
No responses yet