Introduction to PCB LEDs
PCB LED stands for Printed Circuit Board Light Emitting Diode. It is a type of LED that is mounted directly onto a printed circuit board (PCB) instead of being housed in a separate package. PCB LEDs are widely used in various electronic devices, including automotive electronics, consumer appliances, and industrial equipment, due to their compact size, high efficiency, and cost-effectiveness.
What is a Printed Circuit Board (PCB)?
A printed circuit board (PCB) is a thin board made of fiberglass or composite material that is used to mechanically support and electrically connect electronic components using conductive pathways, tracks, or signal traces etched from copper sheets laminated onto a non-conductive substrate. PCBs are the foundation of modern electronic devices and are used in virtually every electronic product, from simple consumer gadgets to complex aerospace systems.
What is a Light Emitting Diode (LED)?
A light emitting diode (LED) is a semiconductor device that emits light when an electric current passes through it. LEDs are based on the electroluminescence principle, which is the phenomenon of a material emitting light when an electric current or an electric field is passed through it. LEDs are highly efficient, long-lasting, and environmentally friendly compared to traditional lighting sources such as incandescent bulbs and fluorescent lamps.
Advantages of PCB LEDs
PCB LEDs offer several advantages over traditional LED packages, making them an attractive choice for various applications. Some of the key advantages of PCB LEDs include:
Compact Size
PCB LEDs are significantly smaller than traditional LED packages, allowing for more compact and space-saving designs. This is particularly important in applications where space is limited, such as in portable devices, wearables, and automotive electronics.
High Efficiency
PCB LEDs are highly efficient compared to traditional lighting sources, converting a higher percentage of electrical energy into light. This high efficiency translates into lower power consumption and longer battery life in portable devices.
Cost-Effectiveness
PCB LEDs are generally more cost-effective than traditional LED packages due to their simpler design and manufacturing process. This makes them an attractive choice for high-volume applications where cost is a critical factor.
Improved Heat Dissipation
PCB LEDs are mounted directly onto the PCB, which acts as a heat sink, allowing for better heat dissipation compared to traditional LED packages. This improved heat dissipation helps to prolong the life of the LED and maintain its performance over time.
Enhanced Reliability
PCB LEDs are more reliable than traditional LED packages due to their simpler design and fewer interconnects. This reduced complexity minimizes the potential for failure and improves the overall reliability of the device.
Applications of PCB LEDs
PCB LEDs are used in a wide range of applications across various industries. Some of the most common applications of PCB LEDs include:
Automotive Electronics
PCB LEDs are widely used in automotive electronics, including interior lighting, dashboard indicators, and rear lighting. Their compact size, high efficiency, and improved reliability make them an ideal choice for automotive applications where space is limited and reliability is critical.
Consumer Appliances
PCB LEDs are used in various consumer appliances, such as home appliances, audio-visual equipment, and gaming devices. Their cost-effectiveness and compact size make them an attractive choice for high-volume consumer applications.
Industrial Equipment
PCB LEDs are used in industrial equipment, such as machine vision systems, inspection equipment, and process control systems. Their high efficiency and improved reliability make them suitable for demanding industrial environments.
Lighting Applications
PCB LEDs are increasingly being used in lighting applications, such as indoor and outdoor lighting, signage, and decorative lighting. Their high efficiency and long lifespan make them an environmentally friendly and cost-effective alternative to traditional lighting sources.
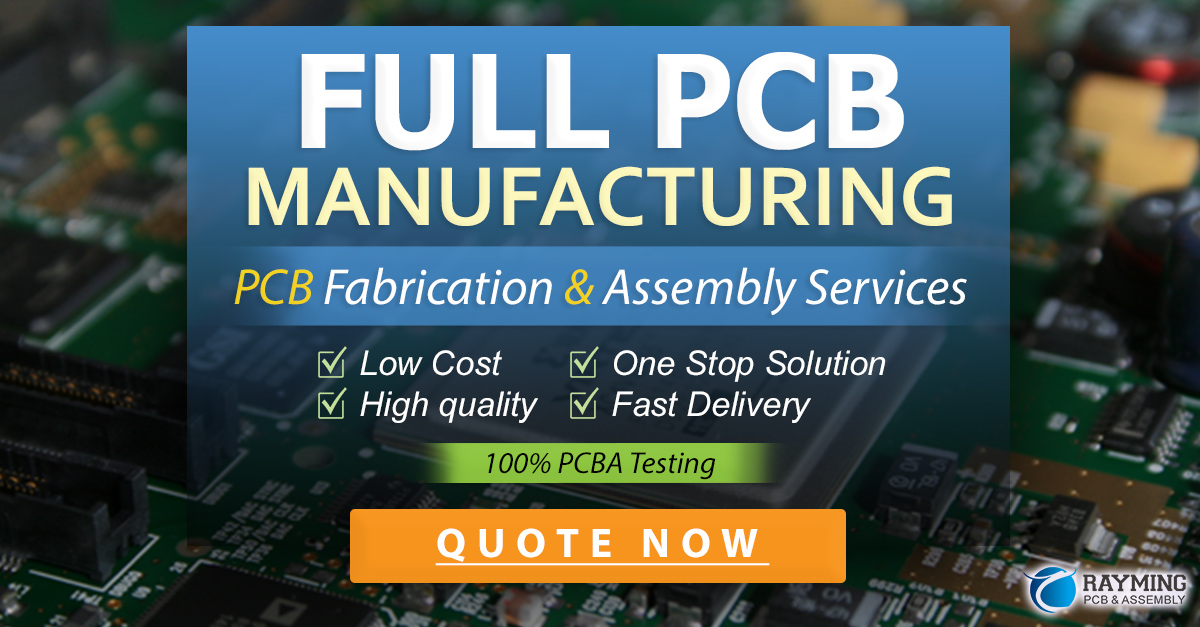
PCB LED Manufacturing Process
The manufacturing process for PCB LEDs involves several steps, from designing the PCB layout to mounting the LED onto the board. The main steps in the PCB LED manufacturing process are:
PCB Design and Fabrication
The first step in the PCB LED manufacturing process is designing the PCB layout and fabricating the board. The PCB layout is designed using specialized software, taking into account factors such as component placement, signal routing, and thermal management. Once the design is finalized, the PCB is fabricated using a multi-step process that includes etching, drilling, and plating.
LED Mounting
After the PCB is fabricated, the LED is mounted onto the board using a pick-and-place machine. The machine precisely places the LED onto the designated location on the PCB and secures it in place using a conductive adhesive or solder.
Wire Bonding
Once the LED is mounted onto the PCB, wire bonding is used to establish electrical connections between the LED and the PCB. This involves using thin gold or aluminum wires to connect the LED’s electrodes to the corresponding pads on the PCB.
Encapsulation
After wire bonding, the LED is encapsulated using a transparent epoxy resin. This protects the LED and the wire bonds from environmental factors such as moisture, dust, and mechanical stress.
Testing and Inspection
The final step in the PCB LED manufacturing process is testing and inspection. Each PCB LED undergoes rigorous quality control tests to ensure that it meets the required specifications for brightness, color, and electrical characteristics. Any defective units are identified and removed from the production line.
Challenges and Future Trends in PCB LED Technology
Despite the numerous advantages of PCB LEDs, there are still some challenges and limitations that need to be addressed. Some of the key challenges and future trends in PCB LED technology include:
Miniaturization
As electronic devices continue to shrink in size, there is a growing demand for even smaller and more compact PCB LEDs. This requires advances in PCB manufacturing technologies, such as high-density interconnect (HDI) PCBs and embedded component packaging.
Improved Thermal Management
While PCB LEDs offer better heat dissipation compared to traditional LED packages, thermal management remains a challenge, particularly in high-power applications. Future developments in PCB LED technology may focus on advanced thermal management techniques, such as the use of thermally conductive materials and active cooling systems.
Smart Lighting
The integration of PCB LEDs with sensors, wireless communication modules, and control systems is enabling the development of smart lighting solutions. These smart lighting systems can automatically adjust the brightness and color temperature based on ambient conditions, occupancy, and user preferences, leading to improved energy efficiency and user comfort.
Sustainable Manufacturing
As environmental concerns continue to grow, there is an increasing focus on sustainable manufacturing practices in the electronics industry. This includes the development of eco-friendly PCB materials, such as halogen-free and biodegradable substrates, as well as the adoption of green manufacturing processes that minimize waste and energy consumption.
Frequently Asked Questions (FAQ)
1. What is the difference between a PCB LED and a traditional LED package?
A PCB LED is mounted directly onto a printed circuit board, while a traditional LED package houses the LED in a separate package that is then soldered onto the PCB. PCB LEDs are generally smaller, more efficient, and more cost-effective than traditional LED packages.
2. What are the main advantages of using PCB LEDs?
The main advantages of using PCB LEDs include their compact size, high efficiency, cost-effectiveness, improved heat dissipation, and enhanced reliability compared to traditional LED packages.
3. In which industries are PCB LEDs commonly used?
PCB LEDs are commonly used in various industries, including automotive electronics, consumer appliances, industrial equipment, and lighting applications.
4. What is the role of wire bonding in the PCB LED manufacturing process?
Wire bonding is used to establish electrical connections between the LED and the PCB. Thin gold or aluminum wires are used to connect the LED’s electrodes to the corresponding pads on the PCB.
5. What are some of the future trends in PCB LED technology?
Some of the future trends in PCB LED technology include miniaturization, improved thermal management, smart lighting solutions, and sustainable manufacturing practices.
Conclusion
PCB LEDs are a compact, efficient, and cost-effective alternative to traditional LED packages, offering numerous advantages for various applications across industries. As electronic devices continue to evolve and become more complex, PCB LED technology will play an increasingly important role in enabling innovative and sustainable lighting solutions. By understanding the basics of PCB LEDs, their manufacturing process, and the challenges and trends shaping the industry, engineers and designers can make informed decisions when incorporating these components into their projects.
No responses yet