What is FR4?
FR4 is a composite material made of woven fiberglass cloth with an epoxy resin binder. The “FR” in FR4 stands for “Flame Retardant,” indicating that the material has been treated to resist the spread of flames in case of a fire. The “4” represents the woven glass reinforcement used in the material.
Composition of FR4
FR4 is composed of two main components:
- Woven fiberglass cloth
- Epoxy resin binder
The fiberglass cloth is made of fine glass fibers woven together to form a fabric. This fabric is then impregnated with an epoxy resin, which is a thermosetting polymer. The combination of these two materials creates a strong, durable, and electrically insulating substrate for PCBs.
Characteristics of FR4
FR4 exhibits several desirable properties that make it an ideal choice for PCB manufacturing:
- High dielectric strength
- Good mechanical strength
- Excellent dimensional stability
- Resistance to moisture and chemicals
- Flame retardancy
These characteristics ensure that FR4-based PCBs can withstand the rigors of various applications and environments.
Manufacturing Process of FR4 PCBs
The manufacturing process of FR4 PCBs involves several steps:
- Preparing the substrate
- Applying the copper layer
- Etching the circuit pattern
- Applying solder mask and silkscreen
- Drilling and plating holes
- Cutting and finishing
Preparing the Substrate
The FR4 substrate is prepared by cutting the material to the desired size and shape. The surfaces are then cleaned and treated to ensure proper adhesion of the copper layer.
Applying the Copper Layer
A thin layer of copper is applied to one or both sides of the FR4 substrate using a process called electroless plating. This layer serves as the conductive pathway for the electrical signals in the PCB.
Etching the Circuit Pattern
The desired circuit pattern is transferred onto the copper layer using a photoresist and exposure to UV light. The unwanted copper is then etched away using a chemical solution, leaving behind the circuit traces.
Applying Solder Mask and Silkscreen
A solder mask, typically green in color, is applied over the copper traces to protect them from oxidation and prevent short circuits. A silkscreen layer is then added to provide labels, logos, and other markings on the PCB.
Drilling and Plating Holes
Holes are drilled through the PCB to accommodate components and connectors. These holes are then plated with copper to create electrical connections between layers.
Cutting and Finishing
The PCB panel is cut into individual boards, and any remaining rough edges are smoothed. The boards are then inspected and tested to ensure they meet the required specifications.
Applications of FR4 PCBs
FR4 PCBs find applications in a wide range of industries due to their versatility and reliability:
- Consumer electronics
- Telecommunications
- Automotive
- Medical devices
- Aerospace and defense
- Industrial equipment
Consumer Electronics
FR4 PCBs are extensively used in consumer electronic devices such as smartphones, laptops, televisions, and home appliances. The material’s excellent electrical insulation properties and ability to accommodate high-density layouts make it ideal for these applications.
Telecommunications
In the telecommunications industry, FR4 PCBs are used in routers, switches, and other networking equipment. The material’s stability and reliability ensure that these devices can operate continuously without failure.
Automotive
FR4 PCBs are used in various automotive applications, including engine control units, infotainment systems, and driver assistance systems. The material’s resistance to high temperatures and vibrations makes it suitable for the harsh environment inside vehicles.
Medical Devices
Medical devices such as pacemakers, insulin pumps, and imaging equipment rely on FR4 PCBs for their critical functions. The material’s biocompatibility and ability to meet strict regulatory requirements make it a preferred choice in this industry.
Aerospace and Defense
FR4 PCBs are used in aerospace and defense applications such as avionics, radar systems, and communication equipment. The material’s ability to withstand extreme conditions and provide reliable performance is essential in these mission-critical applications.
Industrial Equipment
Industrial equipment such as power supplies, motor drives, and process control systems use FR4 PCBs for their control and monitoring functions. The material’s durability and resistance to harsh environments ensure long-term reliability.
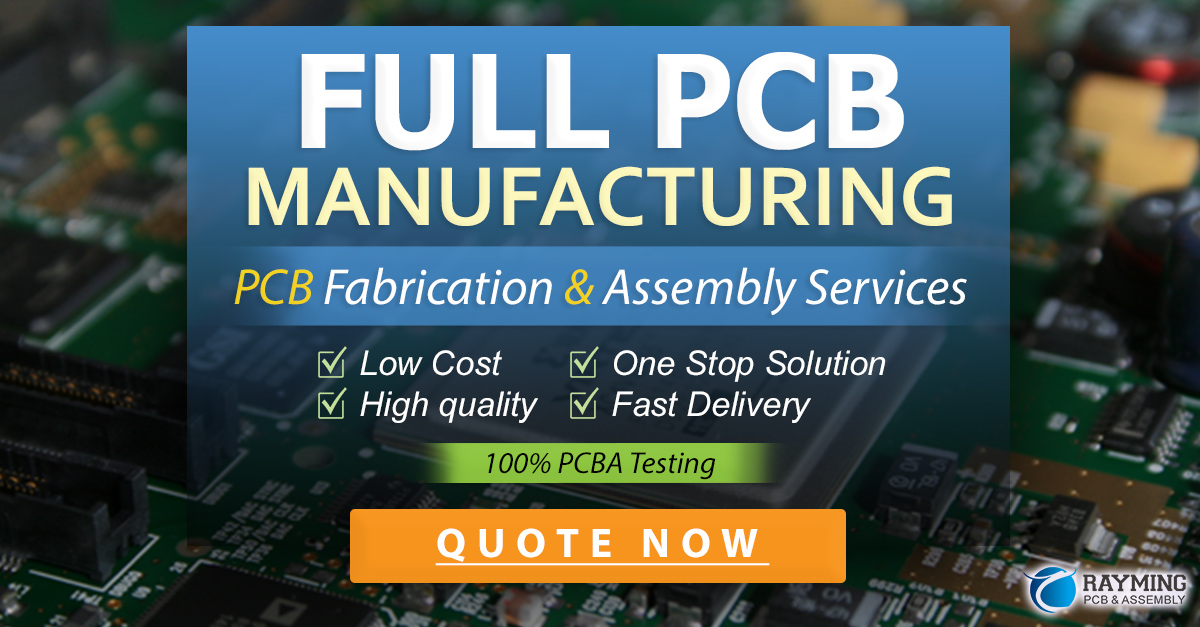
Advantages of FR4 PCBs
FR4 PCBs offer several advantages over other PCB materials:
- Cost-effectiveness
- Wide availability
- Excellent electrical properties
- Good mechanical strength
- Ease of fabrication
Cost-effectiveness
FR4 is a relatively inexpensive material compared to other high-performance PCB substrates. This cost-effectiveness makes it an attractive choice for a wide range of applications.
Wide Availability
FR4 is widely available from numerous manufacturers worldwide, ensuring a stable supply chain for PCB production.
Excellent Electrical Properties
FR4 has a high dielectric strength, which enables it to insulate electrical signals effectively. It also has a low Dielectric constant, which minimizes signal loss and cross-talk between traces.
Good Mechanical Strength
The combination of woven fiberglass and epoxy resin gives FR4 good mechanical strength and dimensional stability. This strength allows FR4 PCBs to withstand physical stresses during assembly and operation.
Ease of Fabrication
FR4 is easy to fabricate using standard PCB manufacturing processes. The material is compatible with a wide range of drilling, routing, and plating techniques, making it suitable for both prototype and high-volume production.
Disadvantages of FR4 PCBs
Despite its many advantages, FR4 also has some limitations:
- Limited high-frequency performance
- Higher dielectric loss compared to some other materials
- Susceptibility to moisture absorption
Limited High-Frequency Performance
FR4’s dielectric constant and loss tangent increase with frequency, which can limit its performance in high-frequency applications such as RF and microwave circuits.
Higher Dielectric Loss Compared to Some Other Materials
While FR4 has a relatively low dielectric loss, some other PCB Materials, such as Rogers laminates, offer even lower loss for demanding high-frequency applications.
Susceptibility to Moisture Absorption
FR4 can absorb moisture from the environment, which can lead to changes in its dielectric properties and dimensions over time. This moisture absorption can be mitigated through proper storage and handling of the PCBs.
Variants of FR4
There are several variants of FR4 available, each with slightly different properties to suit specific applications:
- High Tg FR4
- Halogen-free FR4
- Low-loss FR4
High Tg FR4
High Tg (glass transition temperature) FR4 is designed to withstand higher temperatures than standard FR4. This variant is useful in applications where the PCB may be exposed to elevated temperatures during assembly or operation.
Halogen-free FR4
Halogen-free FR4 is formulated without the use of halogenated flame retardants, which can release toxic fumes during combustion. This variant is preferred in applications where environmental and safety concerns are paramount.
Low-loss FR4
Low-loss FR4 is designed to have a lower dielectric loss than standard FR4, making it more suitable for high-frequency applications. However, it still has limitations compared to specialized high-frequency materials.
FR4 vs. Other PCB Materials
When deciding on a PCB material, it’s essential to consider the specific requirements of the application. Here’s a comparison of FR4 with some other common PCB materials:
Material | Advantages | Disadvantages |
---|---|---|
FR4 | Cost-effective, widely available, good electrical and mechanical properties | Limited high-frequency performance, susceptible to moisture absorption |
Rogers laminates | Excellent high-frequency performance, low dielectric loss | More expensive, less widely available |
Polyimide | High temperature resistance, good flexibility | More expensive, harder to process |
Aluminum | Excellent thermal conductivity, good mechanical strength | Limited electrical insulation, higher cost |
Frequently Asked Questions (FAQs)
- What does FR stand for in FR4?
-
FR stands for “Flame Retardant,” indicating that the material has been treated to resist the spread of flames in case of a fire.
-
What is the difference between FR4 and G10?
-
FR4 and G10 are similar materials, but FR4 has better flame retardancy due to the addition of flame-retardant chemicals in the epoxy resin.
-
Can FR4 be used for high-frequency applications?
-
While FR4 can be used in some high-frequency applications, its performance is limited compared to specialized materials like Rogers laminates. The dielectric constant and loss tangent of FR4 increase with frequency, which can lead to signal integrity issues.
-
Is FR4 suitable for flexible PCBs?
-
No, FR4 is not suitable for flexible PCBs due to its rigid nature. Flexible PCBs typically use materials like polyimide or polyester.
-
How does moisture affect FR4 PCBs?
- Moisture absorption can cause changes in the dielectric properties and dimensions of FR4 PCBs over time. This can be mitigated through proper storage and handling, such as keeping the PCBs in moisture-barrier bags with desiccants.
Conclusion
FR4 is a versatile and widely used PCB material that offers a balanced combination of electrical, mechanical, and thermal properties. Its cost-effectiveness, wide availability, and ease of fabrication make it an attractive choice for a broad range of applications, from consumer electronics to aerospace and defense.
However, it’s essential to understand the limitations of FR4, particularly in high-frequency applications, and consider alternative materials when necessary. By carefully selecting the appropriate PCB material for each project, designers and engineers can ensure optimal performance, reliability, and cost-efficiency in their electronic devices and systems.
No responses yet