What is FR4?
FR4 is a composite material made from woven fiberglass cloth impregnated with an epoxy resin. The term “FR” stands for “Flame Retardant,” while the “4” denotes the specific grade of the material. FR4 is known for its excellent mechanical, thermal, and electrical properties, making it an ideal choice for PCB substrates.
Composition of FR4
The key components of FR4 are:
-
Fiberglass cloth: This woven fabric provides the structural reinforcement for the laminate. The fiberglass is typically made from electrical-grade glass, which offers high tensile strength and dimensional stability.
-
Epoxy resin: The fiberglass cloth is impregnated with a flame-retardant epoxy resin. This resin binds the fiberglass layers together and provides the necessary electrical insulation and heat resistance.
Properties of FR4
FR4 exhibits several desirable properties that make it well-suited for use in PCBs:
-
High dielectric strength: FR4 has excellent insulating properties, which helps prevent electrical leakage and short circuits between conductive layers in a PCB.
-
Flame retardancy: The epoxy resin used in FR4 is designed to be flame-retardant, reducing the risk of fire in electronic devices.
-
Mechanical strength: The combination of fiberglass and epoxy resin gives FR4 a high strength-to-weight ratio, making it resistant to bending, twisting, and impact.
-
Thermal stability: FR4 maintains its mechanical and electrical properties over a wide temperature range, typically from -50°C to +130°C.
-
Moisture resistance: FR4 has low moisture absorption, which helps maintain its dimensional stability and prevents warping or delamination in humid environments.
Role of FR4 in Circuit Boards
FR4 plays a vital role in the construction and functionality of circuit boards. Its primary functions include:
Insulation and Separation
One of the most important roles of FR4 in a PCB is to provide electrical insulation between conductive layers. The insulating properties of FR4 prevent short circuits and ensure that electrical signals travel only along the intended paths. FR4 also separates the conductive layers, such as copper traces and planes, allowing for the creation of complex, multi-layer PCB designs.
Structural Support
FR4 serves as the backbone of a circuit board, providing the necessary structural support to hold all the components in place. The rigidity and strength of FR4 help prevent the PCB from flexing or breaking under stress, which is particularly important in applications subjected to vibration or mechanical shock.
Heat Dissipation
While FR4 is not a primary heat dissipator, it does contribute to the overall thermal management of a PCB. The epoxy resin in FR4 has a relatively low thermal conductivity, which helps to slow the spread of heat from hot spots on the board. This property allows for more even heat distribution and prevents localized overheating, which can damage components or cause premature failure.
Manufacturing Process
The manufacture of FR4 PCBs involves several key steps:
-
Lamination: Multiple layers of fiberglass cloth are impregnated with epoxy resin and sandwiched between copper foils. This stack is then subjected to high temperature and pressure, causing the resin to flow and bond the layers together.
-
Drilling: Holes are drilled through the laminated board to accommodate component leads and vias, which connect different layers of the PCB.
-
Plating: The drilled holes are plated with copper to create conductive pathways between layers.
-
Etching: Unwanted copper is removed from the board using a chemical etching process, leaving behind the desired circuit patterns.
-
Solder mask and silkscreen: A protective solder mask is applied to the board, and a silkscreen layer is added to provide component labels and other markings.
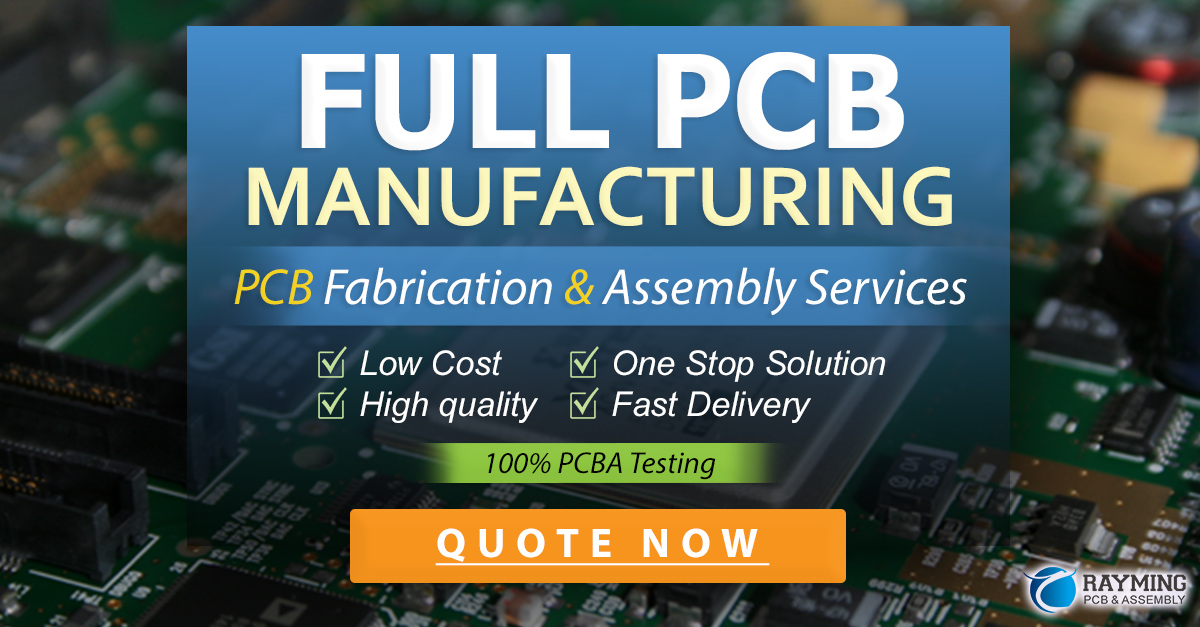
Applications of FR4 PCBs
FR4 PCBs are used in a wide range of electronic devices and industries, including:
-
Consumer electronics: Smartphones, laptops, televisions, and home appliances all rely on FR4 PCBs for their internal circuitry.
-
Automotive electronics: FR4 is used in various automotive applications, such as engine control units, infotainment systems, and sensors.
-
Industrial equipment: FR4 PCBs are found in industrial control systems, power supplies, and automation equipment.
-
Medical devices: Many medical devices, such as patient monitors, imaging equipment, and diagnostic tools, use FR4 PCBs for their reliability and performance.
-
Aerospace and defense: FR4 is used in avionics, satellite systems, and military communications equipment, where high reliability and durability are essential.
Advantages of FR4 over Other PCB Materials
FR4 has several advantages over other PCB substrate materials, such as phenolic paper or CEM-1:
-
Better mechanical properties: FR4 offers higher strength, stiffness, and dimensional stability compared to other materials.
-
Superior electrical insulation: FR4 has a higher dielectric strength and lower dielectric loss, making it better suited for high-frequency applications.
-
Improved thermal stability: FR4 maintains its properties over a wider temperature range, making it more reliable in demanding environments.
-
Enhanced moisture resistance: FR4 is less susceptible to moisture absorption, which reduces the risk of delamination and warping.
Limitations of FR4
Despite its many advantages, FR4 does have some limitations:
-
Limited high-frequency performance: While FR4 is suitable for most applications, its dielectric loss increases at higher frequencies, making it less suitable for very high-frequency designs.
-
Higher cost: FR4 is more expensive than some other PCB materials, such as phenolic paper or CEM-1.
-
Difficulty in machining: The hardness and abrasiveness of FR4 can make it more challenging to drill and cut compared to softer materials.
Future Developments in FR4 Technology
As the demand for high-performance electronics continues to grow, there is ongoing research and development to improve FR4 and create new variations of the material. Some areas of focus include:
-
High-speed materials: Researchers are working on developing FR4 variants with lower dielectric loss and better high-frequency performance.
-
Improved thermal management: New FR4 formulations are being developed to enhance thermal conductivity and heat dissipation.
-
Environmentally friendly materials: There is a growing interest in developing FR4 alternatives that are more eco-friendly and recyclable.
FAQ
-
Q: Is FR4 the only material used for PCBs?
A: No, while FR4 is the most common material used for PCBs, other materials such as polyimide, PTFE, and ceramics are also used in specialized applications. -
Q: Can FR4 PCBs be used in high-temperature environments?
A: Yes, FR4 is rated for use in temperatures ranging from -50°C to +130°C. However, for extreme high-temperature applications, other materials like polyimide may be more suitable. -
Q: Are FR4 PCBs waterproof?
A: FR4 itself is not waterproof, but PCBs made from FR4 can be made water-resistant by applying conformal coatings or using other waterproofing techniques. -
Q: How does the thickness of FR4 affect PCB performance?
A: Thicker FR4 boards offer better mechanical strength and thermal stability, but they can be more difficult to manufacture and may have higher costs. Thinner boards are lighter and more flexible but may be more susceptible to warping or damage. -
Q: Can FR4 PCBs be recycled?
A: Recycling FR4 PCBs can be challenging due to the composite nature of the material. However, some specialized recycling facilities can separate the fiberglass and metal components for recycling.
Conclusion
FR4 is a vital material in the production of modern circuit boards, offering a combination of excellent mechanical, thermal, and electrical properties. Its role in providing insulation, structural support, and heat dissipation makes it an indispensable component in a wide range of electronic devices and industries. As technology continues to advance, researchers and manufacturers will continue to develop new variations of FR4 and other PCB materials to meet the ever-growing demands of the electronics industry.
Property | FR4 | Phenolic Paper | CEM-1 |
---|---|---|---|
Dielectric Strength | High | Low | Medium |
Mechanical Strength | High | Low | Medium |
Thermal Stability | High | Low | Medium |
Moisture Resistance | High | Low | Medium |
Cost | High | Low | Medium |
This table compares the properties of FR4 with two other common PCB substrate materials, phenolic paper and CEM-1. FR4 exhibits superior performance in dielectric strength, mechanical strength, thermal stability, and moisture resistance, but comes at a higher cost compared to the other materials.
No responses yet