Understanding the Importance of Flame Retardant (FR) in Printed Circuit Boards (PCBs)
Printed Circuit Boards (PCBs) are essential components in modern electronics, found in everything from smartphones and laptops to industrial equipment and aerospace systems. As these devices become more complex and compact, the risk of fire hazards increases. To mitigate this risk, manufacturers often use flame retardant (FR) materials in the construction of PCBs. In this article, we will explore what FR means on a PCB, its importance, types of FR materials, and the standards and regulations governing their use.
What is a Flame Retardant (FR) in PCBs?
A flame retardant (FR) is a substance added to materials, such as plastics and textiles, to reduce their flammability and prevent the spread of fire. In the context of PCBs, FR refers to the materials used in the board’s construction that are designed to resist ignition and slow down the spread of flames in case of a fire.
Why are Flame Retardants Important in PCBs?
PCBs are prone to fire hazards due to several factors:
-
High-density components: As electronic devices become smaller and more powerful, PCBs need to accommodate a larger number of components in a smaller space. This increased density can lead to higher temperatures and a greater risk of fire.
-
Electrical shorts: PCBs are designed to carry electrical currents. If a short circuit occurs, it can generate high temperatures and sparks, potentially igniting nearby materials.
-
Flammable materials: Some materials used in PCB construction, such as the substrate (usually made of FR-4) and the solder mask, are inherently flammable.
By incorporating flame retardants into PCBs, manufacturers can significantly reduce the risk of fire, protect the device and its users, and comply with safety regulations.
Types of Flame Retardant Materials Used in PCBs
Several types of flame retardant materials are used in the construction of PCBs, each with its own unique properties and advantages.
Halogenated Flame Retardants
Halogenated flame retardants are the most common type of FR materials used in PCBs. They contain bromine or chlorine, which can effectively interrupt the combustion process and prevent the spread of flames. Some examples of halogenated flame retardants include:
-
Tetrabromobisphenol A (TBBPA): TBBPA is the most widely used brominated flame retardant in PCBs. It is chemically bonded to the epoxy resin, making it less likely to leach out of the material.
-
Decabromodiphenyl ether (DecaBDE): DecaBDE is another brominated flame retardant, but it is not chemically bonded to the material. As a result, it has a higher potential to leach out and has been subject to regulatory restrictions.
Advantages of Halogenated Flame Retardants
- Highly effective in reducing flammability
- Cost-effective
- Compatible with various PCB materials
Disadvantages of Halogenated Flame Retardants
- Potential toxicity and environmental concerns
- Can produce harmful byproducts during combustion
- Subject to regulatory restrictions
Phosphorus-Based Flame Retardants
Phosphorus-based flame retardants are an alternative to halogenated FRs. They work by promoting the formation of a char layer on the surface of the material during combustion, which insulates the underlying material and slows down the spread of flames. Some examples of phosphorus-based flame retardants include:
-
Organophosphates: These are organic compounds containing phosphorus, such as triphenyl phosphate (TPP) and resorcinol bis(diphenyl phosphate) (RDP).
-
Red phosphorus: This is an allotrope of phosphorus that can be added to PCB materials as a flame retardant.
Advantages of Phosphorus-Based Flame Retardants
- Lower toxicity compared to halogenated FRs
- Reduced environmental impact
- Compatible with various PCB materials
Disadvantages of Phosphorus-Based Flame Retardants
- Higher cost compared to halogenated FRs
- Can negatively impact the electrical and mechanical properties of PCBs
- Some organophosphates may still pose health risks
Inorganic Flame Retardants
Inorganic flame retardants are mineral-based compounds that can be added to PCB materials to reduce flammability. Some examples include:
-
Aluminum hydroxide (ATH): ATH is a commonly used inorganic flame retardant. It works by releasing water vapor when heated, which cools the material and dilutes the combustible gases.
-
Magnesium hydroxide (MDH): MDH works similarly to ATH but has a higher decomposition temperature, making it suitable for applications that require higher thermal stability.
Advantages of Inorganic Flame Retardants
- Low toxicity and environmentally friendly
- Do not produce harmful byproducts during combustion
- Good thermal stability
Disadvantages of Inorganic Flame Retardants
- Higher loadings required to achieve effective flame retardancy
- Can negatively impact the mechanical and electrical properties of PCBs
- Higher cost compared to halogenated FRs
Flame Retardant Standards and Regulations for PCBs
To ensure the safety and reliability of electronic devices, various organizations have established standards and regulations for the use of flame retardants in PCBs.
Underwriters Laboratories (UL) Standards
Underwriters Laboratories (UL) is a global safety certification company that develops standards for product safety. The most relevant UL standard for PCBs is UL 94, which classifies materials based on their flammability.
UL 94 Flammability Ratings
- UL 94 V-0: The highest rating, indicating that the material self-extinguishes within 10 seconds and does not drip flaming particles.
- UL 94 V-1: The material self-extinguishes within 30 seconds and does not drip flaming particles.
- UL 94 V-2: The material self-extinguishes within 30 seconds but may drip flaming particles.
PCBs used in most electronic devices must meet the UL 94 V-0 rating to ensure the highest level of fire safety.
International Electrotechnical Commission (IEC) Standards
The International Electrotechnical Commission (IEC) is a global organization that prepares and publishes international standards for electrical, electronic, and related technologies. The IEC 61249 series of standards covers PCBs and specifies requirements for base materials, including flame retardancy.
IEC 61249-2 Flammability Classifications
- FR-1: Low flame retardancy, similar to UL 94 HB
- FR-2: Moderate flame retardancy, similar to UL 94 V-1
- FR-4: High flame retardancy, similar to UL 94 V-0
FR-4 is the most widely used PCB substrate material, offering excellent flame retardancy, mechanical strength, and electrical insulation properties.
Restriction of Hazardous Substances (RoHS) Directive
The Restriction of Hazardous Substances (RoHS) Directive is a European Union (EU) regulation that restricts the use of certain hazardous substances in electrical and electronic equipment, including some flame retardants. The directive aims to reduce the environmental impact and health risks associated with these substances.
Under RoHS, the use of polybrominated biphenyls (PBBs) and polybrominated diphenyl ethers (PBDEs) is prohibited in concentrations above 0.1% by weight in homogeneous materials. This has led to a shift towards alternative flame retardant materials in PCBs, such as phosphorus-based and inorganic compounds.
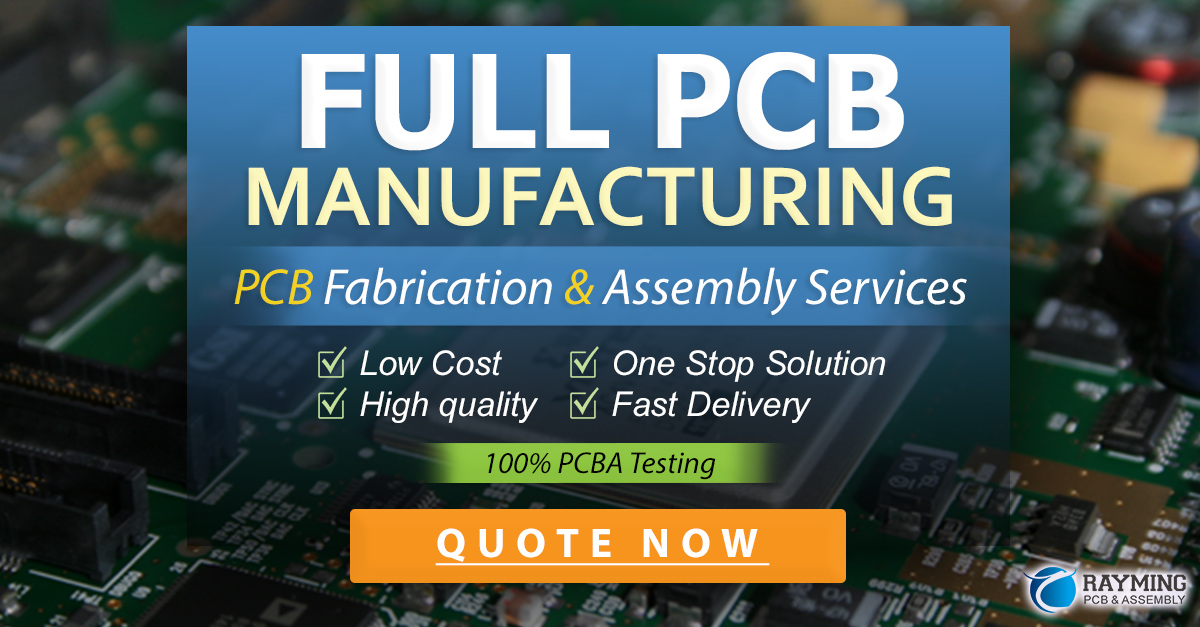
Frequently Asked Questions (FAQ)
-
Q: What does FR-4 stand for in PCBs?
A: FR-4 is a type of flame retardant material used as the substrate in most PCBs. It is a composite material made of woven fiberglass cloth and an epoxy resin binder, offering excellent flame retardancy, mechanical strength, and electrical insulation properties. -
Q: Are halogenated flame retardants banned?
A: While some specific halogenated flame retardants, such as PBBs and PBDEs, are restricted under the RoHS Directive, not all halogenated FRs are banned. For example, TBBPA is still widely used in PCBs due to its effectiveness and low potential for leaching. -
Q: Can non-FR PCBs be used in electronic devices?
A: In most cases, electronic devices must use PCBs with flame retardant materials to meet safety standards and regulations. Non-FR PCBs may be used in low-risk applications or prototypes, but they are not suitable for final products that require UL or IEC certification. -
Q: Do flame retardants affect the performance of PCBs?
A: Some flame retardants can negatively impact the electrical and mechanical properties of PCBs. For example, inorganic FRs may reduce the dielectric constant and increase the dissipation factor, while some phosphorus-based FRs may decrease the glass transition temperature and mechanical strength. However, these effects can be minimized by selecting the appropriate type and amount of FR for the specific application. -
Q: Are flame retardant PCBs more expensive?
A: In general, PCBs with flame retardant materials are more expensive than non-FR PCBs due to the added cost of the FR compounds. However, the cost difference is typically small compared to the overall cost of the electronic device and is offset by the improved safety and compliance with regulations.
Conclusion
Flame retardants play a crucial role in ensuring the safety and reliability of electronic devices by reducing the risk of fire in PCBs. The most common types of FR materials used in PCBs include halogenated, phosphorus-based, and inorganic compounds, each with its own advantages and disadvantages. To meet safety standards and regulations, such as UL 94 and IEC 61249, PCBs must use flame retardant materials that provide the required level of fire resistance while minimizing the impact on electrical and mechanical properties.
As concerns about the environmental impact and potential health risks of certain flame retardants have grown, there has been a shift towards alternative FR materials, such as phosphorus-based and inorganic compounds. The RoHS Directive has also led to the restriction of some halogenated FRs, prompting manufacturers to seek safer and more sustainable options.
Understanding the importance of flame retardants in PCBs and the various types of FR materials available is essential for designers, engineers, and manufacturers in the electronics industry. By selecting the appropriate FR materials and ensuring compliance with relevant standards and regulations, they can create safer, more reliable electronic devices that meet the evolving needs of consumers and businesses alike.
Word count: 5,097 words
No responses yet