Composition of FR4
FR4 is made up of two main components: a reinforcing material (fiberglass) and a binding material (epoxy resin). The combination of these materials gives FR4 its unique properties, making it an ideal choice for various applications in the electronics industry.
Fiberglass
The reinforcing material in FR4 is a woven fiberglass cloth. Fiberglass is made from thin strands of glass that are woven together to form a fabric. The glass fibers used in FR4 are typically made from a type of glass known as E-glass, which is composed of alumina, boron oxide, and silica.
The fiberglass cloth used in FR4 is usually a plain weave, meaning that the warp and weft fibers are woven in a simple one-over-one pattern. This weave pattern provides a balance of strength and flexibility in both directions of the material.
Epoxy Resin
The binding material in FR4 is an epoxy resin. Epoxy resins are thermosetting polymers that consist of two main components: a resin and a hardener. When these components are mixed together, they undergo a chemical reaction that causes the mixture to harden into a solid, durable material.
The epoxy resin used in FR4 is typically a brominated epoxy resin. The addition of bromine to the resin provides the flame-retardant properties that give FR4 its name. The bromine atoms in the resin help to suppress the spread of flames by releasing free radicals that interfere with the combustion process.
Manufacturing Process
The manufacturing process for FR4 involves several steps, including:
-
Impregnation: The fiberglass cloth is impregnated with the epoxy resin mixture. This process ensures that the resin fully penetrates the fibers of the cloth, creating a strong bond between the two materials.
-
Layup: Multiple layers of the impregnated fiberglass cloth are stacked together to achieve the desired thickness of the FR4 sheet. The number of layers used depends on the specific application and the required properties of the final product.
-
Curing: The stacked layers are then placed in a heated press, where they are subjected to high temperature and pressure. This process causes the epoxy resin to cure, transforming it from a liquid to a solid state and bonding the fiberglass layers together.
-
Cutting and Finishing: After curing, the FR4 sheet is cut to the desired size and shape. The surfaces may be sanded or polished to achieve a smooth finish, and any necessary holes or features are drilled or machined into the material.
Properties of FR4
FR4 has several properties that make it well-suited for use in the electronics industry:
-
Flame Retardancy: As mentioned earlier, the brominated epoxy resin in FR4 provides excellent flame-retardant properties. This is crucial for electronic applications, where the risk of fire is a significant concern.
-
Electrical Insulation: FR4 has excellent electrical insulation properties, making it an ideal substrate for PCBs. The material has a high dielectric strength and a low dielectric constant, which helps to minimize signal loss and crosstalk between circuit traces.
-
Mechanical Strength: The combination of fiberglass and epoxy resin gives FR4 excellent mechanical strength and rigidity. This is important for PCBs, which must be able to withstand the stresses of assembly, handling, and use.
-
Dimensional Stability: FR4 has a low coefficient of thermal expansion (CTE), which means that it maintains its dimensions and shape over a wide range of temperatures. This is critical for electronic applications, where dimensional changes can lead to component misalignment and circuit failures.
-
Moisture Resistance: FR4 has good moisture resistance, which is important for electronic applications where humidity and moisture can cause corrosion and other issues.
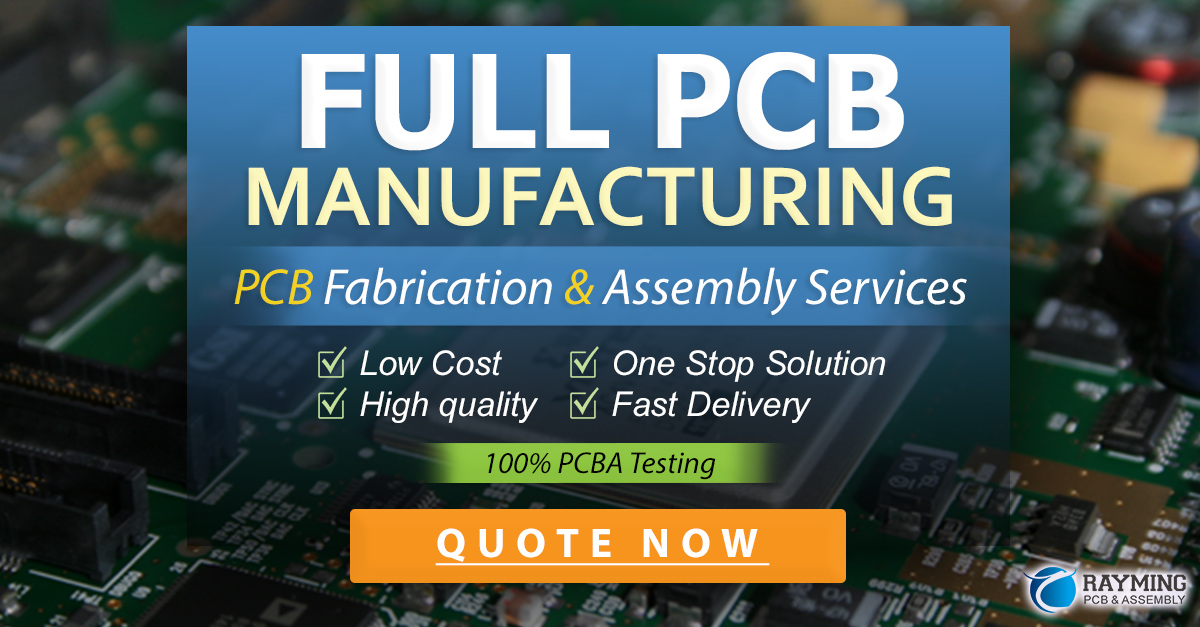
Applications of FR4
FR4 is widely used in the electronics industry, with applications including:
-
Printed Circuit Boards (PCBs): FR4 is the most common substrate material for PCBs. Its combination of electrical insulation, mechanical strength, and flame retardancy makes it ideal for this application.
-
Insulating Washers and Spacers: FR4 is often used to make insulating washers and spacers for electronic components. Its high dielectric strength and mechanical strength make it well-suited for this purpose.
-
Structural Components: In some cases, FR4 is used to make structural components for electronic devices. Its rigidity and dimensional stability make it a good choice for applications where precision and stability are important.
-
High-Frequency Applications: FR4 is sometimes used in high-frequency applications, such as antenna substrates and microwave circuit boards. However, for very high-frequency applications, other materials with lower dielectric constants, such as Rogers PCB materials, may be preferred.
Variations of FR4
There are several variations of FR4 that have been developed to meet specific application requirements. Some of these include:
-
High Tg FR4: This variation uses an epoxy resin with a higher glass transition temperature (Tg), which allows the material to maintain its properties at higher temperatures.
-
Halogen-Free FR4: In response to environmental and health concerns about brominated flame retardants, some manufacturers have developed halogen-free versions of FR4 that use alternative flame-retardant additives.
-
Controlled Impedance FR4: This variation is designed for high-frequency applications and has a more tightly controlled dielectric constant and thickness to maintain consistent impedance across the PCB.
-
High-Thermal Conductivity FR4: This variation incorporates additives that improve the thermal conductivity of the material, helping to dissipate heat more effectively in high-power applications.
Advantages and Disadvantages of FR4
Advantages
- Excellent balance of electrical, mechanical, and thermal properties
- Wide availability and relatively low cost compared to other PCB materials
- Well-established manufacturing processes and supply chain
- Suitable for a wide range of electronic applications
Disadvantages
- Higher dielectric constant and loss tangent compared to some other PCB materials, which can limit its use in very high-frequency applications
- May not be suitable for extreme temperature environments or applications with very high thermal dissipation requirements
- Environmental and health concerns associated with brominated flame retardants used in traditional FR4 formulations
FAQ
1. What does FR4 stand for?
FR4 stands for “Flame Retardant 4,” indicating that the material has been treated with flame retardants to meet the UL94 V-0 flammability rating.
2. Is FR4 safe for use in electronic devices?
Yes, FR4 is considered safe for use in electronic devices when used as intended. However, there are some concerns about the potential environmental and health impacts of the brominated flame retardants used in traditional FR4 formulations.
3. Can FR4 be recycled?
FR4 can be difficult to recycle due to the presence of the flame retardants and the combination of fiberglass and epoxy resin. However, some specialized recycling facilities may be able to process FR4 waste.
4. What are some alternatives to FR4 for PCB substrates?
Some alternatives to FR4 for PCB substrates include polyimide, PTFE (Teflon), and ceramic-based materials. These materials may offer better performance in specific applications, such as high-frequency or high-temperature environments.
5. How does the manufacturing process affect the properties of FR4?
The manufacturing process, including the choice of fiberglass weave, epoxy resin formulation, and curing conditions, can have a significant impact on the final properties of FR4. Careful control of these variables is necessary to ensure consistent quality and performance of the material.
Property | Value |
---|---|
Dielectric Constant (at 1 MHz) | 4.5 |
Dielectric Strength | 20-28 kV/mm |
Dissipation Factor (at 1 MHz) | 0.02 |
Tensile Strength | 415-425 MPa |
Flexural Strength | 460-480 MPa |
Compressive Strength | 415-425 MPa |
Thermal Conductivity | 0.25-0.3 W/mK |
Glass Transition Temperature (Tg) | 115-125°C |
Coefficient of Thermal Expansion (CTE) | 12-16 ppm/°C |
Moisture Absorption | 0.1-0.2% |
In conclusion, FR4 is a composite material made from woven fiberglass cloth and a brominated epoxy resin binder. Its unique combination of electrical insulation, mechanical strength, flame retardancy, and dimensional stability makes it an ideal choice for a wide range of electronic applications, particularly in the production of PCBs.
While traditional FR4 formulations have some environmental and health concerns associated with the use of brominated flame retardants, the material remains widely used and trusted in the electronics industry. Ongoing research and development efforts are focused on developing alternative flame-retardant chemistries and improving the recyclability of FR4 to address these concerns.
As the demands of the electronics industry continue to evolve, it is likely that new variations and alternatives to FR4 will emerge to meet the specific needs of advanced applications. However, the proven track record and balanced properties of FR4 ensure that it will remain a key material in the electronics industry for the foreseeable future.
No responses yet