Excellent Electrical Insulation Properties
One of the primary benefits of FR4 is its excellent electrical insulation properties. The material has a high Dielectric Strength, which means it can withstand high voltages without breaking down or allowing current to pass through. This makes FR4 an ideal choice for PCBs, as it prevents short circuits and ensures the proper functioning of electronic components.
The Dielectric constant of FR4 typically ranges from 4.2 to 4.6 at 1 MHz, depending on the specific composition and manufacturing process. This relatively low dielectric constant helps to minimize signal loss and maintain signal integrity in high-frequency applications.
Property | Value Range |
---|---|
Dielectric Strength | 45-65 kV/mm |
Dielectric Constant | 4.2-4.6 |
Dissipation Factor (1 MHz) | 0.02-0.03 |
Mechanical Strength and Durability
FR4 is known for its impressive mechanical strength and durability. The glass fiber reinforcement within the epoxy resin matrix provides a high degree of tensile and flexural strength, making FR4 resistant to bending, twisting, and impact. This mechanical robustness is crucial for PCBs, as they often experience various stresses during assembly, handling, and operation.
The specific mechanical properties of FR4 may vary depending on the glass fiber content and the manufacturing process. Typical values for FR4 are as follows:
Property | Value Range |
---|---|
Tensile Strength | 300-400 MPa |
Flexural Strength | 400-600 MPa |
Compressive Strength | 400-500 MPa |
Impact Strength (Izod) | 80-120 J/m |
These mechanical properties make FR4 suitable for a wide range of applications, from consumer electronics to industrial equipment and aerospace systems.
Flame Retardancy and Safety
As the name suggests, FR4 is designed to be Flame Retardant. The material contains brominated epoxy resin, which helps to inhibit the spread of flames and reduce the risk of fire in electronic devices. This flame retardancy is essential for ensuring the safety of both users and equipment.
FR4 is rated as UL94 V-0, which means it meets the highest flammability rating set by Underwriters Laboratories (UL). To achieve this rating, the material must self-extinguish within 10 seconds after removing the flame, and the total burn time for five samples must not exceed 50 seconds.
UL94 Rating | Description |
---|---|
V-0 | Burning stops within 10 seconds; no flaming drips allowed |
V-1 | Burning stops within 30 seconds; no flaming drips allowed |
V-2 | Burning stops within 30 seconds; flaming drips allowed |
HB | Slow burning on a horizontal specimen; burning rate < 76 mm/min |
The flame retardancy of FR4 helps to minimize the risk of fire-related accidents and ensures compliance with various safety standards and regulations.
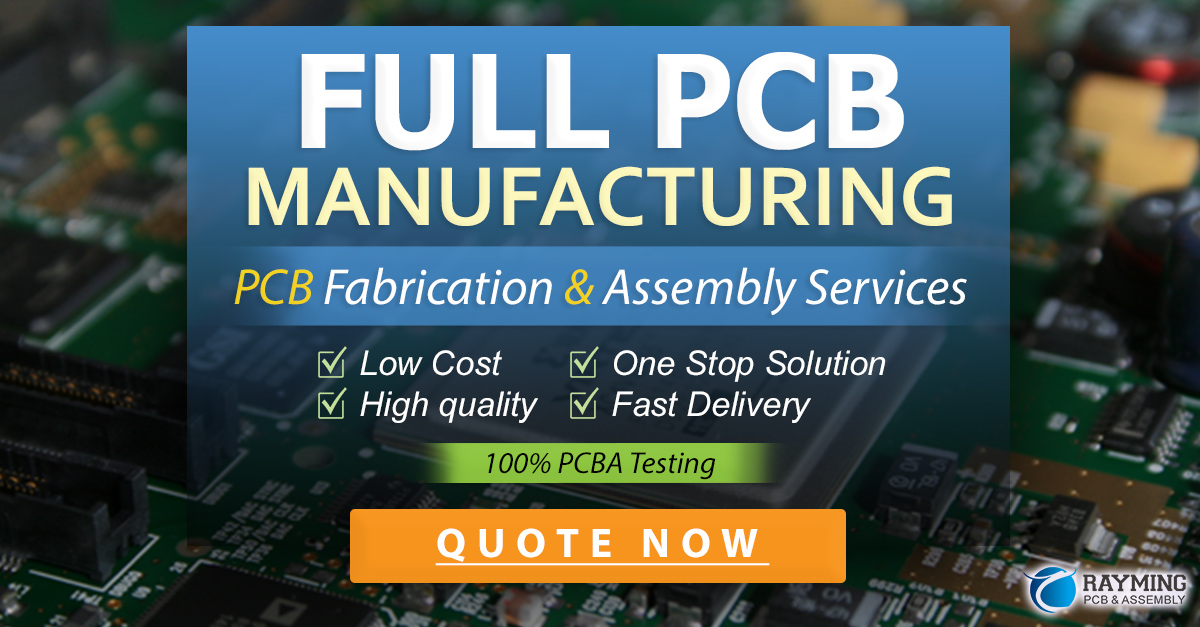
Thermal Stability and Temperature Resistance
FR4 exhibits excellent thermal stability and temperature resistance, making it suitable for a wide range of operating conditions. The glass transition temperature (Tg) of FR4 is typically around 130-140°C, which means the material maintains its mechanical and electrical properties up to this temperature.
The thermal expansion coefficient (CTE) of FR4 is also relatively low, typically around 14-16 ppm/°C in the X-Y plane and 50-70 ppm/°C in the Z-axis. This low CTE helps to minimize thermal stresses and warping of PCBs during temperature fluctuations, ensuring reliable performance and long-term durability.
Property | Value Range |
---|---|
Glass Transition Temperature (Tg) | 130-140°C |
CTE (X-Y plane) | 14-16 ppm/°C |
CTE (Z-axis) | 50-70 ppm/°C |
Thermal Conductivity | 0.3-0.4 W/m·K |
Furthermore, FR4 has a decent thermal conductivity of around 0.3-0.4 W/m·K, which helps to dissipate heat generated by electronic components. This thermal management capability is crucial for maintaining the performance and reliability of electronic devices.
Compatibility with Various Manufacturing Processes
FR4 is compatible with a wide range of manufacturing processes, making it a versatile choice for PCB fabrication. The material can be easily drilled, milled, and routed using standard PCB manufacturing equipment. This compatibility allows for the creation of complex PCB designs with fine features and high-density layouts.
Additionally, FR4 is suitable for various surface finishes, such as:
- Hot Air Solder Leveling (HASL)
- Electroless Nickel Immersion Gold (ENIG)
- Organic Solderability Preservative (OSP)
- Immersion Silver
- Immersion Tin
These surface finishes enhance the solderability and corrosion resistance of PCBs, ensuring reliable connections between electronic components.
Moreover, FR4 is compatible with different lamination processes, such as high-pressure lamination and vacuum lamination. This compatibility allows for the fabrication of multilayer PCBs, which are essential for complex electronic designs.
Cost-effectiveness and Availability
FR4 is widely available and cost-effective compared to other high-performance PCB Materials. The raw materials used in FR4 production, such as glass fibers and epoxy resins, are readily available and relatively inexpensive. This cost-effectiveness makes FR4 an attractive choice for a wide range of applications, from low-cost consumer electronics to high-volume industrial products.
Furthermore, the widespread adoption of FR4 has led to a well-established supply chain and manufacturing ecosystem. This availability ensures a consistent supply of FR4 laminates and helps to minimize lead times for PCB fabrication.
Environmental Considerations
While FR4 offers numerous benefits, it is essential to consider the environmental aspects of the material. The brominated flame retardants used in FR4 have raised concerns about their potential impact on human health and the environment.
In response to these concerns, the electronics industry has been working on developing more eco-friendly alternatives to traditional FR4. Some of these alternatives include:
- Halogen-free FR4 (FR4-HF): This variant uses non-brominated flame retardants, reducing the potential for harmful emissions during manufacturing and disposal.
- Natural fiber-reinforced laminates: These materials use natural fibers, such as bamboo or cotton, as reinforcement instead of glass fibers, reducing the environmental impact of PCB production.
- Biodegradable PCB Materials: Researchers are exploring the use of biodegradable polymers and natural fibers to create PCBs that can decompose more easily after their end-of-life.
Despite these developments, traditional FR4 remains the most widely used material for PCBs due to its proven performance and cost-effectiveness. As environmental regulations evolve and alternative materials mature, the electronics industry may gradually shift towards more sustainable PCB materials.
Frequently Asked Questions (FAQ)
-
Q: What does FR4 stand for?
A: FR4 stands for “Flame Retardant 4,” indicating that it is a flame-resistant material. -
Q: Is FR4 suitable for high-frequency applications?
A: Yes, FR4 is suitable for high-frequency applications due to its low dielectric constant and low dissipation factor. However, for very high-frequency applications (above 10 GHz), other materials like Rogers laminates may be more suitable. -
Q: Can FR4 be used for flexible PCBs?
A: No, FR4 is not suitable for flexible PCBs as it is a rigid material. For flexible PCBs, materials like polyimide or polyester are commonly used. -
Q: Is FR4 resistant to moisture?
A: FR4 has good moisture resistance, but it is not entirely waterproof. Prolonged exposure to high humidity can lead to moisture absorption, which may affect its electrical and mechanical properties. -
Q: Can FR4 be recycled?
A: Recycling FR4 is challenging due to the presence of glass fibers and brominated flame retardants. However, some recycling methods, such as mechanical recycling and chemical recycling, are being developed to recover valuable materials from waste PCBs.
Conclusion
FR4 is a versatile and widely used material for PCBs, offering a range of benefits that make it suitable for various electronic applications. Its excellent electrical insulation properties, mechanical strength, flame retardancy, thermal stability, and compatibility with manufacturing processes have made it the go-to choice for the electronics industry.
As technology advances and environmental concerns grow, the industry may shift towards more eco-friendly alternatives to traditional FR4. However, the proven performance, cost-effectiveness, and widespread availability of FR4 ensure that it will remain a crucial material in the electronics landscape for the foreseeable future.
No responses yet