Introduction to Polyimide PCBs
Polyimide PCBs are a type of printed circuit board known for their excellent thermal stability, chemical resistance, and mechanical strength. They utilize polyimide, a high-performance polymer, as the base material for the board substrate. Polyimide PCBs find applications in various industries, including aerospace, automotive, medical, and telecommunications, where reliability under harsh conditions is paramount.
Types of Polyimide PCBs
Polyimide PCBs come in two main types: rigid and flexible.
Rigid Polyimide PCBs
Rigid polyimide PCBs are constructed using a solid polyimide substrate that provides a stable platform for electronic components. The rigid nature of the board allows for high component density and precise trace routing. Rigid polyimide PCBs offer several advantages:
- High thermal stability (up to 260°C)
- Excellent chemical resistance
- Low dielectric constant and dissipation factor
- Good mechanical strength and dimensional stability
These properties make rigid polyimide PCBs suitable for applications that require high reliability, such as aerospace and military electronics.
Flexible Polyimide PCBs
Flexible polyimide PCBs, also known as flex PCBs, use a thin, flexible polyimide film as the substrate material. The flexibility of the board allows for unique 3D packaging and space-saving designs. Flex PCBs offer several benefits:
- Lightweight and compact design
- Ability to flex and fold, enabling complex shapes
- High resistance to vibration and shock
- Excellent thermal stability and chemical resistance
Flex PCBs are commonly used in applications that require flexibility, such as wearable electronics, medical devices, and automotive electronics.
Polyimide Laminate Materials
Polyimide laminate materials are used to construct the substrate for polyimide PCBs. These laminates consist of a polyimide film bonded to a reinforcement material, such as glass fabric or aramid paper. The choice of laminate material depends on the specific requirements of the application, such as thermal stability, dielectric properties, and mechanical strength.
Common Polyimide Laminate Materials
Laminate Material | Description | Key Properties |
---|---|---|
PI (Polyimide) | Pure polyimide film | – High thermal stability – Excellent chemical resistance – Low dielectric constant and dissipation factor |
FR-4 (Flame Retardant 4) | Glass fabric impregnated with epoxy resin | – Good mechanical strength – Flame retardant – Cost-effective |
CEM-3 (Composite Epoxy Material 3) | Non-woven glass reinforced epoxy laminate | – Improved mechanical strength over FR-4 – Better electrical properties than FR-4 – Cost-effective |
G-10 | Glass fabric impregnated with epoxy resin | – High mechanical strength – Excellent insulation properties – Suitable for high-temperature applications |
The choice of laminate material depends on factors such as the operating temperature range, chemical exposure, and mechanical requirements of the application.
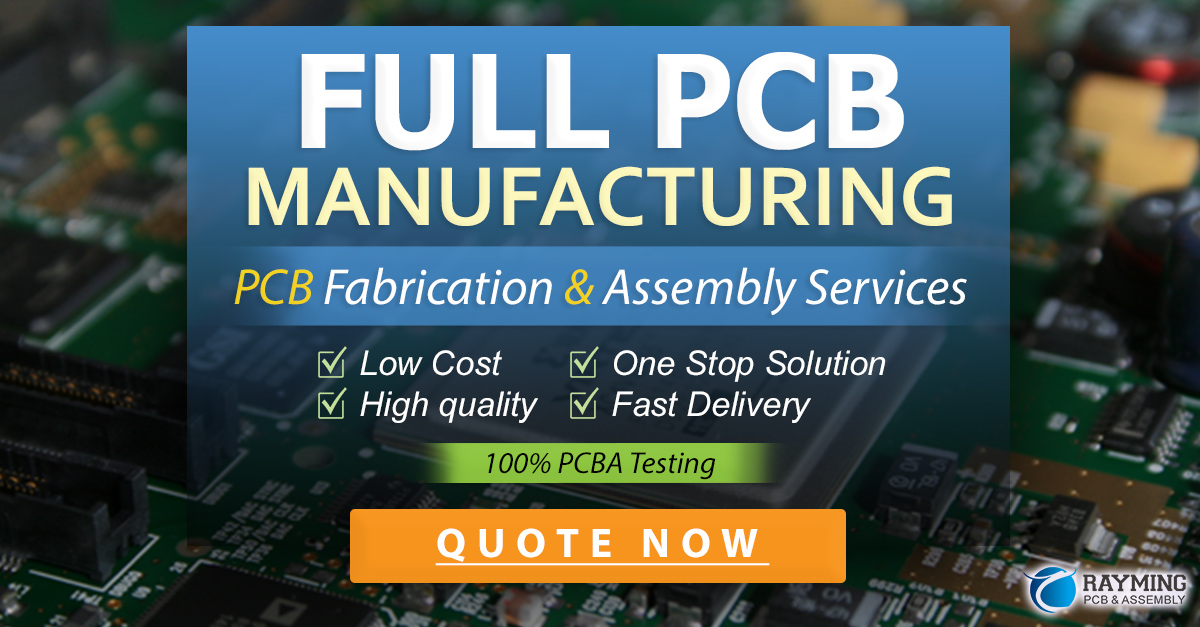
Manufacturing Process of Polyimide PCBs
The manufacturing process for polyimide PCBs involves several steps:
-
Substrate Preparation: The polyimide laminate material is cut to the desired size and shape. For multilayer boards, multiple laminate layers are stacked and bonded together using heat and pressure.
-
Drilling: Holes are drilled into the substrate for through-hole components and vias.
-
Plating: The drilled holes are plated with a conductive material, typically copper, to establish electrical connections between layers.
-
Patterning: The desired circuit pattern is transferred onto the copper-clad laminate using photolithography. A photoresist layer is applied, exposed to UV light through a photomask, and developed to reveal the circuit pattern.
-
Etching: The exposed copper is etched away using a chemical solution, leaving only the desired circuit traces.
-
Solder Mask Application: A solder mask layer is applied to protect the copper traces and prevent short circuits during soldering.
-
Surface Finish: A surface finish, such as HASL (Hot Air Solder Leveling), ENIG (Electroless Nickel Immersion Gold), or OSP (Organic Solderability Preservative), is applied to the exposed copper pads to enhance solderability and protect against oxidation.
-
Electrical Testing: The manufactured PCB undergoes electrical testing to ensure proper functionality and identify any defects.
Applications of Polyimide PCBs
Polyimide PCBs find applications in various industries due to their unique properties and reliability.
Aerospace and Defense
In the aerospace and defense sectors, polyimide PCBs are used in avionics, satellite systems, and military electronics. The high thermal stability and chemical resistance of polyimide make it suitable for harsh environments encountered in these applications.
Automotive Electronics
Polyimide PCBs are used in automotive electronics, such as engine control units, sensors, and infotainment systems. The ability to withstand high temperatures and vibrations makes polyimide PCBs ideal for under-the-hood applications.
Medical Devices
Polyimide PCBs are used in medical devices, such as implantable devices, surgical instruments, and diagnostic equipment. The biocompatibility and reliability of polyimide make it suitable for medical applications.
Telecommunications
In the telecommunications industry, polyimide PCBs are used in high-frequency applications, such as 5G networks and satellite communications. The low dielectric constant and dissipation factor of polyimide enable high-speed signal transmission with minimal losses.
Advantages of Polyimide PCBs
Polyimide PCBs offer several advantages over traditional PCB materials:
-
High Thermal Stability: Polyimide PCBs can withstand temperatures up to 260°C, making them suitable for high-temperature applications.
-
Excellent Chemical Resistance: Polyimide is resistant to a wide range of chemicals, including solvents, acids, and bases, ensuring reliable performance in harsh environments.
-
Low Dielectric Constant and Dissipation Factor: Polyimide has a low dielectric constant and dissipation factor, which minimizes signal loss and enables high-speed signal transmission.
-
Mechanical Strength: Polyimide PCBs have high mechanical strength and dimensional stability, making them resistant to vibration and shock.
-
Flexibility (for Flex PCBs): Flexible polyimide PCBs can bend and fold, enabling unique 3D packaging and space-saving designs.
Challenges and Considerations
While polyimide PCBs offer numerous benefits, there are also some challenges and considerations to keep in mind:
-
Cost: Polyimide PCBs are generally more expensive than traditional FR-4 PCBs due to the higher cost of polyimide materials and specialized manufacturing processes.
-
Manufacturing Complexity: The manufacturing process for polyimide PCBs is more complex compared to FR-4 PCBs, requiring specialized equipment and expertise.
-
Design Considerations: Designing with polyimide PCBs requires careful consideration of thermal management, signal integrity, and mechanical stress to ensure optimal performance.
FAQ
1. What is the main difference between rigid and flex polyimide PCBs?
Rigid polyimide PCBs use a solid polyimide substrate, providing a stable platform for components, while flex polyimide PCBs use a thin, flexible polyimide film, allowing for unique 3D packaging and flexibility.
2. Can polyimide PCBs be used in high-temperature applications?
Yes, polyimide PCBs are known for their high thermal stability and can withstand temperatures up to 260°C, making them suitable for high-temperature applications.
3. Are polyimide PCBs more expensive than traditional FR-4 PCBs?
Yes, polyimide PCBs are generally more expensive than FR-4 PCBs due to the higher cost of polyimide materials and specialized manufacturing processes.
4. What industries commonly use polyimide PCBs?
Polyimide PCBs are commonly used in industries such as aerospace, automotive, medical devices, and telecommunications, where high reliability and performance under harsh conditions are required.
5. Can flexible polyimide PCBs be used in wearable electronics?
Yes, flexible polyimide PCBs are well-suited for wearable electronics due to their ability to flex and fold, enabling compact and lightweight designs that can conform to the human body.
Conclusion
Polyimide PCBs, available in rigid and flexible formats, offer unique properties such as high thermal stability, chemical resistance, and mechanical strength. These properties make them suitable for demanding applications in industries such as aerospace, automotive, medical devices, and telecommunications. The choice of polyimide laminate materials depends on the specific requirements of the application, such as operating temperature range, chemical exposure, and mechanical demands.
While polyimide PCBs offer numerous advantages, they also come with challenges such as higher cost and manufacturing complexity compared to traditional PCB materials. Careful consideration of design factors, such as thermal management and signal integrity, is essential to ensure optimal performance.
As technology continues to advance and the demand for reliable electronics in harsh environments grows, polyimide PCBs are poised to play an increasingly important role in enabling innovative solutions across various industries.
No responses yet