Table of Contents
- Introduction to PCB Composition
- Substrate Materials
- FR-4
- High-Frequency Laminates
- Flexible Substrates
- Ceramic Substrates
- Copper Foil
- Electrodeposited Copper Foil
- Rolled Copper Foil
- Copper Thickness and Weight
- Solder Mask
- Liquid Photoimageable Solder Mask (LPSM)
- Dry Film Solder Mask (DFSM)
- Solder Mask Colors and Properties
- Silkscreen
- Silkscreen Inks
- Silkscreen Application Methods
- Surface Finishes
- Hot Air Solder Leveling (HASL)
- Electroless Nickel Immersion Gold (ENIG)
- Immersion Silver (IAg)
- Immersion Tin (ISn)
- Organic Solderability Preservative (OSP)
- Vias and Plated Through-Holes
- Blind Vias
- Buried Vias
- Microvias
- Through-Hole Plating
- Adhesives and Bonding Materials
- Prepreg
- Laminating Adhesives
- Coverlay and Bondply
- Soldermask and Legend Inks
- UV-Curable Inks
- Thermal-Curable Inks
- Ink Jet Inks
- Environmental Considerations
- Lead-Free Materials
- Halogen-Free Materials
- Recyclability and Disposal
- Frequently Asked Questions (FAQ)
- Conclusion
1. Introduction to PCB Composition
Printed Circuit Boards are composed of multiple layers of materials, each serving a specific purpose in the overall functionality and reliability of the board. The primary components of a PCB include:
- Substrate material
- Copper foil
- Solder mask
- Silkscreen
- Surface finishes
- Vias and plated through-holes
- Adhesives and bonding materials
- Soldermask and legend inks
By understanding the properties and roles of these materials, engineers and manufacturers can design and produce high-quality PCBs that meet the demanding requirements of modern electronics.
2. Substrate Materials
The substrate is the foundation of a PCB, providing mechanical support and electrical insulation between conductive layers. The choice of substrate material depends on factors such as the intended application, operating frequency, and environmental conditions. Common substrate materials include:
FR-4
FR-4 is the most widely used substrate material for PCBs. It is a composite material made of woven fiberglass cloth impregnated with an epoxy resin. FR-4 offers excellent mechanical strength, thermal stability, and electrical insulation properties, making it suitable for a wide range of applications.
High-Frequency Laminates
For high-frequency applications, such as RF and microwave circuits, specialized substrate materials are used to minimize signal loss and maintain signal integrity. These materials, such as Rogers and PTFE laminates, have low dielectric constants and dissipation factors, enabling high-speed signal transmission with minimal distortion.
Flexible Substrates
Flexible PCBs (FPCBs) use thin, flexible substrate materials such as polyimide or polyester films. These materials allow the PCB to bend and conform to various shapes, making them suitable for applications that require flexibility, such as wearable devices and compact electronics.
Ceramic Substrates
Ceramic substrates, such as alumina and aluminum nitride, are used in high-power and high-temperature applications. These materials offer excellent thermal conductivity, electrical insulation, and dimensional stability, making them ideal for use in power electronics and LED lighting.
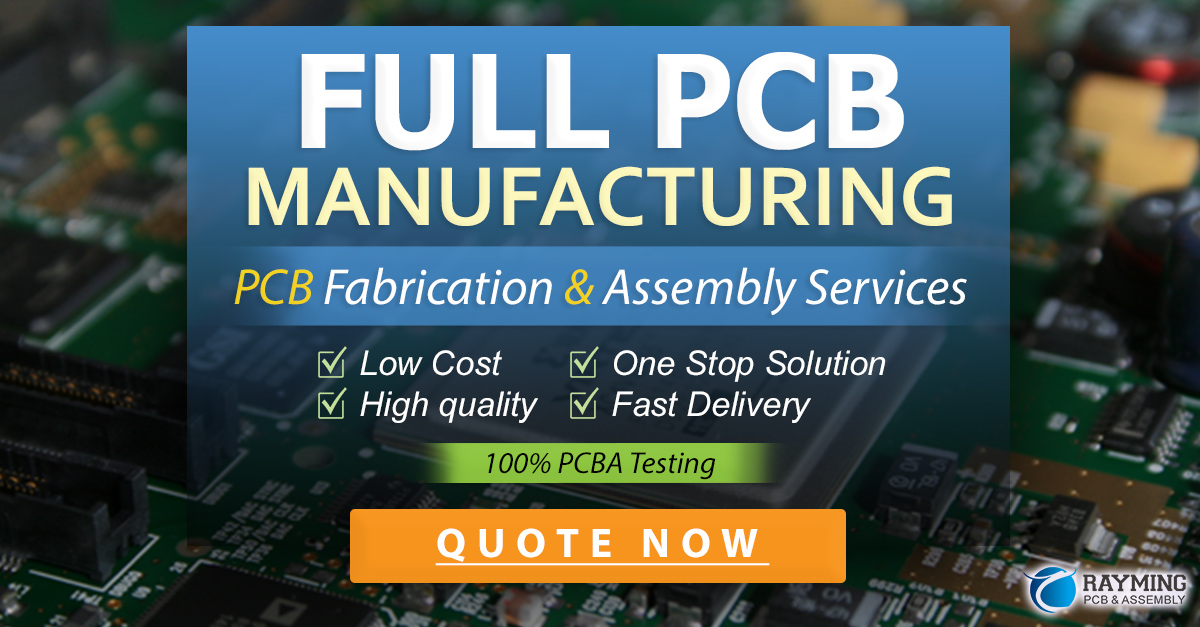
3. Copper Foil
Copper foil is the conductive layer in a PCB, responsible for carrying electrical signals between components. The two main types of copper foil used in PCB manufacturing are:
Electrodeposited Copper Foil
Electrodeposited copper foil is produced by electroplating copper onto a rotating drum or stainless steel cathode. This process creates a fine-grained, ductile copper layer with excellent adhesion to the substrate material. Electrodeposited copper foil is commonly used in multi-layer PCBs and high-density interconnect (HDI) applications.
Rolled Copper Foil
Rolled copper foil is produced by mechanically rolling copper ingots into thin sheets. This process results in a smooth, uniform surface finish and consistent mechanical properties. Rolled copper foil is often used in high-frequency applications and single-layer PCBs.
Copper Thickness and Weight
The thickness and weight of the copper foil play a crucial role in the electrical and thermal performance of the PCB. Copper thickness is typically measured in ounces per square foot (oz/ft²), with common thicknesses ranging from 0.5 oz/ft² to 4 oz/ft². Thicker copper layers offer lower resistance and better current-carrying capacity, but they can also increase the cost and complexity of the PCB manufacturing process.
4. Solder Mask
Solder mask is a protective coating applied to the surface of a PCB to prevent solder bridging and protect the copper traces from oxidation and environmental damage. The two main types of solder mask are:
Liquid Photoimageable Solder Mask (LPSM)
LPSM is a liquid photopolymer that is applied to the PCB surface and then selectively exposed to UV light through a photomask. The exposed areas cure and harden, while the unexposed areas are washed away during development. LPSM offers excellent resolution and can be applied in thin, uniform layers.
Dry Film Solder Mask (DFSM)
DFSM is a solid photopolymer film that is laminated onto the PCB surface and then exposed to UV light through a photomask. The exposed areas cure and bond to the PCB, while the unexposed areas are peeled away. DFSM is often used for high-volume production and offers good durability and chemical resistance.
Solder Mask Colors and Properties
Solder masks are available in a range of colors, with green being the most common. Other colors, such as blue, red, and black, are used for aesthetic purposes or to improve contrast for automated optical inspection (AOI). Solder masks also vary in their surface finish, with matte and glossy options available to suit different application requirements.
5. Silkscreen
Silkscreen, also known as legend or nomenclature, is a printed layer on the surface of a PCB that provides information such as component designators, polarity markers, and company logos. Silkscreen is typically applied using screen printing or inkjet printing methods.
Silkscreen Inks
Silkscreen inks are formulated to provide good adhesion, durability, and legibility on the surface of the PCB. These inks are available in various colors, with white being the most common for optimal contrast against the solder mask. UV-curable and thermal-curable inks are used to ensure fast drying times and resistance to abrasion and chemicals.
Silkscreen Application Methods
Screen printing is the traditional method for applying silkscreen to PCBs. In this process, ink is forced through a fine mesh screen onto the PCB surface using a squeegee. Screen printing offers good ink coverage and can produce fine details, but it requires a separate screen for each unique design.
Inkjet printing is a digital alternative to screen printing that offers greater flexibility and faster turnaround times. In this process, silkscreen ink is deposited directly onto the PCB surface using a high-resolution inkjet printer. Inkjet printing eliminates the need for screens and allows for easy design changes, making it suitable for low-volume production and prototyping.
6. Surface Finishes
Surface finishes are applied to the exposed copper areas of a PCB to protect them from oxidation and improve solderability. The choice of surface finish depends on factors such as the intended application, environmental conditions, and manufacturing process. Common surface finishes include:
Hot Air Solder Leveling (HASL)
HASL is a traditional surface finish that involves dipping the PCB into a molten solder bath and then using hot air to blow off the excess solder. This process creates a thin, uniform layer of solder on the exposed copper areas, providing good solderability and protection against oxidation. However, HASL can result in an uneven surface and may not be suitable for fine-pitch components.
Electroless Nickel Immersion Gold (ENIG)
ENIG is a two-layer surface finish that consists of a thin layer of gold over a layer of nickel. The nickel layer provides a barrier against copper diffusion and improves the mechanical strength of the surface, while the gold layer offers excellent solderability and corrosion resistance. ENIG is suitable for fine-pitch components and has a long shelf life, but it can be more expensive than other surface finishes.
Immersion Silver (IAg)
IAg is a single-layer surface finish that involves immersing the PCB in a silver solution, resulting in a thin layer of silver on the exposed copper areas. IAg offers good solderability and is less expensive than ENIG, but it has a shorter shelf life and may be prone to tarnishing over time.
Immersion Tin (ISn)
ISn is another single-layer surface finish that involves immersing the PCB in a tin solution. ISn provides good solderability and is less expensive than ENIG and IAg, but it has a limited shelf life and may be prone to whisker growth, which can cause short circuits.
Organic Solderability Preservative (OSP)
OSP is a thin, organic coating that is applied to the exposed copper areas of a PCB to prevent oxidation and maintain solderability. OSP is a low-cost, lead-free option that is suitable for quick-turn prototyping and high-volume production. However, OSP has a limited shelf life and may require special handling and storage conditions to maintain its effectiveness.
7. Vias and Plated Through-Holes
Vias and plated through-holes are conductive pathways that connect different layers of a multi-layer PCB. These features are created by drilling holes in the PCB and then plating them with copper to form electrical connections between layers.
Blind Vias
Blind vias are holes that are drilled from one surface of the PCB and terminate at an inner layer, without passing through the entire board. Blind vias are used to connect surface layers to inner layers in high-density designs, saving space and reducing signal path lengths.
Buried Vias
Buried vias are holes that are drilled between inner layers of the PCB, without connecting to either surface. Buried vias are used to create connections between inner layers in complex, multi-layer designs, further increasing routing density and signal integrity.
Microvias
Microvias are small, laser-drilled holes that are typically less than 150 microns in diameter. Microvias are used in high-density interconnect (HDI) designs to create fine-pitch connections between layers, enabling the use of smaller components and more compact layouts.
Through-Hole Plating
Through-hole plating is the process of depositing a layer of copper onto the walls of drilled holes to create electrical connections between layers. This process involves several steps, including cleaning, activation, electroless copper deposition, and electroplating. The quality and uniformity of the through-hole plating are critical factors in ensuring reliable electrical connections and mechanical strength.
8. Adhesives and Bonding Materials
Adhesives and bonding materials are used to laminate the layers of a multi-layer PCB together and provide mechanical support and insulation between layers. The three main types of bonding materials used in PCB manufacturing are:
Prepreg
Prepreg is a partially cured, B-stage epoxy resin that is reinforced with woven or non-woven fiberglass. Prepreg is used as an insulating layer between the copper foil and the substrate material, and it also serves as an adhesive to bond the layers together during the lamination process. The type and thickness of prepreg used in a PCB design depend on factors such as the desired dielectric constant, thermal conductivity, and mechanical strength.
Laminating Adhesives
Laminating adhesives are used to bond the copper foil to the substrate material in single-layer and double-sided PCBs. These adhesives are typically acrylic or epoxy-based and are applied as a thin film or a liquid coating. Laminating adhesives must provide good adhesion, thermal stability, and electrical insulation properties to ensure reliable performance.
Coverlay and Bondply
Coverlay and bondply are adhesive-coated films that are used in flexible PCBs to provide insulation and protection for the copper traces. Coverlay is a polyimide film with a pre-applied adhesive on one side, while bondply is a similar film with adhesive on both sides. These materials are laminated onto the flexible substrate using heat and pressure, creating a durable and flexible assembly.
9. Soldermask and Legend Inks
Soldermask and legend inks are specialized inks used in the application of solder mask and silkscreen layers on PCBs. These inks are formulated to provide specific properties and performance characteristics, such as:
UV-Curable Inks
UV-curable inks are polymer-based inks that cure and harden when exposed to ultraviolet light. These inks offer fast curing times, good resolution, and excellent adhesion to the PCB surface. UV-curable inks are commonly used for liquid photoimageable solder masks and inkjet-printed legends.
Thermal-Curable Inks
Thermal-curable inks are epoxy-based inks that cure and harden when exposed to heat. These inks offer good durability, chemical resistance, and compatibility with a wide range of substrate materials. Thermal-curable inks are often used for screen-printed solder masks and legends.
Ink Jet Inks
Ink jet inks are specialized inks formulated for use in inkjet printing systems. These inks are typically UV-curable or solvent-based and offer good color accuracy, resolution, and compatibility with various printhead technologies. Ink jet inks are used for printing legends, solder masks, and other functional layers in PCB manufacturing.
10. Environmental Considerations
As environmental regulations become more stringent, PCB manufacturers are increasingly focusing on the use of eco-friendly materials and processes. Some key environmental considerations in PCB composition include:
Lead-Free Materials
The use of lead-free solder alloys and surface finishes has become mandatory in many countries due to the toxic nature of lead. Common lead-free solder alloys include tin-silver-copper (SAC) and tin-bismuth (SnBi), while lead-free surface finishes include ENIG, IAg, and ISn.
Halogen-Free Materials
Halogenated compounds, such as brominated flame retardants (BFRs), have been widely used in PCB materials to improve fire resistance. However, these compounds can release toxic substances during combustion and pose environmental and health risks. Halogen-free materials, such as phosphorus-based flame retardants and non-halogenated substrates, are now being used as safer alternatives.
Recyclability and Disposal
The proper disposal and recycling of PCBs are critical for minimizing environmental impact and conserving resources. PCB manufacturers are developing new materials and processes that facilitate the separation and recovery of valuable metals, such as copper and gold, from end-of-life PCBs. Additionally, the use of biodegradable and renewable materials, such as plant-based resins and natural fibers, is being explored as a means of reducing waste and promoting sustainability.
11. Frequently Asked Questions (FAQ)
- What is the difference between a single-layer and a multi-layer PCB?
-
A single-layer PCB has conductive traces on only one side of the substrate, while a multi-layer PCB has conductive traces on multiple layers, separated by insulating layers. Multi-layer PCBs offer higher routing density and better signal integrity, but they are more complex and expensive to manufacture.
-
What is the purpose of vias in a PCB?
-
Vias are conductive pathways that connect different layers of a multi-layer PCB. They allow signals to travel between layers, enabling more complex routing and higher component density. Vias can be blind (connecting surface layers to inner layers), buried (connecting inner layers only), or through-hole (connecting all layers).
-
How does the choice of substrate material affect PCB performance?
- The substrate material plays a critical role in determining the electrical, mechanical, and thermal properties of a PCB. Factors such as dielectric constant, dissipation factor, thermal conductivity, and mechanical strength vary depending on the substrate material, affecting signal integrity, power handling, and reliability. The choice of substrate material depends on the specific application requirements and operating conditions.
4.
No responses yet