Understanding PCB traces
What are PCB Traces?
PCB traces are the thin, conductive paths etched or printed onto the surface of a printed circuit board. They act as electrical highways, connecting components such as resistors, capacitors, integrated circuits, and other electronic devices. Traces allow signals and power to be routed efficiently across the board, ensuring proper communication and functionality within the electronic system.
The Importance of PCB Traces
PCB traces play a vital role in the performance and reliability of electronic devices. Some key reasons why PCB traces are important include:
-
Signal Integrity: Well-designed and properly manufactured PCB traces ensure the integrity of the electrical signals transmitted between components. This is crucial for maintaining signal quality, minimizing noise, and preventing signal degradation.
-
Power Distribution: PCB traces also serve as a means of distributing power to various components on the board. Adequate trace width and thickness are necessary to handle the required current without excessive voltage drop or overheating.
-
Electromagnetic Compatibility (EMC): Properly designed PCB traces help minimize electromagnetic interference (EMI) and ensure electromagnetic compatibility. This is achieved through techniques such as proper trace routing, impedance control, and the use of ground planes.
-
Reliability: The quality and durability of PCB traces directly impact the overall reliability of the electronic device. Traces must withstand environmental factors such as temperature fluctuations, humidity, and mechanical stress to maintain their integrity over the product’s lifetime.
Materials Used for PCB Traces
Copper
Copper is the most commonly used material for creating PCB traces. It offers several advantages that make it an ideal choice:
-
Excellent Electrical Conductivity: Copper has a high electrical conductivity, allowing for efficient signal transmission and low resistance. This minimizes power losses and ensures good signal integrity.
-
Thermal Conductivity: Copper also has good thermal conductivity, which helps dissipate heat generated by electronic components. This is important for preventing overheating and ensuring the longevity of the PCB.
-
Durability: Copper traces are relatively durable and can withstand the stresses of manufacturing processes and normal operating conditions.
-
Cost-effective: Copper is widely available and relatively inexpensive compared to other conductive materials, making it a cost-effective choice for PCB production.
Types of Copper Used in PCB Traces
There are two main types of copper used in PCB manufacturing:
-
Electrodeposited Copper (ED Copper): ED copper is a pure form of copper that is deposited onto the PCB substrate through an electroplating process. It offers excellent adhesion and is commonly used for high-density designs and fine-pitch traces.
-
Rolled Annealed Copper (RA Copper): RA copper is a mechanically processed copper foil that is bonded to the PCB substrate. It has a slightly higher surface roughness compared to ED copper, which can improve adhesion to the substrate. RA copper is often used for general-purpose PCB applications.
Copper Thickness and Trace Width
The thickness of the copper traces and their width are critical factors in PCB design. The thickness is typically measured in ounces per square foot (oz/ft²) and ranges from 0.5 oz/ft² to 4 oz/ft² in most applications. Thicker copper traces can carry higher currents and provide better heat dissipation, but they also increase the overall weight and cost of the PCB.
Trace width, on the other hand, is determined by the current-carrying requirements and the manufacturing capabilities of the PCB fabricator. Wider traces have lower resistance and can handle higher currents, but they also occupy more space on the PCB. The trace width is typically specified in mils (thousandths of an inch) and can range from a few mils for high-density designs to hundreds of mils for power traces.
Other Materials Used for PCB Traces
While copper is the most common material for PCB traces, there are situations where alternative materials may be used:
-
Silver: Silver has even higher electrical conductivity than copper and is sometimes used in high-frequency applications or for specialized PCBs. However, its higher cost and lower durability compared to copper limit its widespread use.
-
Gold: Gold-plated traces are occasionally used in high-reliability applications or for PCBs that require excellent corrosion resistance. Gold is usually plated over a copper base to improve the surface finish and protect the underlying copper from oxidation.
-
Aluminum: In some specialized applications, such as high-power electronics or automotive PCBs, aluminum traces may be used. Aluminum has lower electrical conductivity compared to copper but offers benefits such as lower weight and better thermal conductivity.
-
Carbon-based Materials: Emerging technologies, such as printed electronics and flexible PCBs, may utilize conductive inks or carbon-based materials for creating traces. These materials offer advantages such as flexibility, low cost, and the ability to be printed on various substrates.
Manufacturing Process of PCB Traces
The manufacturing process of PCB traces involves several steps to create the desired conductive pathways on the PCB substrate. Here is an overview of the typical process:
-
PCB Design: The first step is to design the PCB layout using specialized software. The design includes the placement of components, routing of traces, and specification of trace width and spacing.
-
Substrate Preparation: The PCB substrate, typically made of fiberglass-reinforced epoxy (FR-4) or other materials, is cleaned and prepared for the subsequent processes.
-
Copper Cladding: A thin layer of copper foil is laminated onto the substrate using heat and pressure. The copper foil can be pre-bonded (RA copper) or electrodeposited (ED copper) onto the substrate.
-
Photoresist Application: A photosensitive resist material is applied onto the copper surface. This resist will later be used to transfer the trace pattern onto the copper.
-
Exposure and Development: The PCB is exposed to UV light through a photomask that contains the trace pattern. The exposed areas of the photoresist become soluble and are removed during the development process, leaving the desired trace pattern protected by the remaining photoresist.
-
Etching: The PCB is immersed in an etchant solution, typically ferric chloride or ammonium persulfate, which removes the unprotected copper areas. This leaves only the copper traces protected by the photoresist.
-
Resist Removal: The remaining photoresist is stripped away, revealing the final copper trace pattern on the PCB substrate.
-
Inspection and Testing: The PCB undergoes visual inspection and electrical testing to ensure the traces are properly formed and meet the specified requirements.
-
Surface Finish: Depending on the application, the PCB may undergo additional surface finishing processes, such as solder mask application, silkscreen printing, or surface plating (e.g., gold or silver), to protect the copper traces and improve solderability.
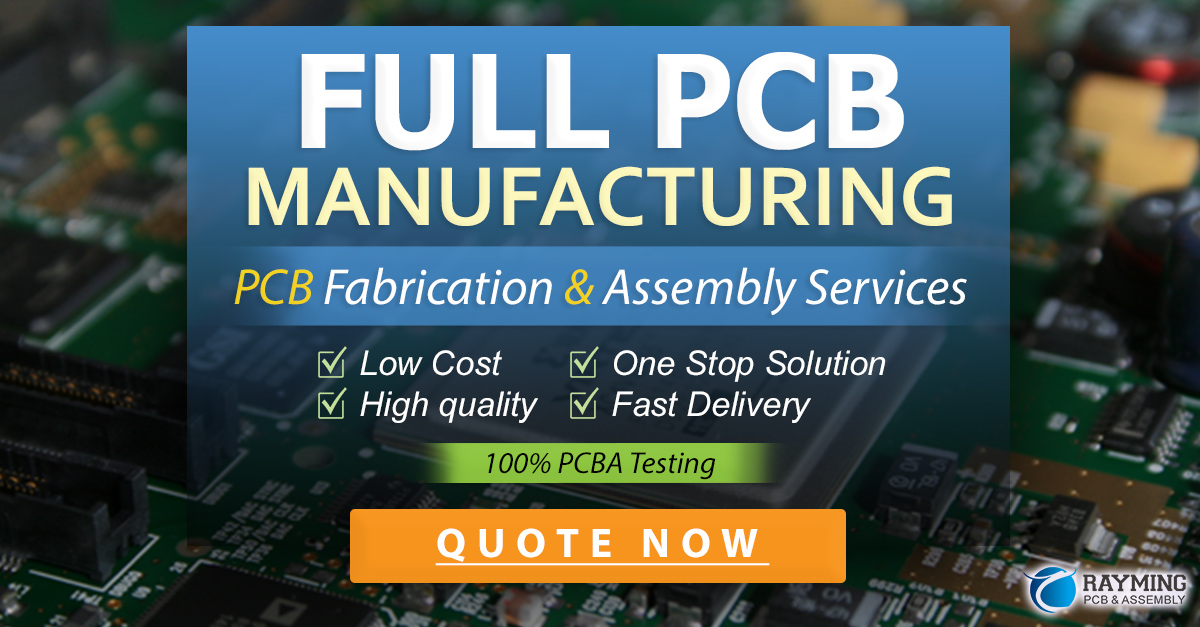
Considerations for PCB Trace Design
When designing PCB traces, several factors need to be considered to ensure optimal performance and reliability:
Trace Width and Thickness
As mentioned earlier, trace width and thickness are crucial parameters in PCB design. The trace width should be selected based on the current-carrying requirements and the available space on the PCB. Thicker traces can handle higher currents and provide better heat dissipation, but they also increase the overall weight and cost of the PCB.
The IPC (Association Connecting Electronics Industries) provides guidelines for determining the appropriate trace width based on the current requirements and copper thickness. These guidelines help designers ensure that the traces can handle the expected current without excessive voltage drop or temperature rise.
Trace Spacing
Trace spacing refers to the distance between adjacent traces on the PCB. Proper spacing is essential to prevent signal interference, crosstalk, and short circuits. The spacing requirements depend on factors such as the operating voltage, signal frequency, and manufacturing capabilities.
The IPC provides recommendations for minimum trace spacing based on the voltage level and the PCB’s intended use (e.g., general-purpose, high-voltage, or high-frequency applications). Adhering to these guidelines helps ensure the reliability and performance of the PCB.
Impedance Control
In high-speed digital circuits and high-frequency applications, controlling the impedance of PCB traces is crucial for maintaining signal integrity. Impedance is the resistance to the flow of alternating current (AC) signals and is determined by factors such as trace geometry, dielectric constant of the substrate, and the presence of ground planes.
Impedance-controlled traces are designed to have a specific characteristic impedance (e.g., 50 ohms or 100 ohms) to match the impedance of the connected components and minimize signal reflections. This is achieved by carefully selecting the trace width, thickness, and spacing, as well as using appropriate substrate materials and ground plane configurations.
Trace Routing
The routing of PCB traces plays a significant role in the overall performance and reliability of the electronic device. Proper trace routing helps minimize signal interference, reduces electromagnetic emissions, and ensures the efficient flow of signals between components.
Some key considerations for trace routing include:
-
Signal Integrity: Traces should be routed to minimize signal reflections, crosstalk, and other signal integrity issues. This involves techniques such as impedance matching, avoiding sharp bends, and using appropriate termination schemes.
-
Electromagnetic Compatibility (EMC): Trace routing should be done in a way that minimizes electromagnetic interference (EMI) and ensures compliance with EMC regulations. This may involve the use of ground planes, shielding, and proper trace spacing.
-
Manufacturing Constraints: The trace routing must adhere to the manufacturing capabilities of the PCB fabricator, such as minimum trace width, spacing, and hole sizes. Violating these constraints can lead to manufacturing issues and reduced yield.
-
Thermal Management: Traces should be routed to facilitate heat dissipation and prevent hot spots on the PCB. This may involve the use of thicker traces, thermal vias, and proper component placement.
FAQ
1. What is the most common material used for PCB traces?
The most common material used for PCB traces is copper. Copper offers excellent electrical conductivity, thermal conductivity, and durability, making it an ideal choice for creating conductive pathways on PCBs.
2. What are the different types of copper used in PCB manufacturing?
The two main types of copper used in PCB manufacturing are electrodeposited copper (ED copper) and rolled annealed copper (RA copper). ED copper is a pure form of copper deposited onto the PCB substrate through electroplating, while RA copper is a mechanically processed copper foil bonded to the substrate.
3. How is the thickness of copper traces measured?
The thickness of copper traces is typically measured in ounces per square foot (oz/ft²). Common thicknesses range from 0.5 oz/ft² to 4 oz/ft² in most PCB applications. Thicker copper traces can carry higher currents and provide better heat dissipation but also increase the overall weight and cost of the PCB.
4. What factors determine the appropriate trace width for a PCB design?
The appropriate trace width for a PCB design is determined by factors such as the current-carrying requirements, available space on the PCB, and the manufacturing capabilities of the PCB fabricator. The IPC (Association Connecting Electronics Industries) provides guidelines for selecting trace widths based on the current requirements and copper thickness.
5. Why is impedance control important for PCB traces?
Impedance control is important for PCB traces in high-speed digital circuits and high-frequency applications to maintain signal integrity. Impedance-controlled traces are designed to have a specific characteristic impedance to match the impedance of the connected components and minimize signal reflections. This helps ensure the reliable transmission of signals and reduces signal distortion.
Conclusion
PCB traces are the conductive pathways that form the backbone of electronic devices, allowing signals and power to flow between components. The most commonly used material for creating PCB traces is copper, which offers excellent electrical conductivity, thermal conductivity, and durability. Other materials such as silver, gold, aluminum, and carbon-based materials may be used in specialized applications.
The manufacturing process of PCB traces involves several steps, including PCB design, substrate preparation, copper cladding, photoresist application, exposure and development, etching, resist removal, inspection, and surface finishing. Careful consideration must be given to trace width, thickness, spacing, impedance control, and routing to ensure optimal performance and reliability.
By understanding the materials, manufacturing processes, and design considerations for PCB traces, engineers and designers can create high-quality, reliable electronic devices that meet the ever-increasing demands of modern technology. As electronics continue to evolve, advancements in materials and manufacturing techniques will further push the boundaries of what is possible with PCB traces, enabling even more innovative and sophisticated electronic systems.
No responses yet