Introduction to Flex PCBs and Stiffeners
Flexible printed circuit boards, also known as flex PCBs or FPCs, are a type of PCB that uses flexible materials like polyimide film instead of rigid FR4 fiberglass. Flex PCBs allow electronics to bend and fit into smaller or unusually shaped enclosures. However, flex PCBs still require some rigid areas for mounting components. This is where Flex PCB Stiffeners come into play.
Flex PCB stiffeners are thin, flat pieces of rigid material bonded to specific areas of a flex PCB to provide extra support and stability. Stiffeners prevent excessive bending that could damage components or conductive traces. They create rigid zones on the flex circuit for attaching connectors, components, or mechanical elements. Stiffeners are an essential part of most flex PCB designs.
Why Use Flex PCBs and Stiffeners?
There are several key advantages of using flex PCBs with stiffeners compared to rigid PCBs:
Compact Packaging
Flex PCBs can bend to fit in tighter spaces and conform to product contours. Stiffeners provide anchor points without sacrificing flexibility elsewhere. This enables miniaturization and sleeker product designs.
Reliability
Flexing puts stress on solder joints. Stiffeners limit flex to specific regions, protecting components and preventing failure from repeated bending. Strategically placed stiffeners improve reliability.
Integration
Flex PCBs can integrate wiring, connectors and components into a single part, reducing assembly steps. Stiffeners provide rigid areas to attach all elements together securely.
Cost Savings
Using a flex PCB with stiffeners can reduce part counts, materials, weight and labor compared to a design with separate rigid PCBs and wiring. Fewer parts means lower BOM costs.
Flex PCB Stiffener Materials
Flex PCB stiffeners are commonly made from FR4, polyimide, aluminum, stainless steel or epoxy glass. Each material has different properties suitable for various applications. Here’s a comparison:
Material | Thickness (mm) | Stiffness | Weight | Cost | Insulation | Machinability |
---|---|---|---|---|---|---|
FR4 | 0.2 – 3.2 | High | Medium | Low | Good | Easy |
Polyimide | 0.025 – 0.1 | Medium | Ultra Light | High | Excellent | Difficult |
Aluminum | 0.3 – 1.5 | Medium | Light | Medium | None | Easy |
Stainless Steel | 0.1 – 0.3 | Very High | Heavy | High | None | Moderate |
Epoxy Glass | 0.2 – 3.2 | High | Medium | Medium | Good | Moderate |
FR4 is the most popular choice for its low cost, good stiffness-to-weight ratio, and electrical insulation. Polyimide stiffeners are ultra-thin and lightweight but more expensive. Metal stiffeners provide the highest stiffness but add weight and require insulation. The right stiffener material depends on the specific electrical, mechanical, environmental and cost constraints of the application.
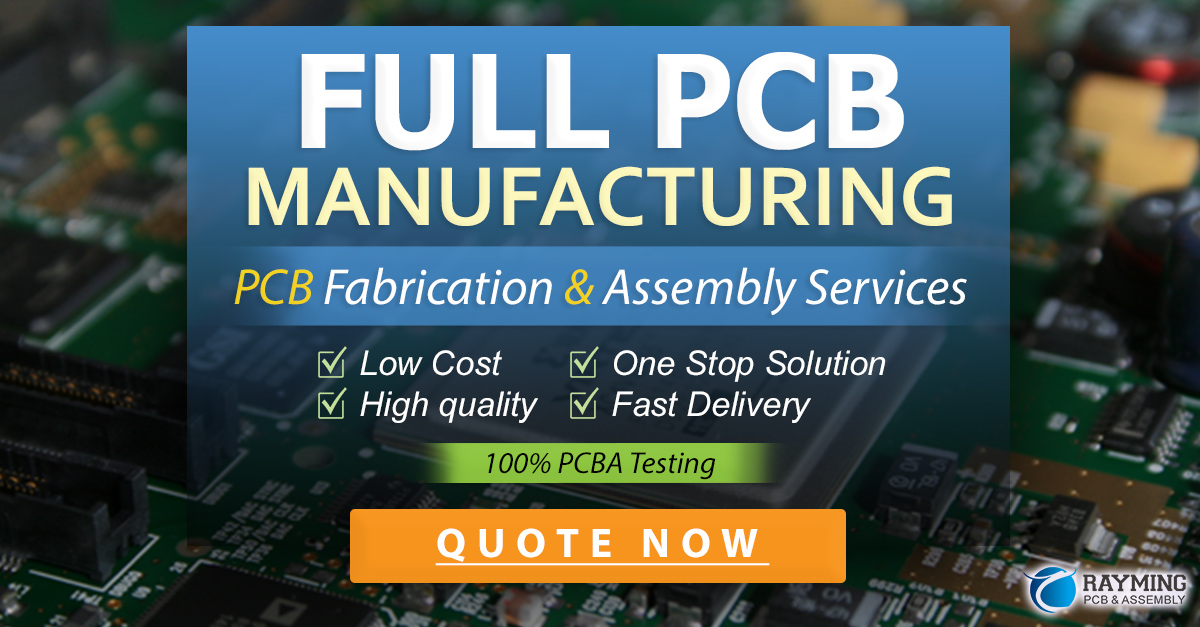
Applying Stiffeners to Flex PCBs
Flex PCB stiffeners are bonded to the circuit using various adhesives and processes:
Adhesive Options
- Pressure-sensitive adhesive (PSA) – double-sided tape
- Thermoset adhesive – epoxy or acrylic, cured with heat
- Thermoplastic adhesive – polyester, nylon, urethane, softens with heat
PSAs are lower cost and easier to apply but not as robust as thermoset or thermoplastic. Epoxies provide high strength bonding for demanding environments. Thermoplastics allow removal and re-attachment of the stiffener.
Attachment Methods
- Lamination – stiffener and adhesive are sandwiched with flex PCB in a heated press
- Spot bonding – stiffener is adhered only in select locations, allowing some movement
- Mechanical fastening – screws, rivets or pins hold stiffener and flex PCB together
Lamination creates the strongest bond and is most common. Spot bonding reduces stresses from CTE mismatches. Mechanical fastening is used when the stiffener needs to be removable.
Designing with Flex PCB Stiffeners
Properly implementing stiffeners requires careful planning during the flex PCB layout process. Key design considerations include:
Stiffener Placement
Stiffened areas should be large enough to support attached components but not interfere with flexing regions. Typical locations are connector sites, through-hole parts, and mounting/grounding points. Use 3D modeling to ensure clearances.
Stiffener Thickness
Stiffener thickness depends on required rigidity, Z-height constraints, and component weights. Thinner stiffeners suffice for small SMT chips. Thick stiffeners are needed for heavy or tall parts. Aim for natural convection and avoid abrupt thickness changes that cause stress concentrations.
Adhesive Selection
The adhesive must be compatible with the stiffener material and PCB surface. It needs sufficient peel strength and temperature tolerance for the assembly and operating conditions. Thicker adhesives are more forgiving of uneven surfaces. Woven glass reinforcement can improve dimensional stability.
Shapes and Cutouts
Stiffeners can be any shape or include cutouts to avoid components or board features. Rounded corners and gradual transitions help prevent stresses and damage to the flex circuit. Consider stiffener orientation relative to the bend axis and use relief slots if needed.
Assembly and Test
Plan for stiffener attachment in the assembly process flow. Lamination requires a press while adhesives may need time to cure. Stiffeners can interfere with ICT/FCT probing so test points should be placed in accessible locations. Boundary scan and flying probe testing can help.
Examples of Flex PCB Stiffener Applications
Flex PCBs with stiffeners are used across many industries, from consumer electronics to aerospace. Here are a few examples highlighting the benefits:
Wearables
Smartwatches and fitness trackers rely on flex PCBs to fit electronics into ergonomic housings. Stiffeners provide rigid areas for the display, buttons and sensors while allowing flexibility for comfort. Polyimide stiffeners keep wearables ultra-light.
Smartphones
Modern phones use flex PCBs for compact packaging of multiple boards and interconnects. Stiffeners are laminated in areas that attach to the rigid main PCB, camera modules, batteries and antennae. This integrated approach saves space and assembly time.
Medical Devices
Patient monitors and imaging equipment use flex PCBs for movable displays, probes and sensors. Stiffened zones protect delicate electronics while allowing articulation. Polyimide and epoxy glass materials can withstand sterilization.
Automobiles
Vehicle electronics like dashboards and lighting use flex PCBs to integrate controls into slim, curved surfaces. Stiffeners provide mechanical attachment points and support for buttons, knobs and LEDs. FR4 is commonly used for low cost.
Aerospace
Aircraft and satellites use flex PCBs for weight savings in instrumentation, avionics and communication systems. Stiffeners add durability in high-vibration environments. Aluminum or FR4 is often used for reliability in harsh conditions.
FAQ
What’s the difference between flex PCBs and rigid PCBs?
Flex PCBs use flexible insulating materials like polyimide while rigid PCBs use inflexible FR4. Flex PCBs can bend and fit in tighter spaces but require stiffeners to support components. Rigid PCBs are simpler and lower cost but limited to flat, 2D designs.
How thin can a flex PCB stiffener be?
Flex PCB stiffeners can be as thin as 0.2 mm for FR4, 0.025 mm for polyimide, 0.3 mm for aluminum, and 0.1 mm for stainless steel. The minimum thickness depends on the material and required stiffness for the application.
Can you use different stiffener materials in the same flex PCB?
Yes, you can mix and match stiffener materials in different areas of a flex PCB based on thickness, weight and stiffness requirements. For example, you could use thin polyimide for dense SMT areas and thicker FR4 for connector locations on the same design.
How do you specify stiffeners in a flex PCB stackup?
Stiffeners are typically defined in a separate drawing or layer of the fabrication files. The drawing should include stiffener material, thickness, shape, and location relative to the PCB. Adhesive type and thickness are also specified. Coordinate with your manufacturer on their preferred format.
Are there any limitations on stiffener sizes or shapes?
Stiffeners can be made in a wide range of sizes and shapes, with cutouts and relief slots as needed. Key limitations are material availability, fabrication capability, and assembly tolerances. Consult with your flex PCB supplier on their specific guidelines and constraints for stiffener geometries.
Conclusion
In summary, flex PCB stiffeners are an enabling technology for achieving the compact packaging, reliable performance and design flexibility of modern electronics. By bonding rigid materials to select areas of a flex circuit, stiffeners provide mechanical support and stability for components and interconnects. Stiffeners expand the applications for flex PCBs in space-constrained, harsh-environment and high-density products.
Choosing the right stiffener material, thickness, shape and attachment method depends on the electrical, mechanical, environmental and cost requirements of the specific application. Careful planning and co-design of the flex PCB and stiffener is essential for a successful product. With the range of material options and design techniques available today, flex PCB stiffeners are a powerful tool for optimizing the form and function of next-generation electronic devices.
No responses yet