Introduction to PCB materials
Printed Circuit Boards (PCBs) are the backbone of modern electronics. They provide a platform for mounting and interconnecting electronic components to create a functional circuit. The choice of materials used in the construction of PCBs is crucial as it determines the performance, reliability, and cost of the final product. In this article, we will explore the various materials used in the manufacture of cheap circuit boards.
What is a PCB?
A PCB is a flat board made of insulating material with conductive tracks etched onto its surface. These tracks are used to connect electronic components such as resistors, capacitors, and integrated circuits. PCBs can be single-sided, double-sided, or multi-layered depending on the complexity of the circuit.
Why are PCB materials important?
The choice of PCB materials is critical because it affects the following:
- Electrical properties: The material should have good insulating properties to prevent short circuits and good conductivity for the tracks.
- Mechanical properties: The material should be strong enough to withstand the stresses of manufacturing and use.
- Thermal properties: The material should be able to dissipate heat efficiently to prevent overheating of components.
- Cost: The material should be affordable to keep the overall cost of the PCB low.
Common PCB materials
FR-4
FR-4 is the most commonly used material for cheap PCBs. It is a composite material made of woven fiberglass cloth and epoxy resin. The fiberglass provides mechanical strength while the epoxy resin provides insulation and binds the fiberglass together.
Advantages of FR-4
- Good insulation properties
- High mechanical strength
- Good thermal stability
- Affordable
Disadvantages of FR-4
- Limited high-frequency performance
- Moisture absorption can cause delamination
- Not suitable for high-temperature applications
CEM-1
CEM-1 is a composite material made of cotton paper and epoxy resin. It is a cheaper alternative to FR-4 and is commonly used in low-cost consumer electronics.
Advantages of CEM-1
- Low cost
- Good insulation properties
- Easy to machine
Disadvantages of CEM-1
- Lower mechanical strength than FR-4
- Higher moisture absorption than FR-4
- Limited high-frequency performance
Phenolic paper
Phenolic paper is a low-cost PCB material made of paper impregnated with phenolic resin. It is commonly used in single-sided PCBs for low-cost consumer electronics.
Advantages of phenolic paper
- Very low cost
- Good insulation properties
- Easy to machine
Disadvantages of phenolic paper
- Low mechanical strength
- High moisture absorption
- Limited thermal stability
- Not suitable for high-frequency applications
Aluminum
Aluminum PCBs are used in applications that require good thermal dissipation, such as power electronics and LED lighting. The aluminum substrate provides excellent thermal conductivity while a thin layer of insulating material is used to isolate the tracks.
Advantages of aluminum PCBs
- Excellent thermal conductivity
- Good mechanical strength
- Lightweight
Disadvantages of aluminum PCBs
- Higher cost than FR-4
- Limited flexibility
- Requires specialized manufacturing processes
Comparison of PCB materials
Material | Cost | Insulation | Mechanical strength | Thermal stability | High-frequency performance |
---|---|---|---|---|---|
FR-4 | Low | Good | High | Good | Limited |
CEM-1 | Low | Good | Moderate | Moderate | Limited |
Phenolic paper | Very low | Good | Low | Low | Poor |
Aluminum | High | Good | High | Excellent | Moderate |
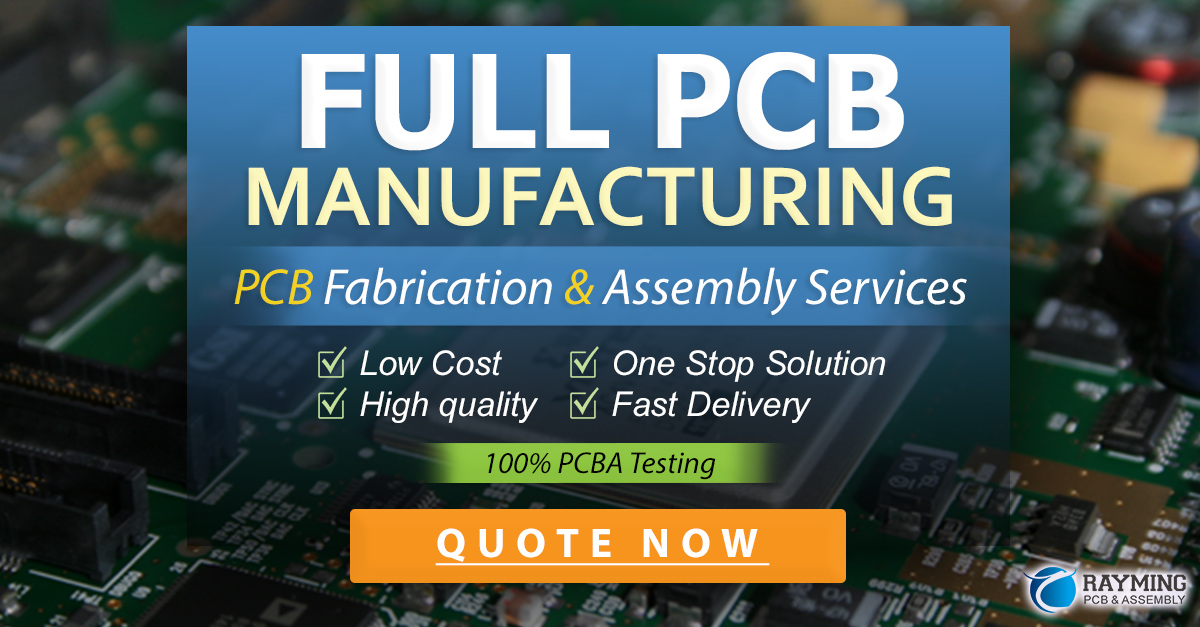
Factors affecting the choice of PCB material
Application requirements
The choice of PCB material depends on the specific requirements of the application. For example, a high-power application may require an aluminum PCB for better thermal dissipation, while a low-cost consumer device may use phenolic paper to keep costs down.
Manufacturing process
The manufacturing process also influences the choice of PCB material. Some materials, such as aluminum, require specialized manufacturing processes that may not be available at all PCB fabrication facilities.
Cost considerations
The cost of the PCB material is a significant factor in the overall cost of the finished product. Cheaper materials like phenolic paper and CEM-1 are often used in low-cost consumer electronics to keep prices down.
Future trends in PCB materials
High-frequency materials
As electronic devices operate at higher frequencies, there is a growing demand for PCB materials that can provide better high-frequency performance. Materials such as PTFE and low-loss ceramics are being developed to meet this demand.
Eco-friendly materials
There is a growing concern about the environmental impact of electronic waste. Researchers are developing eco-friendly PCB materials that are biodegradable or recyclable to reduce the environmental footprint of electronic devices.
3D printing
3D printing technology is being explored as a way to manufacture PCBs with complex geometries and embedded components. This could lead to new PCB materials that are specifically designed for 3D printing.
Frequently Asked Questions (FAQ)
1. What is the Cheapest PCB material?
The cheapest PCB material is phenolic paper, which is made of paper impregnated with phenolic resin. However, it has low mechanical strength and limited thermal stability, making it suitable only for low-cost, low-performance applications.
2. Can I use aluminum for all PCB applications?
No, aluminum is not suitable for all PCB applications. While it provides excellent thermal conductivity, it is more expensive than FR-4 and requires specialized manufacturing processes. Aluminum PCBs are typically used in applications that require good thermal dissipation, such as power electronics and LED lighting.
3. What is the most commonly used PCB material?
The most commonly used PCB material is FR-4, which is a composite material made of woven fiberglass cloth and epoxy resin. It provides a good balance of insulation properties, mechanical strength, thermal stability, and affordability.
4. How does the choice of PCB material affect the cost of the finished product?
The choice of PCB material has a significant impact on the cost of the finished product. Cheaper materials like phenolic paper and CEM-1 are often used in low-cost consumer electronics to keep prices down, while more expensive materials like aluminum may be used in high-performance applications where thermal dissipation is critical.
5. Are there eco-friendly alternatives to traditional PCB materials?
Yes, researchers are developing eco-friendly PCB materials that are biodegradable or recyclable to reduce the environmental footprint of electronic devices. These materials are still in the early stages of development and are not yet widely available in the market.
Conclusion
The choice of materials used in the construction of cheap circuit boards is crucial as it determines the performance, reliability, and cost of the final product. FR-4 is the most commonly used material for cheap PCBs due to its good insulation properties, high mechanical strength, and affordability. Other materials like CEM-1, phenolic paper, and aluminum are used in specific applications based on their unique properties and cost considerations.
As electronic devices continue to evolve, there is a growing demand for new PCB materials that can provide better high-frequency performance, eco-friendliness, and compatibility with advanced manufacturing processes like 3D printing. Researchers and manufacturers are working to develop new materials that can meet these demands while keeping costs down.
Ultimately, the choice of PCB material depends on the specific requirements of the application, the manufacturing process, and cost considerations. By understanding the properties and trade-offs of different PCB materials, designers and manufacturers can make informed decisions that balance performance, reliability, and cost to create high-quality electronic products at an affordable price point.
No responses yet