Introduction to PCB Design
Printed Circuit Board (PCB) design is a crucial aspect of electronic product development. A well-designed PCB ensures the proper functioning, reliability, and manufacturability of the final product. In this comprehensive guide, we will explore essential tips and tricks to help you create high-quality PCB designs that meet your project requirements.
Understanding the Basics of PCB Design
Before diving into specific tips and tricks, it’s important to grasp the fundamentals of PCB design. A PCB is a flat board made of insulating material, such as fiberglass or plastic, with conductive copper traces etched onto its surface. These traces connect various electronic components, such as resistors, capacitors, and integrated circuits (ICs), to form a complete circuit.
PCB design involves several key steps:
- Schematic capture: Creating a schematic diagram that represents the electrical connections between components.
- Component placement: Arranging the components on the PCB layout for optimal performance and manufacturability.
- Routing: Connecting the components with copper traces while adhering to design rules and constraints.
- Design rule checking (DRC): Verifying that the PCB layout meets all the necessary design rules and guidelines.
- Generating manufacturing files: Creating the necessary files, such as Gerber and drill files, for PCB fabrication.
Tips for Schematic Capture
Use a Consistent Naming Convention
Adopt a clear and consistent naming convention for your components, nets, and ports. This practice improves readability and makes it easier to navigate and debug your schematic. Consider using meaningful prefixes or suffixes to indicate the component type or function.
Organize Your Schematic
Arrange your schematic in a logical and organized manner. Group related components together and use hierarchical blocks to simplify complex designs. A well-structured schematic enhances clarity and facilitates collaboration among team members.
Utilize Schematic Symbols Effectively
Choose appropriate schematic symbols that accurately represent the components in your design. Ensure that the symbols are properly labeled with the correct pin names and numbers. If necessary, create custom symbols for specialized components.
Perform Electrical Rule Checks (ERC)
Conduct ERC on your schematic to identify potential issues, such as unconnected pins, short circuits, or missing power connections. Resolving these problems early in the design process saves time and effort during the PCB layout phase.
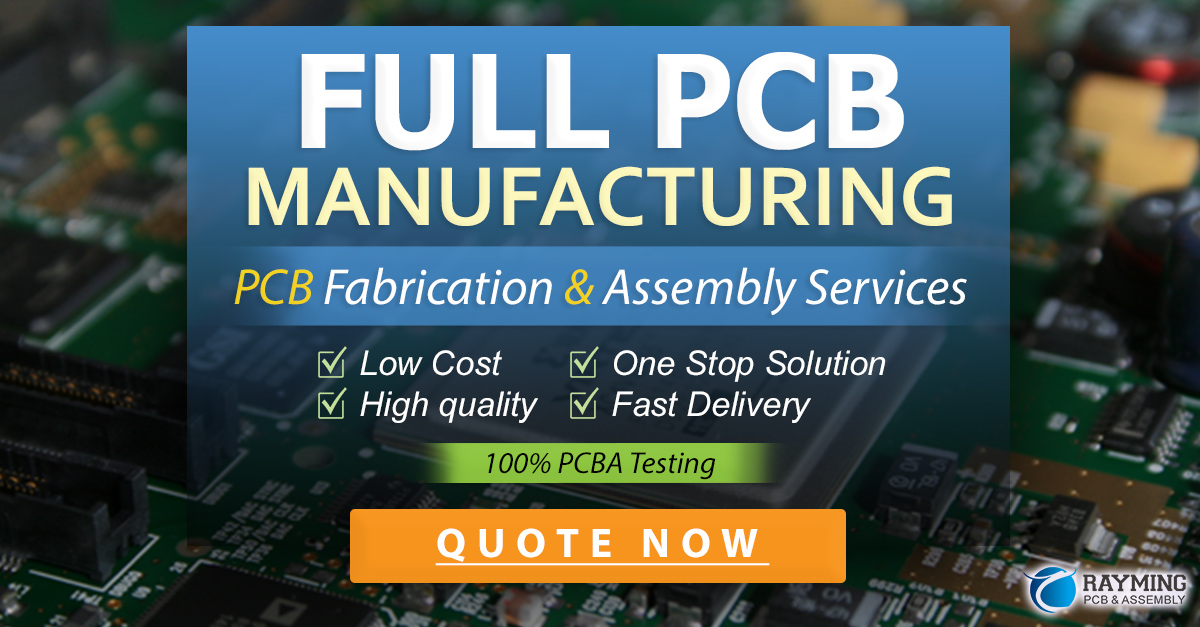
Tips for Component Placement
Consider Component Footprints
Select appropriate component footprints that match the physical dimensions and pin configurations of the actual components. Verify that the footprints are compatible with the manufacturing capabilities of your PCB fabricator.
Optimize Component Positioning
Place components in a way that minimizes the overall PCB size and reduces the complexity of routing. Consider the signal flow and place related components close to each other to minimize trace lengths and improve signal integrity.
Maintain Proper Clearances
Ensure adequate clearances between components, traces, and board edges to avoid manufacturing issues and potential short circuits. Adhere to the minimum clearance requirements specified by your PCB fabricator.
Utilize Component Orientation
Orient components in a consistent and logical manner to enhance readability and facilitate assembly. Align component reference designators and values in the same direction for easy identification during manufacturing and debugging.
Tips for Routing
Define Appropriate Trace Widths
Select trace widths based on the current carrying requirements and signal integrity considerations. Use wider traces for power and ground connections to minimize voltage drop and improve current handling capacity. Use narrower traces for high-speed signals to reduce parasitic effects.
Minimize Trace Lengths
Keep trace lengths as short as possible to reduce signal degradation, crosstalk, and electromagnetic interference (EMI). Avoid unnecessary meanders and route traces directly between connected components.
Implement Proper Grounding Techniques
Create a solid ground plane to provide a low-impedance return path for signals. Use ground pours or grids to minimize ground loops and improve EMI performance. Ensure that all ground connections are properly connected to the ground plane.
Route Differential Pairs Carefully
When dealing with differential signals, such as USB or Ethernet, route the positive and negative traces closely together with equal lengths. Maintain a consistent spacing between the traces to ensure proper signal integrity and minimize crosstalk.
Tips for Design Rule Checking (DRC)
Define Design Rules
Establish a comprehensive set of design rules that govern the various aspects of your PCB layout, such as trace widths, clearances, via sizes, and copper pour settings. Ensure that these rules comply with the manufacturing capabilities of your PCB fabricator.
Run DRC Regularly
Perform DRC frequently throughout the PCB layout process to identify and resolve any rule violations. Addressing these issues early prevents costly redesigns and manufacturing delays.
Review DRC Reports
Carefully review the DRC reports generated by your PCB design software. Investigate each violation and determine the appropriate course of action. Some violations may require layout modifications, while others may necessitate design rule adjustments.
Tips for Generating Manufacturing Files
Use Standard File Formats
Generate manufacturing files, such as Gerber and drill files, in industry-standard formats. Consult with your PCB fabricator to determine their preferred file formats and requirements.
Include Necessary Layers
Ensure that your manufacturing files include all the necessary layers, such as copper layers, solder mask, silkscreen, and drill layers. Provide a clear layer stackup specification to avoid confusion during fabrication.
Verify File Integrity
Double-check the generated manufacturing files for completeness and accuracy. Verify that the files match your intended design and include all the required information for successful manufacturing.
FAQ
1. What is the importance of a well-designed PCB?
A well-designed PCB is crucial for the proper functioning, reliability, and manufacturability of an electronic product. It ensures that the components are connected correctly, signal integrity is maintained, and the board can be manufactured efficiently.
2. How can I improve the readability of my schematic?
To improve the readability of your schematic, use a consistent naming convention for components and nets, organize the schematic in a logical manner, and utilize hierarchical blocks for complex designs. Additionally, choose appropriate schematic symbols and label them clearly.
3. What factors should I consider when placing components on a PCB?
When placing components on a PCB, consider factors such as component footprints, positioning for optimal routing, maintaining proper clearances, and orienting components consistently. Place related components close together to minimize trace lengths and improve signal integrity.
4. How can I ensure the manufacturability of my PCB design?
To ensure the manufacturability of your PCB design, adhere to the design rules and guidelines provided by your PCB fabricator. Define appropriate trace widths, clearances, and via sizes. Regularly run DRC to identify and resolve any rule violations.
5. What are the essential files required for PCB manufacturing?
The essential files required for PCB manufacturing include Gerber Files, drill files, and a layer stackup specification. Gerber files represent the copper layers, solder mask, and silkscreen, while drill files contain information about the hole sizes and locations. The layer stackup specification defines the arrangement and thickness of the PCB Layers.
Conclusion
Designing a high-quality PCB requires attention to detail, adherence to best practices, and a thorough understanding of the design process. By following the tips and tricks outlined in this article, you can create PCB designs that are functional, reliable, and manufacturable.
Remember to focus on schematic capture, component placement, routing, design rule checking, and generating accurate manufacturing files. Regularly communicate with your PCB fabricator to ensure that your design meets their requirements and capabilities.
Continuous learning and staying updated with the latest industry trends and technologies will help you refine your PCB design skills. Embrace the challenges and opportunities that PCB design presents, and strive to create innovative and efficient electronic products.
PCB Design Stage | Key Considerations |
---|---|
Schematic Capture | – Consistent naming convention – Organized schematic structure – Appropriate schematic symbols – Electrical rule checks (ERC) |
Component Placement | – Component footprints – Optimal positioning – Proper clearances – Consistent orientation |
Routing | – Appropriate trace widths – Minimized trace lengths – Proper grounding techniques – Differential pair routing |
Design Rule Checking (DRC) | – Comprehensive design rules – Regular DRC runs – Review of DRC reports |
Generating Manufacturing Files | – Standard file formats – Inclusion of necessary layers – Verification of file integrity |
By following these vital PCB design tips and tricks, you can create robust and reliable electronic products that meet your project requirements and exceed customer expectations. Happy designing!
No responses yet