Introduction to LED PCBs
LED PCBs (Printed Circuit Boards) are specialized circuit boards designed to support and connect Light Emitting Diodes (LEDs). These boards are essential components in various electronic devices and lighting applications, providing a stable and efficient platform for LEDs to function optimally. In this comprehensive guide, we will explore the world of LED PCBs, covering their basics, manufacturing process, applications, and frequently asked questions.
Understanding the Basics of LED PCBs
What are LEDs?
LEDs are semiconductor devices that emit light when an electric current passes through them. They are known for their energy efficiency, long lifespan, and versatility in terms of color and brightness. LEDs have revolutionized the lighting industry and are widely used in various applications, from general lighting to electronic displays and automotive lighting.
The Role of PCBs in LED Lighting
PCBs play a crucial role in LED lighting by providing a stable and reliable platform for the LEDs to be mounted and connected. The main functions of LED PCBs include:
- Mechanical support: PCBs act as a solid base for the LEDs, ensuring they are securely held in place.
- Electrical connectivity: PCBs feature conductive traces that allow electricity to flow to the LEDs, enabling them to illuminate.
- Heat dissipation: PCBs often incorporate heat dissipation features, such as metal core or thermal vias, to effectively remove heat generated by the LEDs, ensuring optimal performance and longevity.
Types of LED PCBs
There are several types of LED PCBs, each designed to cater to specific requirements and applications:
- Rigid PCBs: These are the most common type of LED PCBs, featuring a solid, inflexible substrate material, such as FR-4 or aluminum.
- Flexible PCBs: These PCBs are made from flexible materials, allowing them to bend and conform to various shapes and sizes. They are ideal for applications where space is limited or where the PCB needs to fit into a specific form factor.
- Metal Core PCBs (MCPCBs): These PCBs feature a metal core, typically aluminum, which acts as an excellent heat dissipator. MCPCBs are commonly used in high-power LED applications where heat management is critical.
- High-Density Interconnect (HDI) PCBs: These PCBs feature fine-pitch traces and micro-vias, allowing for higher component density and more complex designs. HDI PCBs are often used in advanced LED lighting applications, such as miniature displays or high-resolution signage.
LED PCB Manufacturing Process
The manufacturing process of LED PCBs involves several key steps:
- PCB Design: The first step is to design the PCB layout using specialized software, such as Altium Designer or Eagle. The design includes the placement of components, routing of traces, and the incorporation of heat dissipation features.
- Substrate Preparation: The chosen substrate material, such as FR-4 or aluminum, is cut to the desired size and shape.
- Copper Lamination: A thin layer of copper is laminated onto the substrate using heat and pressure.
- Photoresist Application: A photosensitive resist is applied to the copper layer, which will later be used to create the desired circuit pattern.
- Exposure and Development: The photoresist is exposed to UV light through a photomask, which contains the circuit pattern. The exposed areas of the photoresist are then removed during the development process, leaving the desired circuit pattern on the copper layer.
- Etching: The exposed copper is etched away using a chemical solution, leaving only the desired circuit pattern on the substrate.
- Soldermask Application: A soldermask layer is applied to the PCB to protect the copper traces and prevent short circuits.
- Silkscreen Printing: A silkscreen layer is printed onto the PCB to add component labels, logos, and other markings.
- Surface Finish: A surface finish, such as HASL (Hot Air Solder Leveling) or ENIG (Electroless Nickel Immersion Gold), is applied to the exposed copper to protect it from oxidation and enhance solderability.
- Assembly: The LED components are soldered onto the PCB using SMT (Surface Mount Technology) or THT (Through-Hole Technology) techniques.
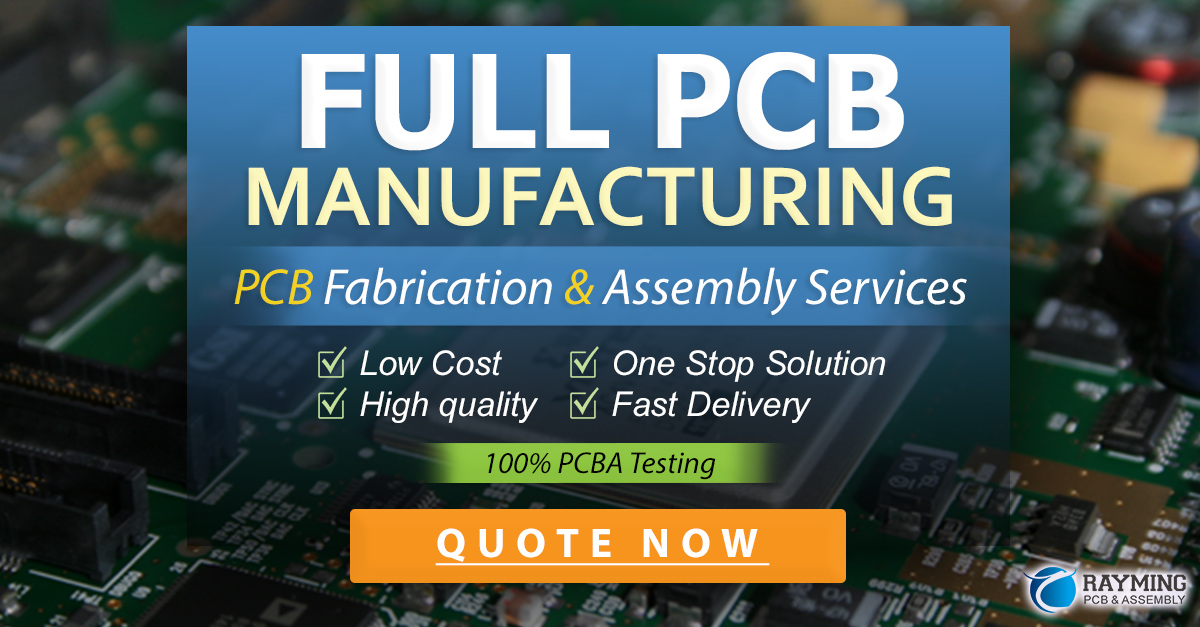
Applications of LED PCBs
LED PCBs find applications in a wide range of industries and products:
- General Lighting: LED PCBs are used in various lighting fixtures, such as bulbs, tubes, and panels, for residential, commercial, and industrial lighting.
- Automotive Lighting: LED PCBs are extensively used in automotive lighting applications, including headlights, taillights, and interior lighting.
- Electronic Displays: LED PCBs are integral components in electronic displays, such as digital signage, billboards, and video walls.
- Backlighting: LED PCBs are used for backlighting in LCD displays, including televisions, monitors, and mobile devices.
- Medical Devices: LED PCBs are used in medical devices, such as endoscopes, surgical lights, and phototherapy equipment.
- Horticulture: LED PCBs are used in horticultural lighting systems to promote plant growth and development in indoor farming and greenhouse applications.
Advantages of LED PCBs
LED PCBs offer several advantages over traditional lighting solutions:
- Energy Efficiency: LEDs are highly energy-efficient, consuming significantly less power than incandescent or fluorescent lights.
- Long Lifespan: LEDs have a much longer lifespan compared to traditional lighting sources, often lasting up to 50,000 hours or more.
- Customization: LED PCBs can be designed and manufactured to meet specific requirements, such as size, shape, and color temperature.
- Environmental Friendliness: LEDs do not contain hazardous materials, such as mercury, making them a more environmentally friendly lighting option.
- Instant On/Off: LEDs turn on and off instantly, without the need for a warm-up period, making them ideal for applications that require frequent switching.
Challenges and Considerations
While LED PCBs offer numerous benefits, there are some challenges and considerations to keep in mind:
- Heat Management: LEDs generate heat, which can negatively impact their performance and lifespan if not properly managed. Effective heat dissipation through PCB design and the use of thermal management materials is crucial.
- Color Consistency: Ensuring color consistency across multiple LED PCBs can be challenging due to variations in LED binning and manufacturing processes.
- Driver Compatibility: LED PCBs require compatible drivers to ensure proper operation and optimal performance. Selecting the right driver is essential for a successful LED lighting solution.
- Cost: While the cost of LEDs has decreased significantly over the years, LED PCBs can still be more expensive than traditional lighting solutions, particularly for high-power or specialized applications.
Frequently Asked Questions (FAQ)
1. What is the difference between rigid and flexible LED PCBs?
Rigid LED PCBs are made from a solid, inflexible substrate material, such as FR-4 or aluminum, while flexible LED PCBs are made from flexible materials that allow them to bend and conform to various shapes and sizes. Flexible LED PCBs are ideal for applications where space is limited or where the PCB needs to fit into a specific form factor.
2. What is a Metal Core PCB (MCPCB), and when is it used?
A Metal Core PCB (MCPCB) is a type of LED PCB that features a metal core, typically aluminum, which acts as an excellent heat dissipator. MCPCBs are commonly used in high-power LED applications where heat management is critical, such as high-brightness lighting fixtures or automotive lighting.
3. What are the advantages of using LED PCBs over traditional lighting solutions?
LED PCBs offer several advantages over traditional lighting solutions, including energy efficiency, long lifespan, customization options, environmental friendliness, and instant on/off capabilities. These benefits make LED PCBs an attractive choice for a wide range of lighting applications.
4. How do I select the right LED driver for my LED PCB?
When selecting an LED driver for your LED PCB, consider factors such as input voltage, output current, dimming capabilities, and form factor. It is essential to choose a driver that is compatible with your LED PCB and meets the specific requirements of your application. Consulting with the LED PCB manufacturer or a lighting expert can help ensure you select the most suitable driver.
5. What is the typical lifespan of an LED PCB?
The lifespan of an LED PCB depends on several factors, including the quality of the components, the operating environment, and the thermal management of the system. On average, LED PCBs can last up to 50,000 hours or more, which is significantly longer than traditional lighting sources such as incandescent or fluorescent lights. However, proper heat management and adherence to the manufacturer’s guidelines are crucial to ensuring the longevity of an LED PCB.
Conclusion
LED PCBs are essential components in modern lighting solutions, offering numerous benefits such as energy efficiency, long lifespan, and customization options. Understanding the basics of LED PCBs, their manufacturing process, and their applications is crucial for anyone involved in the design, development, or implementation of LED lighting systems.
By considering factors such as heat management, color consistency, and driver compatibility, engineers and designers can create innovative and effective LED lighting solutions for a wide range of industries and applications. As the demand for energy-efficient and sustainable lighting continues to grow, the importance of LED PCBs will only increase, driving further advancements in technology and design.
No responses yet