Introduction to Nitrogen Reflow Soldering
Nitrogen reflow soldering is a process used in the assembly of printed circuit boards (PCBs) where the soldering takes place in a nitrogen-rich environment. This method has gained popularity in recent years due to its ability to produce high-quality solder joints with minimal defects. In this ultimate guide, we will explore the basics of nitrogen reflow soldering, its advantages, the equipment used, and best practices for achieving optimal results.
What is Nitrogen Reflow Soldering?
Nitrogen reflow soldering is a type of reflow soldering process that uses nitrogen gas to create an inert atmosphere during the soldering process. In a typical reflow soldering process, the PCB and components are heated to a specific temperature profile, causing the solder paste to melt and form a connection between the components and the PCB. However, in a nitrogen reflow soldering process, nitrogen gas is introduced into the reflow oven, displacing the oxygen and creating an inert environment.
The nitrogen atmosphere helps to prevent oxidation of the solder joints, which can lead to defects such as solder balls, bridging, and poor wetting. By reducing the oxygen content in the reflow oven, nitrogen reflow soldering can produce cleaner, stronger, and more reliable solder joints.
Advantages of Nitrogen Reflow Soldering
Nitrogen reflow soldering offers several advantages over traditional reflow soldering methods. Some of the key benefits include:
-
Reduced Oxidation: The nitrogen atmosphere prevents oxidation of the solder joints, resulting in cleaner and stronger connections.
-
Improved Wetting: Nitrogen reflow soldering promotes better wetting of the solder to the components and PCB pads, leading to more reliable solder joints.
-
Fewer Defects: By reducing oxidation and improving wetting, nitrogen reflow soldering minimizes common defects such as solder balls, bridging, and poor adhesion.
-
Increased Reliability: The high-quality solder joints produced by nitrogen reflow soldering contribute to improved overall reliability of the assembled PCBs.
-
Wider Process Window: Nitrogen reflow soldering allows for a wider range of temperature profiles and process parameters, providing greater flexibility in the assembly process.
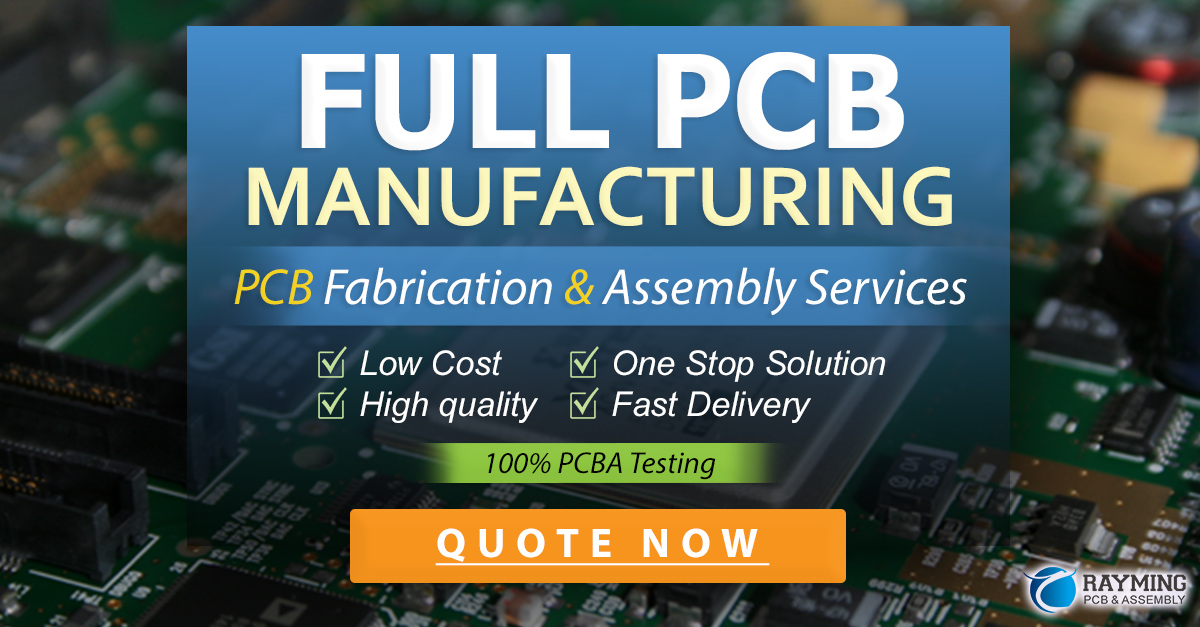
Equipment for Nitrogen Reflow Soldering
To implement nitrogen reflow soldering, specialized equipment is required. The main components of a nitrogen reflow soldering system include:
-
Reflow Oven: A reflow oven capable of maintaining a controlled temperature profile and an inert atmosphere is essential for nitrogen reflow soldering. The oven should have the ability to introduce and maintain a high concentration of nitrogen gas during the soldering process.
-
Nitrogen Generator or Supply: A reliable source of high-purity nitrogen gas is necessary for creating the inert atmosphere in the reflow oven. This can be achieved through the use of a nitrogen generator or a supply of compressed nitrogen gas.
-
Oxygen Analyzer: An oxygen analyzer is used to monitor and control the oxygen content within the reflow oven. Maintaining a low oxygen level (typically below 100 ppm) is critical for achieving the benefits of nitrogen reflow soldering.
-
Conveyors and Handling Equipment: Conveyors and handling equipment are used to transport the PCBs through the reflow oven and ensure proper positioning during the soldering process.
Nitrogen Reflow Soldering Process
The nitrogen reflow soldering process involves several key steps:
-
PCB Preparation: The PCB is cleaned and the solder paste is applied to the pads using a stencil or screen printing process.
-
Component Placement: The components are placed onto the PCB using pick-and-place machines or manual methods.
-
Nitrogen Purging: The PCB is loaded into the reflow oven, and nitrogen gas is introduced to displace the oxygen and create an inert atmosphere.
-
Temperature Profiling: The reflow oven follows a specific temperature profile, heating the PCB and components to the required temperatures for solder melting and joint formation.
-
Cooling: After the peak temperature is reached, the PCB is cooled down, allowing the solder joints to solidify.
-
Inspection: The assembled PCB is inspected for defects and quality control purposes.
Best Practices for Nitrogen Reflow Soldering
To achieve the best results with nitrogen reflow soldering, consider the following best practices:
-
Optimize Nitrogen Concentration: Maintain a low oxygen content (< 100 ppm) in the reflow oven to maximize the benefits of nitrogen reflow soldering.
-
Proper Temperature Profiling: Develop and follow an appropriate temperature profile for your specific PCB and components to ensure proper solder melting and joint formation.
-
Solder Paste Selection: Choose a solder paste that is compatible with nitrogen reflow soldering and has the desired properties for your application.
-
Cleanliness: Maintain a clean environment throughout the assembly process to minimize contamination and defects.
-
Regular Maintenance: Perform regular maintenance on the reflow oven, nitrogen generator, and other equipment to ensure consistent performance and results.
Frequently Asked Questions (FAQ)
-
What is the optimal nitrogen concentration for reflow soldering?
The optimal nitrogen concentration for reflow soldering is typically below 100 parts per million (ppm) of oxygen. This low oxygen content helps to prevent oxidation and ensure high-quality solder joints. -
Can nitrogen reflow soldering be used with lead-free solder?
Yes, nitrogen reflow soldering is compatible with lead-free solder. In fact, it can be particularly beneficial for lead-free soldering processes, as lead-free solders are more susceptible to oxidation and defects. -
How does nitrogen reflow soldering compare to traditional reflow soldering in terms of cost?
Nitrogen reflow soldering does require additional equipment and nitrogen gas, which can increase the initial setup costs compared to traditional reflow soldering. However, the improved solder joint quality and reduced defects can lead to long-term cost savings through higher yields and reduced rework. -
Is nitrogen reflow soldering suitable for all types of PCBs and components?
Nitrogen reflow soldering can be used for a wide range of PCBs and components. However, it is particularly beneficial for assemblies with fine-pitch components, high-density layouts, or sensitive devices that are prone to oxidation. -
Can existing reflow ovens be retrofitted for nitrogen reflow soldering?
Many existing reflow ovens can be retrofitted with nitrogen gas injection systems and oxygen analyzers to enable nitrogen reflow soldering. However, it is important to consult with the equipment manufacturer or a qualified technician to ensure compatibility and proper installation.
Conclusion
Nitrogen reflow soldering is a powerful technique for achieving high-quality solder joints in PCB assembly. By creating an inert atmosphere with nitrogen gas, this process reduces oxidation, improves wetting, and minimizes defects. Implementing nitrogen reflow soldering requires specialized equipment and adherence to best practices, but the benefits in terms of reliability and performance make it a valuable investment for many electronics manufacturers.
As the demand for higher-density PCBs and reliable solder joints continues to grow, nitrogen reflow soldering is likely to become an increasingly important tool in the PCB assembly industry. By understanding the principles, advantages, and best practices of this technique, manufacturers can optimize their assembly processes and deliver products that meet the highest standards of quality and performance.
No responses yet