Introduction to PCB Masses
Printed circuit boards (PCBs) are the backbone of modern electronics, providing the physical structure and electrical connections for components in devices ranging from smartphones to satellites. One key characteristic of a PCB is its mass or weight. The mass of a PCB can impact many aspects of the end product, including:
- Overall device weight and portability
- Mechanical strength and durability
- Thermal management and heat dissipation
- Manufacturing costs and logistics
In this article, we’ll dive deep into the topic of PCB masses. We’ll explore what factors influence a PCB’s mass, typical mass ranges for different types of PCBs, design considerations around mass, and more. By the end, you’ll have a thorough understanding of this important PCB specification.
Factors That Determine a PCB’s Mass
A PCB’s mass is determined by a combination of its physical dimensions, materials, and construction. Let’s break down each of these factors:
PCB dimensions
The most obvious factor influencing a PCB’s mass is its size – the larger the PCB, the more it will weigh, all else being equal. A PCB’s dimensions are typically driven by:
- The size and number of components it needs to accommodate
- The device’s space constraints and form factor
- Required features like mounting holes, connectors, etc.
PCB dimensions are usually specified in terms of length, width, and thickness. Thickness is typically standardized to 0.8mm, 1.0mm, 1.2mm, 1.6mm, or 2.4mm for rigid PCBs. Flexible and rigid-flex PCBs can be thinner.
PCB base material
The base material a PCB is made of also has a big impact on its mass. The most common base material for rigid PCBs is FR-4, a glass-reinforced epoxy laminate. FR-4 has a density of around 1.85 g/cm^3^.
Other base material options include:
- Polyimide (PI) for flexible PCBs
- High-Tg FR-4 or polyimide for high-temp applications
- Teflon, ceramics, or metal core materials for specialty use cases
Each material has a different density that contributes to the overall mass.
Copper Layers and Thickness
Most PCBs have one or more copper layers that form the circuit traces and planes. The number of layers and the thickness of the copper have a significant impact on mass, since copper is much denser than FR-4, at 8.96 g/cm^3^.
Typical copper thicknesses are specified in ounces per square foot:
Copper Thickness | Microns (μm) | Typical Uses |
---|---|---|
0.5 oz/ft^2^ | 17.5 | Very thin, flexible PCBs |
1 oz/ft^2^ | 35 | Most common for signal layers |
2 oz/ft^2^ | 70 | Power delivery, high current |
3 oz/ft^2^ | 105 | Very high current applications |
4 oz/ft^2^ | 140 | Extreme current, e.g. welding |
More and thicker copper layers add significantly to the PCB mass.
Solder Mask and Silkscreen
Most PCBs have a layer of solder mask, usually green, applied over the bare copper. This layer is very thin, around 0.02mm, so it does not add much mass.
Silkscreen is used to add text and graphics onto the PCB surface. It is also a very thin layer that doesn’t contribute meaningfully to total mass.
Components and Solder
Finally, once the bare PCB is populated with components and solder, this adds to the overall assembly mass. The mass of the components can rival or exceed that of the bare board itself, especially for dense SMT assemblies. Through-hole components with large metal leads can also add noticeable mass.
Typical PCB Mass Ranges
So what is a typical mass for a PCB? It depends on the size, layer count, and other factors discussed above. Here are some very rough estimates for common PCB Types:
PCB Type | Typical Mass Range |
---|---|
Business card size, 2 layer | 2-5 grams |
Smartphone main board, 6-10 layer | 10-25 grams |
Laptop motherboard, 6-12 layer | 100-250 grams |
Large server blade, 24 layer | 500-1500 grams |
Very large PCBs over 200 cm^2^ in area can weigh over a kilogram. On the other end, tiny PCBs under 1 cm^2^ may weigh just a fraction of a gram.
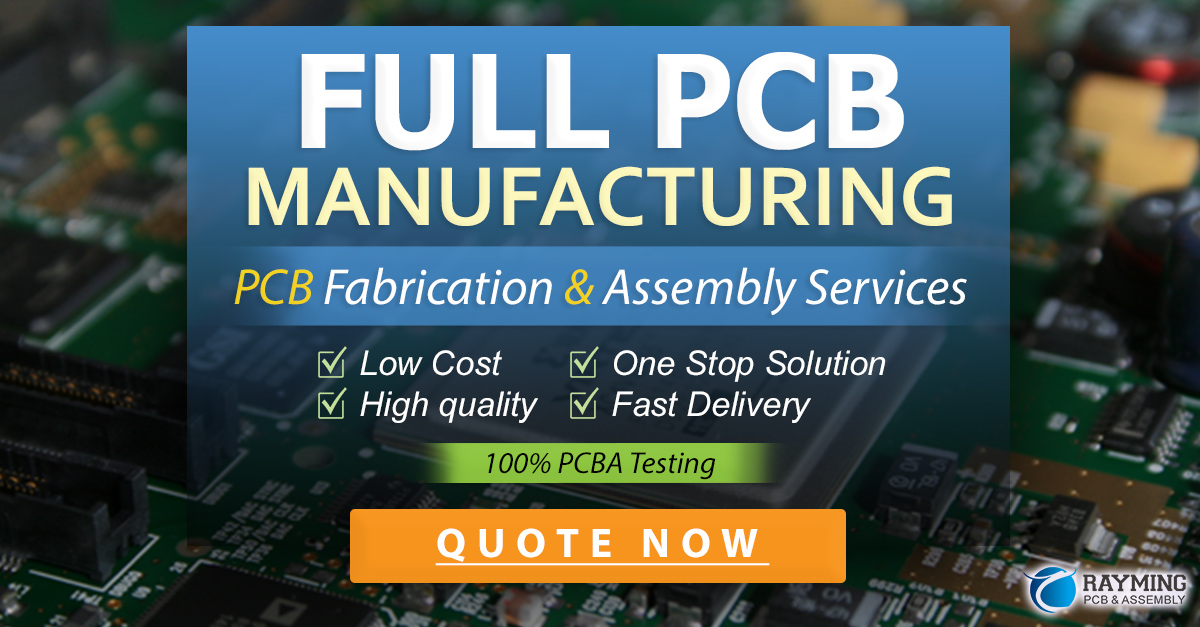
Design Considerations for PCB Mass
PCB designers need to consider mass as one of many requirements that influence the design. Some key design considerations related to mass include:
Meeting Mass Targets
Many products have an overall weight budget that the PCB assembly needs to fit within. Designers need to work with mechanical engineers to allocate mass between the PCB, enclosure, battery, and other components.
Minimizing the PCB size and eliminating unnecessary copper pours are two ways to reduce PCB mass when needed. Using thinner base material can also help in some cases.
Mechanical Strength
PCBs need to be strong enough to withstand vibration, shock, and bending forces. In general, a thicker, heavier PCB will be stronger than a thin, light one.
Using thicker base material, more layers, or a stiffener can increase strength at the cost of added mass. Designers must find the right balance to meet reliability requirements while staying within weight limits.
Thermal Management
Heavier copper layers are often used to spread heat across a PCB and away from hot components. Increasing copper weight to meet thermal performance needs is often at odds with mass reduction goals.
Metal core PCBs or those with large aluminum heatsinks can be very heavy but may be necessary to cool high-power processors, FPGAs, etc.
Cost and Logistics
PCB mass impacts the cost of raw materials, especially the copper and laminates. Heavier boards are more expensive.
Weight also factors into the cost of shipping PCBs from the fab to the assembly house and eventually to the end customer. Choosing lightweight PCB designs can provide cost savings across the supply chain.
Measuring and Reporting PCB Mass
Most PCB manufacturers can provide accurate mass measurements for bare PCBs using precision scales. The Gerber data can also be used to estimate the mass during design, based on the material densities and the PCB area.
Component and assembly masses are typically measured and reported separately. The final assembly mass is the sum of the bare board, components, and solder.
FAQ
What is the typical density of FR-4 PCB Material?
FR-4 has a density of approximately 1.85 grams per cubic centimeter (g/cm^3^). This means a 10×10 cm PCB that is 1.6 mm thick would have a mass of about 30 grams, not including copper, solder mask, or silkscreen.
How much does the copper on a PCB weigh?
Copper weighs 8.96 grams per cubic centimeter, making it much heavier than the FR-4 material. A square foot of 1-ounce copper weighs about 0.46 kg.
For example, a 4-layer PCB with 1 oz copper on all layers would have about 1.84 kg of copper per square foot of PCB area. The actual weight is reduced by the areas without copper pours.
Are heavier PCBs always stronger?
In general, a thicker, heavier PCB will be more rigid and resistant to bending and vibration than a thinner, lighter board. The span between mounting points, number of layers, and stiffness of the material also play a role.
However, heavier does not always mean stronger. Strategic placement of mounting holes, stiffeners, and thick material can provide high strength without excess mass.
How can I reduce my PCB assembly weight?
There are a few ways to reduce PCB assembly mass during design:
- Minimize the overall board dimensions
- Use thinner base material
- Reduce layer count if possible
- Optimize copper pours and plane areas
- Select lightweight components
- Avoid large heatsinks or metal stiffeners
Designers must carefully balance weight against other requirements like strength, thermal performance, and signal integrity.
How does PCB mass impact cost?
Heavier PCBs require more raw material, especially copper, which increases the cost per board. Fabrication and assembly costs may also be higher for heavier, thicker, or stiffer boards, due to limitations of automated equipment.
Shipping costs are directly tied to mass, so heavier PCBs are more expensive to transport. In high volumes, even small reductions in PCB mass can lead to significant cost savings.
Conclusion
The mass of a printed circuit board is an important specification that impacts many aspects of the final product, from mechanical strength to thermal performance to cost. PCB mass depends on the physical dimensions, materials, copper weight, and component loading.
Typical PCB masses range from under a gram for tiny boards up to a kilogram or more for very large, complex boards. Designers must carefully balance PCB mass against other requirements to meet product weight targets and cost goals.
By understanding the factors that influence PCB mass and considering mass during the design process, engineers can optimize their PCBs to strike the right balance between light weight, high performance, and low cost.
No responses yet