What are PCBs?
PCBs are thin, flat boards made of insulating material, such as fiberglass or plastic, with conductive pathways etched onto them. These pathways, also known as traces, connect various electronic components, such as resistors, capacitors, and integrated circuits (ICs), to form a complete circuit. PCBs provide a stable and efficient platform for these components to function together, allowing for the creation of complex electronic devices.
History of PCBs
The concept of PCBs dates back to the early 20th century. In 1903, Albert Hanson, a German inventor, filed a patent for a “printed wire” that described a method of using conductive ink to print circuits on an insulating material. However, it wasn’t until the 1940s that PCBs began to gain widespread use.
During World War II, the United States military required a more reliable and efficient method of connecting electronic components in their equipment. Paul Eisler, an Austrian engineer, developed a process for etching conductive pathways onto a non-conductive substrate, which became the foundation for modern PCB manufacturing.
In the decades that followed, PCB technology continued to evolve. The introduction of through-hole technology in the 1950s allowed for the creation of double-sided PCBs, while the development of Surface-mount technology (SMT) in the 1980s enabled the production of smaller, more complex boards.
PCB Manufacturing Process
The PCB manufacturing process involves several steps, each of which is crucial to ensuring the quality and reliability of the final product. The main steps in PCB manufacturing include:
-
Design: The PCB design is created using specialized software, such as Altium Designer or Eagle. The design includes the layout of the conductive pathways, the placement of components, and any necessary labels or markings.
-
Printing: The PCB design is printed onto a photosensitive film, which is used to transfer the design onto the copper-clad laminate board.
-
Etching: The laminate board is exposed to ultraviolet light through the photosensitive film, which hardens the areas of the board that will become the conductive pathways. The unexposed areas are then removed using a chemical etching process, leaving only the desired conductive pathways.
-
Drilling: Holes are drilled into the board to accommodate through-hole components and to create vias, which are used to connect traces on different layers of the board.
-
Plating: The holes and vias are plated with a conductive material, such as copper, to ensure proper electrical connectivity.
-
Solder Mask Application: A protective layer, called a solder mask, is applied to the board to prevent short circuits and to protect the conductive pathways from damage.
-
Silkscreen Printing: Labels, logos, and other markings are printed onto the board using a silkscreen printing process.
-
Surface Mount Assembly: Surface-mount components are placed onto the board using automated pick-and-place machines, and then soldered onto the board using a reflow soldering process.
-
Through-Hole Assembly: Through-hole components are inserted into the drilled holes and soldered onto the board using a wave soldering process.
-
Testing and Inspection: The completed PCB is tested and inspected to ensure proper functionality and adherence to quality standards.
Types of PCBs
There are several types of PCBs, each with its own unique characteristics and applications. The main types of PCBs include:
-
Single-sided PCBs: These boards have conductive pathways on only one side of the insulating substrate. Single-sided PCBs are the simplest and least expensive type of PCB, making them suitable for basic electronic devices.
-
Double-sided PCBs: These boards have conductive pathways on both sides of the insulating substrate, allowing for more complex circuits and higher component density. Double-sided PCBs are commonly used in consumer electronics, such as smartphones and laptops.
-
Multi-layer PCBs: These boards consist of multiple layers of insulating substrate with conductive pathways on each layer. The layers are interconnected using vias, which are conductive holes drilled through the board. Multi-layer PCBs are used in high-performance electronic devices, such as servers, aerospace equipment, and medical devices.
-
Flexible PCBs: These boards are made of flexible insulating material, such as polyimide, allowing them to bend and conform to various shapes. Flexible PCBs are used in applications where space is limited or where the board needs to fit into a specific form factor, such as in wearable devices or Automotive Electronics.
-
Rigid-Flex PCBs: These boards combine the benefits of both rigid and flexible PCBs, featuring rigid sections for component mounting and flexible sections for interconnections. Rigid-flex PCBs are used in applications that require both stability and flexibility, such as in aerospace and military equipment.
Importance of PCBs in Various Industries
PCBs are essential components in a wide range of industries, each with its own unique requirements and challenges. Some of the key industries that rely heavily on PCBs include:
Consumer Electronics
The consumer electronics industry is one of the largest users of PCBs. From smartphones and tablets to gaming consoles and smart home devices, PCBs are the foundation upon which these devices are built. The ever-increasing demand for smaller, more powerful, and feature-rich consumer electronics has driven the development of advanced PCB technologies, such as high-density interconnect (HDI) and embedded component PCBs.
Automotive Electronics
The automotive industry has seen a significant increase in the use of electronic systems in recent years. PCBs are used in various automotive applications, such as engine control units (ECUs), infotainment systems, and advanced driver assistance systems (ADAS). The harsh operating conditions in automotive environments, such as extreme temperatures, vibrations, and moisture, require the use of specialized PCBs that can withstand these conditions.
Medical Devices
PCBs play a crucial role in the medical device industry, enabling the development of advanced diagnostic and therapeutic equipment. From patient monitoring systems and medical imaging devices to implantable devices and wearable health monitors, PCBs are essential components in ensuring the accuracy, reliability, and safety of these devices. The medical device industry has stringent requirements for PCB manufacturing, including the use of biocompatible materials and adherence to strict quality control standards.
Aerospace and Defense
The aerospace and defense industries rely on PCBs for a wide range of applications, including avionics, communication systems, and weapons systems. PCBs used in these industries must be able to withstand extreme environmental conditions, such as high altitudes, radiation, and electromagnetic interference (EMI). The use of advanced PCB technologies, such as high-frequency laminates and embedded resistors and capacitors, is common in aerospace and defense applications.
Industrial Electronics
PCBs are used in various industrial applications, such as process control systems, automation equipment, and power electronics. Industrial PCBs must be able to withstand harsh operating conditions, such as high temperatures, vibrations, and exposure to chemicals. The use of rugged, high-reliability PCBs is essential in ensuring the longevity and performance of industrial electronic systems.
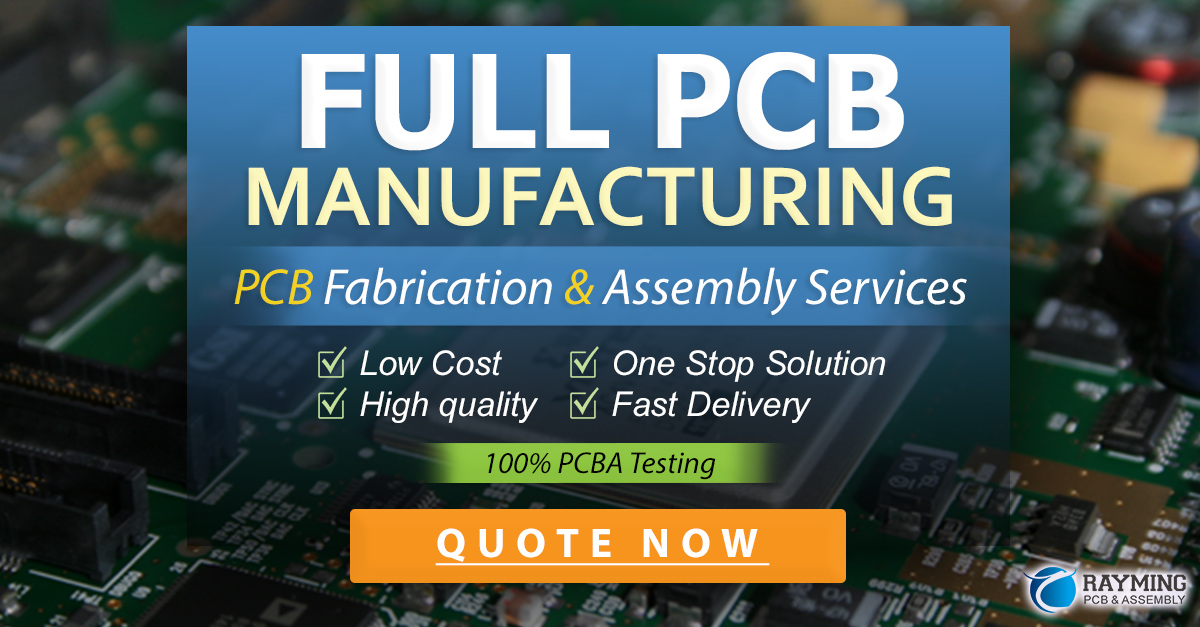
Future Trends in PCB Technology
As electronic devices continue to evolve and become more complex, PCB technology must keep pace to meet the demands of these devices. Some of the key future trends in PCB technology include:
-
Miniaturization: The trend towards smaller, more compact electronic devices is driving the development of miniaturized PCBs. Advanced manufacturing techniques, such as 3D printing and embedded component PCBs, are enabling the creation of ever-smaller PCBs with higher component density.
-
High-speed PCBs: The increasing demand for high-speed data transmission and processing is driving the development of PCBs designed for high-frequency applications. These PCBs use advanced materials, such as low-loss laminates and high-performance copper, to minimize signal loss and maintain signal integrity at high frequencies.
-
Intelligent PCBs: The integration of sensors, microcontrollers, and other intelligent components into PCBs is enabling the creation of smart, self-monitoring electronic systems. These intelligent PCBs can detect and diagnose problems, adjust their performance based on environmental conditions, and communicate with other devices and systems.
-
Sustainable PCBs: As environmental concerns continue to grow, there is an increasing focus on the development of sustainable PCB manufacturing processes and materials. This includes the use of lead-free solders, halogen-free laminates, and recyclable PCB substrates, as well as the adoption of green manufacturing practices to reduce waste and minimize environmental impact.
-
Flexible and Stretchable PCBs: The development of flexible and stretchable PCBs is enabling the creation of novel electronic devices that can conform to various shapes and surfaces. These PCBs are used in applications such as wearable devices, medical implants, and soft robotics, where traditional rigid PCBs are not suitable.
Frequently Asked Questions (FAQ)
- What are the main advantages of using PCBs in electronic devices?
PCBs offer several advantages, including: - Compact size: PCBs allow for the creation of smaller, more compact electronic devices.
- Reliability: PCBs provide a stable and reliable platform for electronic components to function together.
- Cost-effective: PCBs enable the mass production of electronic devices, reducing Manufacturing costs.
-
Customization: PCBs can be customized to meet the specific requirements of different applications.
-
How do I choose the right type of PCB for my application?
The choice of PCB depends on several factors, such as: - Complexity of the circuit: Single-sided PCBs are suitable for simple circuits, while multi-layer PCBs are used for more complex designs.
- Operating environment: PCBs used in harsh environments, such as in automotive or industrial applications, must be able to withstand extreme conditions.
- Size constraints: Flexible or rigid-flex PCBs may be necessary for applications with limited space or specific form factor requirements.
-
Cost: The choice of PCB may also be influenced by budget constraints, with simpler designs being more cost-effective than complex, high-performance boards.
-
What are the main challenges in PCB manufacturing?
Some of the main challenges in PCB manufacturing include: - Miniaturization: As electronic devices become smaller, PCB manufacturers must be able to produce ever-smaller boards with higher component density.
- Signal integrity: Maintaining signal integrity becomes more challenging as PCBs become more complex and operate at higher frequencies.
- Quality control: Ensuring consistent quality across large production runs requires stringent process controls and inspection procedures.
-
Environmental compliance: PCB manufacturers must adhere to increasingly strict environmental regulations, such as the restriction of hazardous substances (RoHS) directive.
-
How can I ensure the reliability and longevity of my PCB design?
To ensure the reliability and longevity of your PCB design, consider the following: - Use high-quality materials: Choose PCB substrates, laminates, and components that are suitable for your application and operating environment.
- Follow best design practices: Adhere to industry-standard design guidelines, such as proper trace spacing, via sizing, and component placement.
- Conduct thorough testing: Perform rigorous testing and inspection procedures to identify and address any potential issues before mass production.
-
Consider protective coatings: Apply conformal coatings or potting compounds to protect the PCB from moisture, dust, and other environmental factors.
-
What is the future outlook for the PCB industry?
The PCB industry is expected to continue growing in the coming years, driven by the increasing demand for electronic devices across various sectors. Some of the key growth drivers include: - Internet of Things (IoT): The proliferation of connected devices is driving the demand for compact, high-performance PCBs.
- 5G technology: The rollout of 5G networks is expected to boost the demand for high-frequency, high-speed PCBs.
- Automotive electronics: The increasing adoption of electric vehicles and advanced driver assistance systems (ADAS) is driving the demand for specialized automotive PCBs.
- Medical devices: The growing need for advanced medical equipment and wearable health monitors is fueling the demand for high-reliability, biocompatible PCBs.
As PCB technology continues to evolve, manufacturers and designers must stay abreast of the latest trends and advancements to remain competitive in this dynamic industry.
Conclusion
Printed Circuit Boards (PCBs) are the unsung heroes of the electronic world, enabling the creation of countless devices that we rely on in our daily lives. From consumer electronics and automotive systems to medical devices and aerospace equipment, PCBs play a crucial role in ensuring the functionality, reliability, and performance of these devices.
As electronic devices continue to evolve and become more complex, PCB technology must keep pace to meet the demands of these devices. The future of PCBs is shaped by trends such as miniaturization, high-speed performance, intelligent functionality, sustainability, and flexibility. By staying at the forefront of these trends, PCB manufacturers and designers can continue to drive innovation and push the boundaries of what is possible in the world of electronics.
In conclusion, the importance of PCBs in modern society cannot be overstated. As we continue to rely on electronic devices in every aspect of our lives, the role of PCBs in enabling these devices will only become more critical. By understanding the importance of PCBs and staying abreast of the latest trends and advancements in PCB technology, we can ensure a future where electronic devices continue to enrich our lives and drive progress across various industries.
No responses yet