Introduction to PCB Fabrication
Printed Circuit Boards (PCBs) are the backbone of modern electronics. They are used in almost every electronic device, from smartphones and computers to medical equipment and aerospace systems. PCB fabrication is the process of creating these boards, which involves several steps and techniques. In this article, we will explore the various steps involved in PCB fabrication and the different manufacturing techniques used.
What is a PCB?
A PCB is a flat board made of insulating materials, such as fiberglass or plastic, with conductive pathways etched onto its surface. These pathways, known as traces, connect various electronic components, such as resistors, capacitors, and integrated circuits (ICs), to form a complete electronic circuit. PCBs are used to mechanically support and electrically connect electronic components using conductive tracks, pads, and other features etched from copper sheets laminated onto a non-conductive substrate.
Types of PCBs
There are several types of PCBs, each with its own unique characteristics and applications. The most common types of PCBs are:
-
Single-sided PCBs: These boards have conductive traces on only one side of the substrate. They are the simplest and most cost-effective type of PCB, suitable for low-complexity circuits.
-
Double-sided PCBs: These boards have conductive traces on both sides of the substrate, allowing for more complex circuits and higher component density. The two sides are connected using through-hole technology or vias.
-
Multi-layer PCBs: These boards consist of multiple layers of conductive traces separated by insulating layers. They offer the highest component density and are used in complex electronic devices, such as smartphones, computers, and medical equipment.
-
Flexible PCBs: These boards are made of flexible materials, such as polyimide or PEEK, allowing them to bend and conform to various shapes. They are used in applications where flexibility and space constraints are crucial, such as wearable devices and aerospace systems.
-
Rigid-Flex PCBs: These boards combine the benefits of rigid and flexible PCBs, featuring both rigid and flexible sections. They are used in applications that require both stability and flexibility, such as automotive electronics and military equipment.
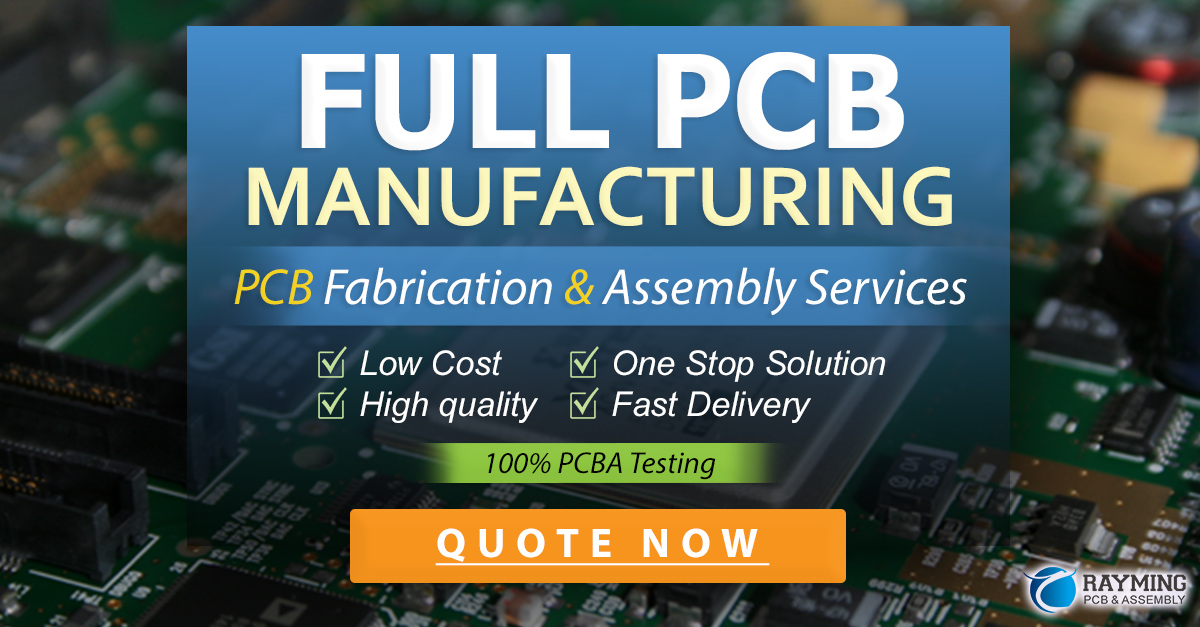
PCB Fabrication Process
The PCB fabrication process involves several steps, each of which is crucial to ensuring the quality and reliability of the final product. The main steps in PCB fabrication are:
Step 1: Design and Layout
The first step in PCB fabrication is designing the circuit and creating the PCB layout. This involves using specialized software, such as Altium Designer or Eagle, to create a schematic diagram of the circuit and then converting it into a physical layout. The layout defines the size and shape of the PCB, the location of components, and the routing of conductive traces.
Step 2: Material Selection
Once the design and layout are complete, the next step is to select the appropriate materials for the PCB. The most common materials used in PCB fabrication are:
- FR-4: A flame-retardant fiberglass-reinforced epoxy laminate, widely used for its excellent electrical and mechanical properties.
- Polyimide: A high-temperature, flexible material used in flexible and rigid-flex PCBs.
- PTFE: A low-Dielectric constant material used in high-frequency applications, such as RF and microwave circuits.
- Aluminum: A metal-based PCB Material used in high-power and heat-dissipation applications.
The choice of material depends on the specific requirements of the application, such as temperature range, flexibility, and electrical performance.
Step 3: Substrate Preparation
The substrate is the foundation of the PCB, providing mechanical support and electrical insulation for the conductive traces. The substrate preparation process involves the following sub-steps:
-
Cutting: The substrate material is cut to the required size and shape using a precision cutting machine.
-
Drilling: Holes are drilled into the substrate to accommodate through-hole components and vias. The drilling process is carried out using a computer-controlled drilling machine, which ensures precise hole placement and size.
-
Cleaning: The drilled substrate is cleaned to remove any debris or contaminants that may affect the subsequent steps.
Step 4: Copper Cladding
After the substrate is prepared, a thin layer of copper is laminated onto one or both sides of the substrate. The copper layer serves as the conductive material for the traces and pads. The lamination process involves the following sub-steps:
-
Lamination: The copper foil is bonded to the substrate using heat and pressure in a lamination press.
-
Cleaning: The laminated substrate is cleaned to remove any oxides or contaminants that may have formed during the lamination process.
Step 5: Patterning
The patterning process involves transferring the PCB layout onto the copper-clad substrate. This is typically done using a photolithographic process, which involves the following sub-steps:
-
Photoresist Application: A light-sensitive polymer, called photoresist, is applied to the copper-clad substrate using a spin coater or a dip coater.
-
Exposure: The photoresist-coated substrate is exposed to UV light through a photomask, which contains the PCB layout pattern. The exposed areas of the photoresist become soluble, while the unexposed areas remain insoluble.
-
Developing: The exposed substrate is developed in a chemical solution, which removes the soluble areas of the photoresist, leaving behind the desired pattern.
Step 6: Etching
The etching process removes the unwanted copper from the substrate, leaving behind the conductive traces and pads. The most common etching methods are:
- Chemical Etching: The patterned substrate is immersed in an etchant solution, typically ferric chloride or ammonium persulfate, which selectively removes the exposed copper.
- Plasma Etching: A plasma, generated by a high-frequency electric field, is used to remove the exposed copper. This method offers higher precision and resolution compared to chemical etching.
After etching, the remaining photoresist is removed using a stripping solution, revealing the final copper pattern.
Step 7: Soldermask Application
A soldermask is a protective coating applied to the PCB to prevent accidental short circuits and improve the board’s aesthetics. The soldermask application process involves the following sub-steps:
-
Soldermask Coating: A layer of soldermask ink is applied to the PCB using a screen printing or photoimaging process.
-
Curing: The soldermask-coated PCB is cured in an oven to harden the ink and improve its adhesion to the substrate.
-
Finishing: The cured soldermask is cleaned and inspected for any defects or irregularities.
Step 8: Surface Finish
The surface finish is a protective and conductive layer applied to the exposed copper areas of the PCB to prevent oxidation and improve solderability. The most common surface finishes are:
- HASL (Hot Air Solder Leveling): A thin layer of solder is applied to the copper areas using a hot air leveling process.
- ENIG (Electroless Nickel Immersion Gold): A layer of nickel is deposited onto the copper areas, followed by a thin layer of gold.
- OSP (Organic Solderability Preservative): An organic compound is applied to the copper areas to prevent oxidation and maintain solderability.
- Immersion Silver: A thin layer of silver is deposited onto the copper areas through an immersion process.
The choice of surface finish depends on the specific requirements of the application, such as shelf life, solderability, and cost.
Step 9: Silkscreen
The silkscreen process involves printing text, logos, and component identifiers onto the PCB using a screen printing process. The silkscreen ink is typically white or yellow and is applied to the soldermask layer. This step improves the readability and aesthetics of the PCB.
Step 10: Electrical Testing
After the PCB fabrication process is complete, the boards undergo electrical testing to ensure their functionality and reliability. The most common testing methods are:
- Flying Probe Test: A set of moving probes are used to test the continuity and isolation of the PCB traces and pads.
- Bed of Nails Test: The PCB is placed on a fixture containing spring-loaded pins (nails) that make contact with the test points on the board.
- In-Circuit Test (ICT): The PCB is tested with its components installed, using a combination of flying probe and bed of nails techniques.
Electrical testing helps identify any manufacturing defects or design issues, ensuring that only high-quality PCBs are delivered to the customer.
PCB Manufacturing Techniques
In addition to the standard PCB fabrication process, there are several specialized manufacturing techniques used for specific applications or requirements. Some of these techniques are:
High-Density Interconnect (HDI)
HDI is a PCB manufacturing technique that offers higher component density and smaller feature sizes compared to traditional PCBs. HDI boards use a combination of microvias, fine-pitch traces, and embedded components to achieve higher interconnect density. This technique is commonly used in smartphones, wearables, and other compact electronic devices.
Feature | Standard PCB | HDI PCB |
---|---|---|
Trace Width | 6-8 mil | 3-4 mil |
Via Diameter | 12-16 mil | 4-8 mil |
Via Pad Diameter | 24-32 mil | 8-16 mil |
Hole Diameter | 10-12 mil | 4-6 mil |
Embedded Component PCBs
Embedded component PCBs are boards that have passive components, such as resistors and capacitors, embedded within the substrate layers. This technique offers several advantages, such as reduced board size, improved signal integrity, and enhanced thermal management. Embedded component PCBs are used in high-performance applications, such as aerospace, defense, and medical devices.
Metal Core PCBs
Metal core PCBs (MCPCBs) are boards that use a metal substrate, typically aluminum, instead of the traditional FR-4 material. The metal substrate offers excellent Thermal conductivity, allowing for better heat dissipation and improved thermal management. MCPCBs are commonly used in high-power LED lighting, automotive electronics, and power electronics applications.
Flex-Rigid PCBs
Flex-rigid PCBs are boards that combine the benefits of flexible and rigid PCBs, featuring both flexible and rigid sections. The flexible sections allow for bending and folding, while the rigid sections provide mechanical support and stability. Flex-rigid PCBs are used in applications that require both flexibility and reliability, such as automotive electronics, medical devices, and aerospace systems.
PCB Type | Advantages | Applications |
---|---|---|
HDI | High component density, smaller form factors | Smartphones, wearables, compact electronics |
Embedded Component | Reduced board size, improved signal integrity, enhanced thermal management | Aerospace, defense, medical devices |
Metal Core | Excellent thermal conductivity, improved heat dissipation | High-power LED lighting, automotive electronics, power electronics |
Flex-Rigid | Combines flexibility and rigidity, allows for bending and folding | Automotive electronics, medical devices, aerospace systems |
Frequently Asked Questions (FAQ)
-
What is the difference between a PCB and a PCBA?
A PCB is a bare board without any components installed, while a PCBA (Printed Circuit Board Assembly) is a PCB with all the components soldered onto it, ready for use in an electronic device. -
What is the typical turnaround time for PCB fabrication?
The turnaround time for PCB fabrication varies depending on the complexity of the board, the manufacturing technique used, and the supplier. Standard PCBs can be fabricated in 5-7 days, while more complex boards, such as HDI or flex-rigid PCBs, may take 2-3 weeks. -
What is the minimum feature size achievable in PCB fabrication?
The minimum feature size depends on the manufacturing technique and the capabilities of the PCB fabricator. For standard PCBs, the minimum trace width and spacing are typically 4-6 mil (0.1-0.15 mm), while HDI boards can achieve trace widths as small as 2-3 mil (0.05-0.075 mm). -
Can PCBs be recycled?
Yes, PCBs can be recycled to recover valuable materials, such as copper, gold, and other metals. However, the recycling process is complex and requires specialized equipment and facilities to ensure proper handling and disposal of hazardous materials. -
What are the environmental considerations in PCB fabrication?
PCB fabrication involves the use of various chemicals and materials that can have an impact on the environment. Responsible PCB manufacturers follow strict environmental regulations and implement sustainable practices, such as using lead-free solders, minimizing waste, and properly disposing of hazardous materials.
Conclusion
PCB fabrication is a complex process that involves several steps and techniques to create the backbone of modern electronics. From design and material selection to etching and surface finishing, each step plays a crucial role in ensuring the quality and reliability of the final product. As technology advances and electronic devices become more compact and sophisticated, specialized manufacturing techniques, such as HDI, embedded components, and flex-rigid PCBs, are becoming increasingly important.
By understanding the various steps and techniques involved in PCB fabrication, designers and engineers can make informed decisions when developing new electronic products, taking into account factors such as cost, performance, and environmental impact. As the demand for high-quality, reliable PCBs continues to grow, the PCB manufacturing industry will continue to evolve and innovate, driving the future of electronics.
No responses yet