What is Solder Paste?
Solder paste is a mixture of tiny solder particles suspended in a flux medium. It is used to form electrical and mechanical connections between electronic components and the PCB substrate. The solder particles are typically made of a tin-lead (SnPb) alloy or lead-free alternatives, such as tin-silver-copper (SAC) alloys.
Composition of Solder Paste
Solder paste consists of two main components:
- Solder alloy particles (50-90% by weight)
- Flux medium (10-50% by weight)
The solder alloy particles are responsible for forming the actual solder joint, while the flux medium serves several purposes:
- Protects the solder particles from oxidation
- Improves the wetting and spreading of the molten solder
- Helps to remove oxides and other contaminants from the surfaces being soldered
Types of Solder Paste
Solder pastes can be classified based on various criteria, such as alloy composition, particle size, and flux type.
Alloy Composition
- Tin-Lead (SnPb) Solder Pastes
- Commonly used: Sn63Pb37, Sn60Pb40
- Melting point: 183°C (361°F)
- Excellent wetting and reliability
-
Being phased out due to RoHS regulations
-
Lead-Free Solder Pastes
- Common alloys: SAC305 (Sn96.5Ag3.0Cu0.5), SN100C (Sn99.3Cu0.7 + Ni+Ge)
- Higher melting points compared to SnPb alloys
- Comply with RoHS and other environmental regulations
Particle Size
Solder paste particle sizes are classified by mesh size or type (e.g., Type 3, Type 4, Type 5). Smaller particle sizes are used for fine-pitch components and high-density PCB layouts.
Type | Mesh Size | Particle Size Range |
---|---|---|
Type 3 | -325/+500 | 25-45 μm |
Type 4 | -400/+635 | 20-38 μm |
Type 5 | -500/+635 | 15-25 μm |
Flux Type
Solder pastes can be categorized by the type of flux they contain, which determines their activity level and residue characteristics.
- Rosin-Based Fluxes (RO)
- Mild (ROL0), Moderate (ROM0), Activated (ROH0)
- Provide good wetting and reliability
-
May require cleaning depending on the activity level
-
Water-Soluble Fluxes (ORH1)
- Higher activity level compared to rosin-based fluxes
- Residues can be easily cleaned with water
-
May cause corrosion if not cleaned properly
-
No-Clean Fluxes (ROL0, ROL1)
- Low activity level and minimal residue
- Designed to be left on the PCB after soldering
- Suitable for applications where cleaning is not feasible or desirable
Solder Paste Application Methods
There are two primary methods for applying solder paste to PCBs:
- Stencil Printing
- Most common method in high-volume production
- Uses a stencil with apertures that match the PCB pad layout
- Solder paste is deposited through the apertures onto the PCB pads
-
Provides consistent and precise solder paste deposits
-
Dispensing
- Used for low-volume production, prototyping, or rework
- Solder paste is dispensed through a needle or nozzle onto the PCB pads
- Offers flexibility but may be less consistent than stencil printing
Stencil Printing Process
The stencil printing process involves the following steps:
- Aligning the stencil with the PCB
- Applying solder paste to the stencil
- Spreading the solder paste across the stencil using a squeegee
- Lifting the stencil, leaving solder paste deposits on the PCB pads
- Inspecting the solder paste deposits for defects
Stencil Design Considerations
To ensure optimal solder paste deposition, stencil design must take into account several factors:
- Aperture size and shape
- Stencil thickness
- Aperture wall angle
- Stencil material (e.g., laser-cut, electroformed, additive manufactured)
Solder Paste Inspection (SPI)
Solder Paste Inspection (SPI) is a critical step in the PCB Assembly process, ensuring that the solder paste deposits meet the required specifications before component placement and reflow.
SPI Technologies
- 2D SPI
- Uses a camera to capture images of the solder paste deposits
- Measures the area and position of the deposits
-
Limited ability to measure deposit height
-
3D SPI
- Uses laser triangulation or structured light to measure the height and volume of the solder paste deposits
- Provides more comprehensive data compared to 2D SPI
- Enables better process control and defect detection
SPI Metrics
SPI systems evaluate solder paste deposits based on various metrics, including:
- Area: The size of the solder paste deposit compared to the stencil aperture or PCB pad
- Height: The height of the solder paste deposit
- Volume: The volume of the solder paste deposit
- Offset: The position of the solder paste deposit relative to the PCB pad
SPI Defect Detection
SPI systems can detect various types of solder paste defects, such as:
- Insufficient solder paste
- Excessive solder paste
- Bridging between adjacent pads
- Solder paste smearing or slumping
- Missing or misaligned deposits
Detecting and correcting these defects early in the assembly process helps to improve yield and reduce rework costs.
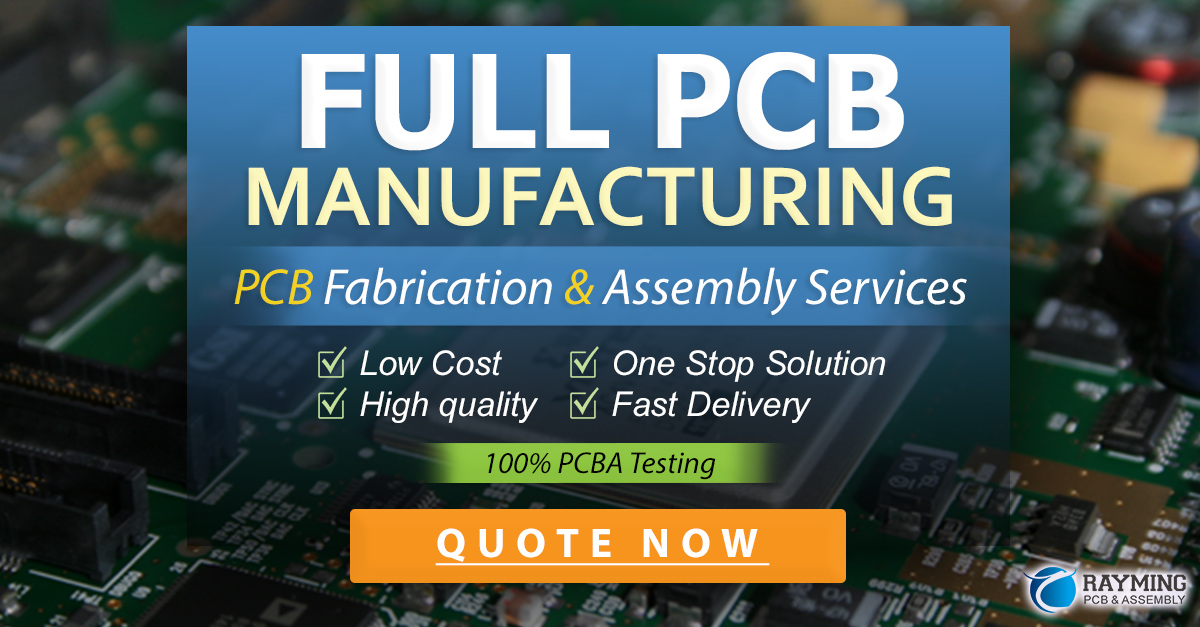
Solder Paste Handling and Storage
Proper handling and storage of solder paste are essential to ensure consistent performance and shelf life.
Storage Conditions
Solder paste should be stored under the following conditions:
- Temperature: 0-10°C (32-50°F)
- Humidity: 30-70% relative humidity
- Sealed containers to prevent contamination and drying out
Shelf Life
The shelf life of solder paste depends on the specific formulation and storage conditions. Typical shelf life ranges from 3 to 12 months when stored properly.
Handling Guidelines
When handling solder paste, follow these guidelines:
- Allow the solder paste to reach room temperature before opening the container
- Gently mix the solder paste before use to ensure homogeneity
- Avoid introducing air bubbles or contamination during mixing
- Use clean, compatible tools and equipment
- Follow the manufacturer’s recommendations for print parameters and reflow profiles
Solder Paste Reflow
After component placement, the PCB assembly undergoes a reflow process to melt the solder paste and form permanent solder joints.
Reflow Profile
A typical reflow profile consists of four stages:
- Preheat: Gradually raises the temperature to activate the flux and evaporate solvents
- Thermal Soak: Maintains a stable temperature to allow the components and PCB to reach thermal equilibrium
- Reflow: Raises the temperature above the solder alloy’s melting point, allowing the solder to melt and form solder joints
- Cooling: Gradually cools the PCB assembly to solidify the solder joints
Reflow Oven Types
There are two main types of reflow ovens used in PCB assembly:
- Convection Reflow Ovens
- Use heated air to transfer heat to the PCB assembly
- Provide uniform heating and good process control
-
Suitable for most PCB assembly applications
-
Vapor Phase Reflow Ovens
- Use a heated vapor to transfer heat to the PCB assembly
- Provide excellent thermal uniformity and reduced risk of overheating
- Suitable for high-thermal-mass assemblies or temperature-sensitive components
Solder Paste Defects and Troubleshooting
Despite careful process control, solder paste defects can still occur. Common defects include:
- Solder bridges: Unintended connections between adjacent pads or pins
- Solder balls: Small, spherical solder particles that can cause short circuits
- Insufficient solder: Weak or unreliable solder joints due to insufficient solder volume
- Tombstoning: Components standing on end due to uneven heating or solder paste volumes
Troubleshooting solder paste defects involves analyzing the root cause and making appropriate adjustments to the process parameters, such as:
- Stencil design
- Print parameters (speed, pressure, separation)
- Reflow profile
- Solder paste formulation
- PCB and component design
Frequently Asked Questions (FAQ)
-
Q: Can solder paste be reused?
A: No, solder paste should not be reused once it has been removed from its original container. Reused solder paste may have altered rheological properties, contamination, or reduced flux activity, leading to poor performance. -
Q: How long can solder paste be left on a stencil?
A: The time solder paste can be left on a stencil depends on the specific formulation and environmental conditions. Generally, it is recommended to limit the time to 4-8 hours to prevent drying out or changes in rheological properties. Always consult the manufacturer’s guidelines for specific recommendations. -
Q: What is the difference between water-soluble and no-clean solder pastes?
A: Water-soluble solder pastes contain flux that is designed to be easily cleaned with water after reflow. No-clean solder pastes have a low activity flux that leaves minimal, non-corrosive residue after reflow, eliminating the need for post-reflow cleaning. -
Q: How do I choose the right solder paste for my application?
A: When selecting a solder paste, consider factors such as the alloy composition, particle size, flux type, and the specific requirements of your application (e.g., fine-pitch components, environmental regulations, cleaning process). Consult with solder paste manufacturers or experienced PCB assembly professionals for guidance. -
Q: What are the most common causes of solder paste defects?
A: Common causes of solder paste defects include improper stencil design, incorrect print parameters, poor PCB or component quality, inadequate reflow profile, and improper handling or storage of solder paste. A thorough understanding of the assembly process and systematic troubleshooting can help identify and resolve the root causes of defects.
Conclusion
Solder paste is a critical component in PCB assembly, enabling the formation of reliable electrical and mechanical connections between components and the PCB substrate. Understanding the composition, types, application methods, and best practices for handling and storage of solder paste is essential for achieving high-quality, defect-free solder joints.
By implementing effective process control, solder paste inspection, and troubleshooting techniques, manufacturers can optimize their PCB assembly processes and improve overall product quality and reliability. As electronic devices continue to advance in complexity and miniaturization, the role of solder paste in enabling these technologies will remain crucial.
No responses yet