Introduction to SMT Stencils
Surface Mount Technology (SMT) has revolutionized the electronics manufacturing industry by enabling the production of smaller, more complex, and more reliable electronic devices. One of the key components in the SMT assembly process is the solder paste stencil, also known as the SMT stencil. This article will provide an in-depth look at SMT Stencils, their importance, types, materials, design considerations, and best practices for use and maintenance.
What is an SMT Stencil?
An SMT stencil is a thin, flat sheet of material with precisely cut openings that correspond to the pads on a printed circuit board (PCB). The stencil is used to apply solder paste onto the PCB pads in a controlled and consistent manner. The solder paste deposited through the stencil openings will later be used to form electrical and mechanical connections between the PCB and surface mount components during the reflow soldering process.
Importance of SMT Stencils in Electronics Manufacturing
SMT stencils play a crucial role in the electronics manufacturing process by ensuring the accurate and consistent application of solder paste on PCB pads. The quality of the solder paste deposit directly impacts the reliability and functionality of the final assembled product. Some key benefits of using SMT stencils include:
- Precise solder paste deposition
- Consistent solder joint formation
- Improved production efficiency
- Reduced defects and rework
- Enabling high-density component placement
Types of SMT Stencils
There are several types of SMT stencils available, each with its own characteristics and advantages. The choice of stencil type depends on factors such as the PCB design, component density, and production requirements.
Laser-Cut Stencils
Laser-cut stencils are the most common type of SMT stencil. They are created by using a high-powered laser to cut the stencil openings in a thin sheet of stainless steel. Laser-cut stencils offer several advantages:
- High precision and accuracy
- Smooth aperture walls for improved paste release
- Suitable for a wide range of aperture sizes and shapes
- Durable and long-lasting
Electroformed Stencils
Electroformed stencils are created by electroplating nickel onto a photoresist-patterned substrate. The photoresist is then removed, leaving behind a nickel stencil with the desired aperture pattern. Electroformed stencils offer some unique benefits:
- Extremely fine pitch capability (down to 0.3 mm)
- Smooth aperture walls for excellent paste release
- Uniform aperture sizes and shapes
- Suitable for high-volume production
Nano-Coated Stencils
Nano-coated stencils are laser-cut or electroformed stencils that have been coated with a nano-scale layer of a hydrophobic material, such as Teflon or a proprietary coating. The nano-coating provides several advantages:
- Improved solder paste release
- Reduced stencil cleaning frequency
- Extended stencil life
- Minimized bridging and solder balling
SMT Stencil Materials
SMT stencils can be made from various materials, each with its own properties and benefits. The choice of material depends on factors such as durability, cost, and performance requirements.
Stainless Steel
Stainless steel is the most commonly used material for SMT stencils. It offers several advantages:
- Excellent durability and long life
- Good paste release properties
- Suitable for a wide range of aperture sizes and shapes
- Cost-effective for most applications
Nickel
Nickel is primarily used for electroformed stencils. It provides some unique benefits:
- Excellent paste release properties
- High precision and accuracy
- Suitable for fine-pitch applications
- Resistant to corrosion and wear
Polyimide
Polyimide stencils are made from a flexible, polymer material. They are often used for specialized applications, such as:
- Printing on flexible or curved substrates
- Prototyping and low-volume production
- Applications requiring a low-cost, disposable stencil
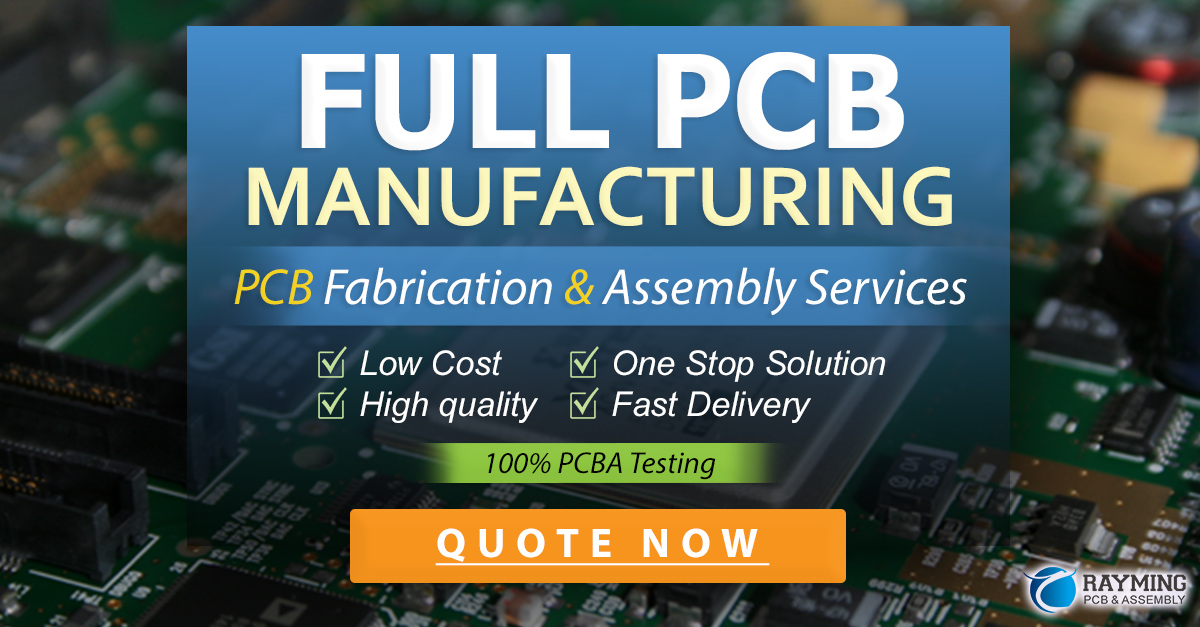
SMT Stencil Design Considerations
Designing an effective SMT stencil involves several key considerations to ensure optimal solder paste deposition and reflow results.
Aperture Size and Shape
The size and shape of the stencil apertures directly impact the volume and geometry of the solder paste deposit. Some important factors to consider include:
- Pad size and shape
- Component pitch and density
- Solder paste type and particle size
- Desired solder joint profile
Aperture sizes are typically expressed as a percentage of the pad size, with common area ratios ranging from 80% to 120%. The aperture shape can be circular, square, or rectangular, depending on the pad geometry and desired solder paste volume.
Stencil Thickness
The thickness of the SMT stencil determines the volume of solder paste deposited on the PCB pads. Thicker stencils deposit more paste, while thinner stencils deposit less. The optimal stencil thickness depends on factors such as:
- Component type and size
- Pad geometry and pitch
- Solder paste type and particle size
- Reflow profile and process parameters
Common stencil thicknesses range from 0.1 mm to 0.2 mm (4 to 8 mils) for standard SMT applications. Fine-pitch and ultra-fine-pitch applications may require thinner stencils, while power electronics and other high-volume applications may benefit from thicker stencils.
Aperture Wall Geometry
The geometry of the aperture walls can significantly impact solder paste release and print quality. Some common aperture wall geometries include:
- Straight walls
- Tapered walls
- Stepped walls
- Rounded corners
Tapered and stepped walls can improve solder paste release by reducing the surface area in contact with the paste. Rounded corners can help prevent paste buildup and improve print consistency.
SMT Stencil Printing Process
The SMT stencil printing process involves several key steps to ensure accurate and consistent solder paste deposition.
Stencil Alignment
Proper alignment of the SMT stencil to the PCB is critical for accurate solder paste deposition. Most modern stencil printers use automatic vision systems to align the stencil to the PCB fiducials or other reference marks. Manual alignment may be used for low-volume or prototype applications.
Solder Paste Application
Once the stencil is aligned, solder paste is applied to the top surface of the stencil. The paste is typically dispensed from a cartridge or jar and spread across the stencil using a squeegee blade. The blade is then moved across the stencil in a controlled manner, forcing the paste through the apertures and onto the PCB pads.
Print Parameters
Several print parameters can be adjusted to optimize the solder paste deposition process, including:
- Squeegee pressure
- Squeegee speed
- Separation speed
- Print stroke length
- Stencil snap-off distance
These parameters should be optimized based on the specific stencil design, solder paste type, and PCB characteristics to achieve the best print quality and consistency.
SMT Stencil Maintenance and Cleaning
Proper maintenance and cleaning of SMT stencils are essential for ensuring consistent print quality and extending stencil life.
Stencil Inspection
Regular inspection of the SMT stencil is important for identifying and addressing any issues that may affect print quality. Some common stencil defects to look for include:
- Clogged or partially clogged apertures
- Damaged or worn aperture edges
- Solder paste buildup on the stencil surface
- Stencil warping or deformation
Stencil inspection can be performed manually using a microscope or automatically using specialized stencil inspection systems.
Stencil Cleaning
SMT stencils should be cleaned regularly to remove solder paste residue and prevent aperture clogging. The frequency of cleaning depends on factors such as the solder paste type, print volume, and environmental conditions. Some common stencil cleaning methods include:
- Manual cleaning with solvents and wipes
- Ultrasonic cleaning in a solvent bath
- Automated stencil cleaning systems
Proper cleaning helps maintain print quality, reduce defects, and extend stencil life.
Stencil Storage
When not in use, SMT stencils should be stored properly to prevent damage and contamination. Stencils should be kept in a clean, dry environment, away from direct sunlight and extreme temperatures. They should also be stored flat or hung vertically to prevent warping or deformation.
Best Practices for SMT Stencil Use
To optimize the performance and longevity of SMT stencils, consider the following best practices:
- Use high-quality solder paste that is compatible with the stencil material and aperture geometry.
- Regularly inspect and clean the stencil to maintain print quality and prevent defects.
- Optimize print parameters based on the specific stencil design, solder paste, and PCB characteristics.
- Store stencils properly to prevent damage and contamination.
- Replace stencils when they become worn or damaged beyond repair.
Conclusion
SMT stencils are a critical component in the electronics manufacturing process, ensuring accurate and consistent solder paste deposition for reliable and high-quality solder joints. By understanding the types, materials, design considerations, and best practices for SMT stencil use and maintenance, manufacturers can optimize their SMT assembly processes and produce superior electronic products.
Frequently Asked Questions
How often should I clean my SMT stencil?
The frequency of cleaning depends on factors such as the solder paste type, print volume, and environmental conditions. As a general rule, stencils should be cleaned every 4-8 hours of continuous printing or whenever print quality begins to degrade.
What is the most common material used for SMT stencils?
Stainless steel is the most common material used for SMT stencils due to its durability, good paste release properties, and cost-effectiveness.
What is the difference between laser-cut and electroformed stencils?
Laser-cut stencils are created by using a high-powered laser to cut apertures in a thin sheet of stainless steel, while electroformed stencils are created by electroplating nickel onto a photoresist-patterned substrate. Electroformed stencils offer finer pitch capabilities and smoother aperture walls, but are generally more expensive than laser-cut stencils.
How do I choose the right stencil thickness for my application?
The optimal stencil thickness depends on factors such as component type and size, pad geometry and pitch, solder paste type, and reflow profile. As a general guideline, use thicker stencils (0.15-0.2 mm) for larger components and higher-volume deposits, and thinner stencils (0.1-0.15 mm) for smaller components and finer pitches.
Can I reuse my SMT stencil after cleaning?
Yes, SMT stencils can be reused many times if they are properly cleaned and maintained. However, stencils should be replaced when they become worn or damaged beyond repair to ensure consistent print quality and prevent defects.
No responses yet