Introduction to Selective Soldering PCB
Selective soldering PCB is a process that allows for the precise application of solder to specific components on a printed circuit board (PCB). This technique has become increasingly popular in the electronics manufacturing industry due to its ability to efficiently and accurately solder components in a targeted manner, reducing the risk of damage to sensitive components and improving overall product quality.
What is Selective Soldering?
Selective soldering is a process that involves applying solder to specific components on a PCB, rather than soldering the entire board at once. This is achieved through the use of specialized equipment that can precisely control the application of solder to the desired areas. The process typically involves the following steps:
- The PCB is loaded into the selective soldering machine.
- The machine identifies the components to be soldered using a vision system or predefined coordinates.
- The machine applies flux to the components to be soldered.
- The machine applies solder to the components using a soldering nozzle or laser.
- The machine cleans any excess flux from the board.
Benefits of Selective Soldering PCB
Selective soldering PCB offers several benefits over traditional wave soldering or hand soldering techniques, including:
- Improved accuracy: Selective soldering allows for precise control over the application of solder, reducing the risk of bridging or other defects.
- Reduced damage to sensitive components: By targeting only the components that require soldering, selective soldering reduces the risk of damage to sensitive components such as connectors or surface mount devices.
- Increased efficiency: Selective soldering can be automated, allowing for faster production times and reduced labor costs.
- Improved quality: Selective soldering results in a higher quality solder joint, reducing the risk of defects and improving overall product reliability.
Types of Selective Soldering PCB
There are several types of selective soldering PCB techniques, each with its own advantages and disadvantages. The most common types include:
Miniwave Selective Soldering
Miniwave selective soldering involves the use of a small wave of molten solder that is precisely controlled to target specific components on the PCB. This technique is often used for through-hole components and can be automated for high-volume production.
Laser Selective Soldering
Laser selective soldering uses a focused laser beam to heat and melt solder onto specific components on the PCB. This technique offers high precision and can be used for both through-hole and surface mount components.
Robotic Selective Soldering
Robotic selective soldering involves the use of a robotic arm equipped with a soldering nozzle to apply solder to specific components on the PCB. This technique offers high flexibility and can be programmed to handle a wide range of component types and sizes.
Selective Soldering PCB Process
The selective soldering PCB process typically involves the following steps:
- PCB Design: The PCB is designed with selective soldering in mind, taking into account the placement of components and the required soldering points.
- Solder Paste Application: Solder paste is applied to the components to be soldered using a stencil or dispensing system.
- Component Placement: The components are placed onto the PCB using a pick-and-place machine or by hand.
- Flux Application: Flux is applied to the components to be soldered to help remove oxides and improve solder wetting.
- Preheating: The PCB is preheated to activate the flux and prepare the components for soldering.
- Selective Soldering: The selective soldering machine applies solder to the desired components using a soldering nozzle or laser.
- Cleaning: Any excess flux or solder is removed from the PCB using a cleaning system.
- Inspection: The PCB is inspected for defects and quality control purposes.
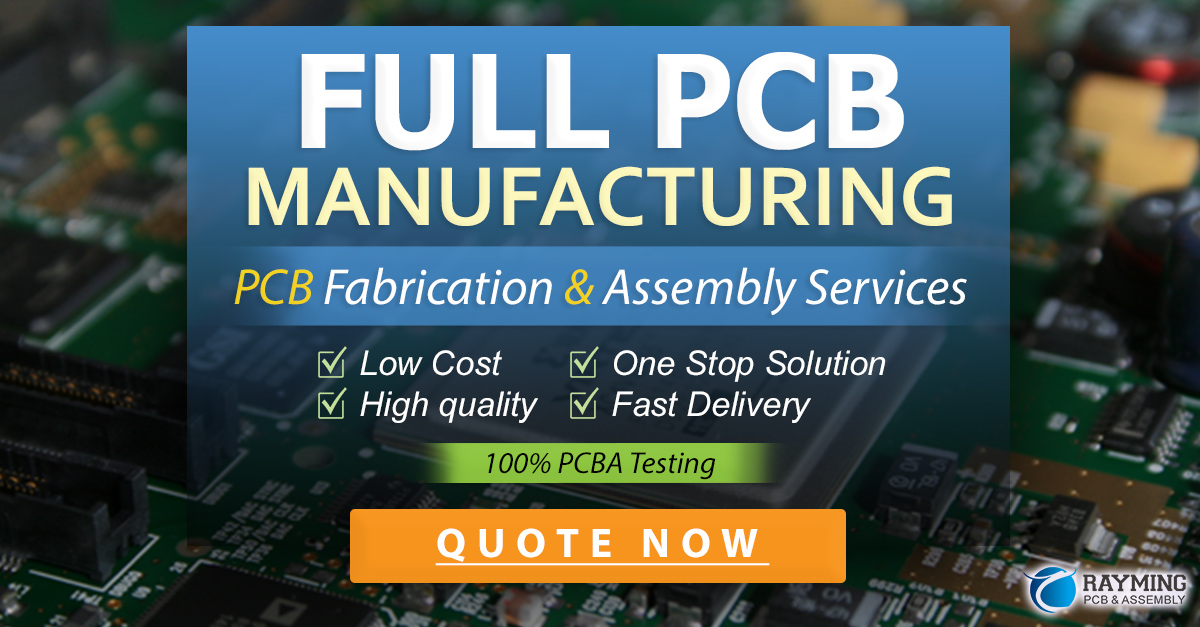
Advantages of Selective Soldering PCB
Selective soldering PCB offers several advantages over traditional soldering techniques, including:
- Reduced thermal stress: By targeting only the components that require soldering, selective soldering reduces the overall thermal stress on the PCB and its components.
- Improved flexibility: Selective soldering allows for greater flexibility in PCB design, as components can be placed in locations that may be difficult to reach with traditional soldering techniques.
- Reduced defects: Selective soldering results in fewer defects such as bridging or insufficient solder, improving overall product quality and reliability.
- Increased efficiency: Selective soldering can be automated, allowing for faster production times and reduced labor costs.
Challenges of Selective Soldering PCB
While selective soldering PCB offers many benefits, there are also some challenges to consider, including:
- Equipment cost: Selective soldering machines can be expensive, requiring a significant upfront investment.
- Programming complexity: Selective soldering requires precise programming to ensure that the correct components are soldered and that the solder is applied correctly.
- Maintenance: Selective soldering machines require regular maintenance to ensure optimal performance and prevent downtime.
Best Practices for Selective Soldering PCB
To ensure the best results when using selective soldering PCB, consider the following best practices:
- Use the right solder and flux: Choose a solder and flux that are compatible with the components being soldered and the selective soldering process.
- Optimize PCB design: Design the PCB with selective soldering in mind, ensuring that components are placed in accessible locations and that there is sufficient clearance for the soldering nozzle.
- Regularly maintain equipment: Regular maintenance of selective soldering machines can help prevent downtime and ensure optimal performance.
- Monitor process parameters: Regularly monitor process parameters such as solder temperature, flux volume, and nozzle height to ensure consistent results.
Conclusion
Selective soldering PCB is a powerful technique that offers many benefits over traditional Soldering Methods. By allowing for precise control over the application of solder, selective soldering reduces the risk of defects, improves product quality, and increases efficiency. While there are some challenges to consider, such as equipment cost and programming complexity, the benefits of selective soldering make it an attractive option for many electronics manufacturers.
FAQs
-
What is selective soldering PCB?
Selective soldering PCB is a process that allows for the precise application of solder to specific components on a printed circuit board (PCB). This technique has become increasingly popular in the electronics manufacturing industry due to its ability to efficiently and accurately solder components in a targeted manner, reducing the risk of damage to sensitive components and improving overall product quality. -
What are the benefits of selective soldering PCB?
The benefits of selective soldering PCB include improved accuracy, reduced damage to sensitive components, increased efficiency, and improved quality. Selective soldering allows for precise control over the application of solder, reducing the risk of bridging or other defects. It also reduces the risk of damage to sensitive components such as connectors or surface mount devices. Selective soldering can be automated, allowing for faster production times and reduced labor costs. Finally, selective soldering results in a higher quality solder joint, reducing the risk of defects and improving overall product reliability. -
What are the different types of selective soldering PCB?
The most common types of selective soldering PCB include miniwave selective soldering, laser selective soldering, and robotic selective soldering. Miniwave selective soldering involves the use of a small wave of molten solder that is precisely controlled to target specific components on the PCB. Laser selective soldering uses a focused laser beam to heat and melt solder onto specific components on the PCB. Robotic selective soldering involves the use of a robotic arm equipped with a soldering nozzle to apply solder to specific components on the PCB. -
What are the challenges of selective soldering PCB?
The challenges of selective soldering PCB include equipment cost, programming complexity, and maintenance. Selective soldering machines can be expensive, requiring a significant upfront investment. Selective soldering requires precise programming to ensure that the correct components are soldered and that the solder is applied correctly. Finally, selective soldering machines require regular maintenance to ensure optimal performance and prevent downtime. -
What are some best practices for selective soldering PCB?
Some best practices for selective soldering PCB include using the right solder and flux, optimizing PCB design, regularly maintaining equipment, and monitoring process parameters. Choose a solder and flux that are compatible with the components being soldered and the selective soldering process. Design the PCB with selective soldering in mind, ensuring that components are placed in accessible locations and that there is sufficient clearance for the soldering nozzle. Regular maintenance of selective soldering machines can help prevent downtime and ensure optimal performance. Finally, regularly monitor process parameters such as solder temperature, flux volume, and nozzle height to ensure consistent results.
Advantage | Description |
---|---|
Improved accuracy | Precise control over solder application, reducing the risk of bridging or other defects |
Reduced component damage | Targeted soldering reduces the risk of damage to sensitive components |
Increased efficiency | Automation allows for faster production times and reduced labor costs |
Improved quality | Higher quality solder joints, reducing the risk of defects and improving overall product reliability |
Challenge | Description |
---|---|
Equipment cost | Selective soldering machines can be expensive, requiring a significant upfront investment |
Programming complexity | Precise programming is required to ensure correct component soldering and solder application |
Maintenance | Regular maintenance is necessary to ensure optimal performance and prevent downtime |
Best Practice | Description |
---|---|
Use the right materials | Choose a solder and flux that are compatible with the components and the selective soldering process |
Optimize PCB design | Design the PCB with selective soldering in mind, ensuring component accessibility and sufficient clearance |
Regularly maintain equipment | Regular maintenance of selective soldering machines helps prevent downtime and ensures optimal performance |
Monitor process parameters | Regularly monitor parameters such as solder temperature, flux volume, and nozzle height for consistent results |
No responses yet