What is a Rigid-Flex PCB?
A rigid-flex PCB is a printed circuit board that combines rigid and flexible substrates laminated together into a single structure. The rigid parts of the board contain standard circuit board layers and components, while the flexible parts allow the board to be bent and folded to fit into tight spaces or movable applications.
Rigid-flex PCBs offer several advantages over traditional rigid PCBs or separate flexible circuits:
- Space savings – bending and folding allows fitting into compact enclosures
- Reliability – integrated structure eliminates connectors between rigid and flex portions
- Design flexibility – 3D shaping enables unique packaging
- Cost reduction – fewer assembly steps and parts compared to rigid and flex boards
Typical Rigid-Flex PCB Structures
Rigid-flex PCBs are custom designed for each application, but typically have a structure consisting of:
Layer | Description |
---|---|
Outer Coverlay | Protective insulating film |
Flexible Copper | Thin copper foil for dynamic areas |
Flexible Substrate | Polyimide or similar for flexibility |
Adhesive | Lamination of rigid and flex portions |
Rigid Layers | FR-4 glass epoxy, standard rigid PCB |
The number of layers, copper weights, substrates, and other aspects vary based on electrical and mechanical requirements. Controlled depth milling and careful bookbinder lamination are used to fabricate the integrated rigid and flexible regions.
Rigid-Flex PCB Manufacturing Process
The manufacturing process for rigid-flex PCBs involves specialized materials, equipment, and techniques compared to standard rigid PCBs. Key steps include:
- Material Selection
- Flexible Layer Fabrication
- Rigid Layer Fabrication
- Drilling and Plating
- Coverlay Application
- Outline Routing
- Electrical Testing
- Final Finish
1. Material Selection
Choosing the right materials is critical for rigid-flex performance and reliability. Key considerations are:
- Polyimide coverlay and substrate for flexibility, heat resistance, and stability
- Copper foil weight for flexibility and current carrying
- Adhesives for temperature, chemical, and flex bond strength
- Rigid layer materials for electrical and mechanical properties
2. Flexible Layer Fabrication
The flexible circuit portions are built up separately using polyimide substrate and coverlays laminated with acrylic or epoxy adhesives. Copper foil is imaged and etched to create circuit traces. Adhesiveless substrates with sputtered copper may also be used.
3. Rigid Layer Fabrication
Standard FR-4 glass epoxy prepreg and laminates are used to build up the rigid board portions. Inner layers are imaged, etched, and laminated into the multilayer structure. Controlled depth milling removes sections of the rigid layers where the flexible portions will be formed.
4. Drilling and Plating
The rigid and flexible substrates are laminated together using heat and pressure. Through-holes are drilled and vias are created to interconnect the layers. Copper electroplating is used to plate the hole walls, creating electrical connections between layers. Blind and buried vias may also be used.
5. Coverlay Application
The outer polyimide coverlay is applied to encapsulate and protect the flexible portions. Photoimaging is used to create openings in the coverlay for component pads and access to the rigid portions.
6. Outline Routing
The final board shape is routed out, including any cutouts or slots. A prototype is checked for fit and function before volume production.
7. Electrical Testing
Flying probe or bed-of-nails testing is used to verify the electrical connections and identify any opens or shorts. High voltage testing may also be performed to check insulation and isolation.
8. Final Finish
The exposed copper pads are coated with the specified surface finish, such as ENIG (gold), HASL (solder), or OSP (organic solderability preservative). Solder mask may also be applied to rigid areas. The boards are then electrically tested again, inspected, and packaged for shipment.
Rigid-Flex PCB Applications
Rigid-flex PCBs are used in a wide range of industries and applications where space savings, reliability, and design flexibility are important. Some common examples include:
Consumer Electronics
- Smartphones, tablets, and wearables
- Digital cameras and camcorders
- Gaming systems and controllers
Rigid-flex allows compact packaging of complex electronics into slim enclosures and moving parts like hinges and sliders. Fine lines and spaces enable high-density interconnects.
Medical Devices
- Hearing aids and medical implants
- Surgical tools and instruments
- Diagnostic and imaging equipment
Rigid-flex provides high reliability, biocompatibility, and resistance to sterilization procedures. Flex circuits can be shaped to fit ergonomic housings.
Automotive Electronics
- Engine control units and sensors
- Infotainment and navigation systems
- Electric vehicle battery packs
Rigid-flex handles high temperatures and vibrations in under-hood applications. 3D packaging allows placement in tight spaces and integrated connector solutions.
Aerospace and Defense
- Avionics and flight controls
- Missile guidance systems
- Soldier-worn electronics
Rigid-flex meets strict reliability standards and saves weight and space in size-constrained systems. Multilayer structures provide EMI shielding.
Industrial Automation
- Robotics and motion control
- Machine vision and inspection
- Process monitoring and control
Rigid-flex enables modular designs that can be reconfigured for different tasks. Flex circuits survive many flex cycles in moving machine parts.
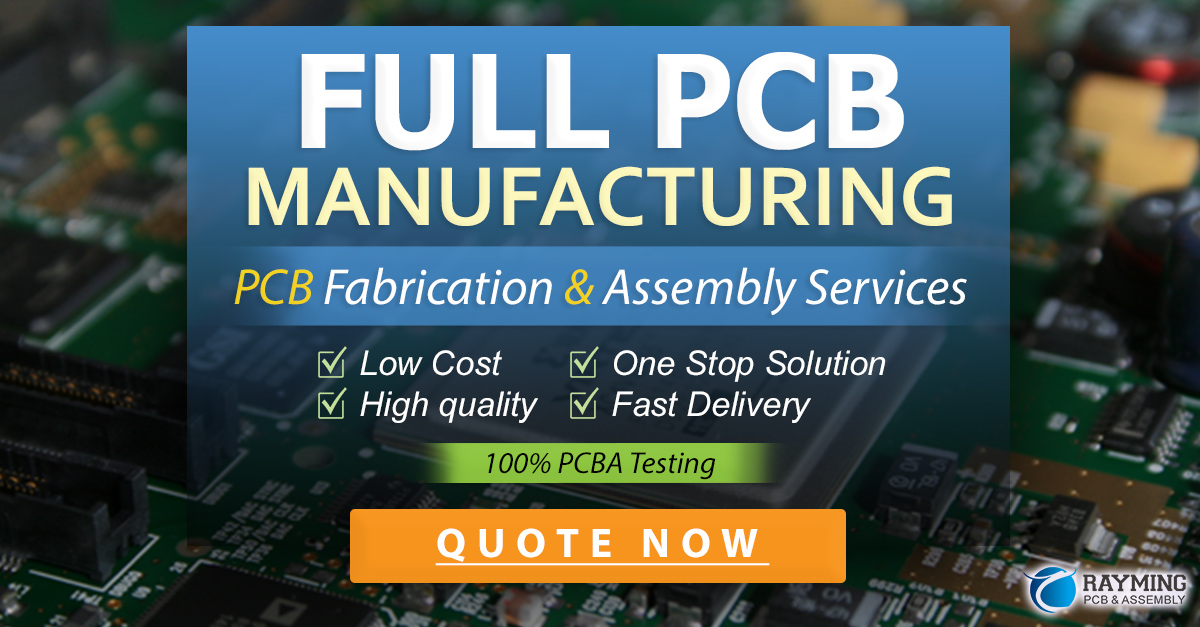
Rigid-Flex PCB FAQ
Q1: What are the benefits of using rigid-flex PCBs?
A1: The main benefits are space savings through dense packaging, reliability by eliminating connectors, and design flexibility with 3D shaping. Rigid-flex can also reduce costs compared to separate rigid and flex circuits.
Q2: What materials are used in rigid-flex PCBs?
A2: Rigid-flex PCBs use a combination of polyimide flexible substrates, acrylic or epoxy adhesives, copper foil, and FR-4 glass epoxy rigid materials. The exact materials are chosen based on the electrical, mechanical, and environmental requirements.
Q3: How are rigid and flexible layers combined?
A3: The rigid and flexible substrates are laminated together using heat and pressure, with controlled depth milling used to remove sections of the rigid layers where flexibility is needed. Through-holes and vias interconnect the layers.
Q4: What are some common applications for rigid-flex PCBs?
A4: Rigid-flex PCBs are commonly used in consumer electronics, medical devices, automotive electronics, aerospace and defense systems, and industrial automation equipment. They are used where space savings, reliability, and design flexibility are important.
Q5: How do rigid-flex PCBs compare to traditional rigid PCBs?
A5: Compared to traditional rigid PCBs, rigid-flex PCBs can save space by enabling dense 3D packaging, improve reliability by eliminating connectors between boards, and provide more design flexibility by allowing circuits to be shaped to fit the enclosure. However, they also require specialized manufacturing processes and may have higher initial costs.
No responses yet