Introduction to Rigid-Flex PCBs
Rigid-flex PCBs are a unique type of printed Circuit board that combines the benefits of both rigid and flexible substrates. This innovative technology allows for the creation of highly complex and compact electronic devices that can withstand harsh environments and repeated flexing. Rigid-flex PCBs consist of multiple layers of flexible and rigid materials, such as polyimide and FR-4, which are laminated together to form a single, cohesive structure.
Benefits of Rigid-Flex PCBs
- Space savings: Rigid-flex PCBs enable the creation of more compact and lightweight electronic devices by eliminating the need for bulky connectors and cables.
- Increased reliability: By reducing the number of interconnects and connectors, rigid-flex PCBs minimize the risk of connection failures and improve overall system reliability.
- Enhanced flexibility: The flexible portions of rigid-flex PCBs allow for greater design freedom and enable the creation of devices with unique form factors and improved ergonomics.
- Improved signal integrity: Rigid-flex PCBs minimize signal loss and interference by reducing the length of interconnects and providing better shielding.
- Cost-effective: Although the initial cost of rigid-flex PCBs may be higher than traditional PCBs, they can lead to overall cost savings by reducing assembly time, minimizing the number of components, and improving product reliability.
Rigid-Flex PCB design Considerations
Layer Stack-up
The layer stack-up of a rigid-flex PCB is crucial to its performance and reliability. A typical rigid-flex PCB stack-up consists of alternating layers of flexible and rigid materials, with copper traces and planes in between. The number of layers and the arrangement of materials depend on the specific requirements of the application, such as signal integrity, power distribution, and mechanical stability.
Layer | Material | Thickness (mm) |
---|---|---|
Top Cover | Polyimide | 0.025 |
Top Copper | Copper | 0.018 |
Flexible Core | Polyimide | 0.050 |
Bottom Copper | Copper | 0.018 |
Rigid Core | FR-4 | 0.200 |
Bottom Copper | Copper | 0.018 |
Bottom Cover | Polyimide | 0.025 |
Bend Radius and Flex Zones
When designing a rigid-flex PCB, it is essential to consider the bend radius and the placement of flex zones. The bend radius refers to the minimum radius at which the flexible portion of the PCB can be bent without causing damage to the copper traces or the substrate. The bend radius depends on factors such as the thickness of the flexible material, the number of copper layers, and the width of the traces.
Flex zones are the areas of the PCB where the flexible material is exposed and allows for bending. These zones should be strategically placed to accommodate the desired form factor of the device and to minimize stress on the components and traces. It is important to provide adequate support for components near flex zones to prevent damage during bending.
Component Placement and Routing
Component placement and routing are critical aspects of rigid-flex PCB design. Components should be placed on the rigid portions of the PCB whenever possible to minimize stress on the solder joints during flexing. If components must be placed on the flexible portions, they should be located close to the rigid-flex interface and properly supported to prevent damage.
When routing traces on a rigid-flex PCB, designers must consider the unique challenges posed by the flexible substrate. Traces should be routed to minimize the number of copper layers in the flexible portions, as this can increase the stiffness of the PCB and reduce its flexibility. Additionally, traces should be routed with gentle curves and avoided sharp angles to prevent stress concentrations and potential fractures.
Manufacturing Process
The manufacturing process for rigid-flex PCBs is more complex than that of traditional rigid PCBs due to the use of multiple materials and the need for precise alignment and lamination. The process typically involves the following steps:
- Material preparation: The flexible and rigid substrates are cut to size and cleaned to remove any contaminants.
- Lamination: The flexible and rigid layers are laminated together using heat and pressure to form a single, cohesive structure.
- Drilling: Holes are drilled through the rigid portions of the PCB to accommodate through-hole components and vias.
- Plating: Copper is plated onto the drilled holes and the surface of the PCB to create conductive paths and pads.
- Patterning: The desired circuit pattern is transferred onto the copper layers using photolithography and etching techniques.
- Solder mask application: A solder mask is applied to the surface of the PCB to protect the copper traces and prevent short circuits.
- Surface finish: A surface finish, such as ENIG (Electroless Nickel Immersion Gold) or OSP (Organic Solderability Preservative), is applied to the exposed copper pads to improve solderability and protect against oxidation.
- Cutting and forming: The PCB is cut and formed into its final shape, with the flexible portions being exposed and the rigid portions remaining intact.
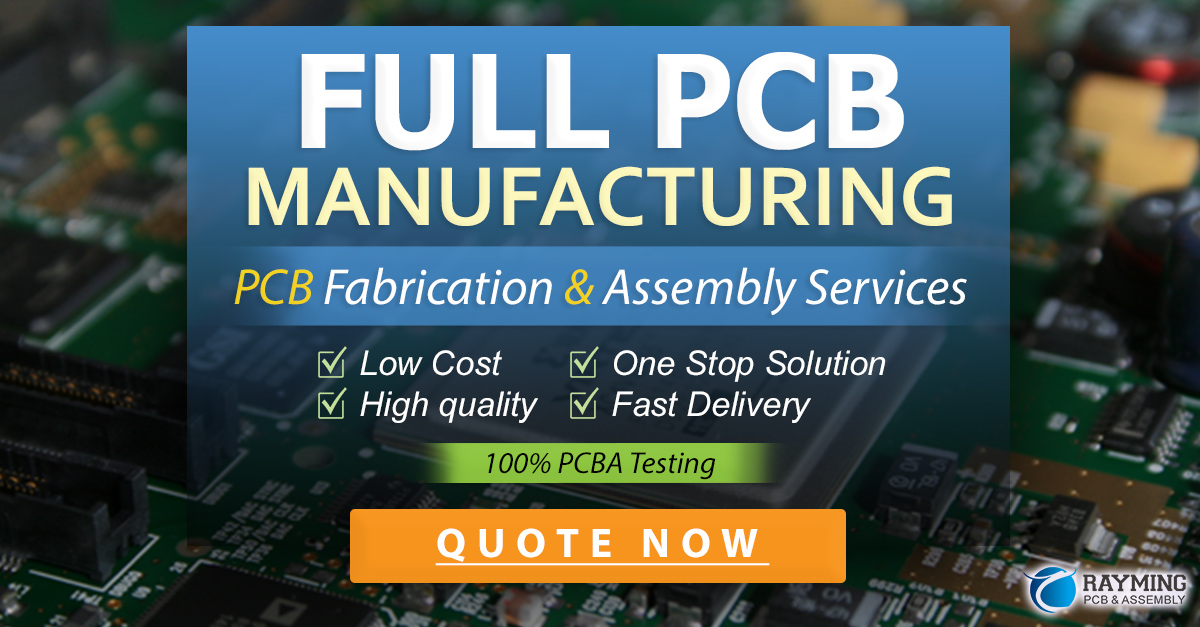
Applications of Rigid-Flex PCBs
Rigid-flex PCBs find applications in a wide range of industries and products, thanks to their unique combination of flexibility, reliability, and space-saving properties. Some common applications include:
Wearable Electronics
Wearable devices, such as smartwatches, fitness trackers, and medical monitoring systems, often require PCBs that can conform to the shape of the human body and withstand repeated flexing. Rigid-flex PCBs are an ideal solution for these applications, as they can be designed to fit within the compact form factors of wearable devices while providing reliable performance and connectivity.
Aerospace and Defense
In aerospace and defense applications, electronic systems must be able to withstand harsh environments, including extreme temperatures, vibrations, and shocks. Rigid-flex PCBs offer increased reliability and durability compared to traditional PCBs, making them well-suited for use in aircraft, satellites, and military equipment. Additionally, the space-saving properties of rigid-flex PCBs are particularly beneficial in these applications, where size and weight are critical factors.
Medical Devices
Medical devices, such as implantable sensors, surgical instruments, and diagnostic equipment, require PCBs that are reliable, compact, and biocompatible. Rigid-flex PCBs can be designed to meet the strict regulatory requirements of the medical industry, while also providing the necessary flexibility and connectivity for these devices. The use of biocompatible materials and surface finishes ensures that rigid-flex PCBs can be safely used in medical applications.
Automotive Electronics
The automotive industry is increasingly relying on advanced electronic systems for vehicle control, communication, and entertainment. Rigid-flex PCBs are well-suited for automotive applications, as they can withstand the harsh environmental conditions and vibrations experienced by vehicles. Additionally, the space-saving properties of rigid-flex PCBs allow for the integration of more features and functionality into vehicle electronic systems without increasing their size or weight.
Consumer Electronics
Consumer electronics, such as smartphones, tablets, and gaming devices, are continually pushing the boundaries of performance and functionality in ever-smaller form factors. Rigid-flex PCBs enable the creation of compact, high-density electronic packages that can accommodate the latest features and technologies. The flexibility and reliability of rigid-flex PCBs also make them ideal for use in foldable and bendable devices, which are becoming increasingly popular in the consumer electronics market.
Advantages of Rigid-Flex PCBs Over Traditional PCBs
Rigid-flex PCBs offer several advantages over traditional rigid PCBs, making them an attractive choice for a wide range of applications. Some of the key advantages include:
-
Reduced size and weight: By eliminating the need for connectors and cables, rigid-flex PCBs enable the creation of more compact and lightweight electronic devices. This is particularly beneficial in applications where space and weight are critical factors, such as aerospace, wearables, and portable electronics.
-
Improved reliability: Rigid-flex PCBs have fewer interconnects and connectors compared to traditional PCBs, which reduces the risk of connection failures and improves overall system reliability. Additionally, the flexible portions of rigid-flex PCBs can absorb stress and vibrations, further enhancing their durability.
-
Enhanced design flexibility: The ability to bend and fold rigid-flex PCBs allows for greater design freedom and the creation of devices with unique form factors. This flexibility enables designers to optimize the placement of components and routing of traces, leading to improved performance and functionality.
-
Better signal integrity: Rigid-flex PCBs minimize signal loss and interference by reducing the length of interconnects and providing better shielding. This is particularly important in high-speed and high-frequency applications, where signal integrity is critical to system performance.
-
Cost-effectiveness: Although the initial cost of rigid-flex PCBs may be higher than traditional PCBs, they can lead to overall cost savings in the long run. The reduced assembly time, fewer components, and improved reliability of rigid-flex PCBs can result in lower manufacturing and maintenance costs over the life of the product.
Challenges and Limitations of Rigid-Flex PCBs
Despite their numerous advantages, rigid-flex PCBs also present some challenges and limitations that designers and manufacturers must consider:
-
Higher initial cost: The materials, design, and manufacturing processes for rigid-flex PCBs are more complex and expensive compared to traditional PCBs. This higher initial cost may be a barrier for some applications, particularly those with tight budget constraints.
-
Complex design process: Designing a rigid-flex PCB requires specialized knowledge and tools to ensure proper layer stack-up, bend radius, and component placement. This complexity can lead to longer design cycles and increased development costs.
-
Limited supplier options: Not all PCB manufacturers have the capabilities and expertise to produce high-quality rigid-flex PCBs. This limited supplier base can result in longer lead times and reduced flexibility in terms of pricing and customization options.
-
Manufacturing challenges: The manufacturing process for rigid-flex PCBs is more complex and requires specialized equipment and processes. This can lead to higher manufacturing costs and longer production times compared to traditional PCBs.
-
Reduced thermal dissipation: The flexible portions of rigid-flex PCBs have a lower Thermal conductivity compared to rigid substrates, which can limit their ability to dissipate heat. This can be a challenge in applications with high power densities or operating in high-temperature environments.
Future Trends in Rigid-Flex PCB Technology
As the demand for smaller, more complex, and more reliable electronic devices continues to grow, rigid-flex PCB technology is expected to evolve to meet these challenges. Some of the future trends in rigid-flex PCB technology include:
-
Advanced materials: The development of new flexible substrates and conductive materials with improved electrical, thermal, and mechanical properties will enable the creation of rigid-flex PCBs with enhanced performance and reliability.
-
High-density interconnects (HDI): The integration of HDI technologies, such as micro vias and fine-pitch traces, will allow for the creation of even more compact and complex rigid-flex PCBs.
-
Embedded components: The integration of passive and active components within the layers of a rigid-flex PCB will further reduce the size and weight of electronic devices while improving their performance and functionality.
-
3D printing: The use of 3D printing technologies for the fabrication of rigid-flex PCBs will enable faster prototyping, greater design flexibility, and the creation of unique form factors.
-
Intelligent systems: The integration of sensors, antennas, and other smart components into rigid-flex PCBs will enable the creation of intelligent systems that can adapt to their environment and provide real-time data and feedback.
Frequently Asked Questions (FAQ)
-
Q: What is a rigid-flex PCB?
A: A rigid-flex PCB is a type of printed circuit board that combines rigid and flexible substrates, allowing for the creation of complex, compact, and reliable electronic devices. -
Q: What are the benefits of using a rigid-flex PCB?
A: Rigid-flex PCBs offer several benefits, including reduced size and weight, improved reliability, enhanced design flexibility, better signal integrity, and cost-effectiveness. -
Q: What industries commonly use rigid-flex PCBs?
A: Rigid-flex PCBs are used in a wide range of industries, including aerospace, defense, medical devices, automotive electronics, consumer electronics, and wearable technology. -
Q: How does the manufacturing process for rigid-flex PCBs differ from traditional PCBs?
A: The manufacturing process for rigid-flex PCBs is more complex and involves additional steps, such as laminating flexible and rigid substrates, precise alignment, and specialized cutting and forming techniques. -
Q: What are some of the challenges and limitations of rigid-flex PCBs?
A: Some of the challenges and limitations of rigid-flex PCBs include higher initial costs, complex design processes, limited supplier options, manufacturing challenges, and reduced thermal dissipation compared to traditional rigid PCBs.
Conclusion
Rigid-flex PCBs offer a unique combination of flexibility, reliability, and space-saving properties that make them an attractive choice for a wide range of applications. By combining the benefits of both rigid and flexible substrates, rigid-flex PCBs enable the creation of highly complex and compact electronic devices that can withstand harsh environments and repeated flexing.
As the demand for smaller, more powerful, and more reliable electronic devices continues to grow, rigid-flex PCB technology is expected to evolve and adapt to meet these challenges. With advancements in materials, manufacturing processes, and integration technologies, rigid-flex PCBs will continue to play a critical role in shaping the future of the electronics industry.
While rigid-flex PCBs present some challenges and limitations, their numerous advantages often outweigh these drawbacks. By carefully considering the design, manufacturing, and application requirements, designers and manufacturers can leverage the power of rigid-flex PCBs to create innovative, high-performance electronic devices that meet the needs of an increasingly demanding market.
No responses yet