What is PCB Assembly?
PCB assembly, short for printed circuit board assembly, is the process of attaching electronic components to a printed circuit board to create a functional electronic device or product. The PCB acts as the base or substrate that mechanically supports and electrically connects the electronic components using conductive tracks, pads, and other features.
PCB assembly involves several steps, including:
- Solder Paste Application
- Component Placement
- Reflow Soldering
- Inspection and Testing
- Rework and Repair (if needed)
The assembled PCB is then integrated into the final electronic product, such as a smartphone, computer, medical device, automotive component, or industrial control system.
Types of PCB Assembly
There are two main types of PCB assembly:
-
Through-Hole Assembly (THA): In through-hole assembly, the component leads are inserted through drilled holes in the PCB and soldered to pads on the opposite side. This method is typically used for larger components that require stronger mechanical connections, such as connectors, capacitors, and transformers.
-
Surface Mount Assembly (SMA): Surface mount assembly involves placing components directly onto pads on the surface of the PCB and soldering them in place using a reflow oven. SMT components are much smaller than through-hole components, allowing for higher component density and smaller PCB sizes. Most modern electronic devices use surface mount assembly.
Some PCBs use a combination of through-hole and surface mount assembly, known as mixed technology assembly.
PCB Assembly Technology
Solder Paste Application
The first step in PCB assembly is applying solder paste to the pads where components will be placed. Solder paste is a mixture of tiny solder particles suspended in a flux medium. The flux helps to clean the surfaces, prevent oxidation, and promote solder wetting during the reflow process.
There are two main methods for applying solder paste:
-
Stencil Printing: A stencil with apertures corresponding to the PCB pads is aligned over the board, and solder paste is spread over the stencil using a squeegee. The paste is deposited onto the pads through the stencil apertures.
-
Dispensing: For smaller production runs or prototypes, solder paste can be dispensed directly onto the pads using a pneumatic or positive displacement dispenser.
Component Placement
After solder paste application, the components are placed onto the PCB pads. This is typically done using automated pick-and-place machines, which use vacuum nozzles to pick up components from feeders and place them accurately on the board.
For through-hole components, the leads are inserted manually or using automated insertion machines.
Reflow Soldering
Once the components are placed, the PCB undergoes reflow soldering. The board is passed through a reflow oven, which heats the solder paste to a temperature above the melting point of the solder (typically around 240°C for lead-free solder).
The reflow process consists of several stages:
-
Preheat: The board is gradually heated to activate the flux and remove any moisture.
-
Thermal Soak: The temperature is maintained to ensure even heating and flux activation.
-
Reflow: The temperature is raised above the solder melting point, causing the solder to melt and wet the component leads and pads.
-
Cooling: The board is cooled, allowing the solder to solidify and form strong mechanical and electrical bonds.
Inspection and Testing
After reflow soldering, the assembled PCB undergoes inspection and testing to ensure quality and functionality. Some common inspection methods include:
-
Visual Inspection: Operators or automated optical inspection (AOI) systems check for visible defects such as missing components, misaligned components, solder bridges, or insufficient solder.
-
X-Ray Inspection: X-ray imaging is used to inspect solder joints hidden under components, such as ball grid arrays (BGAs) or chip scale packages (CSPs).
-
In-Circuit Testing (ICT): The PCB is placed in a fixture with probes that contact test points on the board. Electrical tests are performed to verify component presence, orientation, and functionality.
-
Functional Testing: The assembled PCB is powered on and tested in its intended operating environment to ensure it performs according to specifications.
Rework and Repair
If defects are found during inspection or testing, the PCB may undergo rework or repair. This involves removing and replacing faulty components, repairing damaged solder joints, or cleaning up solder bridges.
Rework can be done manually using soldering irons, hot air rework stations, or specialized desoldering tools. In some cases, the entire board may need to be stripped and reassembled.
Applications of PCB Assembly
PCB assembly is used in virtually every electronic device or product. Some common applications include:
-
Consumer Electronics: Smartphones, tablets, laptops, televisions, gaming consoles, wearables, etc.
-
Automotive Electronics: Engine control units, infotainment systems, sensors, power management systems, etc.
-
Medical Devices: Diagnostic equipment, monitoring systems, implantable devices, surgical instruments, etc.
-
Industrial Control Systems: Programmable logic controllers (PLCs), motor drives, power supplies, sensors, etc.
-
Aerospace and Defense: Avionics, radar systems, satellite communications, guidance systems, etc.
-
Internet of Things (IoT) Devices: Smart home appliances, security systems, environmental monitoring, asset tracking, etc.
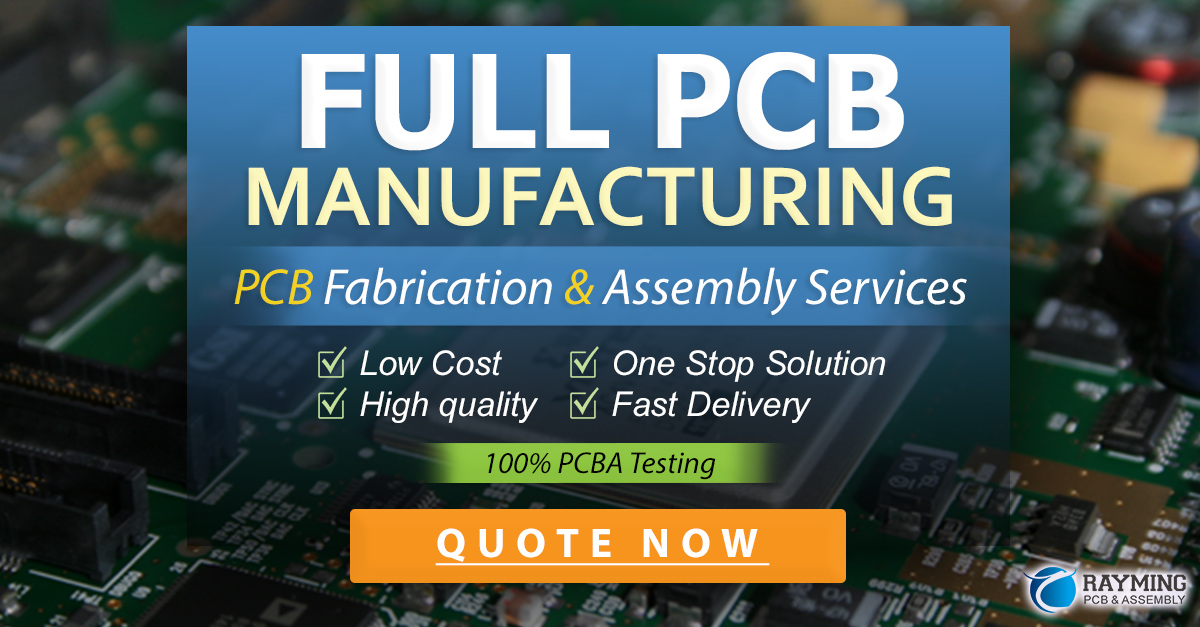
PCB Assembly Service Providers
Many companies specialize in providing PCB assembly services for various industries and applications. These service providers offer a range of capabilities, from prototype assembly to high-volume production.
When choosing a PCB assembly service provider, consider factors such as:
-
Experience and Expertise: Look for a provider with experience in your specific industry or application, as well as expertise in the latest assembly technologies and processes.
-
Quality Management: Ensure the provider has robust quality management systems in place, such as ISO 9001 certification, and follows industry standards like IPC-A-610 for acceptability of electronic assemblies.
-
Manufacturing Capabilities: Consider the provider’s manufacturing capabilities, including the types of PCBs they can assemble (e.g., rigid, flexible, rigid-flex), the component packages they can handle (e.g., BGA, QFN, CSP), and their ability to handle mixed technology assemblies.
-
Testing and Inspection: Look for a provider with comprehensive testing and inspection capabilities, including AOI, X-ray, ICT, and functional testing, to ensure the quality and reliability of your assembled PCBs.
-
Lead Time and Pricing: Consider the provider’s lead times and pricing structure, as well as their ability to handle both small and large production runs.
-
Customer Support: Choose a provider with responsive customer support and a track record of strong communication and collaboration with clients.
Some notable PCB assembly service providers include:
- Foxconn
- Jabil
- Flextronics
- Celestica
- Sanmina
- Benchmark Electronics
- Plexus
- Kimball Electronics
- Venture Corporation
- Zollner Elektronik
Future Trends in PCB Assembly
As electronic devices continue to evolve and become more complex, PCB assembly technology must keep pace to meet the demands of the industry. Some future trends in PCB assembly include:
-
Miniaturization: The trend towards smaller, more compact electronic devices will drive the need for smaller components and higher component density on PCBs. This will require advancements in materials, design, and assembly processes.
-
Advanced Packaging: The adoption of advanced packaging technologies, such as system-in-package (SiP), package-on-package (PoP), and 3D packaging, will enable greater functionality and performance in smaller form factors.
-
Flexible and Stretchable Electronics: The growing demand for wearable devices, medical implants, and IoT sensors will drive the development of flexible and stretchable PCBs that can conform to various shapes and withstand bending and stretching.
-
Additive Manufacturing: 3D printing technologies, such as inkjet printing and aerosol jet printing, may be used to create PCBs and even print components directly onto the board, enabling faster prototyping and more complex geometries.
-
Automation and Industry 4.0: Smart factories and Industry 4.0 principles will drive greater automation, data integration, and process optimization in PCB assembly, improving efficiency, quality, and traceability.
-
Sustainable Manufacturing: There will be a growing emphasis on sustainable PCB assembly practices, including the use of eco-friendly materials, renewable energy, and waste reduction and recycling initiatives.
Frequently Asked Questions (FAQ)
-
What is the difference between PCB fabrication and PCB assembly?
PCB fabrication is the process of manufacturing the bare printed circuit board, while PCB assembly involves attaching electronic components to the fabricated PCB to create a functional electronic assembly. -
What is the most common method for PCB assembly?
Surface mount assembly (SMA) is the most common method for PCB assembly, as it allows for smaller components, higher component density, and automated assembly processes compared to through-hole assembly. -
What is the purpose of solder paste in PCB assembly?
Solder paste is used to provide a mechanical and electrical connection between electronic components and the PCB pads. It consists of tiny solder particles suspended in a flux medium, which helps to clean the surfaces, prevent oxidation, and promote solder wetting during the reflow soldering process. -
What is the difference between reflow soldering and wave soldering?
Reflow soldering is used for surface mount components and involves applying solder paste to the PCB pads, placing the components, and heating the assembly in a reflow oven to melt the solder and form connections. Wave soldering is used for through-hole components and involves passing the PCB over a molten solder wave, which wets the component leads and PCB holes to form connections. -
How can I ensure the quality and reliability of my assembled PCBs?
To ensure the quality and reliability of your assembled PCBs, work with an experienced and reputable PCB assembly service provider that follows industry standards and has robust quality management systems in place. Implement comprehensive inspection and testing procedures, such as AOI, X-ray, ICT, and functional testing, to identify and address any defects or issues early in the production process.
No responses yet