Introduction to PTH PCB
Plated through hole (PTH) is a crucial technology in the fabrication of printed circuit boards (PCBs). PTH refers to the process of creating electrical connections between the layers of a multi-layer PCB by drilling holes through the board and plating them with a conductive material, typically copper. This technique enables the creation of complex, high-density PCB designs that are essential for modern electronic devices.
The Importance of PTH in PCB Manufacturing
PTH technology has revolutionized the PCB industry by providing several key benefits:
- Enables the creation of multi-layer PCBs
- Allows for higher component density
- Improves signal integrity
- Enhances mechanical strength and durability
Without PTH, the development of advanced electronic devices, such as smartphones, computers, and medical equipment, would not be possible.
The PTH PCB Manufacturing Process
The manufacturing process for PTH PCBs involves several critical steps to ensure the creation of high-quality, reliable boards.
Step 1: Drilling
The first step in the PTH process is drilling holes through the PCB substrate. The holes are typically drilled using computer numerical control (CNC) machines, which ensure precise hole placement and size. The diameter of the holes can range from 0.2 mm to 6.35 mm, depending on the specific requirements of the PCB design.
Step 2: Desmearing
After drilling, the holes must undergo a process called desmearing to remove any debris or resin smear that may have formed during the drilling process. Desmearing is typically performed using a chemical or plasma etching process, which cleans the hole walls and prepares them for the subsequent plating process.
Step 3: Electroless Copper Deposition
The next step is to deposit a thin layer of copper onto the hole walls using an electroless plating process. This process involves immersing the PCB in a chemical bath containing copper ions, which adhere to the hole walls and form a uniform, conductive layer. The electroless copper layer serves as a foundation for the subsequent electrolytic copper plating process.
Step 4: Electrolytic Copper Plating
Once the electroless copper layer is in place, the PCB undergoes an electrolytic copper plating process to build up the thickness of the copper layer inside the holes. This process involves applying an electric current to the PCB while it is immersed in an electrolytic bath containing copper sulfate. The electric current causes the copper ions to migrate and deposit onto the hole walls, forming a thick, conductive layer that ensures reliable electrical connections between the PCB Layers.
Step 5: Copper Etching
After the holes have been plated, the excess copper on the surface of the PCB is removed using a copper etching process. This process typically involves applying a photoresist mask to the PCB surface, which protects the desired copper traces while exposing the unwanted copper. The PCB is then immersed in an etching solution, which dissolves the exposed copper, leaving only the desired traces and plated holes intact.
Step 6: Solder Mask Application
The final step in the PTH PCB manufacturing process is the application of a solder mask. The solder mask is a protective layer that covers the PCB surface, leaving only the exposed pads and plated holes for component assembly. The solder mask helps to prevent short circuits, improves the PCB’s resistance to environmental factors, and enhances the board’s overall appearance.
Advantages of PTH PCBs
PTH PCBs offer several advantages over other types of PCBs, such as surface mount technology (SMT) boards.
1. Mechanical Strength
PTH PCBs provide superior mechanical strength compared to SMT boards. The plated holes act as anchors, securely holding components in place and preventing them from becoming dislodged due to vibration or physical stress. This makes PTH PCBs ideal for applications that require high reliability, such as aerospace, military, and automotive electronics.
2. Thermal Management
The plated holes in PTH PCBs also serve as efficient thermal conduits, allowing heat to dissipate more effectively from components to the PCB substrate. This improved thermal management helps to prevent component overheating and enhances the overall reliability and longevity of the PCB.
3. Compatibility with Through-Hole Components
PTH PCBs are compatible with through-hole components, which are still widely used in certain applications due to their robustness and ease of manual assembly. Through-hole components, such as connectors, transformers, and large capacitors, can be easily inserted and soldered into the plated holes, ensuring a secure and reliable connection.
4. Suitability for High-Power Applications
PTH PCBs are well-suited for high-power applications, as the plated holes can accommodate thicker copper traces and larger component leads. This allows for higher current-carrying capacity and improved power handling compared to SMT boards.
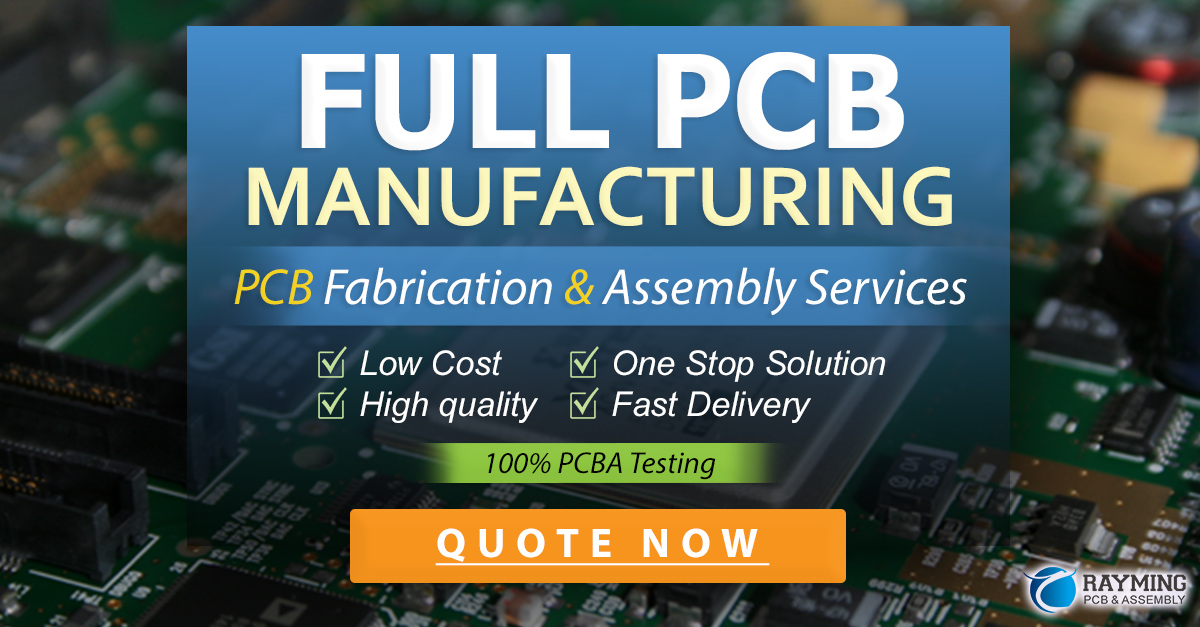
Challenges and Limitations of PTH PCBs
Despite their numerous advantages, PTH PCBs also present some challenges and limitations that must be considered during the design and manufacturing process.
1. Higher Manufacturing Costs
PTH PCBs generally have higher manufacturing costs compared to SMT boards due to the additional drilling and plating processes involved. The cost of drilling and plating holes increases with the number of holes required, making PTH PCBs less economical for high-volume production runs.
2. Larger Footprint
PTH components typically have a larger footprint than their SMT counterparts, which can limit the component density and overall miniaturization of the PCB. This can be a disadvantage in applications where space is at a premium, such as mobile devices and wearable electronics.
3. Potential for Plating Defects
The plating process for PTH PCBs can sometimes result in defects, such as voids, nodules, or thin plating. These defects can compromise the electrical and mechanical integrity of the plated holes, leading to reliability issues. Careful process control and quality assurance measures are necessary to minimize the occurrence of plating defects.
4. Difficulty in Rework and Repair
Reworking or repairing PTH PCBs can be more challenging than SMT boards due to the presence of plated holes. Removing and replacing components can be more time-consuming and may require specialized equipment, such as desoldering tools and microscopes.
Applications of PTH PCBs
PTH PCBs find applications in a wide range of industries and products, including:
- Aerospace and Defense
- Avionics
- Radar systems
- Satellite communications
- Automotive
- Engine control units (ECUs)
- Infotainment systems
- Safety systems (e.g., airbags, ABS)
- Medical Devices
- Diagnostic equipment
- Monitoring systems
- Implantable devices
- Industrial Automation
- Programmable logic controllers (PLCs)
- Sensors and actuators
- Motor drives
- Consumer Electronics
- Home appliances
- Audio/video equipment
- Gaming consoles
Future Trends in PTH PCB Technology
As the electronics industry continues to evolve, PTH PCB technology is also adapting to meet the changing demands of the market.
1. Hybrid PCBs
Hybrid PCBs, which combine both PTH and SMT technologies, are becoming increasingly popular. These boards leverage the advantages of both technologies, allowing for greater design flexibility and optimization of component placement. Hybrid PCBs enable the use of through-hole components for power handling and mechanical strength, while utilizing SMT components for higher density and miniaturization.
2. High-Density Interconnect (HDI) PCBs
HDI PCBs are a type of multi-layer PCB that features fine-pitch traces, small vias, and high component density. HDI PCBs often incorporate microvias, which are small, laser-drilled holes that provide electrical connections between layers. The combination of PTH and microvia technology allows for the creation of highly complex, compact PCB designs that are suitable for advanced electronic devices.
3. Advances in Materials and Processes
Ongoing research and development in PCB materials and manufacturing processes are leading to improvements in the performance and reliability of PTH PCBs. For example, the use of high-temperature laminates and low-loss dielectrics can enhance the thermal and electrical properties of the PCBs. Advances in plating technologies, such as copper filling of microvias, can further improve the reliability and signal integrity of high-density PCB designs.
Frequently Asked Questions (FAQ)
- What is the difference between PTH and SMT PCBs?
-
PTH PCBs have plated holes for through-hole component assembly, while SMT PCBs have surface-mounted components without plated holes. PTH PCBs offer better mechanical strength and thermal management, while SMT PCBs allow for higher component density and smaller footprints.
-
Can PTH and SMT components be used on the same PCB?
-
Yes, hybrid PCBs combine both PTH and SMT technologies, allowing for the use of both through-hole and surface-mounted components on the same board. This enables greater design flexibility and optimization of component placement.
-
What are the common hole sizes for PTH PCBs?
-
The diameter of the holes in PTH PCBs can range from 0.2 mm to 6.35 mm, depending on the specific requirements of the PCB design. Common hole sizes include 0.5 mm, 0.8 mm, 1.0 mm, and 2.54 mm (0.1 inch).
-
How does the plating process work in PTH PCBs?
-
The plating process in PTH PCBs involves depositing a thin layer of copper onto the hole walls using an electroless plating process, followed by an electrolytic copper plating process to build up the thickness of the copper layer. This ensures reliable electrical connections between the PCB layers.
-
What are the main advantages of using PTH PCBs?
- PTH PCBs offer several advantages, including superior mechanical strength, improved thermal management, compatibility with through-hole components, and suitability for high-power applications. These benefits make PTH PCBs ideal for applications that require high reliability and robustness.
Conclusion
Plated through hole (PTH) technology is a fundamental aspect of PCB fabrication, enabling the creation of complex, multi-layer boards that are essential for modern electronic devices. By providing reliable electrical connections between layers, PTH PCBs offer numerous advantages, such as mechanical strength, thermal management, and compatibility with through-hole components.
Despite some challenges and limitations, PTH PCBs continue to play a crucial role in various industries, including aerospace, automotive, medical devices, and industrial automation. As the electronics industry evolves, PTH technology is adapting to meet the changing demands of the market, with trends such as hybrid PCBs, HDI PCBs, and advances in materials and processes driving the future of PCB fabrication.
By understanding the importance, manufacturing process, advantages, and applications of PTH PCBs, engineers and designers can make informed decisions when developing electronic products that meet the ever-increasing demands for performance, reliability, and functionality.
No responses yet