What is PCB Etching with Ferric Chloride?
PCB etching with ferric chloride is a common method used by electronics hobbyists and professionals to create custom printed circuit boards (PCBs). The process involves transferring a circuit design onto a copper-clad board and then dissolving away the unwanted copper using a ferric chloride solution, leaving behind the desired circuit traces.
Ferric chloride (FeCl3) is an acidic salt that acts as a powerful oxidizing agent. When it comes into contact with copper, it reacts and dissolves the metal, effectively “etching” away the unwanted portions of the copper layer.
Advantages of Using Ferric Chloride for PCB Etching
- Readily available and relatively inexpensive
- Easy to use and control
- Provides clean and precise etching results
- Suitable for both single and double-sided PCBs
Disadvantages of Using Ferric Chloride for PCB Etching
- Can be messy and stain surfaces if not handled carefully
- Requires proper disposal as it is considered hazardous waste
- Etching process can be time-consuming for large or complex designs
Preparing the PCB for Etching
Materials Needed
- Copper-clad PCB Board
- PCB design printed on transparency film
- UV exposure unit or sunlight
- Developing solution (sodium hydroxide or potassium carbonate)
- Ferric chloride solution
- Plastic or glass container for etching
- Rubber gloves and protective eyewear
- Drill or punch for making holes in the PCB
Steps for PCB Preparation
-
Design the PCB: Create your PCB design using EDA (Electronic Design Automation) software or hand-draw it on paper. Ensure the design is properly laid out and includes all necessary components and traces.
-
Print the PCB design: Print the design onto a transparency film using a laser printer. Make sure the printed design is dark and opaque to block UV light during exposure.
-
Clean the copper-clad board: Clean the surface of the copper-clad board with steel wool or fine sandpaper to remove any oxidation or dirt. This will help the photoresist adhere better to the copper surface.
-
Apply photoresist: Apply a thin, even layer of photoresist to the copper surface of the PCB. This can be done using pre-sensitized boards or by applying liquid photoresist and allowing it to dry.
-
Expose the PCB: Place the transparency film with the printed design onto the photoresist-coated PCB. Ensure proper alignment and secure it in place. Expose the PCB to UV light for the recommended time (usually a few minutes) to harden the photoresist where it is not covered by the design.
-
Develop the PCB: Immerse the exposed PCB in the developing solution to remove the unexposed photoresist, revealing the copper traces that will form your circuit. Agitate gently until the design is fully visible.
-
Rinse and dry: Rinse the developed PCB with water and dry it thoroughly with compressed air or a lint-free cloth.
Etching the PCB with Ferric Chloride
Preparing the Ferric Chloride Solution
Ferric chloride typically comes in crystalline or liquid form. If using the crystalline form, mix it with water according to the manufacturer’s instructions to create the etching solution. The ideal concentration is usually around 40-45% ferric chloride by weight.
When handling ferric chloride, always wear rubber gloves, protective eyewear, and work in a well-ventilated area to avoid inhaling fumes.
Etching Process
-
Pour the ferric chloride solution into a plastic or glass container large enough to accommodate your PCB.
-
Immerse the prepared PCB into the solution, ensuring it is completely submerged. You can use a plastic or glass weight to keep the PCB from floating.
-
Agitate the container gently to ensure even etching and to prevent air bubbles from forming on the PCB surface.
-
Monitor the etching progress closely. The time required for complete etching depends on factors such as the solution’s temperature, concentration, and the size of the PCB. On average, etching takes between 15-45 minutes.
-
Periodically check the PCB by removing it from the solution and rinsing it with water. If etching is incomplete, return the PCB to the solution and continue the process.
-
Once etching is complete, remove the PCB from the solution and rinse it thoroughly with water.
-
Strip the remaining photoresist from the PCB using a suitable solvent (e.g., acetone) or by gently scrubbing with steel wool.
-
Rinse the PCB again with water and dry it completely.
Tips for Successful Etching
- Maintain the ferric chloride solution at a temperature between 50-55°C (122-131°F) to accelerate the etching process. You can use a slow cooker or double boiler to heat the solution safely.
- Regularly stir or agitate the solution to ensure even etching and prevent the formation of air bubbles on the PCB surface.
- As the etching solution becomes saturated with dissolved copper, its effectiveness decreases. Replenish the solution or replace it entirely when etching times become excessively long.
- To extend the life of your etching solution, consider using an acid-resistant air pump to oxygenate the solution between uses. This helps to convert the dissolved copper back into copper chloride, allowing the solution to be reused more times.
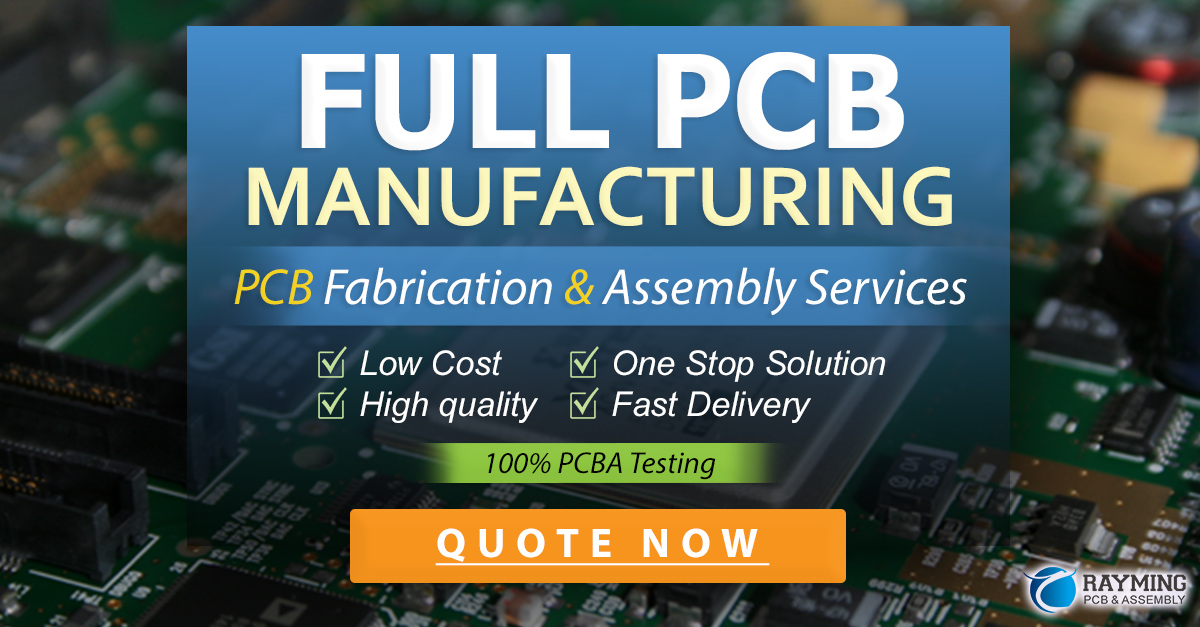
Post-Etching PCB Processing
After etching, there are a few additional steps to complete your PCB:
-
Drilling: Drill any necessary holes in the PCB for component leads and mounting using a drill press or hand drill. Use a drill bit slightly larger than the component leads to ensure a snug fit.
-
Tinning: Apply a thin layer of solder to the copper traces to protect them from oxidation and improve solderability. This can be done using a soldering iron and solder wire or by immersing the PCB in a tin-plating solution.
-
Silkscreening: If desired, apply silkscreen labels to the PCB to indicate component placement, values, and other relevant information. This can be done using a silkscreen stencil and ink or by printing labels on self-adhesive paper and applying them to the PCB.
-
Solder mask: For added protection and insulation, consider applying a solder mask to the PCB. This is a thin, heat-resistant layer that covers the copper traces, leaving only the pads exposed for soldering. Solder mask can be applied using a photoresist process similar to etching or by brushing on a liquid solder mask.
Safety and Environmental Considerations
Ferric chloride is an acidic and corrosive substance that can cause skin and eye irritation, as well as stain surfaces and clothing. Always take proper safety precautions when handling ferric chloride:
- Wear rubber gloves, protective eyewear, and a lab coat or apron to protect your skin and clothing.
- Work in a well-ventilated area to avoid inhaling fumes.
- Keep ferric chloride solutions away from heat sources and open flames, as they can release toxic gases when heated.
- Store ferric chloride in clearly labeled, acid-resistant containers, away from children and pets.
Proper disposal of used ferric chloride is crucial to prevent environmental damage. Ferric chloride is considered hazardous waste and should never be poured down the drain or disposed of in regular trash. Contact your local waste management authority for guidance on proper disposal methods in your area.
Some eco-friendly alternatives to ferric chloride etching include:
- Copper chloride etching: This method uses a less hazardous solution of copper chloride and hydrochloric acid, which can be regenerated and reused multiple times.
- Sodium persulfate etching: Sodium persulfate is a milder etchant that is less harmful to the environment than ferric chloride. However, it has a slower etching rate and may require heating for optimal performance.
Frequently Asked Questions (FAQ)
1. Can I reuse ferric chloride etching solution?
Yes, ferric chloride solution can be reused multiple times until it becomes saturated with dissolved copper and loses its effectiveness. To extend the life of the solution, you can oxygenate it between uses with an acid-resistant air pump.
2. How long does PCB etching with ferric chloride take?
The etching time depends on factors such as the solution’s temperature, concentration, and the size of the PCB. On average, etching takes between 15-45 minutes. Regularly check the progress and remove the PCB once all unwanted copper has been dissolved.
3. What should I do if I get ferric chloride on my skin or in my eyes?
If ferric chloride comes into contact with your skin, immediately rinse the affected area with plenty of water for at least 15 minutes. If it gets into your eyes, flush them with water for at least 15 minutes and seek medical attention. Always wear protective gloves and eyewear when handling ferric chloride.
4. Can I use ferric chloride to etch aluminum or other metals?
No, ferric chloride is primarily used for etching copper. It is not effective for etching aluminum or other metals commonly used in PCB fabrication.
5. How do I dispose of used ferric chloride solution?
Ferric chloride is considered hazardous waste and should be disposed of according to your local regulations. Contact your local waste management authority for guidance on proper disposal methods in your area. Never pour ferric chloride down the drain or dispose of it in regular trash.
Conclusion
PCB etching with ferric chloride is a popular and effective method for creating custom printed circuit boards. By following proper safety precautions and etching techniques, you can achieve clean, precise results suitable for a wide range of electronics projects. Remember to handle ferric chloride with care and dispose of it responsibly to minimize environmental impact.
As you gain experience with PCB etching, experiment with different designs, techniques, and materials to refine your skills and create increasingly complex and professional-looking PCBs.
Factor | Effect on Etching Time |
---|---|
Solution Temperature | Higher temperatures accelerate etching |
Solution Concentration | Higher concentrations accelerate etching |
PCB size | Larger PCBs require longer etching times |
Agitation | Gentle agitation promotes even etching and reduces etching time |
No responses yet