Introduction to PCB Assembly and Panelization
Printed Circuit Board (PCB) assembly is the process of soldering electronic components onto a PCB to create a functional electronic device. In order to efficiently assemble PCBs, manufacturers often use a technique called panelization, which involves arranging multiple PCBs on a single panel for production.
Panelization offers several advantages in PCB assembly, including:
- Increased production efficiency
- Reduced handling and manufacturing costs
- Improved quality control
- Simplified testing and inspection
Types of PCB Panels
There are two main types of PCB panels used in assembly:
-
Scoring Panel: PCBs are arranged on a single panel with pre-cut break-off tabs, allowing individual boards to be easily separated after assembly.
-
Routing Panel: PCBs are arranged on a single panel and separated using a routing machine after assembly, which cuts along the designated paths between the boards.
Key Considerations for PCB Panel Design
When designing a PCB panel for assembly, several factors must be taken into account to ensure optimal production efficiency and quality. These include:
1. Panel Size and Material
The size of the PCB panel is determined by the dimensions of the individual PCBs and the number of boards to be included on a single panel. Common panel sizes include:
Panel Size | Dimensions (mm) |
---|---|
Small | 100 x 100 |
Medium | 200 x 200 |
Large | 300 x 300 |
The material used for the PCB panel is typically FR-4, a glass-reinforced epoxy laminate that offers excellent electrical insulation and mechanical stability.
2. Board Orientation and Spacing
PCBs should be oriented on the panel in a way that maximizes the number of boards per panel while ensuring adequate spacing between the boards for easy separation and to avoid damage during assembly. The minimum spacing between boards depends on the separation method used:
Separation Method | Minimum Spacing (mm) |
---|---|
Scoring | 1.5 |
Routing | 2.0 |
3. Fiducial Marks and Tooling Holes
Fiducial marks are used by Pick-and-Place machines and other automated assembly equipment to accurately position and orient the PCB panel during the assembly process. These marks should be placed at the corners of the panel and near each individual PCB.
Tooling holes are used to secure the PCB panel during assembly and should be placed along the edges of the panel, ensuring they do not interfere with the individual PCBs.
4. Panelization Methods
There are two primary methods for panelizing PCBs:
-
Tab Routing: PCBs are connected to the panel using small tabs, which are milled away after assembly to separate the individual boards.
-
V-Scoring: V-shaped grooves are cut along the edges of each PCB, allowing the boards to be easily broken away from the panel after assembly.
The choice of panelization method depends on factors such as the size and shape of the PCBs, the required board density, and the capabilities of the assembly equipment.
Assembly Process Considerations
When assembling PCBs using panelized boards, there are several key considerations to ensure optimal efficiency and quality:
1. Solder Paste Application
Solder paste is applied to the PCB panel using a stencil, which is aligned with the panel using the fiducial marks. The stencil apertures must be designed to match the pads on the individual PCBs, ensuring the correct amount of solder paste is deposited for each component.
2. Component Placement
Components are placed on the PCB panel using pick-and-place machines, which use the fiducial marks to accurately position each component. The machine program must be carefully designed to ensure the correct components are placed on each individual PCB.
3. Reflow Soldering
After component placement, the PCB panel is passed through a reflow oven, which melts the solder paste and forms a permanent connection between the components and the PCB. The reflow profile must be carefully controlled to ensure optimal solder joint formation and to avoid damage to the components or the PCB.
4. Panel Separation
Once the assembly process is complete, the individual PCBs must be separated from the panel. For scored panels, this is typically done by manually breaking the boards along the scored lines. For routed panels, a routing machine is used to cut along the designated paths between the boards.
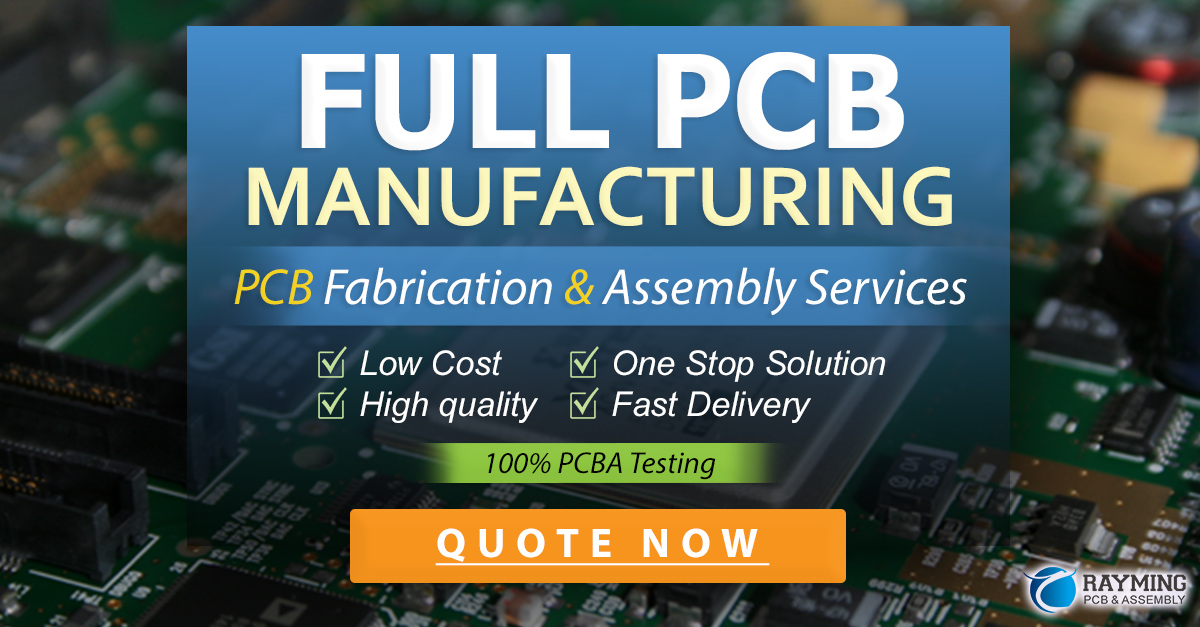
Quality Control and Testing
Panelized PCB assembly offers several advantages for quality control and testing:
-
Automated Optical Inspection (AOI): AOI systems can quickly and accurately inspect the entire PCB panel for defects such as missing components, incorrect component placement, and solder joint issues.
-
In-Circuit Testing (ICT): ICT can be performed on the entire PCB panel, allowing multiple boards to be tested simultaneously, reducing testing time and costs.
-
Functional Testing: Panelization allows for the design of test fixtures that can accommodate multiple PCBs, enabling efficient functional testing of the assembled boards.
Best Practices for PCB Panel Design
To ensure optimal efficiency and quality in panelized PCB assembly, follow these best practices:
- Minimize the number of different panel designs to reduce setup times and costs.
- Use a consistent board orientation and spacing to simplify machine programming and reduce errors.
- Include clear and accurate fiducial marks and tooling holes to ensure precise alignment and positioning.
- Choose the appropriate panelization method based on the specific requirements of the PCBs and the assembly process.
- Work closely with the assembly provider to ensure the panel design is compatible with their equipment and processes.
Frequently Asked Questions (FAQ)
1. What is the purpose of using fiducial marks in PCB Panelization?
Fiducial marks are used by automated assembly equipment to accurately position and orient the PCB panel during the assembly process, ensuring precise component placement and solder joint formation.
2. What is the difference between scoring and routing for PCB panel separation?
Scoring involves creating v-shaped grooves along the edges of each PCB, allowing the boards to be easily broken away from the panel after assembly. Routing uses a machine to cut along designated paths between the boards for separation.
3. How does panelization improve PCB assembly efficiency?
Panelization allows multiple PCBs to be assembled simultaneously on a single panel, reducing handling time and costs, simplifying machine setup, and enabling more efficient testing and inspection processes.
4. What factors should be considered when choosing a panelization method?
Factors to consider when choosing a panelization method include the size and shape of the PCBs, the required board density, the capabilities of the assembly equipment, and the specific requirements of the end application.
5. How can panelization facilitate PCB Testing and quality control?
Panelization enables the use of automated optical inspection (AOI) systems to quickly inspect the entire panel for defects, allows for simultaneous in-circuit testing (ICT) of multiple boards, and facilitates the design of test fixtures for efficient functional testing of the assembled PCBs.
Conclusion
Panelization is a crucial aspect of efficient and cost-effective PCB assembly. By carefully designing PCB panels to optimize board density, minimize handling, and facilitate automated assembly processes, manufacturers can significantly improve production throughput and reduce costs.
When designing PCB panels for assembly, it is essential to consider factors such as panel size and material, board orientation and spacing, fiducial marks and tooling holes, and the appropriate panelization method. Additionally, the assembly process itself must be carefully planned and executed to ensure optimal solder joint formation and component placement accuracy.
By following best practices for PCB panel design and working closely with experienced assembly providers, manufacturers can leverage the benefits of panelization to produce high-quality, reliable electronic devices while minimizing production time and costs.
No responses yet