Introduction to PCB Layout Specifications
When designing printed circuit boards (PCBs) using PCB Artist Layout Software, it is crucial to provide accurate and comprehensive specifications to ensure the desired functionality and manufacturability of the final product. This article will delve into the essential aspects of ordering specifications for PCB Artist Layout Software, covering various topics such as design rules, layer stackup, component placement, routing, and manufacturing requirements.
Understanding the Importance of PCB Layout Specifications
The Role of Specifications in PCB Design
PCB layout specifications play a vital role in the successful design and manufacturing of printed circuit boards. These specifications serve as a blueprint for the PCB designer, providing clear guidelines and constraints to follow throughout the design process. By adhering to well-defined specifications, designers can ensure that the PCB meets the required electrical, mechanical, and manufacturing standards.
Consequences of Incomplete or Inaccurate Specifications
Incomplete or inaccurate PCB layout specifications can lead to several issues, including:
- Design errors and inconsistencies
- Manufacturability problems
- Increased production costs
- Delays in the development timeline
- Suboptimal performance of the final product
To avoid these consequences, it is essential to provide comprehensive and accurate specifications when ordering PCB Artist Layout Software.
Key Elements of PCB Layout Specifications
Design Rules and Constraints
Design rules and constraints form the foundation of PCB layout specifications. These rules define the minimum and maximum values for various parameters, such as:
- Track width and spacing
- Via size and drill diameter
- Clearance between components and tracks
- Solder mask and silkscreen requirements
PCB Artist Layout Software allows designers to set up and manage design rules effectively, ensuring that the layout adheres to the specified constraints.
Layer Stackup and Material Selection
The layer stackup and material selection are critical aspects of PCB layout specifications. The layer stackup defines the arrangement and thickness of the conductive and insulating layers within the PCB. It also specifies the material properties, such as the Dielectric constant and loss tangent, which impact the electrical performance of the board.
When ordering PCB Artist Layout Software, it is essential to provide detailed information about the desired layer stackup, including:
- Number of layers
- Layer thickness and tolerances
- Material type (e.g., FR-4, Rogers, etc.)
- Copper weight and finishing
Component Placement and Orientation
Component placement and orientation play a significant role in the overall performance and manufacturability of the PCB. When specifying component placement requirements, consider the following factors:
- Component footprint and package type
- Placement density and spacing
- Thermal considerations
- Mechanical constraints
- Assembly and manufacturing requirements
PCB Artist Layout Software offers powerful tools for component placement, allowing designers to optimize the layout based on the specified requirements.
Routing and Signal Integrity
Routing and signal integrity are crucial aspects of PCB layout specifications, particularly for high-speed designs. When specifying routing requirements, consider the following factors:
- Signal trace width and spacing
- Impedance control and matching
- Length matching and delay tuning
- Crosstalk and noise reduction techniques
- Ground planes and power distribution
PCB Artist Layout Software provides advanced routing capabilities, including interactive and automatic routing, to ensure optimal signal integrity and performance.
Manufacturing Requirements and Tolerances
Manufacturing requirements and tolerances are essential considerations when ordering PCB Artist Layout Software. These specifications ensure that the designed PCB can be efficiently and reliably manufactured. Some key manufacturing requirements include:
- Minimum hole size and spacing
- Soldermask and silkscreen specifications
- Surface finish requirements (e.g., HASL, ENIG, etc.)
- Panelization and tooling holes
- Testing and inspection requirements
By providing clear manufacturing specifications, designers can minimize the risk of production issues and ensure a smooth transition from design to manufacturing.
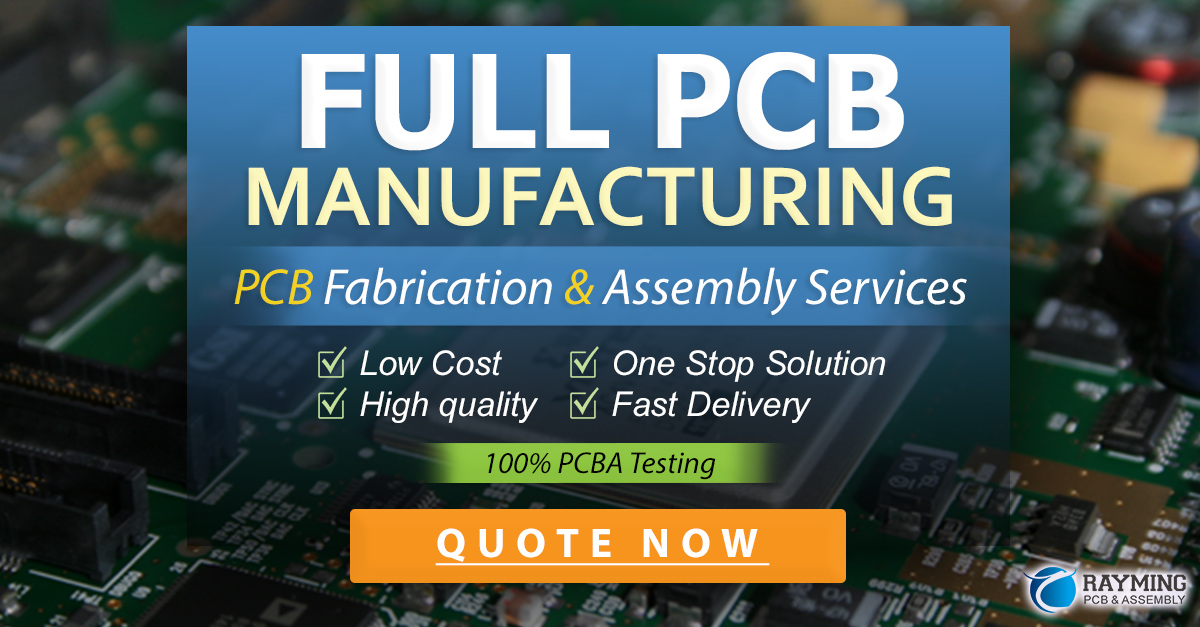
Best Practices for Specifying PCB Layout Requirements
Collaboration with Stakeholders
Effective collaboration with stakeholders is essential when defining PCB layout specifications. Engage with the following stakeholders to gather requirements and constraints:
- Electrical engineers and circuit designers
- Mechanical engineers and product designers
- Manufacturing and assembly teams
- Quality assurance and testing personnel
By involving relevant stakeholders early in the design process, you can ensure that all requirements are captured and incorporated into the PCB layout specifications.
Documentation and Version Control
Proper documentation and version control are crucial for maintaining accurate and up-to-date PCB layout specifications. Consider the following best practices:
- Create a comprehensive design document that outlines all specifications and requirements
- Use a version control system to track changes and revisions
- Maintain a clear naming convention for files and documents
- Regularly review and update the specifications as the design evolves
Effective documentation and version control help prevent errors, reduce confusion, and streamline the design process.
Design for Manufacturability (DFM)
Design for Manufacturability (DFM) is an essential consideration when specifying PCB layout requirements. DFM guidelines ensure that the designed PCB can be efficiently and reliably manufactured. Some key DFM considerations include:
- Adhering to minimum feature sizes and spacing
- Avoiding sharp corners and acute angles
- Providing adequate clearance for tooling and assembly
- Minimizing the number of unique parts and components
- Considering the limitations of the manufacturing process
By incorporating DFM principles into the PCB layout specifications, designers can optimize the design for manufacturability, reducing costs and improving quality.
Verification and Validation
Verification and validation are critical steps in ensuring the accuracy and completeness of PCB layout specifications. Consider the following approaches:
- Perform design rule checks (DRC) to verify adherence to specified constraints
- Conduct electrical rule checks (ERC) to validate connectivity and signal integrity
- Utilize simulation tools to analyze the performance of the PCB
- Generate and review manufacturing files (e.g., Gerber, drill files) for accuracy
- Collaborate with the manufacturing team to validate the specifications
Through thorough verification and validation, designers can identify and resolve issues early in the design process, minimizing the risk of costly errors and delays.
Frequently Asked Questions (FAQ)
-
What are the key elements of PCB layout specifications?
The key elements of PCB layout specifications include design rules and constraints, layer stackup and material selection, component placement and orientation, routing and signal integrity, and manufacturing requirements and tolerances. -
Why is it important to provide accurate PCB layout specifications?
Accurate PCB layout specifications are essential to ensure the desired functionality, manufacturability, and reliability of the final product. Incomplete or inaccurate specifications can lead to design errors, manufacturing issues, increased costs, and delays in the development timeline. -
How can I ensure that my PCB layout specifications are comprehensive?
To ensure comprehensive PCB layout specifications, collaborate with relevant stakeholders (e.g., electrical engineers, mechanical engineers, manufacturing teams) to gather all requirements and constraints. Additionally, maintain proper documentation and version control to track changes and revisions throughout the design process. -
What is Design for Manufacturability (DFM), and why is it important?
Design for Manufacturability (DFM) is an approach that focuses on designing PCBs that can be efficiently and reliably manufactured. DFM guidelines consider factors such as minimum feature sizes, clearances, and manufacturing process limitations. Incorporating DFM principles into PCB layout specifications helps optimize the design for manufacturability, reducing costs and improving quality. -
How can I validate my PCB layout specifications?
To validate PCB layout specifications, perform design rule checks (DRC) and electrical rule checks (ERC) to verify adherence to specified constraints and connectivity requirements. Utilize simulation tools to analyze the performance of the PCB, and generate and review manufacturing files for accuracy. Collaborating with the manufacturing team can also help validate the specifications and identify potential issues early in the design process.
Conclusion
Ordering specifications for PCB Artist Layout Software is a critical aspect of designing high-quality and manufacturable printed circuit boards. By providing comprehensive and accurate specifications, designers can ensure that the PCB meets the required electrical, mechanical, and manufacturing standards. Key elements of PCB layout specifications include design rules and constraints, layer stackup and material selection, component placement and orientation, routing and signal integrity, and manufacturing requirements and tolerances.
To streamline the specification process, designers should collaborate with relevant stakeholders, maintain proper documentation and version control, incorporate Design for Manufacturability (DFM) principles, and conduct thorough verification and validation. By following best practices and leveraging the capabilities of PCB Artist Layout Software, designers can create robust and reliable PCBs that meet the desired functionality and performance requirements.
Specification Category | Key Considerations |
---|---|
Design Rules and Constraints | – Track width and spacing – Via size and drill diameter – Clearance between components and tracks – Solder mask and silkscreen requirements |
Layer Stackup and Material Selection | – Number of layers – Layer thickness and tolerances – Material type (e.g., FR-4, Rogers, etc.) – Copper weight and finishing |
Component Placement and Orientation | – Component footprint and package type – Placement density and spacing – Thermal considerations – Mechanical constraints – Assembly and manufacturing requirements |
Routing and Signal Integrity | – Signal trace width and spacing – Impedance control and matching – Length matching and delay tuning – Crosstalk and noise reduction techniques – Ground planes and power distribution |
Manufacturing Requirements and Tolerances | – Minimum hole size and spacing – Soldermask and silkscreen specifications – Surface finish requirements (e.g., HASL, ENIG, etc.) – Panelization and tooling holes – Testing and inspection requirements |
By carefully considering these specification categories and their associated key considerations, designers can create comprehensive and accurate PCB layout specifications that ensure the success of their PCB design projects.
No responses yet