Introduction to PCB Assembly
Printed Circuit Board (PCB) assembly is the process of soldering or assembly of electronic components to a PCB. It is a core activity in electronics manufacturing where components like capacitors, resistors, and integrated circuits are soldered onto the PCB.
PCB serves as the base for the components to be soldered and interconnected into a functioning circuit or assembly. Modern electronics with their miniature components and high density interconnects have made the PCB assembly process very intricate and complex.
Key Steps Involved in PCB Assembly
The PCB assembly process involves several key steps:
-
Solder Paste Application: Solder paste, a sticky mixture of powdered solder and flux, is applied to the PCB pads where components will be placed. This is done using a stencil or screen printing process.
-
Component Placement: The components are then positioned on the PCB, either manually for low volume or prototypes, or by automated machines for high volume production. The machines pick and place the components from reels or trays and position them precisely on the PCB pads.
-
Reflow Soldering: The PCB with components placed then goes through a reflow oven. The oven heats up the board in a controlled manner, melting the solder paste and creating permanent solder joints between component leads and PCB pads as it cools down.
-
Inspection and Testing: The assembled PCBs are inspected, often by automated optical inspection (AOI) systems to check for any assembly defects like missing components, wrong components, poor solder joints, etc. The boards are then tested electrically to ensure they function as intended.
-
Final Finishing and Packaging: Any final finishing steps like conformal coating for protection are done. The PCBAs are then packaged appropriately for shipping.
Types of PCB Assembly
There are three main types of PCB assembly:
-
Through-Hole Assembly (THA): In THA, component leads are inserted into drilled holes on the PCB and soldered to pads on the opposite side. Though robust, it limits component density.
-
Surface Mount Assembly (SMA): SMA involves placing components directly onto PCB pads and soldering. Components are smaller, allowing higher density. It’s the most common type currently.
-
Mixed Technology Assembly: This is a combination of through-hole and surface mount assembly where both types of components are used on the same PCB.
Challenges in Complex PCB Assembly
As PCBs get more complex with higher component density, finer pitch leads, and smaller form factors, the assembly process faces several challenges:
-
Miniaturization: Smaller components are harder to place accurately and solder reliably. They require precise machines and fine-tuned processes.
-
High Mix Low Volume: Many products now require a high mix of different PCBs in low volumes. This demands flexible assembly lines that can handle frequent changeovers.
-
Quality Control: With miniature components, defects are harder to detect. Advanced inspection systems and stringent quality control are crucial.
-
Lead-Times: Complex PCBs often have long lead-times for components. Careful supply chain management and inventory planning are necessary.
-
Skilled Workforce: Skilled operators and technicians are needed to set up, operate and maintain the complex assembly equipment and processes.
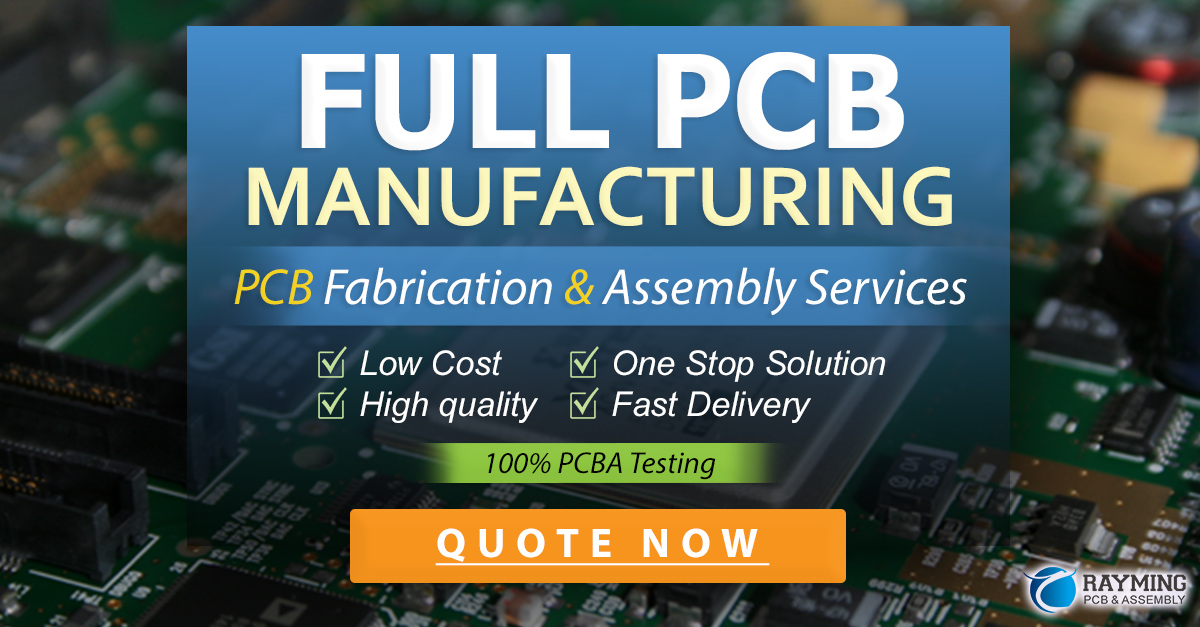
Choosing the Right EMS Partner for Complex PCB Assembly
Given these challenges, it’s crucial to choose the right Electronic Manufacturing Services (EMS) partner for complex PCB assembly. Here are some key factors to consider:
Technical Capabilities
The EMS partner should have:
– Advanced SMT lines capable of handling fine pitch components
– State-of-the-art AOI and testing equipment
– Expertise in complex PCB designs like HDI, rigid-flex, etc.
– Robust engineering support for DFM, testing, etc.
Quality Systems
Look for an EMS with:
– Stringent quality control processes (e.g. IPC standards)
– Regular equipment calibration and maintenance
– Traceability through the production process
– Continuous improvement programs
Supply Chain Management
The EMS should be able to:
– Manage a complex global supply chain
– Have strong relationships with component suppliers
– Provide inventory management and JIT delivery
– Handle component obsolescence
Flexibility and Scalability
Ensure the EMS can:
– Handle both high mix low volume and high volume production
– Scale up quickly as your product demand grows
– Offer flexible terms for NPI, prototyping, etc.
Cost-Effectiveness
While cost is important, don’t compromise on quality and reliability. Look for an EMS that:
– Provides value through efficient processes and automation
– Has cost-reduction programs
– Offers transparent and competitive pricing
– Doesn’t cut corners that could impact product quality
Case Study: Complex PCB Assembly for Medical Devices
ABC Electronics, a leading EMS provider, was approached by a medical device company to manufacture a complex PCB for their new wearable health monitor. The PCB was a 12-layer HDI design with BGA components and 0.3mm pitch CSPs. It also had to meet strict FDA regulations.
ABC’s team worked closely with the client’s design team to optimize the PCB design for manufacturing. They conducted thorough DFM checks and suggested changes to improve yield and reliability.
For the assembly, ABC utilized their state-of-the-art SMT lines with high-precision placement machines. The lines were set up in a clean room environment to prevent contamination. All components and materials were strictly sourced from FDA-approved suppliers and underwent incoming quality control.
The assembled PCBs went through rigorous AOI, X-ray inspection, and functional testing to ensure every board met the stringent quality requirements. ABC also implemented traceability through the production process, crucial for medical devices.
Throughout the project, ABC provided regular updates to the client and worked flexibly to accommodate design changes and timeline pressures. They also managed the supply chain efficiently to ensure on-time delivery despite some long lead-time components.
The end result was a reliable, high-quality PCB assembly that met all the functional and regulatory requirements of the medical device. The client was able to launch their product on time and gain a competitive edge in the market.
This case study illustrates how a capable and experienced EMS partner can navigate the challenges of complex PCB assembly to deliver a successful product.
Frequently Asked Questions (FAQ)
1. What is the difference between PCB fabrication and PCB assembly?
PCB fabrication is the process of manufacturing the bare printed circuit board. It includes designing the circuit, generating gerber files, making the copper traces, drilling holes, and applying solder mask and silkscreen. PCB assembly, on the other hand, is the process of soldering or mounting of electronic components onto the fabricated PCB.
2. What are the common defects in PCB assembly?
Some common defects in PCB assembly include:
– Solder bridging: Unintended solder connection between two leads
– Cold solder joint: Solder joint that looks dull and may crack due to insufficient heat during soldering
– Tombstoning: When a component stands up on one end due to uneven heating
– Missing or misaligned components
– Lifted pads or traces
– Insufficient or excessive solder
3. What is DFM and why is it important?
DFM stands for Design for Manufacturability. It is the practice of designing PCBs in a way that makes them easy to manufacture reliably and cost-effectively. DFM involves adhering to certain design rules and guidelines related to minimum trace widths and spacing, hole sizes, component placement, etc. Proper DFM can help avoid manufacturing issues, improve yield, and reduce costs and time to market.
4. What certifications are important for EMS providers?
Some key certifications to look for in an EMS provider include:
– ISO 9001 for quality management systems
– ISO 13485 for medical device manufacturing
– ISO 14001 for environmental management
– IATF 16949 for automotive industry quality
– IPC certifications for PCB assembly standards
These certifications demonstrate the EMS provider’s commitment to quality, reliability, and industry standards.
5. How can I ensure the security and confidentiality of my PCB design when working with an EMS provider?
To protect your intellectual property when outsourcing PCB assembly, take the following steps:
– Sign a non-disclosure agreement (NDA) with the EMS provider
– Provide only the necessary files and information for manufacturing, not the complete design details
– Work with EMS providers who have secure data handling and storage practices
– Consider splitting the assembly across multiple providers to minimise risk
– Regularly audit your EMS provider’s security practices
A trustworthy EMS partner will have robust measures in place to safeguard your sensitive information.
Conclusion
Complex PCB assembly is a critical aspect of electronics manufacturing that demands deep technical expertise, advanced equipment, and robust processes. Choosing the right EMS partner is crucial to navigate the challenges and ensure a successful product launch.
Look for an EMS provider with strong technical capabilities, stringent quality systems, efficient supply chain management, flexibility, and cost-effectiveness. They should be able to not only handle the complexities of the assembly process but also provide value-added services like DFM, testing, and box build.
With the right partner, complex PCB assembly can be streamlined into a smooth, reliable process that delivers high-quality products consistently. Whether it’s for medical devices, automotive electronics, or industrial controls, a capable EMS provider can be your one-stop solution for all your complex PCB assembly needs.
No responses yet