Introduction to Multilayer PCB Manufacturing
Multilayer PCB manufacturing has become an essential component in the electronics industry, enabling the production of complex and high-density printed circuit boards. These boards are used in a wide range of applications, from consumer electronics to aerospace and military systems. One-stop multilayer PCB manufacturing services have emerged as a convenient and efficient solution for businesses looking to streamline their PCB production process.
What is a Multilayer PCB?
A multilayer PCB is a printed circuit board that consists of three or more conductive copper layers separated by insulating layers. These layers are laminated together using heat and pressure to form a single, compact board. The conductive layers are interconnected through plated through-holes (PTHs) or via, allowing for complex electrical connections between components on different layers.
Advantages of Multilayer PCBs
Multilayer PCBs offer several advantages over single or double-layer boards:
- Increased circuit density: Multilayer PCBs allow for a higher component density, as circuits can be spread across multiple layers, reducing the overall board size.
- Improved signal integrity: By separating signal layers with ground and power planes, multilayer PCBs minimize electromagnetic interference (EMI) and crosstalk, ensuring better signal integrity.
- Enhanced reliability: The compact structure of multilayer PCBs reduces the distance between components, minimizing signal loss and improving overall reliability.
- Space and weight reduction: With the ability to accommodate more components in a smaller area, multilayer PCBs help reduce the overall size and weight of electronic devices.
The Multilayer PCB Manufacturing Process
Step 1: PCB Design and Layout
The first step in multilayer PCB manufacturing is designing the circuit and creating the PCB layout. This process involves using computer-aided design (CAD) software to create a schematic diagram of the circuit and then converting it into a physical layout. The layout determines the placement of components, routing of traces, and the number of layers required.
Step 2: Layer Stackup Planning
Once the layout is finalized, the next step is to plan the layer stackup. This involves determining the arrangement of conductive and insulating layers, as well as the thickness of each layer. The stackup plan must take into account factors such as signal integrity, power distribution, and manufacturing feasibility.
Step 3: Material Selection
The choice of materials for the conductive and insulating layers is crucial for the performance and reliability of the multilayer PCB. Common materials include:
- Conductive layers: Copper foil (standard or high-temperature)
- Insulating layers: FR-4, Rogers, or other high-frequency laminates
- Solder mask: LPI (liquid photoimageable) or dry film
- Silkscreen: Epoxy or UV curable ink
Step 4: Inner Layer Fabrication
The inner layers of the multilayer PCB are fabricated by etching the copper foil laminated onto the insulating substrate. The process involves the following steps:
- Cleaning and deburring the substrate
- Laminating the copper foil
- Applying a photoresist layer
- Exposing the photoresist to UV light through a photomask
- Developing the photoresist to reveal the desired pattern
- Etching away the unwanted copper
- Stripping the remaining photoresist
Step 5: Layer Lamination
After the inner layers are fabricated, they are aligned and laminated together with the prepreg (pre-impregnated) insulating layers using heat and pressure. The lamination process ensures a strong bond between the layers and eliminates any air gaps that could compromise the board’s integrity.
Step 6: Drilling and Plating
To interconnect the layers, holes are drilled through the laminated board using CNC drilling machines. These holes are then plated with copper to create conductive paths between the layers. The plating process involves the following steps:
- Desmearing: Removing any resin smear from the drilled holes
- Electroless copper deposition: Creating a thin conductive layer on the hole walls
- Electrolytic copper plating: Building up the copper thickness to the desired level
Step 7: Outer Layer Processing
The outer layers of the multilayer PCB undergo a similar process to the inner layers, with the addition of solder mask and silkscreen application:
- Etching the outer layer copper patterns
- Applying solder mask to protect the copper traces
- Applying silkscreen for component labels and other markings
Step 8: Surface Finishing
To enhance solderability and protect the exposed copper, a surface finish is applied to the PCB. Common surface finishes include:
- HASL (Hot Air Solder Leveling)
- ENIG (Electroless Nickel Immersion Gold)
- OSP (Organic Solderability Preservative)
- Immersion Silver
- Immersion Tin
Step 9: Electrical Testing and Inspection
Before the multilayer PCB is shipped, it undergoes thorough electrical testing and visual inspection to ensure that it meets the required specifications. This includes:
- Continuity testing
- Insulation resistance testing
- Impedance testing
- Visual inspection for defects
One-Stop Multilayer PCB Manufacturing Services
One-stop multilayer PCB manufacturing services provide a comprehensive solution for businesses looking to outsource their PCB production. These services offer several benefits:
- Time and cost savings: By consolidating all aspects of PCB manufacturing under one roof, one-stop services eliminate the need for multiple vendors, reducing lead times and costs.
- Streamlined communication: With a single point of contact, communication is simplified, minimizing the risk of miscommunication and errors.
- Consistent quality: One-stop services ensure consistent quality control throughout the manufacturing process, as all steps are performed in-house.
- Flexibility and scalability: One-stop services can accommodate a wide range of PCB designs and quantities, from prototypes to large-scale production runs.
When choosing a one-stop multilayer PCB manufacturing service, consider the following factors:
- Technical capabilities: Ensure that the service provider can handle the complexity and layer count of your PCB design.
- Quality certifications: Look for providers with relevant certifications such as ISO 9001, UL, and IPC standards.
- Lead times and pricing: Compare lead times and pricing among different providers to find the best fit for your project timeline and budget.
- Customer support: Choose a provider with responsive and knowledgeable customer support to ensure smooth communication throughout the manufacturing process.
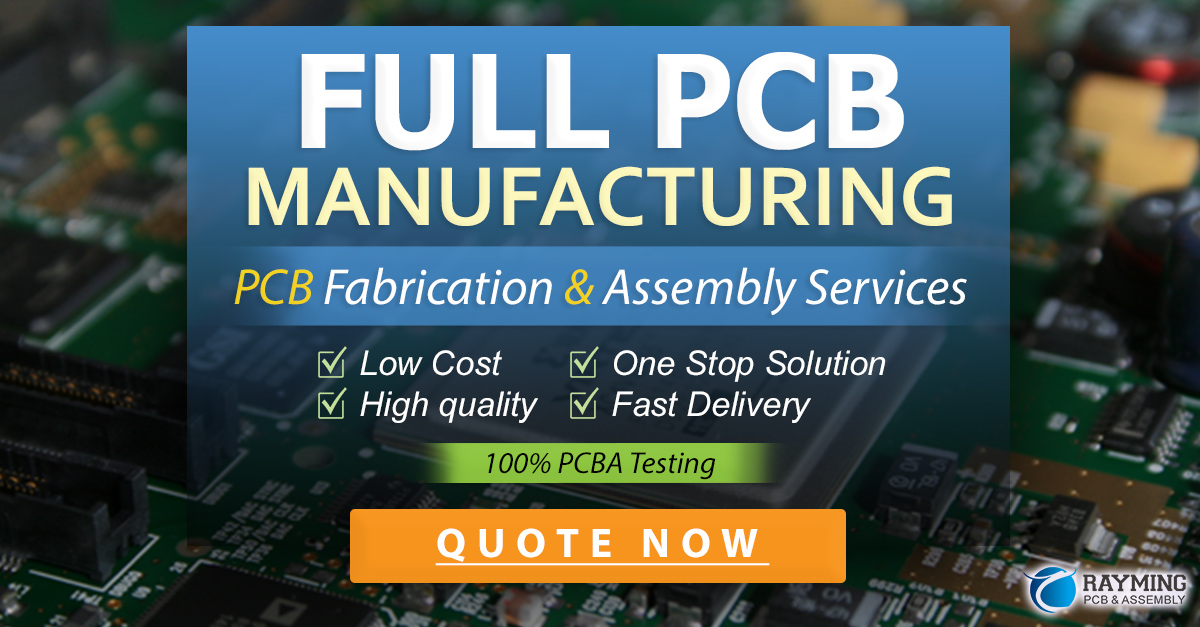
PCB Layer Count and Applications
Multilayer PCBs can be categorized based on the number of layers they contain. The following table provides an overview of common layer counts and their typical applications:
Layer Count | Applications |
---|---|
3-4 | – Simple consumer electronics – Low-power devices – Basic control systems |
6-8 | – Smartphones and tablets – Automotive electronics – Industrial control systems |
10-12 | – High-speed digital devices – Telecommunications equipment – Medical devices |
14-20 | – Complex industrial controls – Aerospace and defense systems – High-performance computing |
22-32 | – Supercomputers – Advanced radar systems – Satellite communication devices |
33-64 | – Cutting-edge research and development – Specialized high-density applications |
As the layer count increases, so does the complexity and cost of the PCB. However, higher layer counts enable more advanced functionality and performance in electronic devices.
Frequently Asked Questions (FAQ)
- What is the minimum and maximum layer count for multilayer PCBs?
-
The minimum layer count for a multilayer PCB is three, while the maximum can reach 64 layers or more, depending on the manufacturer’s capabilities and the specific application requirements.
-
How long does it take to manufacture a multilayer PCB?
-
The lead time for multilayer PCB manufacturing varies depending on the complexity of the design, the layer count, and the manufacturer’s capacity. Typical lead times range from 1-2 weeks for simple designs to 4-6 weeks for more complex, high-layer-count boards.
-
What are the benefits of using a one-stop multilayer PCB manufacturing service?
-
One-stop services offer time and cost savings, streamlined communication, consistent quality control, and flexibility in accommodating different PCB designs and quantities.
-
What factors should I consider when choosing a multilayer PCB manufacturer?
-
When selecting a manufacturer, consider their technical capabilities, quality certifications, lead times, pricing, and customer support to ensure they can meet your project requirements and provide a smooth manufacturing experience.
-
How can I ensure the reliability and performance of my multilayer PCB?
- To ensure reliability and performance, work closely with your PCB manufacturer throughout the design and manufacturing process. Adhere to industry standards and best practices for PCB design, material selection, and testing. Additionally, choose a reputable manufacturer with a proven track record of producing high-quality multilayer PCBs.
Conclusion
Multilayer PCB manufacturing has revolutionized the electronics industry, enabling the production of compact, high-density, and high-performance printed circuit boards. One-stop multilayer PCB manufacturing services provide a convenient and efficient solution for businesses looking to streamline their PCB production process, offering benefits such as time and cost savings, consistent quality, and flexibility.
By understanding the multilayer PCB manufacturing process, layer count options, and key considerations when choosing a manufacturer, businesses can make informed decisions and ensure the success of their electronic products. As technology continues to advance, the demand for multilayer PCBs with higher layer counts and more complex designs will only continue to grow, making one-stop manufacturing services an increasingly valuable partner in the electronics industry.
No responses yet