Introduction to MCPCB
Metal Core Printed Circuit Boards (MCPCBs) are a specialized type of PCB that incorporates a metal substrate, typically aluminum, to enhance thermal management and heat dissipation. Unlike traditional FR-4 PCBs, MCPCBs are designed to efficiently transfer heat away from high-power components, making them ideal for applications such as LED lighting, power electronics, and automotive systems.
What is an MCPCB?
An MCPCB consists of a metal core, usually aluminum, sandwiched between a thin layer of dielectric material and a copper circuit layer. The dielectric layer electrically isolates the copper traces from the metal core while allowing efficient thermal transfer. The metal core acts as a heat sink, quickly dissipating heat generated by the components mounted on the PCB.
Advantages of using MCPCBs
- Enhanced thermal management
- Improved reliability and longevity of components
- Reduced size and weight compared to traditional PCBs with external heat sinks
- Increased power handling capability
- Better mechanical stability and durability
MCPCB Structure and Materials
Layers of an MCPCB
- Copper circuit layer
- Dielectric layer
- Metal core (aluminum)
- Optional: Thermal interface material (TIM)
- Optional: Additional copper layer for thermal spreading
Metal Core Materials
Aluminum is the most common metal core material used in MCPCBs due to its excellent thermal conductivity, low cost, and easy machinability. Other materials, such as copper or copper-molybdenum alloys, may be used in high-performance applications that require even better thermal management.
Metal Core Material | Thermal Conductivity (W/mK) |
---|---|
Aluminum | 150-220 |
Copper | 380-400 |
Copper-Molybdenum | 180-220 |
Dielectric Layer Materials
The dielectric layer in an MCPCB must provide excellent electrical insulation while allowing efficient heat transfer. Common dielectric materials include:
- Aluminum oxide (Al2O3)
- Boron nitride (BN)
- Aluminum nitride (AlN)
- Epoxy-based polymers
Dielectric Material | Thermal Conductivity (W/mK) | Dielectric Strength (kV/mm) |
---|---|---|
Aluminum Oxide | 20-30 | 10-20 |
Boron Nitride | 50-70 | 40-50 |
Aluminum Nitride | 140-180 | 15-20 |
Epoxy-based Polymers | 1-10 | 20-50 |
MCPCB Manufacturing Process
Step 1: Metal Core Preparation
The aluminum or other metal core is cleaned and treated to improve adhesion with the dielectric layer. This may involve surface roughening, anodizing, or applying a special coating.
Step 2: Dielectric Layer Application
The dielectric layer is applied to the metal core using techniques such as screen printing, lamination, or vapor deposition. The dielectric layer thickness is carefully controlled to ensure proper electrical insulation and thermal conductivity.
Step 3: Copper Foil Lamination
A thin layer of copper foil is laminated onto the dielectric layer using heat and pressure. The copper foil thickness typically ranges from 0.5 oz to 4 oz (17 µm to 140 µm).
Step 4: Circuit Patterning
The desired circuit pattern is transferred onto the copper layer using photolithography. The exposed copper is then etched away, leaving the final circuit pattern.
Step 5: Surface Finishing
To protect the copper traces and improve solderability, a surface finish such as HASL, ENIG, or OSP is applied.
Step 6: Singulation and Drilling
The MCPCB panel is cut into individual boards, and any necessary holes or slots are drilled.
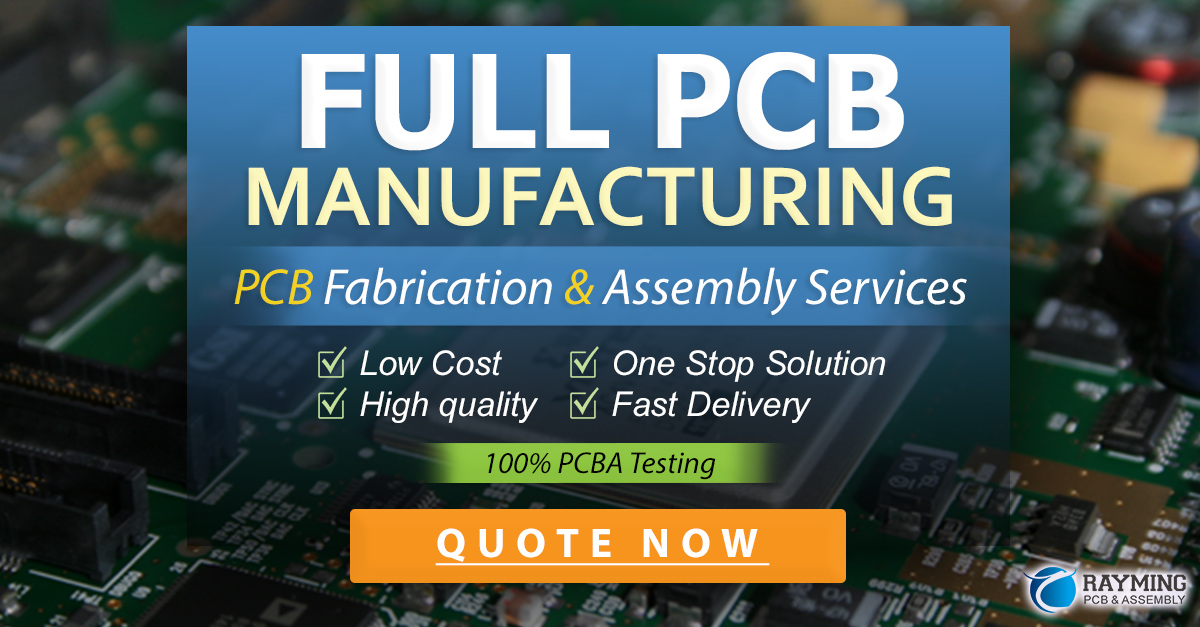
Thermal Management with MCPCBs
Thermal Resistance
Thermal resistance is a measure of a material’s ability to resist heat flow. In an MCPCB, the overall thermal resistance (Rth) is the sum of the thermal resistances of each layer:
Rth = Rth_copper + Rth_dielectric + Rth_metal_core
To minimize thermal resistance, it is essential to:
1. Use a metal core with high thermal conductivity
2. Keep the dielectric layer as thin as possible while maintaining electrical insulation
3. Maximize the copper area for better heat spreading
Thermal Vias
Thermal vias are copper-plated holes that pass through the MCPCB to improve heat transfer from the copper layer to the metal core. By strategically placing thermal vias near high-power components, designers can further enhance the thermal performance of the MCPCB.
Thermal Interface Materials (TIMs)
TIMs are used to fill air gaps and improve thermal contact between the MCPCB and external heat sinks or cooling systems. Common TIMs include:
1. Thermal greases
2. Phase-change materials
3. Thermal pads
4. Gap fillers
Applications of MCPCBs
LED Lighting
MCPCBs are widely used in LED lighting applications due to their ability to dissipate heat efficiently, which is critical for maintaining LED performance and longevity. By using MCPCBs, designers can create compact, high-power LED fixtures without the need for bulky external heat sinks.
Power Electronics
In power electronics applications, such as switch-mode power supplies and motor drives, MCPCBs help manage heat generated by high-current components like MOSFETs and IGBTs. The improved thermal management enables higher power densities and more reliable operation.
Automotive Electronics
MCPCBs are increasingly used in automotive electronics, particularly in LED headlights, tail lights, and other lighting systems. The enhanced thermal performance and durability of MCPCBs make them well-suited for the harsh operating conditions encountered in automotive environments.
MCPCB Design Considerations
Thermal Design
- Identify high-power components and their heat generation
- Calculate the required thermal resistance for efficient heat dissipation
- Select appropriate metal core and dielectric materials
- Optimize copper area and thermal via placement
Electrical Design
- Ensure proper electrical insulation between the copper layer and metal core
- Consider the impact of thermal vias on signal integrity
- Use appropriate trace widths and spacing for the required current carrying capacity
Mechanical Design
- Consider the mechanical stresses induced by the different thermal expansion coefficients of the materials used
- Design for manufacturability, including minimum hole sizes and spacing
- Incorporate mounting features and strain relief for connectors and cables
Future Trends in MCPCB Technology
Advanced Materials
Researchers are continually developing new materials with improved thermal and electrical properties for use in MCPCBs. Some promising materials include:
1. Carbon nanotubes (CNTs)
2. Graphene
3. Diamond-like carbon (DLC)
3D Printing
Additive manufacturing techniques, such as 3D printing, may enable the creation of MCPCBs with complex geometries and embedded cooling channels. This could lead to even more efficient thermal management and greater design flexibility.
Integration with Other Thermal Management Solutions
MCPCBs can be combined with other thermal management technologies, such as heat pipes, vapor chambers, or liquid cooling systems, to further enhance heat dissipation in high-power applications.
Frequently Asked Questions (FAQ)
1. What is the difference between an MCPCB and a traditional FR-4 PCB?
MCPCBs incorporate a metal core, typically aluminum, to enhance thermal management and heat dissipation. FR-4 PCBs are made of a glass-reinforced epoxy laminate and do not have a metal core for thermal management.
2. Can MCPCBs be used for high-frequency applications?
While MCPCBs are primarily designed for thermal management, they can be used in high-frequency applications with proper design considerations. The metal core can provide a stable reference plane for controlled impedance and shielding.
3. How does the dielectric layer thickness affect MCPCB performance?
A thinner dielectric layer improves thermal conductivity between the copper layer and the metal core, but it also reduces electrical insulation. Designers must balance thermal and electrical requirements when selecting the dielectric layer thickness.
4. Are MCPCBs more expensive than traditional FR-4 PCBs?
Yes, MCPCBs are generally more expensive than FR-4 PCBs due to the additional materials and manufacturing steps involved. However, the improved thermal performance and potential for reduced system costs (by eliminating external heat sinks) can make MCPCBs a cost-effective solution in many applications.
5. Can MCPCBs be used in flexible or bendable applications?
MCPCBs are typically rigid due to the metal core. However, some manufacturers offer flexible MCPCBs that use a thin, flexible metal core or a composite material with high thermal conductivity. These flexible MCPCBs can be used in applications that require a degree of flexibility or conformability.
Conclusion
Metal Core PCBs (MCPCBs) are an essential technology for managing heat in high-power electronic applications. By incorporating a metal core and specialized dielectric materials, MCPCBs enable efficient thermal management, improved reliability, and reduced system size and weight. As electronic systems continue to push the boundaries of power density and performance, the demand for advanced thermal management solutions like MCPCBs will only continue to grow.
No responses yet