What is PTFE?
PTFE is a synthetic polymer consisting of carbon and fluorine atoms arranged in a repeating pattern of -CF2-CF2-. It was accidentally discovered by Roy Plunkett, a chemist at DuPont, in 1938 while he was working on developing a new refrigerant. Plunkett noticed that a pressurized cylinder containing tetrafluoroethylene gas had polymerized into a white, waxy solid. This solid material exhibited remarkable properties, such as low friction, high heat resistance, and chemical inertness.
The chemical structure of PTFE is as follows:
F F
| |
-[-C---C-]-n
| |
F F
The strong carbon-fluorine bonds and the high electronegativity of fluorine atoms contribute to PTFE’s unique properties.
Properties of PTFE
PTFE possesses a combination of properties that make it an attractive material for various applications. Some of its key properties include:
-
Low Friction: PTFE has one of the lowest coefficients of friction among solid materials. Its slippery surface allows objects to slide easily over it, making it an ideal material for non-stick coatings and low-friction applications.
-
High Temperature Resistance: PTFE can withstand temperatures ranging from -200°C to +260°C (-328°F to +500°F) without significant changes in its properties. It maintains its strength and flexibility even at extreme temperatures.
-
Chemical Inertness: PTFE is resistant to most chemicals, including strong acids, bases, and solvents. It does not react with other substances, making it suitable for use in harsh chemical environments.
-
Electrical Insulation: PTFE has excellent dielectric properties, making it an effective electrical insulator. It is often used in wire and cable insulation, as well as in electronic components.
-
Non-Stick Properties: PTFE’s low surface energy prevents materials from adhering to its surface, making it an ideal choice for non-stick cookware and other applications where easy cleaning is essential.
Property | Value |
---|---|
Density | 2.13-2.19 g/cm³ |
Melting Point | 327°C (621°F) |
Tensile Strength | 20-35 MPa |
Elongation at Break | 200-400% |
Dielectric Constant | 2.1 at 1 MHz |
Coefficient of Friction | 0.05-0.1 |
Manufacturing Process of PTFE
PTFE is manufactured through a process called emulsion polymerization. The basic steps involved in the production of PTFE are as follows:
-
Monomer Preparation: Tetrafluoroethylene (TFE) monomer is produced by the pyrolysis of chlorodifluoromethane (HCFC-22) at high temperatures.
-
Emulsion Polymerization: The TFE monomer is dispersed in water along with an emulsifier and an initiator. The mixture is agitated and heated to initiate polymerization. As the reaction progresses, PTFE particles form and grow in size.
-
Coagulation and Drying: Once the desired particle size is achieved, the PTFE emulsion is coagulated using chemicals or mechanical methods. The coagulated PTFE is then washed, filtered, and dried to remove any impurities and moisture.
-
Sintering: The dried PTFE powder is compressed into a preform and sintered at temperatures above its melting point (327°C). During sintering, the PTFE particles fuse together, forming a solid mass.
-
Shaping and Finishing: The sintered PTFE can be shaped into various forms, such as sheets, rods, tubes, or custom-molded parts, using techniques like machining, extrusion, or compression molding. The final products are then inspected for quality and packaged for distribution.
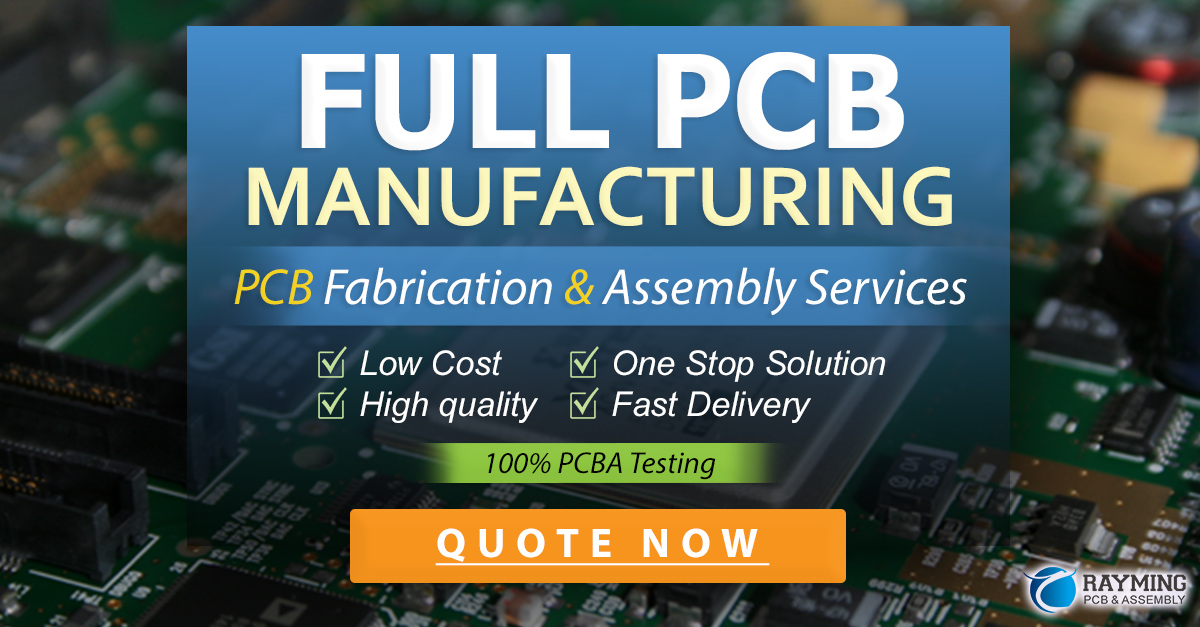
Applications of PTFE
PTFE’s unique properties make it suitable for a wide range of applications across various industries. Some of the common applications of PTFE include:
-
Non-Stick Cookware: PTFE coatings are used on pots, pans, and baking trays to prevent food from sticking and to facilitate easy cleaning.
-
Seals and Gaskets: PTFE’s chemical inertness and temperature resistance make it an ideal material for seals and gaskets in chemical processing, automotive, and aerospace industries.
-
Electrical Insulation: PTFE is used as an insulator in wires, cables, and electronic components due to its excellent dielectric properties.
-
Medical Devices: PTFE’s biocompatibility and non-reactive nature make it suitable for use in medical implants, surgical instruments, and pharmaceutical equipment.
-
Textile Coatings: PTFE coatings are applied to fabrics to create water-resistant, stain-resistant, and breathable materials for outdoor clothing and technical textiles.
-
Lubricants: PTFE powders and dispersions are used as lubricants in various applications, such as bearings, gears, and sliding surfaces, to reduce friction and wear.
Is PTFE a Rubber or a Plastic?
The classification of PTFE as a rubber or a plastic has been a subject of debate due to its unique properties that differ from traditional materials in these categories. To determine whether PTFE is a rubber or a plastic, let’s examine the characteristics of each material class.
Characteristics of Rubbers
Rubbers are elastomeric materials characterized by their ability to undergo large elastic deformations and recover their original shape upon the removal of stress. They typically have the following properties:
- High elasticity and flexibility
- Low modulus of elasticity
- Good tear and abrasion resistance
- Ability to absorb vibrations and shocks
Examples of rubbers include natural rubber, styrene-butadiene rubber (SBR), and nitrile rubber (NBR).
Characteristics of Plastics
Plastics are synthetic materials composed of long-chain polymers that can be molded or shaped into various forms. They are generally characterized by the following properties:
- Good formability and processability
- Wide range of mechanical and thermal properties
- Resistance to chemicals and corrosion
- Electrical insulation properties
Examples of plastics include polyethylene (PE), polypropylene (PP), and polyvinyl chloride (PVC).
PTFE: A Thermoplastic Fluoropolymer
Based on its properties and behavior, PTFE is classified as a thermoplastic fluoropolymer. Thermoplastics are a type of plastic that can be repeatedly melted and reshaped upon heating, and they solidify upon cooling. PTFE exhibits thermoplastic behavior, as it can be melted and reshaped multiple times without significant degradation of its properties.
However, PTFE also displays some unique characteristics that set it apart from other thermoplastics:
- High melting point (327°C) compared to most thermoplastics
- Excellent chemical resistance and inertness
- Low surface energy and friction
- Exceptional temperature resistance
While PTFE shares some properties with rubbers, such as flexibility and low modulus of elasticity, it lacks the high elasticity and ability to recover its original shape after deformation, which are key characteristics of rubbers.
Frequently Asked Questions (FAQ)
-
Is PTFE safe for use in cookware?
Yes, PTFE is generally considered safe for use in cookware when used according to the manufacturer’s instructions. However, overheating PTFE-coated cookware above 260°C (500°F) can cause the release of toxic fumes, which may cause flu-like symptoms known as polymer fume fever. It is recommended to avoid using PTFE-coated cookware at very high temperatures and to ensure proper ventilation in the kitchen. -
Can PTFE be recycled?
PTFE is not commonly recycled due to the challenges associated with its high melting point and chemical inertness. However, some specialized recycling facilities may accept PTFE products for recycling. It is essential to check with local recycling centers or the manufacturer for specific recycling guidelines. -
How does PTFE compare to other fluoropolymers?
PTFE is one of the most well-known fluoropolymers, but there are other fluoropolymers with similar properties, such as fluorinated ethylene propylene (FEP), perfluoroalkoxy alkanes (PFA), and ethylene tetrafluoroethylene (ETFE). These fluoropolymers share some characteristics with PTFE, such as chemical inertness and high temperature resistance, but they may have different melting points, mechanical properties, and processing requirements. -
What are the limitations of PTFE?
While PTFE has many desirable properties, it also has some limitations. PTFE has a relatively high cost compared to other plastics due to its complex manufacturing process. It also has a low wear resistance and can be prone to creep under sustained loads. Additionally, PTFE has a limited solubility in most solvents, which can make it challenging to bond or adhere to other materials. -
Can PTFE be used in medical implants?
Yes, PTFE is biocompatible and has been used in various medical implants, such as vascular grafts, hernia meshes, and sutures. Its non-reactive nature and resistance to bodily fluids make it suitable for long-term implantation. However, the use of PTFE in medical applications is subject to strict regulations and testing to ensure patient safety.
Conclusion
In conclusion, PTFE is a unique thermoplastic fluoropolymer that exhibits a combination of properties that distinguish it from traditional rubbers and plastics. While it shares some characteristics with both material classes, PTFE is primarily classified as a plastic due to its thermoplastic behavior and ability to be molded and reshaped upon heating.
PTFE’s low friction, high temperature resistance, chemical inertness, and non-stick properties make it an invaluable material in various industries, ranging from cookware and automotive components to medical devices and industrial equipment. As researchers continue to explore new applications and modifications of PTFE, it is expected that this versatile material will continue to play a significant role in shaping the future of materials science and engineering.
No responses yet