What is FR4?
FR4 is a composite material made from woven fiberglass cloth and an epoxy resin binder. The “FR” stands for “Flame Retardant,” and the “4” indicates the specific grade of the material. FR4 is the most common type of PCB material used in the electronics industry due to its balance of properties and cost-effectiveness.
The fiberglass cloth provides the mechanical strength and dimensional stability to the FR4 laminate, while the epoxy resin offers excellent electrical insulation and resistance to moisture and chemicals. The flame retardant properties of FR4 come from the addition of halogenated compounds, such as bromine, to the epoxy resin.
Factors Affecting FR4 durability
1. Mechanical Stress
FR4 PCBs are subjected to various mechanical stresses during their lifetime, including vibration, shock, and bending. The durability of FR4 in these situations depends on several factors, such as the thickness of the board, the number of layers, and the design of the PCB.
Thicker FR4 boards tend to be more durable than thinner ones, as they can withstand higher levels of mechanical stress without cracking or breaking. Multi-layer FR4 PCBs are also generally more durable than single-layer boards, as the additional layers provide extra reinforcement and distribute the stress more evenly.
The design of the PCB also plays a crucial role in its durability. Proper placement of components, use of strain relief features, and avoidance of sharp corners and edges can all help to minimize mechanical stress and improve the durability of the FR4 board.
2. Thermal Stress
FR4 PCBs are also subjected to thermal stress during their lifetime, as the temperature of the board can fluctuate due to the heat generated by the electronic components and the ambient temperature of the environment.
The durability of FR4 under thermal stress depends on its glass transition temperature (Tg), which is the temperature at which the material transitions from a rigid, glassy state to a soft, rubbery state. Standard FR4 has a Tg of around 130°C to 140°C, while high-Tg FR4 variants can have a Tg of up to 170°C or higher.
When the temperature of the FR4 board exceeds its Tg, the material can soften and deform, leading to warping, twisting, or delamination of the PCB. This can cause mechanical stress on the components and solder joints, leading to failures and reduced durability.
To improve the thermal durability of FR4 PCBs, designers can use high-Tg FR4 variants, incorporate thermal management features such as heat sinks and cooling fans, and optimize the placement of high-heat generating components.
3. Environmental Factors
FR4 PCBs can also be affected by environmental factors such as humidity, chemicals, and UV radiation. These factors can degrade the properties of the FR4 material over time, leading to reduced durability and reliability.
Humidity can cause moisture absorption in the FR4 material, leading to swelling, warping, and delamination of the PCB. This can be particularly problematic in high-humidity environments or applications where the PCB is exposed to liquid water.
Chemicals can also degrade the properties of FR4, particularly if the board is exposed to harsh chemicals such as acids, bases, or solvents. These chemicals can attack the epoxy resin and fiberglass reinforcement, leading to weakening and failure of the PCB.
UV radiation can cause the FR4 material to become brittle and discolored over time, particularly if the board is exposed to direct sunlight or other sources of UV light. This can lead to cracking, chalking, and reduced mechanical strength of the PCB.
To improve the environmental durability of FR4 PCBs, designers can use conformal coatings or encapsulation to protect the board from humidity and chemicals, and use UV-resistant materials or coatings to protect against UV degradation.
Testing FR4 Durability
To ensure the durability of FR4 PCBs, manufacturers and designers often perform various tests to evaluate the material’s performance under different stress conditions. Some common tests include:
1. Thermal Cycling
Thermal cycling tests involve subjecting the FR4 PCB to repeated cycles of high and low temperatures to simulate the thermal stresses experienced during operation. The test typically involves heating the board to a high temperature (e.g., 125°C) and then cooling it to a low temperature (e.g., -40°C) for a specified number of cycles.
The number of cycles and the temperature range used in the test depend on the specific application and the expected operating conditions of the PCB. After the test, the board is inspected for any signs of damage, such as cracks, delamination, or warping.
2. Mechanical Shock and Vibration
Mechanical shock and vibration tests involve subjecting the FR4 PCB to sudden impacts or continuous vibrations to simulate the mechanical stresses experienced during transportation, handling, and operation.
Shock tests typically involve subjecting the board to a high-acceleration, short-duration impact, such as dropping the board from a specified height onto a hard surface. Vibration tests involve subjecting the board to continuous, low-frequency vibrations for a specified duration, such as placing the board on a shaker table.
After the test, the board is inspected for any signs of damage, such as cracks, fractures, or component failures.
3. Humidity and Temperature
Humidity and temperature tests involve subjecting the FR4 PCB to high humidity and temperature conditions to simulate the environmental stresses experienced during operation in harsh environments.
The test typically involves placing the board in a humidity chamber and exposing it to a specified humidity level (e.g., 85% relative humidity) and temperature (e.g., 85°C) for a specified duration (e.g., 1000 hours). After the test, the board is inspected for any signs of damage, such as moisture absorption, swelling, or delamination.
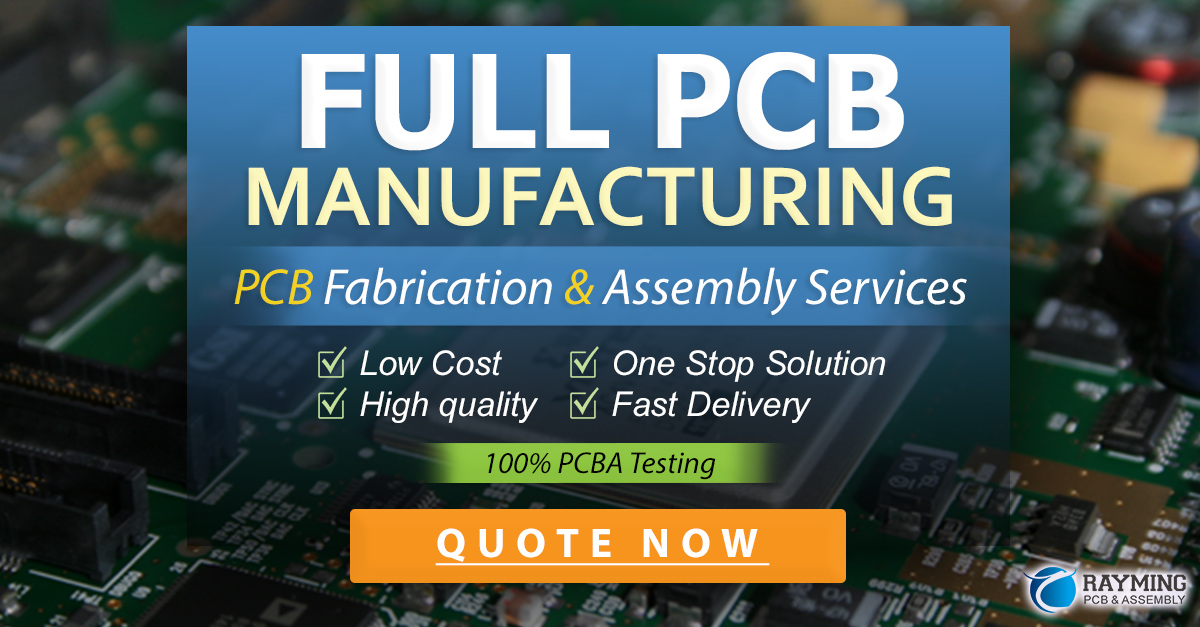
Comparison of FR4 to Other PCB Materials
While FR4 is the most widely used PCB material, there are other materials available that offer different properties and durability characteristics. Some common PCB materials include:
1. Polyimide
Polyimide is a high-performance polymer that offers excellent thermal stability, chemical resistance, and mechanical strength. It has a higher Tg than FR4 (typically around 250°C) and can withstand higher temperatures without deformation or degradation.
Polyimide PCBs are often used in high-reliability applications, such as aerospace, military, and medical devices, where durability and performance are critical. However, polyimide is also more expensive than FR4 and can be more difficult to process and manufacture.
2. PTFE
PTFE (polytetrafluoroethylene) is a fluoropolymer that offers excellent electrical properties, low dielectric constant, and high thermal stability. It is commonly used in high-frequency applications, such as radar and telecommunications, where signal integrity and low loss are critical.
PTFE-PCB/”>PTFE PCBs are also highly resistant to chemicals and moisture, making them suitable for use in harsh environments. However, PTFE is also more expensive than FR4 and can be more difficult to process and manufacture.
3. Ceramic
Ceramic PCBs are made from inorganic materials, such as alumina or beryllia, and offer excellent thermal conductivity, electrical insulation, and mechanical strength. They are often used in high-power applications, such as LED lighting and power electronics, where heat dissipation and durability are critical.
Ceramic PCBs are also highly resistant to chemicals, moisture, and UV radiation, making them suitable for use in harsh environments. However, ceramic is also more expensive than FR4 and can be more brittle and prone to cracking under mechanical stress.
FR4 Durability in Different Applications
The durability requirements for FR4 PCBs vary depending on the specific application and operating environment. Some common applications and their durability requirements include:
1. Consumer Electronics
Consumer electronics, such as smartphones, laptops, and televisions, typically have moderate durability requirements. The PCBs in these devices are subjected to moderate levels of mechanical stress, thermal stress, and environmental exposure during normal use and handling.
FR4 is a suitable material for most consumer electronics applications, as it offers a good balance of properties and cost-effectiveness. However, designers may need to use thicker boards, high-Tg FR4 variants, or incorporate additional protection features to improve durability in more demanding applications.
2. Automotive Electronics
Automotive electronics, such as engine control units, infotainment systems, and sensors, have high durability requirements due to the harsh operating environment and safety-critical nature of the application.
The PCBs in automotive electronics are subjected to high levels of mechanical stress, thermal stress, and environmental exposure, including vibration, shock, temperature extremes, humidity, and chemicals. As a result, automotive-grade FR4 PCBs typically require additional testing and certification to ensure they meet the required durability standards.
Designers may also need to use high-Tg FR4 variants, incorporate additional protection features, or use alternative materials such as polyimide or ceramic in more demanding automotive applications.
3. Industrial Electronics
Industrial electronics, such as factory automation systems, process control equipment, and power supplies, have high durability requirements due to the harsh operating environment and critical nature of the application.
The PCBs in industrial electronics are subjected to high levels of mechanical stress, thermal stress, and environmental exposure, including vibration, shock, temperature extremes, humidity, and chemicals. As a result, industrial-grade FR4 PCBs typically require additional testing and certification to ensure they meet the required durability standards.
Designers may also need to use high-Tg FR4 variants, incorporate additional protection features, or use alternative materials such as polyimide or ceramic in more demanding industrial applications.
4. Aerospace and Defense Electronics
Aerospace and defense electronics, such as avionics systems, communication equipment, and military vehicles, have the highest durability requirements due to the extreme operating environment and mission-critical nature of the application.
The PCBs in aerospace and defense electronics are subjected to extreme levels of mechanical stress, thermal stress, and environmental exposure, including high-g acceleration, shock, vibration, temperature extremes, humidity, and radiation. As a result, aerospace and defense-grade FR4 PCBs typically require extensive testing and certification to ensure they meet the required durability standards.
Designers often need to use alternative materials such as polyimide or ceramic, incorporate extensive protection features, and follow strict design guidelines to ensure the durability and reliability of the PCBs in these applications.
FAQs
1. What is the difference between standard FR4 and high-Tg FR4?
Standard FR4 has a glass transition temperature (Tg) of around 130°C to 140°C, while high-Tg FR4 variants have a Tg of up to 170°C or higher. The higher Tg of high-Tg FR4 allows it to withstand higher temperatures without deformation or degradation, making it more suitable for high-temperature applications.
2. Can FR4 PCBs be used in high-humidity environments?
FR4 PCBs can be used in high-humidity environments, but they may require additional protection features such as conformal coatings or encapsulation to prevent moisture absorption and degradation. Designers may also need to use alternative materials such as polyimide or ceramic in more demanding high-humidity applications.
3. How does the thickness of the FR4 board affect its durability?
Thicker FR4 boards tend to be more durable than thinner ones, as they can withstand higher levels of mechanical stress without cracking or breaking. However, thicker boards also have higher material costs and may require more processing steps, so designers need to balance durability requirements with cost and manufacturing considerations.
4. What is the typical lifespan of an FR4 PCB?
The lifespan of an FR4 PCB depends on many factors, including the specific application, operating environment, and design of the board. In general, a well-designed and manufactured FR4 PCB can last for several years to several decades, depending on the application. However, the actual lifespan will depend on the specific durability requirements and operating conditions of the application.
5. Can FR4 PCBs be recycled?
FR4 PCBs can be recycled, but the process is more complex than recycling other materials such as metals or plastics. The recycling process typically involves shredding the PCBs and separating the metal components (such as copper and gold) from the fiberglass and epoxy material. The metal components can then be recycled and used in new products, while the fiberglass and epoxy material may be used as a filler in construction materials or other applications.
Conclusion
FR4 is a widely used material for PCBs due to its good balance of electrical, mechanical, and thermal properties, as well as its cost-effectiveness. However, the durability of FR4 PCBs depends on many factors, including the specific application, operating environment, and design of the board.
To ensure the durability of FR4 PCBs, designers need to consider factors such as mechanical stress, thermal stress, and environmental exposure, and incorporate appropriate design features and protection measures. In more demanding applications, designers may need to use alternative materials such as polyimide or ceramic, or incorporate extensive testing and certification to ensure the required durability standards are met.
Overall, while FR4 is a versatile and widely used material for PCBs, its durability is not a one-size-fits-all proposition. Designers need to carefully consider the specific requirements and operating conditions of each application to ensure the appropriate level of durability is achieved.
No responses yet